Abstract
The article discusses the feasibility and effectiveness of combining project management tools with the lean manufacturing concept tools. At a large enterprise in the dairy food industry, a lean transformation project has been developed and three types of lean improvements have been implemented based on the classic design approach. The choice of this approach is determined by the limitations associated with the need for a strict sequence of tasks in connection with the industry technological features of production. The project approach to lean transformations made it possible to achieve the goal of optimizing production processes and solving the problem of reducing resource consumption at the enterprise. The effectiveness of the lean transformation project was assessed according to SQCDME indicators (labor safety, product quality, production costs, delivery to the customer or compliance with the production plan, staff motivation, environment), which showed the positive dynamics of most of them: safety, compliance with the production plan, motivation personnel of the project team and the technogenic impact of the enterprise on the environment. A significant economic effect was obtained in terms of production costs. The study showed that the project approach to lean-transformations at the enterprise allows to increase their efficiency and streamline the process of introducing lean-improvements. It is concluded that the combination of project management tools with the tools of the lean manufacturing concept increases the organization of the transition to the desired target state of the enterprise.
Keywords: Designdesign approachlean manufacturinglean transformationsmanufacturing processes
Introduction
Market relations are characterized with a high level of competition, which requires of manufacturers to constantly improve their technologies and management methods in order to ensure high competitiveness and efficiency of modern enterprises, both in the field of technological processes and in management.
The globalization of the economy made it possible to unite local markets into a global world market, where the best global manufacturers of this or that product were determined (Kuznecova & Rud', 2011). The development of their own highly efficient methods, one of which, in particular, is the concept of lean manufacturing, which allows to reduce costs, increase the efficiency of processes and improve the quality of manufactured products (Bazhenov & D'yachkova, 2016), has achieved high performance indicators for world leading companies. And the developed methodology and tools of the project approach allow enterprises to implement the planned initiatives with maximum efficiency (Rahimova & Suetina, 2015). Regardless of the type of concept of building the enterprise’s production system, the project approach to managing its development is universal (Popov & Kalugin, 2015). The project approach has a high degree of adaptability, contributes to the development of innovative activities of enterprises, elimination of unnecessary business processes, effective phased control, interfunctional cooperation between departments, increasing the professionalism of personnel, increasing their motivation and involvement (Backlund, Chronéer, & Sundqvist, 2015).
We believe that combining these two concepts, that is, using the project approach to implement lean transformations, will give a synergistic effect and lead to an increase in the efficiency of applying the lean manufacturing concept at the enterprise, since the project approach will increase the organization of the transition to the desired target state of the enterprise. The difficulties of this transition are related to the novelty and complexity of tasks that no one has previously performed, and the organization of teamwork to solve them (Fomin, Sadovaya, Poleshchuk, & Shivyryalkina, 2017). The application of the project approach for the implementation of Lean transformations at the enterprise when combining project management tools with the lean manufacturing concept tools will increase the efficiency of meeting their deadlines and costs, the quality of control, will allow involving the best employees in lean transformations and streamline the process of introducing lean improvements.
Problem Statement
The study is devoted to the study of the appropriateness of applying the project approach to lean-transformations at the enterprise and evaluating the effectiveness of combining two concepts: Lean Thinking and Project Management. This problem is not sufficiently studied, in contrast to independent research on the effectiveness of the application of the project approach, as well as research in the application of the concept of lean manufacturing.
Research Questions
To assess the appropriateness of applying the project approach to lean-transformations at the enterprise, it is necessary to study issues relating to:
development of a lean transformation project based on Project Management Body Of Knowledge;
implementation of a lean transformation project;
assessment of the feasibility and effectiveness of the application of the project approach to lean-transformations in the enterprise.
Purpose of the Study
The purpose of the study is to study the feasibility of applying the project approach to the implementation of lean-transformations at the enterprise and assess the effectiveness of combining project management tools with the tools of the lean manufacturing concept.
Research Methods
The study uses methods of systemic, logical and situational analysis. Their application allows you to objectively perceive the essential features of the concept of lean manufacturing, tools and lean-transformation models based on the project approach.
The study of the appropriateness of applying the project approach to lean-transformations was carried out at a large enterprise in the dairy industry of the food industry of the Kemerovo region – JSC “Kemerovo Dairy Plant”. It should be noted that this company uses the concept of lean manufacturing, but does not apply the combination of lean-manufacturing and the design approach. The task was to develop and implement lean-transformations of production processes based on the project approach. The technology of milk processing is complex in comparison with other areas of food production, a short cycle of processing of raw materials, and must meet the increased requirements for the quality and competitiveness of its products and the enterprise as a whole. The concept of lean manufacturing does not contradict these goals, and is a powerful tool to achieve them (Starodubceva & Egorov, 2017). The project approach to lean-improvements will contribute to their effective implementation.
For the implementation of lean-transformations, a classical project approach was used, according to Project Management Body of Knowledge (PMBoK). The choice of this approach is determined by the limitations associated with the need for a strict sequence of tasks in connection with the industry technological features of production. The lean transformation project was divided into five stages: initiation, planning, implementation, control and closure of the project (Figure
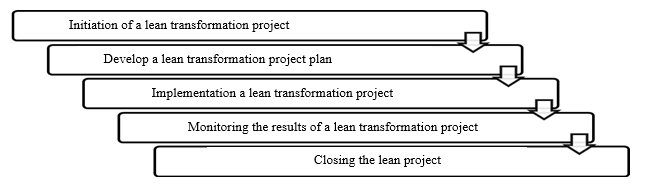
Source: compiled by the authors.
The project approach implies that the transition from stage to stage occurs only at the end of the previous stage of the project, which helps to achieve the goals and objectives of lean-transformations, not allowing them to be left without a solution, unlike the PDCA cycle used at the enterprise (Plan, Do, Check, Act), when at the stage of monitoring the results, in the event of their absence, they again proceed to the first stage – determination of the problem.
At the initiation stage of the lean-improvement project, the task was set to reduce water consumption in the baby food workshop. In this workshop, high water consumption in the production process was revealed, which negatively affected the general goals of the organization, since a high level of water consumption negatively affects, in particular, such performance indicators as costs and environmental impact.
For the development and implementation of the lean-transformation project, an inter-functional project team was created with the involvement of employees, each of whom could contribute to solving problems, determine which actions can be useful for solving. The project team included:
A specialist who owns information about production and equipment, has the authority to start and stop equipment, and is responsible for it, is the operator of the process section.
A specialist who has the ability to make changes to the operation algorithm of the equipment, has the right to change parameters, and is responsible for the correctness of parameter changes, is a software engineer.
The specialist for risk assessment in the process of changing the washing algorithm, responsible for the washing processes, as well as interested in the improvements achieved by optimization, is an optimization engineer.
A specialist in conducting microbiological analyzes to confirm that the changes did not affect the quality of the process is a microbiological engineer.
Thus, an inter-functional project team of specialists was created, consisting of four people, under the guidance of a software engineer. A cross-functional team is created as a small organization for the implementation of projects (Zotov & Muzipov, 2012).
At the planning stage of the lean transformation project to reduce water consumption in the baby food workshop, the following plan was developed:
The definition of processes and equipment on which resource consumption occurs, the allocation of the largest consumers.
Identification of the root causes of high resource consumption.
Listing and implementation of actions to effectively address root causes.
The establishment of new norms of water consumption, corresponding to the target state of the equipment.
Tracking the results and calculating the effect of the implemented lean transforms.
At the stage of the lean project, the project team, according to the project plan, identified the most significant water consumers (Figure
To identify the root causes of high water consumption, the main resource-consuming processes were identified: filling / displacing lines and plants, rinsing after production, automatic washing, disinfection, as well as water consumption for cooling the sterilizer during disinfection and downtime.
From the obtained information on water consumption, only those processes that can be influenced are selected. As a result, the water losses that can be affected are reduced to the following categories:
Losses during automatic washing.
Losses during disinfection or simple installation of ultra-high temperatures.
Losses on lines and plants during rinsing after production.
Reducing each of these types of losses can be considered a sub-task for solving the general problem of reducing water consumption in the workshop. This list of subtasks has been compiled in accordance with the order of importance for optimization based on empirical data on water flow. The highest consumption occurs during washing, therefore, in accordance with the accepted practice of using the Pareto 80/20 rule, the priority task for optimization will be where the greatest resource consumption occurs. The resource consumption in each process was estimated and priorities for work were determined. Data was collected on how much total resources are spent on each of the processes.
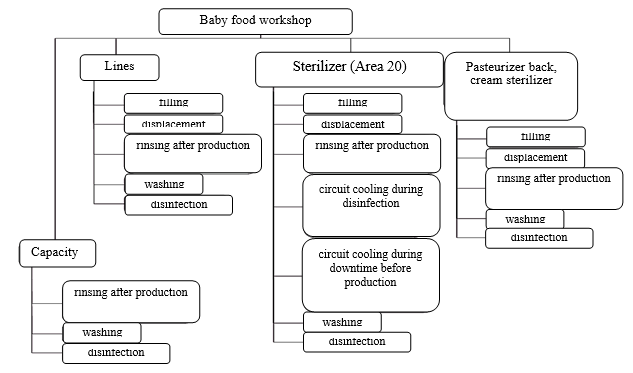
Source: compiled by the authors based on an analysis of the processes of the workshop.
A possible source of losses may be the unoptimized operation of equipment, where operations may be present that do not create value for the final result, but which are the cause of the cost of resources and time. In order to understand whether such operations are present, a method of mapping the flow of value has been applied. The value stream mapping tool, which is widely used in lean manufacturing, has not previously been used in this enterprise. It was this tool that helped identify the root causes of high water consumption.
According to the developed project plan for lean-transformations, a list of actions has been drawn up to effectively address the root causes of high levels of water consumption, which would save a resource without compromising quality:
reduction in primary rinsing;
elimination of intermediate rinsing;
exclusion of final rinse;
the use of recycled water for primary rinsing.
In the process of implementing optimization measures, each object was examined, the necessary analyzes were taken and it was confirmed that these optimization actions do not damage the quality.
Further, according to the project plan, new water consumption standards are established that correspond to the target state of the equipment. It is important to standardize all improvements so that previous mistakes are not repeated (Belysh, 2018).
At the stages of control and closure of the project, the results of the lean-transformation project are tracked and the effect of their implementation is calculated. Comparison with water consumption before optimization showed a reduction in resource consumption by almost five times without loss of quality.
Findings
It is necessary to evaluate how lean-transformations carried out on the basis of the project approach influenced performance indicators. It should be noted that the company uses the concept of lean production, but the problem of reducing water consumption was solved only when using the project approach to lean-transformations. In the field of project management (PM), the concepts of efficiency and effectiveness are commonly used (Sundqvist, Backlund, & Chronéer, 2014). The effectiveness of the lean transformation project was assessed using SQCDME indicators (labor safety, product quality, production costs, delivery to the customer or compliance with the production plan, staff motivation, environment), which are used at the enterprise as part of lean-production. The estimated period is one year.
As a result of the implementation of the project of lean-transformations, three types of lean-improvements were carried out, aimed at reducing the amount of water consumed in the production of baby food in the workshop:
Optimization of water consumption during automatic washing.
Elimination of losses of hot water used for cooling during the disinfection of ultra-high temperature installations.
Optimization of rinse volumes after production on lines and plants.
It is necessary to evaluate how the implementation of the project has affected the performance indicators of SQCDME.
S is security. The impact on safety is not easy to evaluate, since high water consumption is not a risk in itself, but it should be noted that lean is an improvement in safety related to eliminating the loss of hot water that was removed into the drainage, which created an additional risk of burns and impaired visibility in the workshop. Thus, lean-improvement eliminates some of the risks that threaten injuries.
Q is quality. It is shown that the implemented lean-improvements did not adversely affect the quality, which is confirmed by the quality control of processes that were influenced by the introduced improvements. The influence of these lean improvements on quality is neutral.
C is the cost. Costs are one of the indicators that has been most affected.
Data on savings are shown in Table
It is also worth noting that a side effect of reducing the amount of water consumed is the energy savings spent on transporting water. Taking into account the operating time of the pumps, their capacity and percent load, the savings amounted to more than 92 thousand rubles, and the overall economic effect of the introduction of lean-transformations based on the project approach amounted to more than three million rubles.
D is delivery. This ratio shows the timeliness of product delivery to the consumer. The magnitude of this coefficient is influenced with the accuracy of planning, and the more accurately the plan converges with the result, this coefficient is higher. Reducing the time for washing equipment allows you to earlier switch from object to object, which in the general case contributes to accurate synchronization of equipment preparation. This reduces unnecessary organizational costs by waiting for equipment to be released for the next operation. As a result, easier planning and faster completion of supporting processes has a positive effect on improving delivery rates.
M is motivation. This performance indicator gives an idea of how motivated the staff is and a developed corporate culture. As a result of the project approach to lean transformations, an inter-functional project team was formed. This has strengthened cross-functional ties. As a result of applying the project approach to lean transformations, the project team was highly motivated, showed the ability to effectively solve problems and the desire to develop a culture of continuous improvement, adopted at the enterprise.
E is the environment. The indicator includes an assessment of the environmental impact of the enterprise. As a result of the implemented lean-transformation project, the amount of water consumed as a natural resource was optimized, as well as a decrease in electricity consumption, which positively affects the industrial impact of the enterprise on the environment, reducing it. This fact allows us to talk about a more efficient use of resources.
Conclusion
The results obtained allow us to conclude that it is advisable to apply the project approach to the implementation of lean-transformations in the enterprise. The project approach to lean-transformations allowed us to achieve the goal of optimizing production processes, which earlier, in the framework of using the concept of lean manufacturing at the enterprise, was not achieved. It should be noted that the project approach to lean transformations made it possible to find effective ways to solve problems, and the implemented lean improvements did not require any additional investments. The study showed the effectiveness of combining project management tools with the tools of the concept of lean manufacturing. The project approach to lean-transformations increased their efficiency, streamlined the process of introducing lean-improvements, as a result of which production processes were improved and their control improved, the efficiency of resource use was increased, the best employees were involved and motivated, significant savings were obtained. It is shown that the project approach to lean transformations improves the organization of the transition to the desired target state of the enterprise.
References
- Backlund, F., Chronéer, D., & Sundqvist, E. (2015). Maturity assessment: towards continuous improvements for project-based organisations? International Journal of Managing Projects in Business, 8(2), 256-278.
- Bazhenov, G. E., & D'yachkova, A. V. (2016). Problemy vnedreniya koncepcii berezhlivogo proizvodstva na rossijskih predpriyatiyah. Biznes. Obrazovanie. Pravo, 3(36), 14-20. [in Russ.].
- Belysh, K. V. (2018). Kompleksnyj podhod k vnedreniyu i ocenke rezul'tativnosti vnedreniya berezhlivogo proizvodstva na promyshlennom predpriyatii. Vestnik UrFU. Seriya: Ekonomika i upravlenie, 17(5), 751-771. [in Russ.].
- Fomin, A. V., Sadovaya, O. N., Poleshchuk, M. N., & Shivyryalkina, O. S. (2017). Ob organizacii proizvodstva i truda na predpriyatiyah Yaponii. Ugol', 2(1091), 30-33. [in Russ.].
- Kuznecova, T. E., & Rud', V. A. (2011). Faktory effektivnosti i motivy innovacionnoj deyatel'nosti rossijskih promyshlennyh predpriyatij. Forsajt, 5(2), 34-47. [in Russ.].
- Popov, V. L., & Kalugin, S. A. (2015). Upravlenie innovacionnymi proektami pri razvitii proizvodstvennyh sistem. Ekonomika i predprinimatel'stvo. 8-2(61), 617-620. [in Russ.].
- Rahimova, G. S., & Suetina, T. A. (2015). Proektnyj menedzhment kak osnova tekhnicheskoj modernizacii ekonomiki Rossii. Nauchnoe obozrenie, 10(2), 251-254. [in Russ.].
- Starodubceva, O. A., & Egorov, K. D. (2017). Proektnyj podhod kak sredstvo povysheniya effektivnosti deyatel'nosti proizvodstvennoj sistemy. Biznes. Obrazovanie. Pravo, 2(39), 96-101. [in Russ.].
- Sundqvist, E., Backlund, F., & Chronéer, D. (2014). What is project efficiency and effectiveness? Procedia - Social and Behavioral Sciences, 119, 278-287.
- Zotov, F. P., & Muzipov, R. M. (2012). Innovacionnye instrumenty ekonomicheskogo razvitiya predpriyatiya. Ekonomika regiona, 4(32), 191-196. [in Russ.].
Copyright information
This work is licensed under a Creative Commons Attribution-NonCommercial-NoDerivatives 4.0 International License.
About this article
Publication Date
31 December 2019
Article Doi
eBook ISBN
978-1-80296-076-1
Publisher
Future Academy
Volume
77
Print ISBN (optional)
-
Edition Number
1st Edition
Pages
1-1056
Subjects
Industry, industrial studies, project management, sustainability, business, innovation
Cite this article as:
Podzorova*, G. A., Gryaznova, N. L., Egorova, N. M., Behtgold, I. V., & Pleshkova, N. A. (2019). Design Approach To Lean Transformations at The Enterprise. In I. O. Petrovna (Ed.), Project Management in the Regions of Russia, vol 77. European Proceedings of Social and Behavioural Sciences (pp. 687-694). Future Academy. https://doi.org/10.15405/epsbs.2019.12.05.84