Abstract
More than 50 years have passed since the discovery of large oil fields in the Volga region and Western Siberia. Since then, all of them have entered the final stage of development, characterized by a decrease in oil production, an increase in water cut in wells and an increase in the share of hard-to-recover reserves. In such conditions, the achievement of economic efficiency of implemented projects largely depends on the productivity of the business process management system at the enterprise. In the last decade, the improvement of the management system at the enterprises of the oil-producing complex was associated with the withdrawal of non-core assets from the structure, the basis of which was oilfield services. However, due to insufficiently effective competition in this market segment, the price for the provision of oilfield services is overstated. This work is devoted to the management of service production processes in the system of an oil production enterprise. According to statistics, service production is a major source of cost formation for an enterprise. For example, it accounts for 30-50% of all operating costs. Due to the fact that most of the large oil fields in Russia are at the final stage of development (over 70%), the largest share of operating costs is well workover services. Accordingly, the purpose of the study is to substantiate the theoretical provisions for the implementation of reengineering of business processes and develop practical recommendations for improving the efficiency of management in this segment of services.
Keywords: Oil production enterprise, well workover, reengineering, business process, management system
Introduction
The characteristic features of the final stage of oil field development are high production of reserves, an increase in the water cut of the well fluid, a large wear of fixed assets and an increase in the cost of oil extraction. Taking into account all the above factors, one of the main directions for the implementation of investment projects of oil producing enterprises is the stabilization of the level of oil production through workover of wells, which largely determines the financial result of the company as a whole (Aganbegyan, 2018).
The object of the study was the economic activity of oil production enterprises in terms of the organization of well workover services, and the subject was the organizational and economic relations for the development of business processes for the provision of these services.
Problem Statement
The traditional approach to well workover management at an oil production enterprise is a set of works that are performed by structural divisions based on functional and operational characteristics (Kolesova & Nekrasov, 2012). Until recently, this form of management was considered quite effective: due to the clear centralization of the functions performed and the specialization of personnel, high profitability of the main production was achieved.
However, in the context of an increase in the cost of production, it is necessary to ensure not only the achievement of the planned level for oil production, but also the maximum efficiency of spending funds for workover of wells (Chazov et al., 2018).
The directions for improving business processes in the provision of well workover services presented in the scientific literature are focused on increasing efficiency through the development of measures on a functional basis (Orekhova, 2018; Orekhova & Evseeva, 2020).
The question of the influence of the implemented measures developed in the framework of improving the efficiency of indicators of one of the management functions on indicators in related areas of activity has not been studied. Thus, an integrated approach to assessing the effectiveness of the implemented measures for the enterprise as a whole is not provided.
Research Questions
In the basis of the solution of the issues in this study, it seems necessary to use a modern approach to improving the management (Krainova & Parkhomenko, 2017a) of workover of wells, which should have a set of properties and features that determine not only the fulfillment of the task, but its implementation in the shortest possible time, with minimal costs and high quality of service provision in difficult, constantly changing conditions. Accordingly, he must coordinate the actions of various departments; be results-oriented and efficiency-driven; have transparency in actions to achieve the result; identify opportunities for targeted improvement of processes and elimination of barriers between functional units; aims at reducing unnecessary vertical interactions and eliminating unclaimed processes; should help to reduce time and material costs (Orekhova & Evseeva, 2020).
Purpose of the Study
The purpose of this study is to substantiate the theoretical provisions of the implementation of reengineering of business processes and develop practical recommendations for improving the efficiency of management in this segment of services.
Research Methods
Existing well workover management system
In order to improve the efficiency of the activities of the oil-extracting industry enterprises are actively moving from a three-level (functional-operational) to a two-level (functional-process) management system (Figure 1). This process made it possible to exclude duplication of functions at the level of the central administrative office, branches, production shops; distortion of information coming from the production shops; the difficulty of pursuing a unified policy in managing end-to-end processes (Kolomeets & Tikunov, 2005).
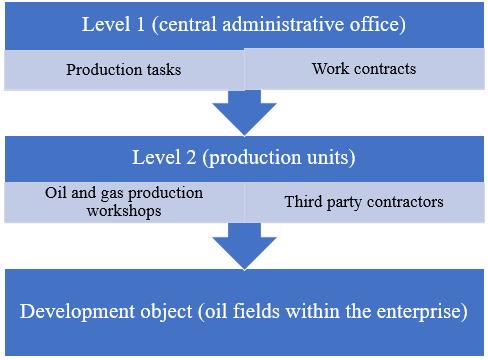
Within the framework of the implementation of a two-tier management system, a profile and non-core type of activity is distinguished.
The most attention is paid to the management of the processes of the specialized type of activity, since they are directly responsible for oil production and delivery to the main oil pipeline. They are the source of the company's revenue. At the same time, the production divisions are in the structure of the oil production enterprise and are directly interested in the implementation of the oil production plan.
Management of non-core business processes, including well workover, is provided at the level of selection of contractors according to established criteria (Krainova & Parkhomenko, 2017b).
The Customer's function is reduced to the selection of contractors on a competitive basis, the preparation of local regulations governing the relationship of the Customer's production services with the contractor and the preparation of information on the achieved performance indicators.
Let us consider how the existing management structure is organized in terms of performing well workovers (workover) at an oil production enterprise (Figure 2):
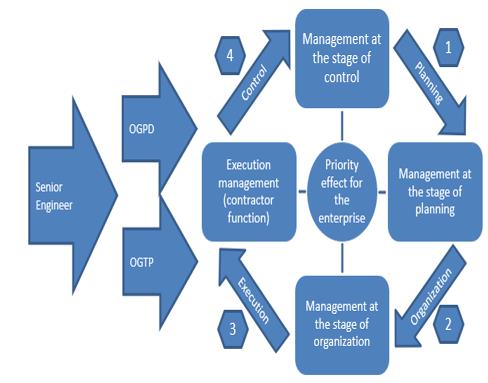
There are four departments involved in the main production process: The Oil/Gas Production Department (OGPD), the Reservoir Pressure Maintenance Department (RPMD), the Oil/Gas Treatment Department (OGTP), and the Pipeline Operations Department (POD). The chief engineer manages these processes through the heads of departments. Under the direct supervision of the head of OGPD there are oil/gas production shops (OGPS), as well as production services/departments that provide support for the main production of oil/gas. In particular, the well maintenance and workover department (WMWD) is responsible for ensuring the workover crew resource.
As can be seen from Figure 2, the direct management of workover consists of 4 main stages: planning, organization, execution and control. In this case, the functions of organization and execution are implemented on the basis of outsourcing. This approach involves obtaining a result from a business process without managing it, attracting competent specialists, increasing the efficiency of using fixed assets, economies of scale, and reducing risks.
At the first stage, WMWD, based on the needs of OGPS, calculates the production program for workover and concludes contracts for the provision of these services.
At the second stage, OGPS, in cooperation with workover contractors, form operational schedules for the movement of brigades.
At the third stage, the workover contractors, in cooperation with OGPS, directly ensure the implementation of the workover program in accordance with the operational schedules.
At the fourth stage, WMWD, on the basis of the documentation submitted by the workover contractors, analyzes the implementation of the production program.
The implemented structure of workover management at an oil production enterprise makes it possible to ensure the achievement of the oil/gas production plan due to the possibility of taking prompt measures at each stage of the workover process. But it does not allow to improve the quality of management of the workover process itself, which consists in continuous improvement of the organization's system, taking into account not so much the achievement of basic production indicators, but ensuring an integrated approach when implementing a new measure, taking into account the economic assessment of efficiency as a whole for the entire enterprise.
Proposed workover management system
The main characteristic of modern business is a rapid change in the environment inside and outside the company, a change in the conditions in which the company exists. This is due to the constant appearance on the market of new technologies and information and technical means, along with which new customer needs for more modern, high-quality products and services appear. A modern company must meet these challenges: monitor market development trends and the activities of competitors, develop and offer new services, master new technologies for organizing activities and management (Tikhanov et al., 2016). The company must forget about static and learn to live in a state of constant change, improving current and introducing new methods of work. Moreover, at any given time, it must work efficiently and be fully controllable. This is possible only if there is a certain management methodology that allows you to implement changes and at the same time not lose the stability and efficiency of daily work (Simchenko et al., 2018).
To achieve the set goal of the study in terms of substantiating the theoretical provisions for the formation of an effective organization of business processes (Chazov et al., 2019), it is proposed to implement the following interaction scheme in the workover of wells (Figure 3).
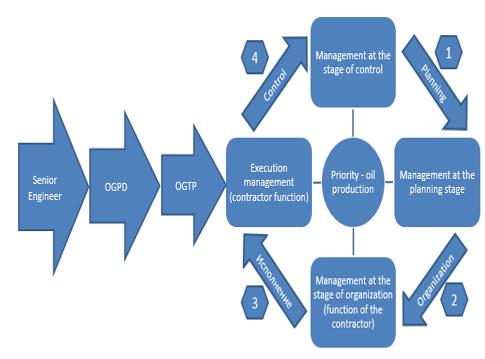
This scheme is based on the implementation of 3 basic principles of increasing the efficiency of business processes:
Centralization of management;
Creation of vertical links between the main and auxiliary business process;
Availability of operational feedback within management functions (Krainova, 2016).
The implementation of the formed principles of improving the efficiency of business processes in workover provides for the following changes in the organizational structure:
- Enhancing the role of key auxiliary business processes, primarily WMWD, due to direct subordination to the chief engineer (after changing the structure of the management of current and workover of wells or MCWW/УТКРС);
- Creation of three departments in the MCWW block according to the process principle with a focus on the final result and the possibility of operational interaction with related structural divisions / contractors: planning department of workover work (the management function is provided at the planning stage); department of maintenance of services of workover (the management function is provided at the organizational stage); department of workover monitoring (the function of management of the stage of execution is provided); the head of the MCWW (the function of management/interaction is provided at the control stage).
Thus, the implementation of reengineering of business processes in the workover management system is to create a cyclical model of continuous improvement of the enterprise at each level and close interaction with related structural divisions/contractors, providing an integrated approach to the implementation of a new measure, taking into account the economic assessment of efficiency in general for everything. enterprises.
Findings
Methodology for an integrated approach to assessing the effectiveness of implemented measures
A method for assessing the effectiveness of projects is proposed, a distinctive feature of which is the assessment of the achievement of the set goals, taking into account the reflection of changes in the key areas of the enterprise: safety, quality, timing, costs, culture, which allows you to quickly make decisions on adjusting processes and projects taking into account internal factors and external development barriers (Chepur et al., 2019).
Let us consider how this approach functions on the example of the implementation of measures for the implementation of combined brigade equipment (installation of a filling tank, a technological tank and a tool shop on one chassis).
We will assess the degree of influence on each other 5 key performance criteria: safety - the number of tanks operated with violations of industrial safety; quality - the proportion of rejects due to poor-quality wellbore flushing; terms - the average duration of the repair; costs - transportation costs for 1 move; culture - the number of violations of production culture for 1 repair.
The scale is based on the dynamics of changes in each indicator based on the results of work over the past year. Let's calculate the correlation coefficient between each of the five performance criteria in Microsoft Excel using the CORREL function (Table 1).
The closer the paired correlation coefficient in absolute value is to one, the closer the statistical relationship between the evaluated criteria. It is worth noting that the increase in the indicators "Quality", "Terms", "Costs" should begin with training personnel in the order and organization of safe working conditions ("Culture", "Safety"), which do not require additional funding.
At the first stage of the implementation of the methodology for each criterion of effectiveness, it is necessary to determine the weighting factor. It is determined by the ranking method using an expert survey. According to the results of the survey, the following coefficients were determined: safety - 0.19; quality - 0.22; terms - 0.21; costs - 0.20; culture - 0.18.
At the second stage, based on the concept of result management according to P. Drucker's goals, we will determine the efficiency factor of the measure for the implementation of combined brigade equipment (Table 2) (Bamel & Bamel, 2018).
As can be seen from Table 2, the coefficient of effectiveness from the implementation of measures for the introduction of combined brigade equipment is not the maximum value. It is necessary to make prompt decisions on adjusting internal and external factors that could have an impact on the failure to achieve indicators for three out of five performance criteria: culture - 0.75; quality - 0.80; costs - 0.90.
The most effective approach in terms of adjusting internal and external factors in order to achieve the maximum indicator for all 5 criteria is implemented in the proposed management system (Figure 3). Its implementation will allow you to get the following advantages when developing measures aimed at achieving planned targets:
Efficiency in the preparation of the initial data required for a comprehensive analysis;
Objectivity in assessing the opinion of experts by examining the position on each issue of all interested parties;
Conducting a multivariate analysis of the reasons for not achieving the goal by competent specialists;
Assessment of the impact of changes in the implementation of measures on the financial and economic activities of the enterprise as a whole;
The minimum period of time between the development and the beginning of the implementation of activities;
An individual approach to the implementation of activities, taking into account the characteristics of each region;
Prompt interaction at all levels in case of need for corrective action.
At the third stage, in accordance with the basic concept of the proposed management system, the planned activities should be low-cost and cost-effective. Consider the option of searching for the optimal size of one-time costs using an economic and mathematical model (Table 3).
Taking into account the weight coefficients for each performance indicator and the fact that the activities carried out in the framework of the directions "Security" and "Culture" will contribute to the achievement of goals for the rest of the indicators, and their planned effect will be conditional, the economic and mathematical model of searching for options for achieving the set goal with a minimum number of one-time costs with the planned economic effect will be as follows:
(1)
where:X1-safety, X2-quality, X3-terms, X4-costs, X5-culture.
In this case, there are the following restrictions (2) and (3):
(2)
(3)
where: X i is the optimal desired value of one-time costs for the implementation each events;
Ai-the calculated economic effect expected from the implementation of each events.
The economic and mathematical model of this problem will look like this:
(4)
Let us solve the direct linear programming problem using the simplex method.
With the use of weighting factors, for the implementation of the set goals with a certain planned economic effect - 96,000 thousand rubles, one-time project costs should be less than 19,840 thousand rubles:
2640 + 8400 + 8800 = 19840 thousand rubles.
"F(x) ≤ 19840 thousand rubles."
Taking into account the fact that the one-time costs to achieve the set goal were used in full, it is most expedient to implement activities that do not require additional funding. Based on the obtained correlation between the three indicators ("Culture", "Quality", "Costs"), to achieve the target indicators, organizational measures were developed in the direction of "Culture" (Table 4).
Similarly, to the economic and mathematical model (1), provided that the amount of costs that an enterprise can invest in the implementation of the project is known, it is possible to estimate the optimal economic effect of each event (Table 5) (Belysh, 2018).
The economic and mathematical model for achieving the minimum economic effect will be solved as a double task of achieving the set goal with a minimum amount of one-time costs:
(5)
In this case, there are the following restrictions (6) and (7):
(6)
(7)
where: Xi is the optimal desired value of the economic effect expected from implementation of each event;
Ai-costs for the implementation of each activity.
Using the weighting factors for the importance of changes for each indicator, we calculate the amount of one-time costs:
(8)
(9)
9750 + 9091 + 9286 = 19840 thousand rubles.
"F (A) ≥28127 thousand rubles."
To achieve the set goals with a certain amount of one-time investment in the project - 5,000 thousand rubles, the amount of economic effect (in terms of funds spent) must be at least 28,127 thousand rubles.
Conclusion
In modern conditions of growth in the share of hard-to-recover oil reserves, the cost of oil production is increasing. The previously implemented approach at oil production enterprises to ensure the planned level of oil production with the involvement of traditional services is a high-cost and ineffective solution.
In this paper, the increase in the efficiency of oilfield services is implemented through the reengineering of business processes in the workover management system. The essence of reengineering is to create a cyclical model of continuous improvement of the enterprise's activities at each level and close interaction with related structural divisions/contractors, providing an integrated approach to the implementation of any event, taking into account the economic assessment of efficiency as a whole for the entire enterprise. It is based on three main principles: centralization of management, the creation of vertical links between the main and auxiliary business processes, the presence of operational feedback within the management functions.
One of the tools for implementing the reengineering of business processes in the workover management system is the method of an integrated approach to assessing the effectiveness of the activities being implemented. The developed methodology allows you to visually assess the effectiveness of the proposed management system. Based on the calculations, the degree of interconnection between each of the five key performance criteria was established using the example of the implementation of combined equipment (installation of a filling tank, a technological tank and a tool shop on one chassis), which ultimately made it possible to implement measures to improve efficiency, taking into account the achievement of target values, and also to determine the ratio of the minimum amount of costs (19.8 million rubles) and the planned economic effect (96.0 million rubles) using the proposed economic and mathematical model of searching for options to achieve this goal.
References
Aganbegyan, A. (2018). Towards a civilized market, Bulletin of the Institute of Economics of the Russian Academy of Sciences, 1. 7-26.
Bamel, U. K., & Bamel, N. (2018). Organizational resources, KM process capability and strategic flexibility: a dynamic resource-capability perspective, Journal of Knowledge Management, 7(22), 1555-1572.
Belysh, K. V. (2018). Methodological tools for the implementation and functioning of lean production at an industrial enterprise. Izhevsk.
Chazov, E. L., Grakhov, V. P., Krivorotov, V. V., & Simchenko, O. L. (2019). Improving planning efficiency as the basis for managing the investment activities of an industrial enterprise, Energy. Izv. higher. study. institutions and energy. associations of the CIS, 62(1), 88-100.
Chazov, E. L., Grakhov, V. P., & Simchenko, O. L. (2018). A strategic cash flow optimization model used in managing the efficiency of an industrial enterprise in the face of changes in environmental factors, Fundamental research, 8, 127-130.
Chepur, P., Tarasenko, A., Tikhanov, E., Krivorotov, V., & Gruchenkova, A. (2019). Development of a technology for diagnosingstteel tanks without removing the protective coating, Advances in Intelligent Systems and Computing, 983, 686-692.
Kolesova, S. B., & Nekrasov, V. I. (2012). Development of business processes for the production of oil producing enterprises. Monograph (FGBOU VPO "UdSU").
Kolomeets, V. V., & Tikunov, S. V. (2005). Criteria for the economic efficiency of well workover as an investment process, Oil industry, 6, 60-61.
Krainova, E. A. (2016). Coordination of interests of oil and gas and service companies in the development of the country's oil and gas complex. Collection of scientific papers of the international scientific conference “Economic problems and mechanisms of development of the mineral resource complex (Russian and world experience). National Mineral Resources University "Mining".
Krainova, E. A., & Parkhomenko, A. K. (2017a). Organizational and managerial mechanism of interaction between oil and gas producing and service enterprises at the stage of oil wells operation, Economics and Entrepreneurship, 9(1), 899-904.
Krainova, E. A., & Parkhomenko, A. K. (2017b). Process-oriented control of oil drilling, Problems of economics and management of oil and gas complexes, 9, 35-43.
Orekhova, S. V. (2018). Industrial Enterprises: Electronic VS Traditional Business Model, Terra Economicus, 16(4), 77-94.
Orekhova, S. V., & Evseeva, M. V. (2020). Technological systems in economics: a heterodox approach to the institutional framework, Journal of Institutional Research, 12(4), 34-53.
Simchenko, O. L., Grakhov, V. P., Maksimov, K. V., & Chazov, E. L. (2018). Analysis and systematization of the main approaches and methods for assessing the efficiency of an enterprise, Bulletin of the Chelyabinsk State University, 7(417), 104-111.
Tikhanov, E. A., Krivorotov, V. V., & Chepur, P. V. (2016). Analysis and systematization of methods for assessing the competitiveness of an enterprise, Fundamental research, 10(3). 647-651.
Copyright information
This work is licensed under a Creative Commons Attribution-NonCommercial-NoDerivatives 4.0 International License.
About this article
Publication Date
25 September 2021
Article Doi
eBook ISBN
978-1-80296-115-7
Publisher
European Publisher
Volume
116
Print ISBN (optional)
-
Edition Number
1st Edition
Pages
1-2895
Subjects
Economics, social trends, sustainability, modern society, behavioural sciences, education
Cite this article as:
Chazov, E., Simchenko, O., Krivorotov, V., & Kamdina, L. (2021). Reengineering Of Management System Of Oil Production Enterprise Capital Repairs. In I. V. Kovalev, A. A. Voroshilova, & A. S. Budagov (Eds.), Economic and Social Trends for Sustainability of Modern Society (ICEST-II 2021), vol 116. European Proceedings of Social and Behavioural Sciences (pp. 186-198). European Publisher. https://doi.org/10.15405/epsbs.2021.09.02.20