Abstract
The paper presents a comparative analysis of approaches to the construction and implementation of safety management systems in in transport ergatic systems with an emphasis on the study of changes in understanding the role and place of the human factor in human-machine systems on transport. This article presents the results of a study of the evolution of approaches to taking into account the human factor in ergatic systems on transport and the differences in the implementation of these approaches in safety management systems in aviation and the maritime fleet. Lack of attention to socio-psychological factors (human factor) and fatigue management in the fleet was revealed. Using the example of taking into account the influence of the human factor and managing the fatigue of aircraft crew members (Fatigue Risk Management System), a higher level of development of safety management systems in aviation is demonstrated in comparison with the maritime fleet. The directions of development of the control system in the marine fleet are proposed that meet the current and future needs of the fleet. The study used retrospective analysis, information retrieval, analysis of bibliographic sources, comparison, analysis and synthesis, induction, logical method. During the study, the current regulations and recommendations of ICAO, IATA, IMO, ILO, scientific publications on the topic of the study were used. As a result, the statement is substantiated that a modern safety management system in the fleet should use data-driven decision management (DDDM).
Keywords: ergatic systems, safety management systems, transport
Introduction
In the twentieth century, there was a sharp increase in the volume of cargo transportation by sea. The development of knowledge and elaboration of technology has allowed the construction of ships of increasing size, which has significantly reduced the cost of transportation. However, the growth in the size of ships also had a negative side. Now the death of even one ship turned into a major catastrophe, in which both the loss of people and property and significant environmental pollution occurred. And if this death happened to the citizens of developed countries or the coasts of such countries were polluted, then the public reaction to these events was very loud.
A common point of view on the causes of accidents is that their root cause is the human factor, which means non-compliance with the rules, negligence, carelessness, lack of qualifications, etc. That is, man is viewed as a destructive factor in the “man-machine” system. This approach assumes that if there is strict adherence to instructions and rules, then no accidents should occur. However, man is not a mechanism. If the mechanism needs a scheduled break of 2 hours, then it doesn't matter whether it is day or night, warm or hot, quiet or noisy. If we have the need to give a person 6 hours of sleep, then it is essential whether he sleeps in a bed or in an economy-class airplane seat, in his cabin or on the floor of the engine room. However, the governing documents in force in the maritime fleet ignore this fact, considering a person as a machine that does not have circadian rhythms and other psycho-physiological features, which just needs to accumulate certain hours of rest in the allocated time interval.
Planning, organization and registration of work and rest hours, both in aviation and in the fleet, have general fundamental principles, but their specific implementation is significantly different. Not because of differences in the operation of ships, but, to a greater extent, due to ignoring the facts of excessive workload and fatigue of modern seafarers and the lack of regulation of ensuring compliance with the time standards. The working time and recovery time of seafarers is recognized as a constant value, not taking into account the actual state of a person, the characteristics of his metabolism, and other factors. As a result, the reporting system for work and rest hours in the fleet has a life of its own and, to put it mildly, has clear signs of low reliability.
Problem Statement
The peculiarities of human psychology are such that even the daily death of several thousand people is not an official tragedy and a reason for national mourning. Although about 3–4 thousand people in the world die in car accidents every day and about 100 thousand are injured, and 1.2–1.4 million people die in a year, humanity continues to use cars, often not observing even the minimum safety requirements. since these deaths are not concentrated in one place and moment. According to the WHO, for adults under 35, car accidents are the most common cause of death, ahead of all other diseases, disasters and criminal violence. In contrast, airplane accidents occur much less frequently, but the concentrated death of a large group of people causes a much greater public outcry. In 2019, there were 20 plane crashes in the world in which not 1.3 million died, as in car accidents, but only 283 people, although the loss of even one person is a tragedy. Therefore, the level of development of human factor management systems in aviation is the highest, even higher than in the oil and gas sector. (Sætren et al., 2015).
It may seem cruel, but it was the mass death of people in plane crashes that led to a significant advance in the level of security development in terms of managing crew fatigue in aviation over the maritime fleet. Lacking passenger traffic and such brutal incentives as the death of passengers, the fleet is very slowly progressing in its development and the application of new tools in the management of crew fatigue. Traditionalism and inertia – these are the words that characterize the modern fatigue management system in the fleet. And, despite the adoption of norms in STCW and MLC on this issue, the situation is not improving, but worsening. Many scheduled tasks and trainings are performed on paper, since the crews do not physically have enough time for them.
The accident report (U.S Chemical Safety and Hazard Investigation Board, 2016) directly draws attention to the lack of consideration of the human factor: «the lack of effective integration of human factors into the design, planning, and execution of drilling and completions activities ... and it illustrates a demonstrable gap in US offshore regulation and guidance to incorporate more robust management of human factors».
Despite the measures taken by the IMO, other international organizations and national governments to improve safety in the maritime fleet, they contain a number of gaps that, unfortunately, are not being resolved and are waiting for their disaster, where they will be recognized as the main causes.
Research Questions
The crews of aircraft and ships, interacting in man-machine systems with various equipment, are exposed to fatigue factors, the significance of which is caused by the presence of psychophysiological qualities in a crew member. Traditional approaches to personnel management on transport are characterized by the primacy of human error and weakness as an element of the human-machine system, i.e. consider it as a destructive factor, the presence of which on board the ship is caused solely by the impossibility of replacing it with technical means.
At the beginning of the twentieth century, neither air nor road transport could compete with sea transport in intercontinental traffic. And the sinking of the Titanic led to public demands to change the existing rules in the field of safety, or rather to establish them – the first edition of SOLAS ("SOLAS, International Convention for the Safety of Life at Sea") was adopted. Subsequent major disasters also led to industry responses (Table 01) to catastrophic events, with the response focused on preventing the recurrence of such events. In general, the construction of a safety management system in the maritime fleet has a pronounced reactive character, which does not distinguish it from many other spheres of human activity.
However, since the middle of the twentieth century, sea transport is no longer a means of transportation for passengers, it is moving into a recreational status – a place of rest. Accordingly, if accidents at sea do occur, now they are more concerned with cargo ships. And there is no mass death of people – there is no corresponding public reaction, requirements for changing the rules. Partly for this reason, the negotiation of amendments to international conventions, which are recognized by the transport industry professionals, has been very slow.
Air transport, on the contrary, sharply increases the volume of traffic in the second half of the twentieth century. And the growth in traffic is also an increase in the number of accidents and fatalities. According to the results of investigations of a number of air crashes, certain measures are taken, and since the public resonance from the death of passengers in air crashes is much higher, then the measures taken are not only promises to prevent a repetition of the same event, but also specific, preventive and quantifiable (identifiable) measures, including use of contemporary technologies.
Both in the maritime and aviation industries there is now such an element as the Safety Management System – in aviation it is called the Flight Safety Management System (FSMS), in the fleet – the Safety Management System (SMS).
The emergence of such modern systems did not happen overnight. This was the result of a long journey.
Mass transportation of passengers has actualized the need to ensure the reliability safety of transport. The maritime industry was characterized by the initial freedom from any general (international) regulation, security issues until the middle of the twentieth century were dealt with only by states and their efforts and demands on carriers were very different. Aviation, as a younger industry, initially lacked the freedom characteristic of seafarers. As with any young technology, the initial problem was the low reliability of aircraft and their equipment.
Therefore, the in the development of safety management systems is the era of elimination of technical factors. In 1950–1970, the solution to the safety problem was seen through the technical improvement of aircraft. This bore fruit – the number of accidents due to technical failures decreased annually (Figure 01). However, a number of plane crashes with technically sound aircraft but crew members' mistakes, brought the human factor to the fore.
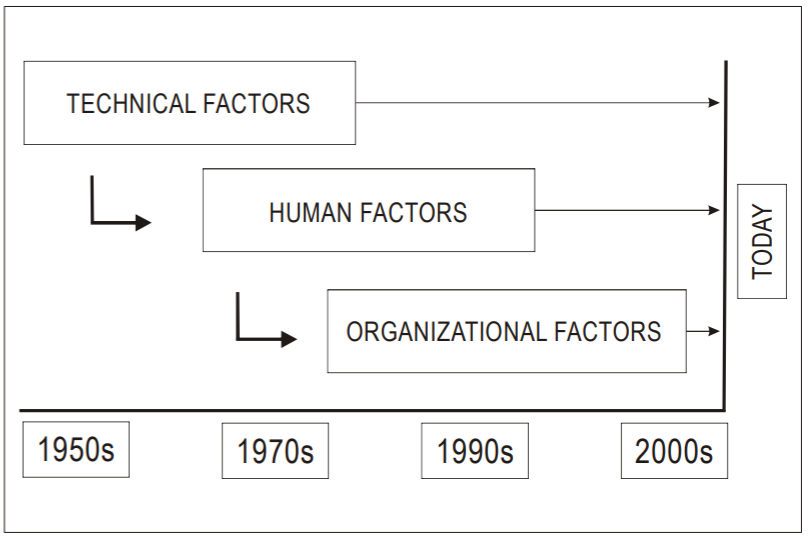
In the, in the period from the 1970s to the 1990s, the main efforts are aimed at building an effective man-machine system (interface), transferring advanced experience in personnel training. Significant attention began to be paid to the human factor, but it was limited only to the individual, without due attention to organizational, technical aspects. In this system, man is increasingly viewed as a weak link, which cannot be replaced (excluded) due to the weakness of technology and the impossibility of building reliable automatic systems. Therefore, it is necessary to limit human freedom by establishing a rigid system of rules, instructions, procedures, checklists, etc. However, man is not a machine, he does not want and cannot be the same all the time and is strongly affected by lack of interest and involvement in work.
It is being replaced by the (organizational) – (from the 1990s to the present). Now, not an individual person but the whole system is considered. It is impossible to overcome all its shortcomings, and by them, in most cases, man and his interaction with other people and machines are meant. But it is possible to create multiple barriers and breaking even some of them should not lead to disaster.
Risk management has become widespread in both the navy and aviation, and James Reason and his model of holed Swiss cheese is well-known in each industry.
However, a significant difference is the basis on which safety management in the sky and at sea is based. And, more precisely, on what data is the safety management system built and the risk assessment is carried out.
The study of the influence of the human factor is interdisciplinary and is now viewed through three directions:
- the ergonomics of the physical environment (physical ergonomics) – considering the anatomical, anthropometric, biochemical and physiological characteristics of man, his workplace and environment (working environment (WE);
- organizational – consideration of processes and management structures, communication between people, human-machine interface (HMI), resource management, including workload and rest, etc.;
- cognitive ergonomics – mental characteristics of man (memory, perception, decision-making speed, skilled labor, interaction with machines, etc.) (Karwowski, 2012).
However, when investigating accidents, cognitive and organizational ergonomics are rarely assessed (Skogdalen and Vinnem, 2011) and the development of an objective assessment toolkit that is currently lacking is required. Although the Manual for the Investigation of Marine Accidents and Incidents (IMO resolution А.884 (21)) mentions the need to take into account the human factor, data collection, but nothing is said about measurability, quantitative assessment, and the phrase "systematic investigation" actually means rigid sequence of operations, but not systematic research of the human factor.
In the absence of assessments (measurements) of the state of a person before the accident and comparing them with systematically obtained data during normal work, it is impossible to assess with high confidence the state of a person much later, during the investigation of the accident.
The study (Johnsen et al., 2017) also notes that in aviation, the level of quality of human factor management tools is significantly higher, even in comparison with offshore oil production, so advanced in this field. For the study, the authors analyzed data on the Norwegian PETROMAKS project for 2001–2012.
Purpose of the Study
The purpose of this study is to consider and compare approaches to the management of human activities in ergatic transport systems – in aviation and in the maritime fleet. The expansion of the use of personnel fatigue assessment tools in aviation, as well as the construction of information systems that use them, made it possible to switch to fatigue management based on facts, rather than on subjective, unverifiable and possibly falsified assessments, which is typical for the maritime industry.
Research hypotheses:
- the adoption of international and national regulatory measures in the maritime fleet is based on a reactive approach – when the decisions and actions taken are a reaction to a significant event (catastrophe) that has occurred, and are not preventive measures;
- oversimplification of approaches to the "man-machine" system in the maritime fleet predetermines man (seafarer) to be the guilty and most unreliable element in this system, with the erroneous identification of the concepts of "human factor", "human element" and human actor;
- crew tiredness and fatigue in the maritime fleet is caused by the lack of instruments to measure and quantify seafarers’ condition on board, and fatigue management does not rely on quantification and data-driven decision management (DDDM).
Research Methods
The research used retrospective analysis, information retrieval, analysis of bibliographic sources, comparison, analysis and synthesis, induction, logical method. During the study, the current regulations and recommendations of ICAO, IATA, IMO, ILO, scientific publications on the topic of the study were used. As a result, the statement is substantiated that a modern safety management system in the fleet should use data-driven decision management (DDDM).
Findings
Normative regulation of work and rest hours in the fleet
The International Convention on Standards of Training, Certification and Watchkeeping for Seafarers (STCW) gives the following instructions:
Chapter VIII. Watchkeeping. Rule VIII/1 – Fitness for Duty:
Each Administration shall, for the purpose of preventing fatigue:
1) establish and enforce rest periods for watchkeeping personnel and those whose responsibilities include assigned safety, security and pollution prevention responsibilities in accordance with section AVIII/1 of the STCW Code;
2) require that watch systems are so arranged that the efficiency of all watchkeeping personnel is not impaired by fatigue and that duties are so organized that the first watch at the commencement of a voyage and subsequent relieving watches are sufficiently rested and otherwise fit for duty.
STCW and SOLAS 74/78 require the issuance of a Minimum Safe Manning Document (Certificate). However, the procedure for determining the size of the crew, calculating the load, the physical ability to perform work and observe the established work and rest regimes is not defined and it is not required from the shipowner/operator to justify the calculated number of crew members required by him for approval.
At the 21st session of IMO in 1999, Resolution A.890 (21) "Principles for determining safe manning" was adopted, which is also limited to general words, without any numerical specifics, and recommends. Resolution А.1047 (27), adopted in 2011, "Principles of the minimum safe manning of a ship" was also limited to general words about the need for accounting, assessment and clause 2.4 states that "The administration must only approve the proposal on the minimum safe manning of a ship and draw up, accordingly, to the vessel Document on the minimum safe manning of the crew. " Under 2.7, the Administration only needs to consider “very carefully the circumstances that would permit the indication ... of fewer than three qualified officers in charge of a navigational watch”. No prohibitions, no instrumental assessments and calculations are required.
The MLC and Section A-VIII/1 of the STCW Code establish working hours and hours of rest:
- the maximum working time must not exceed:
- 14 hours in any 24 hour period;
- 72 hours in any period of seven days;
- the minimum duration of rest time is not less than:
- ten hours in any 24 hour period;
- 77 hours in any period of seven days.
US Coast Guard regulations (CFR 15.1111 (a)) require each officer in charge of the watch (engineer) to receive a minimum of 10 hours of rest in a 24-hour period. According to the requirements of (CFR 15.1111 (b)), rest hours can be divided into no more than two periods, one of which is at least 6 hours. The US applies STCW requirements for US-flagged ships outside the US and for foreign-flagged ships sailing in the US. For US-flagged vessels operating in the US, US CG rules will only apply.
According to the OPA-90 requirements, tanker crews are required to have no more than 15 hours of operation in any 24-hour interval, or no more than 36 hours in a 72-hour interval, with the exception of emergencies or exercises.
Approaches to the identification of fatigue factors and the construction of a safety management system in aviation
Formed in the 1970s and dominant in the maritime fleet, the approach, let's call it “traditional”, was also used in aviation. Its basis is compliance with regulatory requirements and instructions, and it was built on the basis of reaction to events (incidents) to prevent their recurrence. This is a reactive approach (Figure 2). That is, we are trying to learn from our mistakes by conducting an investigation and identifying, as we believe, the cause of the events that occurred. However, the “response threshold” in the reactive approach is quite high – response measures are taken after major incidents, with large negative consequences.

The next stage of development is a – an active search for hazards and their management is added to the instructions and rules (Figure 03). These include the adoption of risk assessment methods, the creation of a safety culture, the study of incident experiences, open discussion of problems, the exchange of best practices, and systematic safety monitoring.
An important difference in the approaches is the analysis time – if, with a reactive approach, information is analyzed after an incident (during the investigation), then with a proactive approach, the collection of information should be carried out constantly, i.e. and before the incident. The collected information is analyzed based on the existing patterns. The purpose of the analysis is to identify the hazard (to assess the risk) before it develops into an accident and to take preventive measures. For these purposes, indicators of the actual state (Safety Performance Indicators (SPIs)) and goals, desired parameters (Safety Performance Targets (SPTs)) are used (SMM Doc 9859, 2018).

The next stage of development is the predictive approach (Figure 04). As it was rightly noted (Bartulovic, 2021), the predictive methodology has not yet been worked out, and is at the initial stage of its development. It is aimed at identifying potential and possible hazards based on predictive analysis (forecasts), which extracts information from historical and current safety data, as well as to predict trends and behavior patterns of emerging hazards (Čokorilo et al., 2019; SMM Doc 9859, 2018; Luxhoj, 2013; Cusick et al., 2017). For the predictive approach, an event (incident) is no longer needed, data is collected and analyzed constantly. At the same time, their volume is so large that, unlike the proactive approach, where analysis can be performed by a person, the collection, processing and analysis of data is carried out in an automated or automatic mode in real time.
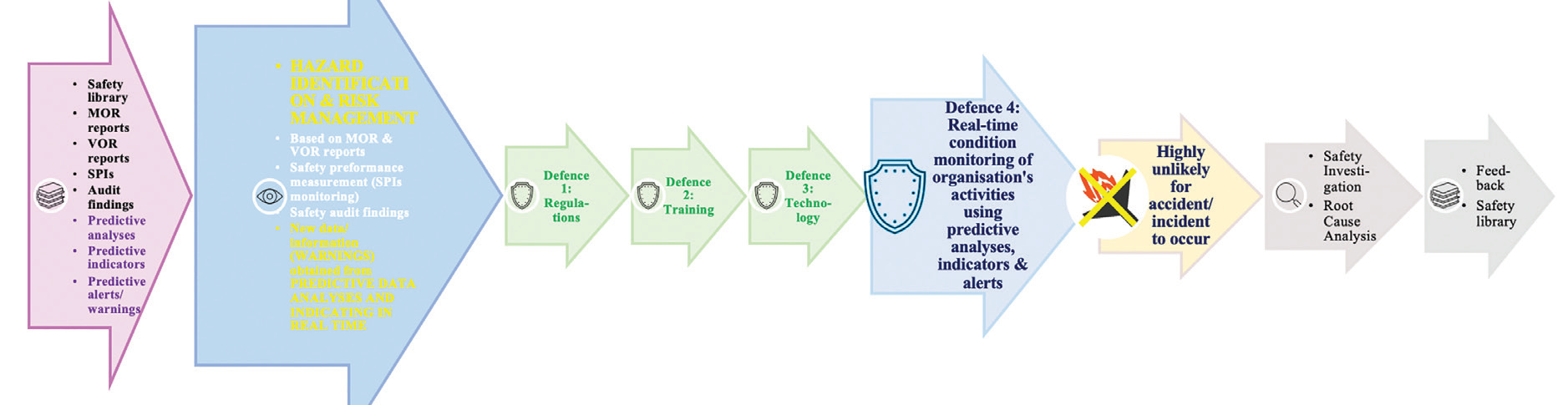
In (Bartulovic, 2021), an analysis of various approaches to the implementation of the predictive approach is given.
Fatigue Risk Management System
Earlier in aviation, as now in the fleet, fatigue management was carried out on the basis of a regulatory approach (maximum allowable work time, minimum rest time, total duration of work in the reporting period, etc.). However, in addition to the work time itself, something else affects general fatigue:
- the sufficiency and quality of sleep, and not just rest, which is especially important for seafarers, when instead of rest, a person spends time with a smartphone or another communication device.
- the influence of daily biorhythms on the ability to fall asleep and the overall quality of sleep at different times of the day.
The accumulation of scientific data on the peculiarities of fatigue and recovery of the human body, as well as the emergence of the possibility of measuring the state of the body of a crew member not only in laboratory, but also in normal working conditions, now allows us to create "real time" fatigue management systems.
Existing systems for recording hours of work and rest imply a simplified binary assessment – either the rules are followed or not. It is clear that none of the responsible persons of the crew wants to receive punishments for non-compliance with the norms, and as a result we get the adjustment of the reporting to the norms, and not the actual reflection of the hours of work and rest.
With respect to the issue of interest to us, i.e. fatigue management, a system used in aviation – Fatigue Risk Management System (FRMS) should be noted. According to the ICAO recommendations (FRMS Implementation Guide for Operators, 2011), the following definition of FRMS is given: “A data-driven means of continuously monitoring and managing fatigue-related safety risks, based on scientific principles and knowledge as well as operational experience, which aim to ensure relevant personnel are performing at adequate levels of alertness.” FRMS employs a layered safety strategy to manage fatigue-related risks regardless of their source.
The basis of its functioning is the continuous collection and analysis of evidence, making it possible to identify the risks associated with fatigue, and then – to develop and implement management mechanisms and measures to reduce these risks, as well as to assess their effectiveness (FRMS, 2011).
Table 02 summarizes the existing aviation instruments that are used as part of the SMS/FRMS.
Table 03 summarizes which of the FRMS tools have similar elements in SMS in the maritime fleet. Most of the tools used in aviation have never been used in the fleet at all. The main emphasis is on fulfilling the norms by filling out reports (Work And Rest Hours), investigating accidents.
Technical solutions for monitoring the condition of crew members
Data-driven decision-making (DDDM) is defined as a combined use of various information, such as facts, metrics and data for making management decisions. In doing that, this information must be converted into a format suitable for automated processing. The use of subjective qualitative assessments in determining the degree of fatigue, especially by a person who does not have specialized knowledge, leads to significant errors and variation in values. Shifting to tools that represent measurement results in a quantitative format eliminates the subjectivity of assessments. The increase in the power of computing facilities, the emergence and reduction of the cost of wearable sensors, allows generating and processing significant amounts of data (big data) about the psychophysiological state of crew members, assessing and managing fatigue and recovery of the body.
The traditional tool for analyzing the quality of rest (sleep) in aviation is the use of actigraph (Figure 05), a non-invasive method for monitoring a person's rest/activity cycles. It is a wearable monitor.
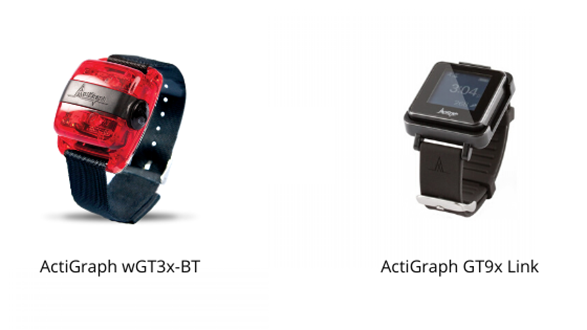
There are single-channel (wrist) systems that fix the position of the body, movement along the axes, lighting (TIB-time in bed), patient marker, as well as multichannel ones – with a PLM (restless legs syndrome) sensor, a CPAP pressure sensor, a chest mount, nasal cannulas that monitor snoring and flow, with ECG and EEG sensors.
The most accessible for independent use by the pilot is the single-channel version.
For a comprehensive assessment of the condition of the body, another solution can be used – the Vital Jacket®. Using the Vital Jacket wearable sensor system (Figure 06), the state of air traffic controllers was assessed through stress testing in 2016–2018 under the STRESS (Human Performance Neurometrics Toolbox For Highly Automated Systems Design) project (www.stressproject.eu), during which strengs and weaknesses of neurometric diagnostics and the possibility of its use in normal conditions were revealed (Rodrigues et al., 2018; Cunha, 2010).
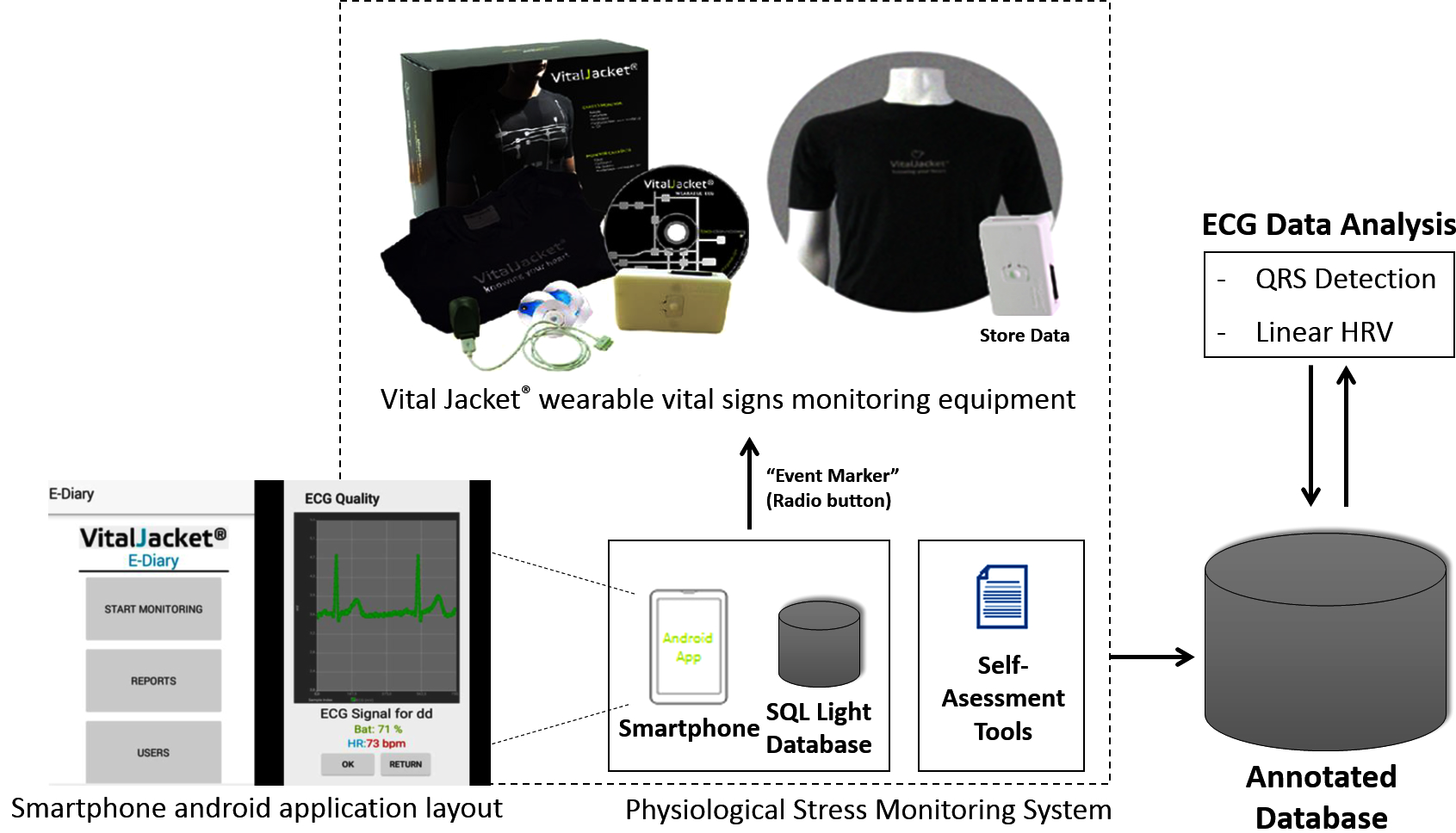
If earlier actigraphs were highly specialized devices, nowadays various models of fitness bracelets performing similar functions are widely represented on the market of household wearable devices. An important difference between fitness bracelets and smart watches is the absence or impossibility of using light sensors for users. Light metering is an important parameter affecting the quality of sleep.
Conclusion
The analysis, performed in this study, showed that the level of the safety management system development in the maritime fleet corresponds, in terms of human factor management, to the level of the 1970–80s of the aviation industry and is objectively inadequate to the modern needs and capabilities of the fleet. The reactive approach used in the fleet from the outset, no longer ensures the advanced development of safety management systems and safety enhancement.
Organizational, informational and technical solutions developed for the aviation industry can be transferred to the maritime fleet. The application of these decisions will allow for a deeper and more qualitative assessment of the condition of the crew members, to manage them and make informed decisions based on data (data-driven decision management (DDDM).
The analysis of the regulatory requirements for the management of hours of work and rest in the fleet allows us to conclude that there is a lack of specificity in them, which condones the distortion of the ideas laid down in them during their adoption, does not make possible to form a reliable idea of the state of the crew members and make the necessary decisions. This, in the future does not ensure the achievement of the required security level.
References
Bartulovic, D. (2021). Predictive Safety Management System Development. Transactions on Maritime Science, 10, 1–12.
Čokorilo, O., Ivković, I., & Kaplanović, S. (2019). Prediction of Exhaust Emission Costs in Air and Road Transportation. Sustainability, 11(17), 4688. https://doi.org/10.3390/su11174688.
Cusick, S. K., Cortes, A. I., & Rodrigues, C. C. (2017). Commercial Aviation Safety (6th Ed.). McGraw-Hill.
Fatigue Risk Management System, Implementation Guide for Operators. (2011). IATA, ICAO, IFALPA. https://www.icao.int/safety/fatiguemanagement/FRMS%20Tools/FRMS%20 Implementation%20Guide%20for%20Operators%20July%202011.pdf
Johnsen, S., Kilskar, S., & Fossum, K. (2017). Missing focus on Human Factors – Organizational and cognitive ergonomics – In the safety management for the petroleum industry. Proceedings of the Institution of Mechanical Engineers, Part O: Journal of Risk and Reliability, 231, 400–410.
Karwowski, W. (2012). The discipline of human factors and ergonomics. In: G. Salvendy (ed.), Handbook of human factors and ergonomics (pp. 3–37). John Wiley & Sons.
Luxhøj, J. T. (2013). Predictive Safety Analytics for Complex Aerospace Systems. Procedia Computer Science, 20, 331–336. https://doi.org/ 10.1016/j.procs.2013.09.281
Rodrigues, S., Paiva, J., Dias, D., Aleixo, M., Filipe, R., & Cunha, J. P. (2018). A Wearable System for the Stress Monitoring of Air Traffic Controllers During An Air Traffic Control Refresher Training and the Trier Social Stress Test: A Comparative Study. The Open Bioinformatics Journal, 11, 106–116.
Sætren, G. B., Hogenboom, S., & Laumann, K. (2015). A study of a technological development process: human factors – the forgotten factors? Cognition, Technology & Work, 18, 595–611.
Safety Management Manual (SMM). (3rd ed.). (2018). International Civil Aviation Organization. Order no. 9859. ISBN 978-92-9249-214-4. https://www.icao.int/NACC/Documents/Meetings/2014/SSPSMSANT/Doc9859.pdf
Skogdalen, J. E., & Vinnem, J. E. (2011). Quantitative risk analysis offshore – Human and organizational factors. Reliability Engineering & System Safety, 96(4), 468–479.
U.S Chemical Safety and Hazard Investigation Board. (2016). Drilling rig explosion and fire at the Macondo well. Investigation report, vol. 3, of 20 April 2016, no. 2010-10-I-OS. U.S Chemical Safety and Hazard Investigation Board.
Copyright information
This work is licensed under a Creative Commons Attribution-NonCommercial-NoDerivatives 4.0 International License.
About this article
Publication Date
31 March 2022
Article Doi
eBook ISBN
978-1-80296-124-9
Publisher
European Publisher
Volume
125
Print ISBN (optional)
-
Edition Number
1st Edition
Pages
1-1329
Subjects
Freedom, philosophy, civilization, media, communication, information age, globalization
Cite this article as:
Deruzhinskiy, G. V., & Kondratyev, S. I. (2022). Comparative Analysis Of Approaches To Personnel Fatigue Management In Transport Ergatic Systems. In I. Savchenko (Ed.), Freedom and Responsibility in Pivotal Times, vol 125. European Proceedings of Social and Behavioural Sciences (pp. 512-525). European Publisher. https://doi.org/10.15405/epsbs.2022.03.62