Abstract
The issue of allocating human resources costs in a realistic manner to products, processes, activities and individual employees has been an issue of research and practice in the field of accounting during the last two decades. The major problem is that the cost of calculating human resources costs has proven to be very high in the vast majority of cases. Also, in the vast majority of approaches the validity of the calculation of time allocated to resource usage has been questioned putting costing estimations in doubt. Approaches like activity based costing have been enhanced by incorporating the element of Time and led to the creation of the so called Time Driven activity based costing approaches. However, even these approaches are depended on the calculations of unit costs of time usage per resource and in the majority of cases have also been questioned if unit costs have been calculated correctly and also if the time allocated to individual employees per activity are realistic. Our research presented in this paper proposes the use of a process mining approach for human resource cost estimations based on data-records captured in event logs that enhances existing Time Driven activity based costing approaches.
Keywords: Activity based costing, event logs, effort based costing, full time equivalents, human resources accounting, time driven activity based costing process mining
Introduction
The pace of rapid changes caused by the globalized economy and the changing customer requirements have forced companies to focus even more on their human resources (HR) in their effort to become adaptable to these constantly changing conditions (Vultur, 2018). The HR asset is, however, the far more complex in terms of accounting estimations (Monday, 2017; Nielsen, 2017). Allocating HR costs is one of the most difficult tasks in organizations (Vultur, 2018).
Management accounting approaches have addressed and elaborated on the issue (Heshmat et al., 2015). Traditional methods of costing, proved to be unable to associate costs to activities (Kaplan & Anderson, 2003). To overcome the issue researchers focused on the development of more sophisticated cost systems, such as Activity Based Costing (ABC) that allocates resource usage costs to activities, cost centers, products or services and to the overall profitability of the enterprise (Chea, 2011).
One of the resource costs types allocated to activities are the HR costs. However, there is a lot of criticism in the last decade on the validity of resource allocation in ABC that affects the accuracy of cost estimations. One of the approaches developed to assist in more accurate cost allocation in ABC is the Resource Consumption Accounting (Wegmann, 2019). Resource Consumption Accounting has proved to be a useful approach in developing cost allocation scenarios but does not by any means provide real time monitoring of activity costs (Heshmat et al., 2015).
The issue of the use of time in resource usage cost allocations has become a research focus area in ABC approaches. In the vast majority of approaches, the use of time of resource usage is estimated subjectively or approximately causing many criticisms on the final costing estimations (Kaplan & Anderson, 2003). This led researchers to propose the Time Driven ABC approach that enhances traditional ABC approaches by calculating resource usage costs more accurately based on the multiplication of the execution time of a transaction or activity with the unit cost of each resource used per time unit. However, Time Driven ABC does not by any means provide real time monitoring of activity costs or provides by any means actual costing or reorganization scenarios based on real time data.
As a solution to the aforementioned limitations of ABC, RCA and Time Driven ABC systems our research presented in this paper proposes the use of a Process Mining based approach. Process mining analyzes event logs or repositories that capture records about the execution of an activity. Each event contains useful information about the duration of the activity, the person that executed it and some of the resources used during the activity (Aalst & Medeiros, 2005).
The aim of our research presented is this paper is encapsulated in the following research objective: To propose an enhanced Process Mining Approach for HRM Cost Estimations in Time Driven ABC Costing.
In order to address the research objective our research addresses a series of research questions:
Q1: What is the state of the art in resource usage cost allocation in ABC, RCA and Time Driven ABC approaches?
Q2: What are the limitations of existing, ABC, RCA and Time Driven ABC approaches in allocating HRM costs?
Q3: How can we extract HRM costing related data from event logs?
Q4: How can we calculate HRM effort from event logs
Q5: How can we calculate HRM costing per employee activity and process?
Q6: What should an integrated Process Mining based ABC costing model should be composed of?
In order to provide answers to the aforementioned research questions in section 2 we resent a literature survey of ABC, RCA and Time Driven ABC with an analysis of the most relevant literature in these three areas. In section 3 we analyze the process mining literature. Emphasis is put on event logs and approaches for extracting information related to accounting resources and costing with special attention to HRM costing. In chapter 4 we propose a novel approach for HRM cost calculation utilizing the theory of effort based costing. In section 5 we propose and Integrated Costing System for process mining based ABC costing. Both the process mining event log based effort based HRM costing approach and the Integrated Costing System proposed constitute the two major contributions of our research.
Management Accounting Activity Cost Calculation
The most important problem faced by businesses over time is the estimation of profit, i.e. the ratio of the cost of production of goods or services against their selling price (calculation of actual costs). This is the reason for the ever-increasing interest of scientists and enterprises towards a reduction in overheads, which are created as the complexity of the economic environment increases, due to developments and constant changes in globalized markets (Berliner & Brimson, 1988; Cooper & Kaplan, 1988), which led to the design and development of a variety of cost accounting management methods such as: Activity Basic Costing, RCA, Time-Based Costing (TDABC) and ABC Light Costing System (Heshmat et al., 2015).
Activity Based Costing – ABC
Since the 70s, when American industrialists used a cost accounting system for recording the cost of the volume of production and the cost of their products, depending on the necessary activities, they essentially created a potential method of Activity Basic Costing (ABC). However, the cost management strategy is considered by scientists to be the forerunner of Activity Based Costing, which made its appearance in the 1980s, a time when the complexity of management was leading to ever higher overhead and procedural costs, thus pushing researchers to design its foundations (Wegmann, 2019).
The design and development of an integrated Activity-Based Costing system was finally achieved by Harvard Business School professors, Robert Kaplan and Robin Cooper in 1988 (Oseifuah, 2014). The above researchers, with their fundamental work on accounting management practices and strategy-based accounting developments, highlighted the importance of accounting management, while laying the foundations of ABC. At the same time, looking for the accounting management methods themselves that could interpret the decision in the process, they first proposed an in-depth analysis of the processes and activities and then a close link between operational and strategic management, which was the reason for the design of the strategically oriented ABC (Wegmann, 2019).
While since the early 1980s there has been an interest in accounting management strategy, with many scholars promoting the benefits of this method (Wegmann, 2019), in the 1990s, however, ABC was recognized as a timely and reliable method of informing the factors that influence costs and guide management in rational decision-making (Ferdows et al., 1986). In 1989 in particular, a functional model of confrontational environmental analysis and analysis of internal processes through ABC was developed by Shank and Govindarajan who proposed the integration of supplier and customer dimensions into the cost allocation system. Over the years, in many cases businesses, in order to manage their costs, have essentially experimented with ABC-based tools (Wegmann, 2019).
In the international literature, several definitions have been developed concerning Activity-Based Costing. According to a broad definition, 'Activity-Based Costing' is considered to be the method of measuring the costs and performance of activities as well as of the cost carriers. ABC first assigns costs to resource use activities and then to resource-using operators. It focuses on the extraction of information on the real costs of products and services, activities and processes, distribution networks, works and contracts, thus contributing to the identification of any problems and the development of harmless routes to opportunities and solutions (Wegmann, 2019).
According to Glykas et al. (2018), ABC is defined as a "costing approach that focuses on individual activities as fundamental carriers of costs. It uses the cost of these activities as a basis for allocating costs to other items – cost carriers, such as products or services." While for Sezenias et al., (2013), the activity-based costing system is defined as the method that allocates all direct and indirect costs per activity and allocates the costs of activity to the products, with the help of the relevant cost guide (Sezenias et al., 2013).
It is an innovative method of activity-based cost accounting, devised by Kaplan and Cooper in 1988, in order to overcome the difficulties identified in the conventional method of accounting management, i.e. the conflict between strategic management procedures and management and operational control which led to a weakness in their coordination (Johnson & Kaplan, 2002). In order to overcome this difficulty, the theory of accounting management strategy, which includes a set of practices, has been devised. A strategy of the accounting management tool, connects marketing decisions and strategies with business decisions and creates a multidimensional approach to performance. There are hidden factors affecting General Industrial Costs, which should be allocated in a way that will facilitate control and increase production and administrative efficiency (Wegmann, 2019).
The concept of accounting management strategy has been studied in depth over the years by many researchers, most recently Smith (2017), who studied the concept in a new way, linking it to a more comprehensive frame of reference. The cost management strategy is a dimension of accounting management strategy, dedicated to cost management in relation to the strategy and is the forerunner of ABC.
There are three methods of approaching it: the restrictive one, where cost management examines the range of strategic options and the control of strategic assumptions (repressive). The intermediate way, where cost management validates strategic assumptions, requiring more detailed analysis of strategic assumptions, constituting a more dynamic approach. Finally, the broad approach, in which costing is a fundamental part of the strategy and according to it, cost management should be interactive (Wegmann, 2019).
Cost management can be defined as a set of measures implemented by the management in order to ensure the satisfaction of its customers while limiting and controlling its production costs. The cost management system emphasizes on the cost management of the business activities and focuses on the perception that businesses should have when supplying comprehensive and smart pricing plans and compliance at competitive prices. Therefore, cost management requires the use of accounting tools and techniques such as ABC (Heshmat et al., 2015).
ABC is considered to be a sensitive cost system, which allows the classification of direct costs, the expansion of the number of indirect cost groups and finally identifies the cost drivers, i.e. it favors a better distribution of costs, using smaller cost groups called activities. At the heart of the method is a sophisticated cost assignment approach, which assigns resources to activities and then costs to cost items. The cost of activities is considered the basis for sharing costs into products or services (Heshmat et al., 2015; Wegmann, 2019). It classifies into five main categories the activities that are not exclusively related to the way of production of several units as opposed to the traditional cost estimation systems that depend on the measurement of volume (such as hours of direct work, hours of operation of a machine) for the distribution of the general and indirect costs to the final products. These categories include activity: at the unit level, at the batch level, at the customer level, the business activity and the activity at the product level (Kenton, 2022).
The most important role of the cost driver as a variable that interprets cost utilization and describes value chains is the link between operational and strategic management. At the heart of the ABC is a process approach, with the enterprise seen as a network of flat, horizontal and vertical structures where activities depend on market requirements. Its initial objective was to improve the deception in overhead allocations at the design stage of an ABC system, in order to counter the inaccurate American costing standard. Very quickly, as various researchers point out, ABC took on administrative (activity-based management) and strategic dimensions, others again emphasized the connection between ABC and strategic cost management theory (Wegmann, 2019). The cost of activity guides (as a component of the business) provide a more accurate determination of the actual cost of the business activity, since they take into account the indirect costs used in the cost accounting process (Kenton, 2022).
ABC recognizes the direct relationships between the activities, the cost of resources, cost drivers and cost carriers when carrying out their assignment first to the activities and then to the entities, as illustrated schematically in Figure 1 (Jeyaraj, 2015).
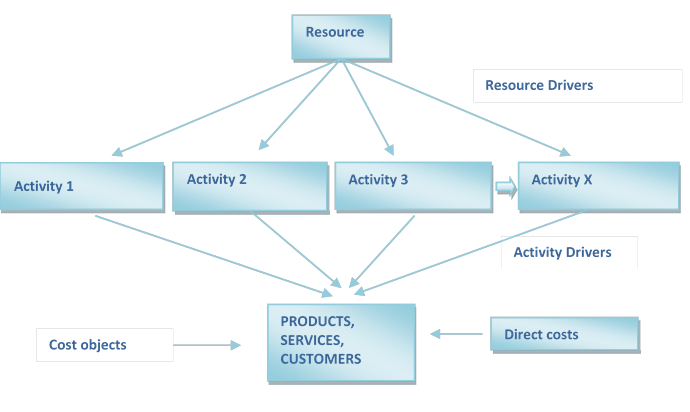
This method is based on the activities and as activities are taken any events that are a cost factor, tasks with a specific objective or units of work, such as the design of the products, the installation or operation of the production machines and the distribution of finished products. The resources consumed by the activities are items of cost. As a cost guide is considered an activity such as for example the settings of machines, orders, etc. The total cost divided by the cost factor is the percentage of guide costs and is used to calculate the value of overheads and indirect costs related to a particular activity. It is a method of better cost allocation, thus allowing businesses to formulate the optimal pricing policy. It is used for product costing, target costing, customer profitability analysis, product line profitability analysis and service pricing, allowing businesses to formulate the appropriate pricing policy. Activity measures are divided into two categories, duration drivers (they measure the required time to complete an activity) and transaction drivers (count the frequency of occurrence of an activity) (Kenton, 2022).
ABC is the method that assigns overhead and indirect costs (e.g. wages, utilities) to services and products. The ABC costing system is mainly applied to processing industries, as it enhances the reliability of cost data, i.e. produces the real costs and enhances the better classification of the costs that burden the production process.
This method recognizes the relationship between costs and overheads and final products, thus allocating indirect costs to products less arbitrarily, although costs such as management salaries are difficult to apportion. This method expands the number of cost groups that can be used in the analysis of overheads and makes it detectable indirect costs in some activities, thus enhancing the cost accounting process in three ways. It expands the number of cost groups that can be used to accumulate overheads, i.e. instead of concentrating all the costs on one group in the economic unit, the cost per activity accumulates. In addition, it creates new bases for the distribution of overheads to products so that the cost, instead of volume sizes (hours of machines, direct labor costs) is distributed on the basis of activities. It differentiates the nature of several indirect costs (depreciation, utilities, wages), making them detectable in some activities. In addition, it transfers the overheads of high-volume products to those with a small volume, increasing the unit cost of these (Kenton, 2022).
Cost accounting is a form of administrative accounting that aims to collect and capture the total cost of production of an organization, calculating fixed and variable costs. Overhead operating expenses, in addition, are the fixed costs that are allocated to a particular task or part of an organization. While a cost pool is called a group of costs of activities derived from the sum of all the costs related to the performance of a certain task. Part of the costing is also the process of analyzing an activity driver that evaluates and determines the factors involved in the costing of services or products and finally, the overhead factor refers to the costs that are not directly related to production (overheads), but are allocated to the production of a service or good (Kenton, 2022).
Activity-based costing is therefore based on basic costing concepts such as:,,, and (Kenton, 2022; Wegmann, 2019).
include all available animate and inanimate elements that an organization has in order to operate. Alternatively, the ability to execute a project can be characterized as a resource, since it includes all the means consumed by various tasks – activities, such as salaries, raw and auxiliary materials, etc. (Hashim, 2015).
An is a transaction, event or transaction that uses an organization's resources to produce products or services, creating costs. The products also consume activities. Construction costs in products can be determined directly and with relative accuracy, after determining the value of the resource consumed in an activity and the value of the activity spent on the production of a product (Dhubea & Al-Riami, 2017).
A, on the other hand, is a product or part of which costs are measured or accumulated. A product for example is a cost carrier for direct labor, general industrial costs and direct materials. In addition, the maintenance department of an industry can be considered a cost carrier because they accumulate in this cost of maintenance supplies and the costs of its employees. The total costs of this section will then be allocated to the final products, which are carriers of costs. A machine, a customer, a group of employees or machinery, etc. can also be considered as a cost carrier (Bragg, 2022).
are the mechanisms that link cost carriers to the cost of activities. In other words, they transfer the costs from the various activities to the respective cost carriers. They are associated either with the duration of an activity (time-duration guides), or with transactions, i.e. directly intertwined with the frequency (frequency guides), since they are an estimate of the repetitions of a transaction. Cost guides can be characterized as: material orders, machine settings, production orders, spent energy, quality inspections, maintenance requests, operating hours of machines, numbers of shipments, energy consumed, distance travelled (Glykas, 2011). They divided into activity drivers, the links between cost and cost of activity carriers and resource drivers, which are the basis for finding cost drivers (Kumar & Mahto, 2013). The cost guide factor used to calculate the amount of overheads and indirect costs in the activity-based costing process is derived from total cost quotient with the cost guide of the specific activity (Kenton, 2022).
Finally, are called groups of individual costs, per center or service department, of an institution. In other words, they constitute the sum of the cost elements of a group of activities related to each other. They are used for the distribution of General Industrial Expenses to the production units. A cost reservoir, for example, can be the movement of materials in a unit, which is an activity with many individual activities such as transportation, loading, counting, etc. (Bragg, 2022). The role played by the above concepts in the operation of an ABC system is schematically depicted as follows (Figure 2):
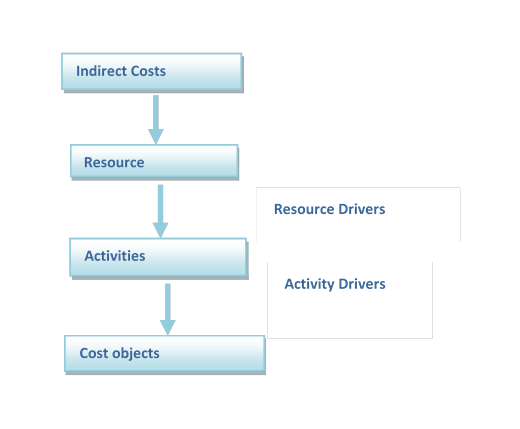
However, the steps of activity-based costing are the following: a) identification of all activities required for the production of a product, b) division of activities into cost groups, including all individual costs related to the activity, c) calculation of overheads for each group of costs, d) allocation of guide activity costs for each cost group (units or hours), (e) calculation of the cost driver rate (division of the total overheads in each group of costs by the total cost guides), (g) multiplication of the number of cost drivers by the percentage of the cost driver (Kenton, 2022).
In a numerical example of activity-based costing, we assume that the annual electricity consumption (which is directly affected by the working hours) amounts to 50.000,00 € and it took 2,500 hours of work, then the price of the cost driver will result from the ratio of 50.000 €/ 2.500 hours = 20 €. If for the X product the company consumes 10 hours of electricity, then the overhead costs of product X will be 20 € x10 hours = 200 € (Kenton, 2022).
According to ABC's basic philosophy, all business activities exist to support the operation of production and then the distribution of the products or services produced, therefore the cost of all operations is also the cost of the final product (Cooper & Kaplan, 1988).
In conclusion, ABC can be considered a sophisticated two-stage cost method, the foundation of modern industrial costing systems and the calculation of the cost of each product to determine its selling price. In traditional cost accounting, costs are allocated according to the volume of production of products, while in ABC the direct consumers of costs are considered to be the activities and not the final products or services, since the activity is considered the main cost factor (Figure 3). The ABC system, unlike traditional accounting management systems, provides: accurate calculation of the cost and selling price of products, elimination of unnecessary activities, improvement of production processes, identification of value-added activities and subsequent elimination of useless activities, identification of cost factors, planning of operations and definition of business strategy as well as proper measurement of performance (Heshmat et al., 2015).
ABC systems therefore lead to an increase in the value of the business, because through their use the cost of inefficient processes can be determined and the amount of the savings resulting from the improved methods can be identified and measured. In addition, the redesign of systems using effective processes reduces costs and enhances product quality and thus the competitiveness of the business (Heshmat et al., 2015).
ABC systems therefore lead to an increase in the value of the business, because through their use the cost of inefficient processes can be determined and the amount of the savings resulting from the improved methods can be identified and measured. In addition, the redesign of systems using effective processes reduces costs and enhances product quality and thus the competitiveness of the business (Heshmat et al., 2015).
Figure 3 Schematically illustrates the stages of an ABC system.
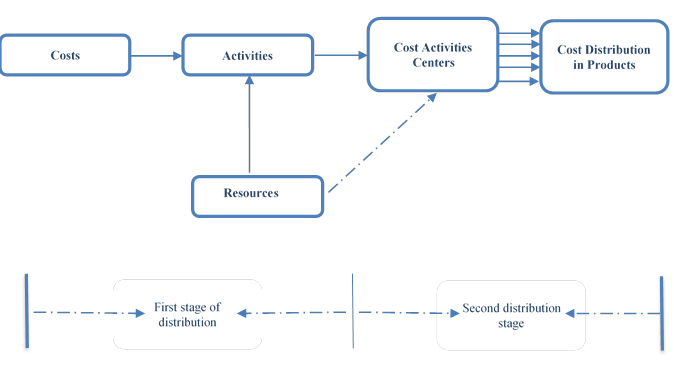
Resource Consumption Accounting (RCA)
Some researchers, based on the views of ABC critics, developed the Method of Resource Consumption Accounting in an effort to improve ABC in the resource allocation process (Wegmann, 2019). The RCA focuses on the manager (not the external financial situation) as the main user of the information and is mainly based on German accounting methods. This method incorporates the experience for the ABC, the Theory of constraints (TOC) and the traditional accounting theory (White, 2009). The RCA follows a streamlined process of allocating resources to activities and statistical methods, by correlating resource consumption with activities and cost guides (Wegmann, 2019).
RCA is the recent development in accounting and management. It was introduced with a series of articles by Anton van late Miró and developed by the Association of Accounting Resources, however there is no reliable data on its use in enterprises. It is based on GPK costing, which has been successfully used for more than 60 years in German businesses. The GPK cost accounting system emphasizes the true value of the resources a company has to produce a particular product, trying to determine as best as possible, the actual flow between resources and between resources and products, thus preventing any unreasonable allocation. It is considered a high-precision costing system and often consists of hundreds or more cost and price tanks. The RCA system essentially combines the GPK and the ABC systems (Heshmat et al., 2015).
A key feature of the RCA system is the monitoring of the primary and secondary costs per tank and the calculation separately of the variable (adjusted) and fixed costs. The size of such a system (in relation to the number of connectors) exceeds that of the ABC, making it more costly. Also, updating such a system, due to the large number of connections, becomes much more demanding. The RCA system identifies the grouped costs at different levels of the cost object. For example, it allows the enterprise to determine the final cost of a decision at the product level, by grouping costs based on production lines or similarity and allowing to determine the final costs attributed to decisions. Property devoid of an ABC system (Heshmat et al., 2015).
On the other hand, is disadvantaged compared to ABC in monitoring the cost of activity (it does not take this into account), because the product is a virtual resource consumption analysis unit and not the entire business unit (Heshmat et al., 2015).
Time – Driven Activity Based Costing – TDABC
Another simplified ABC method, offered for services and simplified processes, is Time-Driven Activity Based Costing (TDABC) (Wegmann, 2019).
The difficulty of implementing Activity Basic Costing (ABC) in many enterprises, due to: the high cost required by personalized research, the use of subjective and costly time allocations, as well as the difficulty in updating and adapting the model to add new activities (changing procedures and resource costs and increasing the diversity and complexity of individual orders, channels and customers), led researchers to study another time-based costing system (Kaplan & Anderson, 2003). Time Driven Activity Based Costing addresses these difficulties by using time equations to explain variations in time requirements generated by different types of transactions and uses the duration driver as the the time-based ABC estimates only two parameters: the required execution time of a transaction or activity and the unit cost of the capacity provided. The advantages of time-based ABC are: the rapid installation and estimation, its easy updating (adaptation) to reflect the diversity of orders, changes in processes and resource costs, the ability to feed data from transaction CRM and ERP systems, the explicit integration of resource capacity and the identification of unused practical ability that can be exploited, the ability to confirm the estimates of the model for unit times with direct observation, the exploitation of time equations that include fluctuations in customer behavior and orders without becoming even more complicated as a model, and the ability to easily scale in order to process a multitude of transactions, while continuing to produce fast and real-time reports and processing times (Kaplan & Anderson, 2003).
Activity-based costing, as mentioned above, was introduced in the mid-1980s after many surveys, which had a common feature and different parameters in each case. The determination of the costs assigned to each activity was determined by the interviews and time recordings, as well as the direct observation of the percentage or amount of time spent by individuals on the various activities. The cost, for example, of storing products, will be channeled to activities such as inspection, receipt and installation and then, receipt, packaging and shipment, based on the percentage of time spent on each activity, according to the estimates of the warehouse employees. The activity cost guide rates applied to the assignment of activity costs to each individual product or customer are calculated and the activity costs are divided by the outputs of each activity (e.g. number of inspections, number of items, number of shipments and number of receipts). The process of estimating an ABC model can be applied at an initial (pilot) stage of study, but it becomes difficult and costly to implement it throughout the organization. Moreover, updating the model with the changes in the company's operations, after its initial construction, requires in essence, re-assessments through interviews and surveys, with the result that in a short period of time, the cost estimates of these models become obsolete. These disadvantages of ABC led the researchers to a simpler and more accurate, time-driven approach that allows for greater heterogeneity in orders, activities and customer behaviors, without burdensome requirements for calculating the cost of activities, products and customers (Kaplan & Anderson, 2003).
Activity-based costing is an alternative approach to estimating an ABC model that addresses all its limitations and is called an activity-based chrono cost (Time-Driven ABC-TDABC). This approach was based on the article by Robin Cooper, who formulated the difference between transaction costs and effort costs guides, with transaction cost guides measuring how many times an activity is performed (e.g. number of shipments, number of settings, number of production series, number of orders, etc.). The resources required to perform each form of activity differ, in that the way some customer orders that require more time and processing are handled than others differs, or some settings are more complex and complex than others, in these cases it is measured how many times an activity is performed that gives an inaccurate estimate of the required resources of its completion (Kaplan & Anderson, 2003).
The benefits of TDABC according to Kaplan and Anderson (2003), are as follows: a) the ease and speed in the construction of such an accurate model, b) the compatibility of data with the resource planning and customer management systems, c) the passing on of costs to transactions and orders using the details of orders, processes, suppliers and customers, d) the possibility of its monthly implementation, showing the financial situation of the organizational operation, e) the transparency it creates in the utilization of the capacity and efficiency of the processes, f) the forecasting of the demand for necessary resources and the provision of possible possibilities of budgetary resources, g) its compatibility with company-level models through software applications and database technologies, h) the rapid and economic maintenance and i) the ability to use it in any sector or business, with any degree of complexity (products, processes, spare parts, human resources and cost of capital) (Heshmat et al., 2015).
Addressing the heterogeneity of transactions through ABC can be addressed, either by expanding the number of activities to handle an order, such as an average and a complex series. The cost of spent resources is then allocated to the three types of order management activities and a transaction guide and a number of complex and simple orders are defined for each activity. The cost system can alternatively use a duration driver, which calculates the required runtime of a task. As drivers of duration, they can be considered the hours of installation and operation of the machines, the hours of direct work and the hours of handling materials. Duration drivers, considered more expensive than trading drivers, are also more expensive, which is why the latter were selected (Kaplan & Anderson, 2003).
The transaction cost guide is calculated from the quotient of the cost of activity with the quantity of the transaction cost guide (e.g. number of customer orders, number of settings, etc.) and the result gives the cost per transaction. This procedure is based on the assumption that for each occurrence of a new event the same amount of available resources is consumed, which is the key to the approximation of cost guide rates (Kaplan & Anderson, 2003).
In essence, activity-based management and activity-based costing is the assessment and management of an organization's capacity, which requires two calculations: a) the unit cost of capacity supply (unit cost estimation) and b) the capacity consumption (unit times) from the organization's activities attributable to products, services and customers (unit time estimation) (Kaplan & Anderson, 2003).
When estimating unit costs, the analyst identifies the different groups of resources performing tasks (activities), such as all the activities performed by employees involved in customer service (determining which employees are on the front line of service, their moderators, and the resources needed to perform their functions; buildings, equipment, etc.), as well as the potentially employed resources of other departments assisting in their work (services of general interest, information technology, etc.) (Kaplan & Anderson, 2003).
In addition, the analyst estimates the practical capacity of the available resources as a percentage of theoretical ability. For example, if we assume that this percentage is 80% and a machine or a person can work 40 hours a week, then the practical capacity is calculated at 32 hours per week. The remaining 20% of the time is estimated as time for breaks, arrival-departure and communication, in the case of the employee, or interruptions of maintenance, repairs and planning respectively, when it comes to a machine. Alternatively, the assessment of practical competence is a time series review of previous activity levels, such as the number of orders for the last year or the last two years. Any excessive delays, poor quality, stressed or exhausted employees are checked and, if so, the starting point is the maximum number of resource capacity performing a certain activity (Kaplan & Anderson, 2003).
As in any design, so with ABC's design, the analysis is sensitive to estimation errors. The aim is to provide relative certainty and for this reason a deviation from reality between 5%-10% is tolerable. In the event that an incorrect assessment is made, this will be revealed by the ABC's process based on time. By estimating the cost of capacity provision and practical capacity, the analyst can calculate the unit costs as follows:
Unit cost =(Cost of capacity supplied )/(Practical capacity of resources supplied)
In the numerical example above, assuming that in a customer service department that employs a total of 28 frontline employees, each employee provides work of approximately 10,560 minutes/month or 31,680 minutes/quarter, and the practical capacity is approximately 80% of the theoretical one, so 25,000 cents/quarterly per employee or 700,000 minutes in total, and the sum of all resources is $560,000 per quarter, then the unit cost (per minute) of the supply capacity amounts (Kaplan & Anderson, 2003):
Cost per minute=560.000$/700.000=0,80$ / Per minute
As mentioned above, a second element required to implement TDABC, is the estimation of the unit time of a trading activity. This system uses a transaction driver whenever an activity, such as issuing a purchase order or installing a machine or processing a customer request, has the same duration. Each time an activity is performed, TDABC uses an estimate of the time required. The estimation of the time unit replaces the process and through interviews of the employees, an update is made on the time they devote to all the activities, thus creating an activity manual. These estimates can be obtained through interviews or by direct observation and do not have to be accurate, a rough estimate is sufficient (Kaplan & Anderson, 2003).
Assuming, for example, that the analyst estimates the unit times of three customer-related activities as follows: 40 minutes for order handling, 220 minutes for complaint processing, and 250 minutes to perform a credit check (Table 1).
It is understood that the cost of activity is not in line with the previous estimate. The reason for disagreement can be easily understood when calculating the cost of performing the same activities over a three-month period, as follows (Table 2):
With this analysis it is understood, that during the period only 83% of the practical capacity (578,600/700,000) of the resources for the execution of the activities were provided and therefore, only 83% of the expenses (of 560,000$) are allocated to customers in the same period (Kaplan & Anderson, 2003).
A traditional ABC system overestimates the cost of performing activities because it investigates the distribution of production effort, and although it is quite an accurate process, the work is roughly allocated to the three activities, incorporating both the costs of the used and the unused capacity of the resources, determining as a unit of measurement, the "times" of execution of each stage of the activity (Kaplan & Anderson, 2003).
Ostadi et al. (2019) however, developed a new sophisticated mechanism for the TDABC system using the theory of fuzzy sets for sanitary structures under conditions of uncertainty, in order to address the unreliability of data and overcome the limitations, uncertainty and shortcomings of TDABC, related to data estimation, to determine the exact health costs (Ostadi et al., 2019).
Although activity-based costing has allowed managers to find that not all customers are profitable and all revenues are positive for their business, difficulties in applying the traditional approach have prevented its use. These difficulties have been overcome with the time-guided ABC, since it provides easy and fast implementation, is easily integrated with data drawn from ERP and CRM systems, requires financial and short maintenance and updating, provides the possibility of extending it to models for the entire enterprise, makes it easy to integrate certain characteristics of specific ordering processes, customers and suppliers, provides better forecasting for the effectiveness of activities and capacity used and enables future resource requirements to be predicted on the basis of complexity, planned order and quantities. All of the above allow activity-based costing to become, from a complex and costly application, to an important tool for the rapid and inexpensive provision of practical data to management (Kaplan & Anderson, 2003).
In conclusion, the TDABC model is related to the calculation of time, while the ABC method is related to the calculation of the cost of activities and the cost of resources. TDABC can facilitate and make the costing process more accurate than ABC, in complex conditions, where the time required to perform an activity is influenced by a number of factors and determines unused capacity more accurately. In addition, unlike the ABC model, this model, this model, is easily maintained and does not need regular updating. Accordingly, the cost of implementing TDABC is also lower than the ABC, due to its simplicity and ease of application process (Ostadi et al., 2019). The TDABC model finally, could be used by most companies, regardless of the complexity of their products, services, customers, components or processes (Kaplan & Anderson, 2003).
The ABC and TDABC models usually include the following steps (Table 3):
Typology perspectives and costing practices
Over the last twenty years or so, the researchers' interest has turned to ABC's developments both in the gallery and its techniques, regarding the customer (cost object the customers) dimension of cost management. Through customer profitability analyses, management strives to optimize customer-related processes. In the value chain, cost and analysis guides highlight the value created by customer relationships. In his study, Otley (2003) evaluates the evolution of accounting management, describing the initial connection of the concept with economic rationality, shareholder opinion and internal auditing. Then, due to the ever-changing environment as he explains, attention shifted from internal control to value chain management. This development reveals the need to coordinate external with internal processes (Wegmann, 2019).
Wegmann (2019), in his study, presents four perspectives and practices that he observed as follows (Table 4): the first focuses on external stakeholders, i.e. takes into account external stakeholders in cost accounting systems, with a positive impact when making process decisions. The second focuses on methods of future costs, which contribute to the analysis of prospects and life cycles. The next groups efforts to improve cost accounting systems of various aspects, such as resource allocation, mathematical improvements and differentiation of factors. Finally, the fourth perspective attempts to simplify cost accounting systems (Wegmann, 2019).
Process-Operations Mining
The rapid development of databases in modern enterprises makes data analysis increasingly important (Olafsson et al., 2008). The need of enterprises for systematic and immediate adaptation to the ever-changing demands of the market has increased the interest of both the academic community and industries in the study of process mining and analysis of operations mining (Daft et al., 2010). This great shift in science towards data collection and storage has made data mining easier and less costly, which is why business databases are often huge. Particularly in areas related to electronic services and their systems are based on the internet, data mining is becoming necessary (Olafsson et al., 2008).
Traditional methods of analysis fail to turn into knowledge the wealth contained in large databases, a problem that the science of operational research comes to face, through the formation and resolution of numerous data mining barriers, as optimization problems. Many operations research applications can also be addressed through data mining (Olafsson et al., 2008).
The goal of data mining is to improve decision-making through the use of various methods and techniques, based on specialized rules for processing the available data (Gerard, et al., 2014).
The aim of Process-Operations Mining is to improve decision-making through the use of a variety of methods and techniques, based on specialized rules for the processing of available data (Gerard, et al., 2014). The term data mining refers to all aspects of a semi-automated or automated process for the extraction of initially unknown and potentially useful knowledge (Olafsson et al., 2008), as well as standards and correlations of the huge amount of data stored in the databases (Ray Li, 2022). This process follows many steps, such as consolidating the different data from a variety of databases, preparing them and inducing a model with a learning algorithm. Subsequently, the model is used to detect and implement actions that are required to be performed by the enterprise (Freed & Glover, 1986; Olafsson et al., 2008; Padmanabhan &Tuzhilin, 2003).
According to Fayyad et al. (1996), the extraction of valid and useful information as well as innovative data management models, from one or more databases, is carried out by a "deterministic" process (Fayyad et al., 1996).
The process of data mining begins with the collection of data, called as a training set, consisting of cases that describe the observed values of some characteristics or variables. These cases are then used to learn a given design or goal concept, and depending on the nature of the concept, different inductive learning algorithms are applied. Common concepts derived from data mining are data grouping, sorting and finding correlation rules. When sorting, the training data is highlighted (i.e. each snapshot is identified in one or more categories), and using an inductive learning algorithm, a model is created that distinguishes the class values. This model can then be used to sort new instances according to the class attribute. The class attribute does not exist when grouping data and detecting correlation rules (Olafsson et al., 2008).
Van der Aalst and Medeiros (2005) for example, who applied process mining techniques to analyze the paths of controlling security breaches (cryptography and role-based access control), presented schematically (Figure 4) certain mining results, for the process perspective (a) and the organizational (b and c) perspective, based on an event log (Annex). Since the process perspective deals with "How?" and the case perspective with "What?" they listed in a table (Appendix), five process cases. As illustrated in Figure 4, the log file shows that for four cases (1, 2, 3 and 4), activities A, B, C and D have been performed. For the fifth case, only three activities are carried out: activities A, E and D. Each case starts with the execution of A and ends with the execution of D. If activity B is performed, then activity C is also performed. However, for some cases activity C is carried out before activity B (Aalst & Medeiros, 2005).
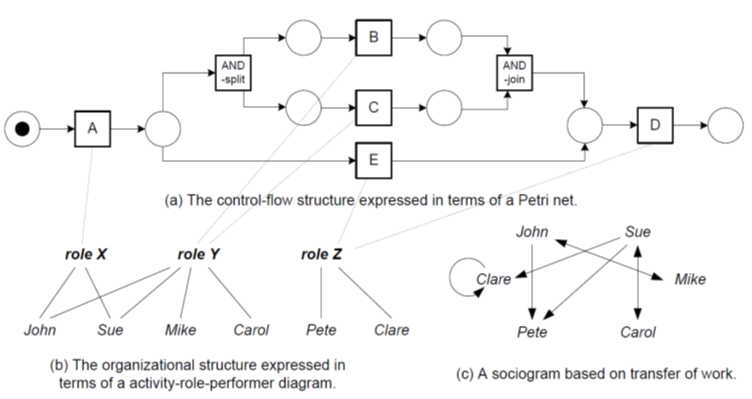
Process mining aims to extract process information from trade repositories. It is based on the assumption that it is possible to record events in such a way that: a) each event refers to an activity (i.e. a defined process step), b) each event refers to only one case (one process case), c) each event has an interpreter (the creator who starts or performs the activity), d) the events are entirely sorted and time-marked. The perspective of the process focuses on the control flow (series of activities) in order to find a good characterization of all paths expressed in terms of network, or chain process based on the events, that is, it focuses on the creator, the performers involved and how to relate to each other. For example, when a case concerns a supply order, it is useful to know the supplier or the number of products ordered (Aalst & Medeiros, 2005).
Information management systems receive a huge amount of raw data, which they process in order to aggregate useful information (Chapman, 2019). The business administrator is interested in obtaining aggregated information resulting from the processing of a targeted dataset, through appropriate algorithms (Dong & Qin, 2018). The information is derived in the form of reports and is produced either with a constant frequency, taking specific data, or is created parametrically on an ongoing basis, based on the choices of the company's executives (Glykas et al., 2018).
Although the operational scientific community has made a significant contribution to the field of data mining, due to its increased popularity in recent years, especially in the design and analysis of mining algorithms (e.g. use of mathematical programming for classification and grouping, selection of characteristics through simulated annealing of genetic algorithms, nested partition method), however, the field of data mining is not limited to the design of algorithms but can be play an important role in many operational investigation applications (Olafsson et al., 2008).
The study of data mining, although in recent years has attracted the interest of many researchers (Tsumoto et al., 2014), few of these studies nevertheless approach the issue of business reorganisation and human resources, creating a gap in the development of integrated such methods (Huang et al., 2011; Kerzner, 2003; Liu et al., 2013; Ly et al., 2005; Rinderle-ma & Van der Aalst, 2007; Schönig et al., 2016). In contrast, research into the development of automated decision-making tools through the extraction of functional data and the estimation of employee performance does not exist in the literature (Boj et al., 2014; Gurrea et al., 2014; Song &Van der Aalst, 2008; Van der Aalst & Song, 2004).
Process Mining and Effort Based Activity Based Costing
In this section we present an alternative effort based activity-process costing and analysis methodology. Cost calculation is performed on the percentage of effort that each employee is devoting per activity. The total percentage an employee can devote on all activities is 100%. Percentages of effort devoted on activities by employees are derived either from event logs or declared by the employees themselves and agreed by their managers. In the last decade, we use event logs in either case i.e for direct employee percentage of effort calculation or for validating the percentages declared by employees.
The focus in our approach is on the employee not on the event(s) as triggers-generators of either accounting records (Hong, 2016; Wynn et al., 2014) or economic events (Vom Brocke & Christian Sonnenberg, 2014). This by no means states that we do not take into account resource based costing in our final cost calculation as used in the mentioned previous research.
The main difference and contribution however is that we become specific in employee costs per activity. As an example we present the event log of a bank branch below (Table 5). For demonstration and space saving purposes we have extracted only the activities of "Clerk 1" (name not disclosed for confidentiality reasons) for the period 11:54 AM to 13:09 PM for a particular date (7th of May 2021).
Via this event log extract, we can calculate the time spent per activity by "Clerk 1" for this specific one hour and fifteen minutes’ period. With the day's full event log extract, we can calculate the time spent per activity by "Clerk 1" for the whole working day. We can then calculate the activity percentage for "Clerk 1" via the calculation ratio:
Employee Activity Percentage = (Sum of Time Spent on Activity in a Day)/(Time Employee worked at the Bank that Day).
For the deposits-withdrawals activity the sum of time "Clerk 1" spent on this activity for his working day was 148,58 minutes of the total 498 minutes he worked that day (Table 6). The result of the division is 0,21 (104,58/498) or 21%. In a similar manner we can continue calculating all percentages of effort per activity for "Clerk 1". We usually perform the same exercise for event log data representing longer periods of time before concluding with the final effort per activity results. We prefer a full representative week but in some cases we have reached the maximum of a monthly period.
For demonstration and space purposes we assume that the percentages calculated for "Clerk 1" for that day coincide with his concluding percentages of effort. We can then derive cost attributed on activities performed by "Clerk 1" for a yearly period or any other period we select. To calculate his yearly attributed cost per activity we need the overall salary costs the company spends for this specific employee for this specific period. We then multiply by the percentage of effort he devotes per activity. By following this type of analysis we end up with the following results:
In the example bellow (Table 7), we present the results for the six clerks working at the specific branch and the percentages they devote per activity and thus we can calculate total effort per activity.
Process Mining Effort Based Costing
In our research we tried to handle the basic perennial problem of human resources accounting via the costing of human effort. In the previous section we presented an approach for calculating human resources effort from process mining event logs. We also presented an approach for achieving HR activity based costing both at the level of the employee, the activity and the process.
Our Integrated Costing System proposal is shown in Figure 5:
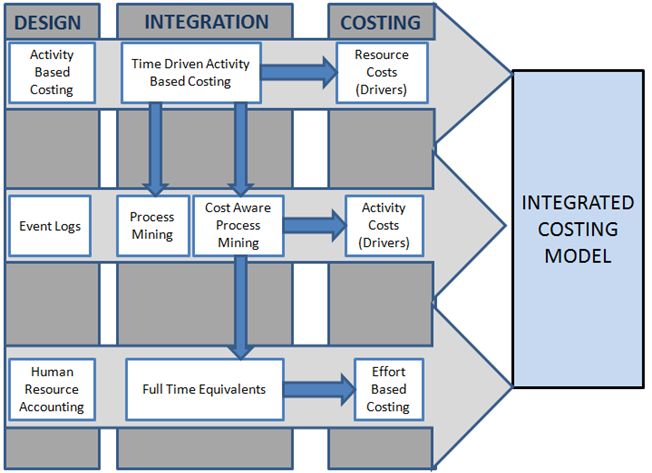
The proposed model is composed of 3 phases: design, integration and costing. The design phase involves the parameterization of the ABC system and the human resources accounting elements as well as the event logs records relevant to resources costing.
In the integration phase we refine the ABC system design with Time-Driven Activity Based Costing drivers. Based on these final drivers we calculate resource costs in the final costing phase.
In a similar manner in the integration phase we use these Time Driven ABC drivers in order to create cost aware event logs and apply cost aware process mining techniques. The result of the application of these cost aware process mining techniques is the calculation of the activity costs according to resource usage in the costing phase. The same techniques are used for the calculation of full time equivalents in the integration phase and the desired effort based costs in the costing phase.
All final cost calculations of the costing phase are combined in order to achieve the holistic cost calculation.
Conclusions
The aim of our research as set out in our research objective was to propose an enhanced Process Mining Approach for HRM Cost Estimations in Time Driven ABC Costing. In order to address the research objective our research addressed a series of research questions each of which we tried to elaborate and answer in the chapters 2 to 5 as presented in the following Table 8:
In section 2 we presented a literature survey of ABC, RCA and Time Driven ABC the focus was placed on highlighting their theoretical underpinnings of these three approaches. We highlighted the differences between traditional ABC and Time Driven ABC approaches and the evolution of ABC perspectives.
The aim of the section was to answer research questions 1 and 2. From the literature survey became evident that there were no approaches in these three disciplines (ABC, RCA and Time Driven ABC) that had the capability to analyze real time data and none of the approaches was using records extracted from event logs. Additionally, there was little or nonexistent evidence or validation that unit costs assigned to resources were calculated properly based on actual cost data in particular in the case of HRM costing.
In section 3 we presented the state of the art in process mining. We provided a literature survey on existing approaches that concentrate on the usage of event logs in extracting accounting related data that are used in resource allocation costing and in HRM costing in particular. The aim of the literature survey in this section was to provide answers to research question 3. There were no identified approaches that calculate HRM costs based on event logs.
In chapter 4 we presented our novel proposal in calculating HRM costs based on effort based calculations in order to answer research questions 4 and 5. This novel proposal is the first of its kind in the literature and is constitutes one of the two major contributions of our research.
In section 5 we presented a novel integrated costing model for process mining based on ABC costing and thus providing an answer to research question 6. The integrated model proposed is based in three distinct but interrelated streams of academic disciplines set out in the research objective, namely: ABC, Process Mining and Time Driven ABC. The proposed Process Mining Approach for HRM Cost Estimations in Time Driven ABC Costing is the second contribution of our research
Both our effort based HRM costing and the proposed Integrated Process Mining Approach to HRM costing has been applied to only a limited case of a bank branch. Even though the results are very promising further research is needed in the application of both approaches to larger organizational environments that require more advanced calculations. Also both approaches have not been applied in reorganization scenarios in which future desired cost per activity per employee could drive effort assigned by employees to activities in real time in an effort to achieve this future desired cost state.
Based on these limitations our future research directions would be focusing towards creating and linking performance measures to activities, effort and cost calculations derived by event logs. These measures will create a performance management system with real time information about the employees’ performance even on a daily basis or real time depending on the availability of event logs. Research on the development of state of the art information systems for HRM costing and reporting is also envisaged in the near future.
References
Berliner, C., & Brimson, J. A. (Eds.). (1988). Cost management for today's advanced manufacturing: The CAM-I conceptual design. Harvard Business Review Press.
Boj, J. J., Rodriguez-Rodriguez, R., & Alfaro-Saiz, J. J. (2014). An ANP-multi-criteria-based methodology to link intangible assets and organizational performance in a Balanced Scorecard context. Decision Support Systems, 68, 98-110. DOI:
Bragg St. (2022 May 24). Cost Object. Accounting CPE Courses & Books. Accounting Tools. Retrieved on 31 August, 2021, from https://www.accountingtools.com/articles/2017/5/4/cost-object
Chapman, R. J. (2019). The rules of project risk management: Implementation guidelines for major projects. Routledge. DOI:
Chea, A. C. (2011). Activity-based costing system in the service sector: A strategic approach for enhancing managerial decision making and competitiveness. International Journal of Business and Management, 6(11), 3. DOI:
Cooper, R., & Kaplan, R. S. (1988). How cost accounting distorts product costs. Strategic Finance, 69(10), 20.
Cooper, R., & Kaplan, R. S. (1991). Profit priorities from activity-based costing. Harvard business review, 69(3), 130-135.
Daft, R. L., Murphy, J., & Willmott, H., (2010). Organisation Theorie and Design (Vol. 10). Mason, OH: South-Western Cengage Learning.
Dhubea, H. M. S. B., & Al-Riami, S. A. (2017). The application of activity-based costing and activity-based planning influences decision making. Asia-Pacific Management Accounting Journal, 12(1), 1-38.
Dong, Y., & Qin, S. J. (2018). A novel dynamic PCA algorithm for dynamic data modeling and process monitoring. Journal of Process Control, 67, 1-11. DOI:
Fayyad, U., Piatetsky-Shapiro, G., & Smyth, P. (1996). From data mining to knowledge discovery in databases. AI magazine, 17(3), 37-37.
Ferdows, K., Miller, J. G., Nakane, J., & Vollmann, T. E. (1986). Evolving global manufacturing strategies: projections into the 1990s. International Journal of Operations & Production Management, 6(4), 6-16. DOI:
Freed, N., & Glover, F. (1986). Evaluating alternative linear programming models to solve the two‐group discriminant problem. Decision Sciences, 17(2), 151-162. DOI:
Gerard, G., Martine, R., Haas, & Pentland, A. (2014). Big data and management. Academy of management Journal, 57(2), 321-326. DOI:
Glykas, M. M. (2011). Effort based performance measurement in business process management. Knowledge and Process Management, 18(1), 10-33. DOI:
Glykas, M., Valiris, G., Kokkinaki, A., & Koutsoukou, Z. (2018). Banking business process management implementation. International Journal of Productivity Management and Assessment Technologies (IJPMAT), 6(1), 50-69. DOI:
Gurrea Montesinos, V., Alfaro Saiz, J. J., Rodríguez Rodríguez, R., & Verdecho Sáez, M. J. (2014). Application of fuzzy logic in performance management: a literature review. International Journal of Production Management and Engineering, 2(2), 93-100. DOI:
Hashim, J. H. (2015). The activity-based costing in institutions of higher education: Do private and public bring a different? Asian Journal of Basic & Applied Sciences, 2(1), 16-30.
Heshmat, A. A. E., Agha, S. S. A., Mousavi, S. M., Rezaeipour, M., & Samim, N. (2015). Cost Management, Activity-Based Costing and new generations of ABC. Indian Journal of Fundamental and Applied Life Sciences, 5(SI), 3948-3954. www.cibtech.org/sp.ed/jls/2015/01/jls.htm
Hong, T. T. B. (2016). Process Mining-driven Performance Analysis in Manufacturing Process: Cost and Quality Perspective.
Huang, Z., Lu, X., & Duan, H. (2011). Mining association rules to support resource allocation in business process management. Expert Systems with Applications, 38(8), 9483-9490. DOI:
Jeyaraj, S. S. (2015). Activity based costing vs Volume based costing: relevance and applicability. The international journal of management, 4, 39-46.
Johnson, H. T., & Kaplan, R. S. (2002). Relevance lost–The rise and fall of management accounting. Harvard Business School Press, Boston, MA apud KENNERLEY, M., NEELY. A., A framework of the factors affecting the evolution of performance measurement systems. International Journal of Operations and Production Management, 22(11), 1222-1245. DOI:
Kaplan, R. S., & Anderson, S. R. (2003). Time-driven activity-based costing. DOI:
Kenton W. (2022). Activity-Based Costing (ABC). Method and Advantages Defined with Example. Reviewed by Janet Berry-Johnson. In Investopedia. https://www.investopedia.com/terms/a/abc.asp
Kerzner, H. (2003). Project Manegement: a system approach to planning, scheduling, and controlling (8th ed.). John Wiles & Sons.
Kumar, N., & Mahto, D. G. (2013). A comparative analysis and implementation of activity based costing (ABC) and traditional cost accounting (TCA) methods in an automobile parts manufacturing company: a case study. Global Journal of Management and Business Research, Accounting and Auditing, 13(4).
Liu, R., Agarwal, S., Sindhgatta, & Lee, R. R. J. (2013). Accelerating collaboration in task assignment using a socially enhanced resource model, in: Business Process Management (pp. 251–258). Springer. DOI:
Ly, L. T., Rinderle, S., Dadam, P., & Reichert, M. (2005, September). Mining staff assignment rules from event-based data. In International Conference on Business Process Management (pp. 177-190). Springer. DOI:
Monday, O. (2017). Human Resources Accounting: Issues, Benefits and Challenges. International journal of economics, finance and management sciences, 5(3), 129-138. DOI:
Nielsen, H. (2017). The Roles of Finance functions, Management Accounting, and Lean. Universitetsforlag. [The PhD series for the Faculty of Engineering and Natural Sciences, Aalborg University]. DOI: 10.5278/vbn.phd.eng.00031
Olafsson, S., Li, X., & Wu, S. (2008). Operations research and data mining. European Journal of Operational Research, 187(3), 1429-1448. DOI:
Oseifuah, E. K. (2014). Activity based costing (ABC) in the public sector: benefits and challenges. Problems and Perspectives in Management, 12(4-2), 581-588.
Ostadi, B., Daloie, R. M., & Sepehri, M. M. (2019). A combined modelling of fuzzy logic and Time-Driven Activity-based Costing (TDABC) for hospital services costing under uncertainty. Journal of biomedical informatics, 89, 11-28. DOI:
Otley, D. (2003). Management control and performance management: whence and whither? The British Accounting Review, 35(4), 309-326. DOI:
Padmanabhan, B., & Tuzhilin, A. (2003). On the use of optimization for data mining: Theoretical interactions and eCRM opportunities. Management Science, 49(10), 1327-1343. DOI:
Ray Li (2022, May 10). History of Data Mining. KDnuggets Blogs. https://www.kdnuggets.com/2016/06/rayli-history-data-mining.html
Rinderle-Ma, S., & van der Aalst, W. M. (2007). Life-cycle support for staff assignment rules in process-aware information systems. (BETA publicatie: working papers; Vol. 213). Technische Universiteit Eindhoven.
Schönig, S., Cabanillas, C., Jablonski, S., & Mendling, J. (2016). A framework for efficiently mining the organisational perspective of business processes. Decision Support Systems, 89, 87-97. DOI:
Sezenias, E., Farmakis, A., Karagiannis, G., Diagkou, E., & Glykas, M. (2013). A Holistic Business Performance Measurement Framework. Business Process Management (pp. 75-98). Springer. DOI:
Smith, S. T. (2017). Strategic management accounting. delivering value in a changing business environment through integrated reporting. Business Expert Press.
Song, M., & Van der Aalst, W. M. (2008). Towards comprehensive support for organizational mining. Decision support systems, 46(1), 300-317. DOI:
Tsumoto, S., Iwata, H., Hirano, S., & Tsumoto, Y. (2014). Similarity-based behavior and process mining of medical practices. Future Generation Computer Systems, 33, 21-31. DOI:
Van der Aalst, W. M., & de Medeiros, A. K. A. (2005). Process mining and security: Detecting anomalous process executions and checking process conformance. Electronic Notes in Theoretical Computer Science, 121, 3-21. DOI:
Van der Aalst, W. M., & Song, M. (2004, June 8). Mining social networks: Uncovering interaction patterns in business processes. In International conference on business process management (pp. 244-260). Springer. DOI:
Vom Brocke, J., & Sonnenberg, C. (2014). Process management and accounting-an overdue take on measuring the economic value of business processes. Class Notes: BPM and Education and Research.
Vultur, P. (2018). Study based on the importance of the information provided by management accounting on the managerial process in the joint stock companies in the north-east area of Moldova. The USV annals of economics and public administration, 18(1 (27), 134-142.
Wegmann, G. (2019). A typology of cost accounting practices based on activity-based costing-a strategic cost management approach. Asia-Pacific Management Accounting Journal, 14, 161-184. DOI:
White, L. (2009). Resource consumption accounting: Manager‐focused management accounting. Journal of Corporate Accounting & Finance, 20(4), 63-77. DOI:
Wynn, M., Low, W. Z., ter Hofstede, A., & Nauta, W. (2014). A framework for cost-aware process management: cost reporting and cost prediction. Journal of Universal Computer Science, 20(3), 406-430.
Copyright information
This work is licensed under a Creative Commons Attribution-NonCommercial-NoDerivatives 4.0 International License.
About this article
Publication Date
31 December 2022
Article Doi
eBook ISBN
978-1-80296-129-4
Publisher
European Publisher
Volume
130
Print ISBN (optional)
-
Edition Number
1st Edition
Pages
1-270
Subjects
Strategic Management, Leadership, Technology, Post-Pandemic, New frontiers
Cite this article as:
Sachini, E., Nikou, E., & Glykas, M. (2022). Process Mining Human Resources Cost Calculations in Time Driven Activity Based Costing. In E. N. Degirmenci (Ed.), New Frontiers for Management and Strategy in the Post-Pandemic Era, vol 130. European Proceedings of Social and Behavioural Sciences (pp. 170-193). European Publisher. https://doi.org/10.15405/epsbs.2022.12.02.15