Abstract
The implementation of Industrialised Building System (IBS) is highly challenged with fragmentation problems in traditional construction process. The adoption of Building Information Modeling (BIM) in integrated practice is distinguished as an alternative solution that could minimize the problem associated with fragmentation in construction. This research study the impacts of fragmentation issue in IBS projects and assess the awareness and current usage of IBS towards BIM. The study was carried out through the interview session and distribution of questionnaires to contractors listed under the G7, G6 and G5 within Penang region. The main conclusion drawn from the study are that the high rate of fragmentation issue in Malaysian construction industry has resulted in poor quality and low productivity of IBS construction projects and the adoption rate of BIM is still very low in the construction industry due to unawareness of potential benefit of BIM application in construction projects. Hence, these potential factors have been identified which could encourage the acceptance of BIM in integrated practice in order to minimize the fragmentation issue in IBS projects.
Keywords: Industrialised Building System, IBS, Building Information Modelling, BIM fragmentation problem, integrated practice
Introduction
The construction industry is one of the drivers of economic growth of every country. It has shown a significant impact on social, environment and economic of the country. However, the quality of construction environment in Malaysia has been hindered by multiple factors related to material, process or people (Nawi, Azman, Osman, Radzuan, & Yaakob, 2016). The successful adoption of Information Communication Technologies (ICTs) is now emerging within the construction industry due to the increasing awareness of digitalised construction. Industrialised Building System (IBS) is known as technology systems that enhance the construction industry in terms of the effectiveness and productive effort. It is the method of construction which the construction system is built up by using prefabricated components; which are manufactured, transported, arranged and assembled structurally with minimal work at site. The advantages of the application of IBS include improved quality, reduced waste material, increased efficiency and productivity and enhance cost effectiveness (Abedi, Fathi, & Mirasa, 2011).
Building Information Modelling (BIM) is recognised to be among of the powerful tools used in the construction industry. BIM covers all stages of construction ranging from designing, operation management, structural analysis, data management and construction workflow. BIM is adopted by construction contractors in order to enhance the decision-making in planning and organizing the management of construction projects. The idea on the adaptation of BIM in Malaysia has been established by Public Works Department (PWD) since 2007 (Kamar, Hami, & Ismail, 2010). However, it is hardly used in the local construction of Malaysia. This study tends to explore the adoption of BIM in integrated practice in the purpose of expanding the potency of IBS construction.
Problem Statement
Generally, most Industrialised Building System (IBS) project procurement or delivery methods in Malaysia are still based on the traditional approach. As consequences, this traditional approach is then massively criticized as cumbersome for its disintegration approach to deliver projects systematically which resulting failure in forming effective teams’ network among the construction members. (CREAM, 2014).
The fragmentation problem of IBS has impacted Malaysian construction industry greatly through the lack of integrity among teamwork members in design phase, construction stage and production process towards the productivity and efficiency of IBS projects. Such problem as the lack of integrity among relevant players in design stage had caused the requirement to redesign the plan increasing project span time to delay and attributing unnecessary project cost if IBS is adopted (Yeboah-Boateng & Essandoh, 2014).
Disputes always arise due to the misunderstanding between design professionals and contractors. The construction work only begins after the design drawing prepared and completed by design professionals. The projects are carried out in a sequential manner and the construction cannot be commenced prior to the completion of the design. The misunderstanding between the design consultant and contractors causes the design conflict to happen. Meanwhile, the separation process between design and construction also caused lack of coordination in the project (Latiffi, Mohd, Kasim, & Fathi, 2013). It causes poor communication between the design consultants and contractors. This is because all the project works are carried out individually rather than as a team. The coordination problem will arise when each trade contractors have not scheduled appropriately.
Normally, the construction process is carried in a sequential manner that only begin after the design which causes the project works to be incomplete within the project period. This will cause the cost of the project increase and cost overrun. Besides, the design and construction that are not complete perfectly may cause high probability of rework (Nawi, Haron, Hamid, Kamar, & Baharuddin, 2014). Moreover, the design and construction error also cause rework in the projects, whereby sometimes the projects time allocated is prolonged and delayed as consequences and it took longer than the construction time phase during the rework.
All the decision making for each stage of the project may cause time-consuming. Thus, the projects always fall behind the timetable. Uncontrolled rework and wastage affect the performance of the construction (Kamar et al., 2010). As a result, IBS system produces a low productivity and efficiency construction work.
Research Questions
The Integrated Project Delivery (IPD) is considered as a new project delivery method which involves the integrated project team such as designer, owner, contractor work together from the initial design stage until the project handover (Nawi, Nadarajan, Omar, Zaidi, & Yasin, 2014). Architect, engineer, designer, developer, contractor and owner will collaborate more closely and effectively towards a successful project delivery. Fragmentation problem in IBS project is due to the separation in the process of design and construction stage. Thus, a high effective collaboration and information sharing among the project team is crucial in project delivery (Wasfy, 2010). According Eastman, Teicholz, Sacks, and Liston, (2008), IPD with the utilisation of Building Information Modelling (BIM) could improve the traditional fragmented construction process (Ajayi, & Oyeyipo, 2015). The principle of early involvement of Integrated Project Delivery allows the concurrent processes to integrate the people, business structures, systems and practices based from The American Institute of Architects Integrated Project Delivery: A Guide Version 1 (Integrated practice in perspective, 2007). Therefore, it can reduce wastage and optimise efficiency through all phase of the project. As a result, the issue of lack of integration and collaboration existing in IBS projects can be overcome. Through the integrated practice, project stakeholders do not require to spend time on conveying certain information of documentation in the traditional design process (Kenig, Allison, & Black, 2010). This can save a lot of time and money in IBS projects. Therefore, the weakness of current IBS projects in Malaysia can be improved by the integrated practice of BIM, making the IBS project delivery process more effective and efficient.
Purpose of the Study
The objective of this study is to examine the impacts of fragmentation issue in IBS projects, to assess the awareness and current use of IBS towards BIM as well as to identify the potential factor that could encourage the adoption of BIM in integrated practice.
Research Methods
In the present study, questionnaire survey was used to collect the relevant supportive information. Out of 188 questionnaires sent out, 104 were received. The data analysis is carried out by using MS Excel and IBM SPSS Statistics 20. The data collected were presented based on the outcome of the statistical analysis such as frequencies, average index, Relative Important Index (RII) and rank. The use of A.I. is to determine the average response of the respondents. A five-point scale of 1 to 5 was adopted to show priority.
Findings
Respondent profile
The respondents are contractors registered in Construction Industry Development Board (CIDB) of grade G7, G6 and G5. The grade indicates the limit of tender value of RM 5,000,000 for G5, RM 10,000,000 for G6 and limitless for G7. The region of the listed contractors only concentrates within Penang, one of the northern states in Malaysia. Out of the 104 sets of questionnaires that were received, the background of the respondents were quantity surveyors (30.8%), followed by engineer (20.2%), architect (18.3%), contractor (15.4%), project manager (7.7%) and others (7.7%). Most of the respondents were degree holders (56.7%) and only 3.8% of them were certificate holders (3.8%). In terms of experience, about 40.4% from the respondents have 5-10 years working experience and only 5.8% for respondents were above than 15 years working experience. Most of the respondents were listed under G7 IBS contractor firm (64.4%) with larger organization which has more than 20 employees (50.0%).
Fragmentation Issue in IBS Projects
Based on the result from Figure 1, it can be concluded that the rate of fragmentation issue in Malaysian construction industry is very high which has resulted in poor quality and low productivity of IBS construction.
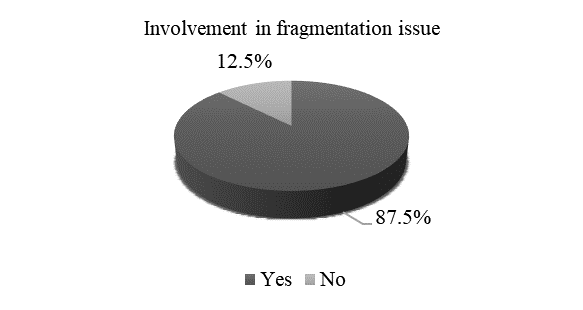
Table 1 shows the results of the responses to the impact of fragmentation issue in IBS construction. The average index values (AI) of these variables indicated that the responds to the fragmentation issue in IBS projects. From the Relative Importance Index (RII) and overall ranking for impact of fragmentation issue in Table 1, it shows that the adoption of traditional procurement approach in construction projects has caused the lack of integration between contractors and designers.
Awareness and Current Uses of BIM in Malaysia
From the analysis, it shows that most of the construction professionals have least aware on the awareness of BIM and its application. This would contribute the reasons why the acceptance rate of BIM in Malaysia is still low although Malaysia government has provided BIM training to the construction industry. The awareness of BIM was divided into four stages as shown in Table 2. In these stages, the most aware stage is during the feasibility stage (RII = 0.425). The least aware stage is during the in-use and the maintenance stage (RII = 0.345).
Table 3 shows the result of the respondents to the awareness of BIM application. The average index values of these variables indicated that the respondents only have slightly awareness of BIM application. According to the data analysis, able to quantify every element and generate Bills of Quantities automatically (RII = 0.486) and able to reduce construction wastage and construction period (RII = 0.486) are the most aware element of BIM application. The role of quantity surveyors in taking off quantities to produce a bill of quantities indicated that they have more understanding towards the BIM application since quantity surveyors represent a large number of the respondents in this study.
Figure 2 shows the involvement of respondent in BIM projects. From the figure, only 4.8% of respondent was involved in BIM projects and almost all of the respondents have never been involved in BIM projects. This may be due to unawareness on the potential benefit of BIM application in the construction projects.
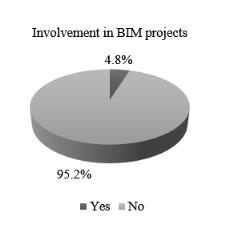
Potential Factor that could encourage the Adoption of BIM in Integrated Practice
Table 4 shows the perception of respondents on the potential factor that could encourage the adoption of BIM in integrated practice. The average index values (AI) indicates that the respondents agreed that the potential factor that could encourage the adoption of BIM. The findings show that it has a high potential of BIM implementation in construction industry as it can solve fragmentation issue of IBS construction. According to the data analysis, reduce design-related issues during construction phase such as constructability, rework and wastage (RII = 0.916) are the most potential factor to encourage the adoption of BIM application.
Conclusion
The objective of this research is to explore the adoption of BIM in IBS construction. From the finding of the study, it can be concluded that:
- The rate of fragmentation problem in Malaysian construction’s industry is very high which needs attention and serious effort to ensure productivity and efficiency of IBS construction.
- The major impact of fragmentation issue in IBS construction are experienced by the lack of integrity between team network between designers and the contractors, follow by design disputes, omission and errors and changes of design.
- Majority of the construction industry has low level of awareness and uses towards BIM although Malaysia government has provided BIM training courses to make establishment of BIM trending in the recent construction’s industry.
- The ability to reduce design-related issues during construction phase such as constructability, rework and wastage, enhance communication between parties in the Architecture, Engineer and Construction (AEC) industry and reduce construction cost and time are the most potential influences that could encourage the acceptance of BIM in IBS construction.
Acknowledgments
The authors would like to acknowledge and thanks for the support to the Ministry of Education, Malaysia (FRGS-203/PPBGN/6711449, ‘Understanding the Behaviour of Industrialised Building System Panel Connection Using Finite Element Analysis), Universiti Sains Malaysia.
References
Abedi, M., Fathi, M. S., & Mirasa, A. K. (2011). Establishment and development of IBS in Malaysia. Sustainable Building and Infrastructure Systems: Our Future Today, 405.
Ajayi, O., & Oyeyipo, O. (2015). Effect of Rework on Project Performance in Building Project in Nigeria. International Journal of Engineering Research & Technology (IJERT), 4(2), 294-300.
Construction Research Institute of Malaysia (CREAM). (2014). Issues and Challenges in Implementing BIM For SME's in the Construction Industry. Malaysia. Construction Research Institute of Malaysia (CREAM).
Eastman, C., Teicholz, P., Sacks, R., & Liston, K. (2008). BIM Handbook: A Guide to Building Information Modelling for Owner, Managers, Designers, Engineers, and Contractors. New Jersey: John Wiley and Sons, Inc.
Integrated practice in perspective: (2007). A new model for the architectural profession. Architectural Record, May, 2007.The American Institute of Architects Integrated Project Delivery: A Guide Version 1.
Kamar, K. A. M., Hami, Z. A., & Ismail, Z. (2010). Modernising the Malaysian Construction Industry through the Adoption of Industrialised Building System (IBS). The Sixth International Conference On Multi£National Joint Ventures For Construction Works Kyoto, 1-14.
Kenig, M., Allison, M., & Black, B. (2010). Integrated Project Delivery for Public and Private Owners. National Association of State Facilities Administrators (NASFA), Construction Owners Association of America (COAA), The Association of Higher Education Facilities Officers (APPA), Associated General Contractors of America (AGC) and American Institute of Architects (AIA).
Latiffi, A. A., Mohd, S., Kasim, N., & Fathi, M. S. (2013). Building information modeling (BIM) application in Malaysian construction industry. International Journal of Construction Engineering and Management, 2(4A), 1-6.
Nawi, M. N. M., Azman, M. N. A., Osman, W. N., Radzuan, K., & Yaakob, M. (2016). Key success factors for team integration practice in Malaysia Industrialised Building System (IBS) construction industry. Themed issued on technological, vocational and educational empowerment of Malaysia’s human resource. GEOGRAFIA Online TM Malaysian Journal of Society and Space 12(3), 88-94.
Nawi, M. N. M., Haron. A.T., Hamid, Z. A., Kamar, K. A. M., & Baharuddin, Y. (2014). Improving Integrated Practice through Building Information Modeling-Integrated Project Delivery (BIM-IPD) for Malaysian Industrialised Building System (IBS) Construction Projects. Malaysia Construction Research Journal (MCRJ), 15(2).
Nawi, M. N. M, Nadarajan, S., Omar, M. F., Zaidi, M. A., & Yasin, M. F. M. (2014). Towards Integrated Team Practice: A Case of Malaysian Industrialised Building System (IBS) Construction Projects. EDP Sciences, E3S Web Conferences 3.
Wasfy, M. A. F. (2010). Severity and Impact of Rework, A Case Study of A Residential Commercial Tower Project in the Eastern Province-KSA. Master Thesis, King Fahd University of Petroleum & Minerals Dhahran, Saudi Arabia.
Yeboah-Boateng, E. O., & Essandoh, K. A. (2014). Factors Influencing the Adoption of Cloud Computing by Small and Medium Enterprises (SMEs) in Developing Economies. International Journal of Emerging Science and Engineering (IJESE), 2(4), 13-20.
Copyright information
This work is licensed under a Creative Commons Attribution-NonCommercial-NoDerivatives 4.0 International License.
About this article
Publication Date
26 December 2017
Article Doi
eBook ISBN
978-1-80296-950-4
Publisher
Future Academy
Volume
2
Print ISBN (optional)
-
Edition Number
1st Edition
Pages
1-882
Subjects
Technology, smart cities, digital construction, industrial revolution 4.0, wellbeing & social resilience, economic resilience, environmental resilience
Cite this article as:
Shan, T. Y., Shukri, S., & Taib*, M. (2017). Improvising Industrialised Building System Through the Adoption of Building Information Modeling. In P. A. J. Wahid, P. I. D. A. Aziz Abdul Samad, P. D. S. Sheikh Ahmad, & A. P. D. P. Pujinda (Eds.), Carving The Future Built Environment: Environmental, Economic And Social Resilience, vol 2. European Proceedings of Multidisciplinary Sciences (pp. 26-33). Future Academy. https://doi.org/10.15405/epms.2019.12.3