Abstract
In the era of digital transformation, the concept of Industry 4.0 brings tools, methods, and technologies such as big data, autonomous robots, sensors and actuators, simulation, AR/VR, additive manufacturing, cloud computing, artificial intelligence, internet of things, cybersecurity together for higher levels of effectiveness and creates high expectations both in organizations and individuals. Exploring the advantages of Industry 4.0 has been one of the hottest research topics in recent years; however, its implications on production relations and welfare are rarely discussed. In its highest level of adoption, Industry 4.0 promises lights-out manufacturing or dark factories where the intelligent hardware and equipment replace labour force and brings the discussions on the increasing unemployment and decreasing value of existing human skills and experience. In the relevant literature, there are many academic studies on the effect of Industry 4.0 on work, jobs, and employment, but these studies focus mainly on blue-collar workers. In this context, the current paper aims to examine how engineers who make a significant contribution to the emergence, diffusion, and development of new technologies will be affected by Industry 4.0. By using qualitative data collection and case study methods, the impact of digital transformation in manufacturing on engineering work and jobs are explored. Structured interviews were conducted with the managers, who are also engineers, in two manufacturing companies that operate in the different tiers of the value chain in the white goods industry, which is one of the sectors with the highest level of digital maturity and high value-added in Turkey.
Keywords: Industry 40fourth industrial revolutiondigital transformationtechnologyengineering workwhite goods industry
Introduction
It is imperative to follow the advancements in manufacturing technologies in order to adapt quickly to the ever-changing market demands, to make high quality, low-cost, and efficient production, and to keep up with the global competition (Rojko, 2017). The new reality of production and economy is the concept of Industry 4.0, which has been a trend in recent years (Ślusarczyk, 2018). The concept of Industry 4.0, which is used synonymously with the Fourth Industrial Revolution, was first introduced at the Hannover Fair in 2011 and announced in 2013 as a strategic initiative of Germany (Xu et al., 2018).
Industry 4.0 refers to making devices smarter by aligning traditional production systems with Internet technologies (Lackey, 2014). More specifically, Industry 4.0 is the digital transformation of the entire value chain based on cyber-physical production systems, which are the innovations in digital technology such as the internet of things (IoT), data analytics, robotics, cloud computing, and artificial intelligence (Kowang et al., 2019; Ng, 2020). The definitions mentioned above bring to mind the third industrial revolution. However, the fact that digital technologies used since the third industrial revolution have become more advanced and integrated systems that can transform the global economy and society has given birth to Industry 4.0 and made it different from the third industrial revolution (Schwab, 2016). Brynjolfsson and McAfee (2014) argue that the factors that led to the emergence of Industry 4.0 and differentiated it from other industrial revolutions are innovation based on the recombination of existing parts, exponential developments, and digitalisation.
Obviously, this transformation in the industry will lead to significant transformations in work life, as well. Technologies that contribute to cyber-physical production systems have already begun to change the work practices of scientific management principles that consider people as a part of the business process (De Kok, 2016). The work that means “the performance of some act or skill in return for an economic reward, or in the ultimate hope of receiving some such reward” (Danaher, 2017, p. 43) is now more cognitively sophisticated, team-oriented, time-pressured, mobile, and also requires new skills (Lee, 2016). Furthermore, how technological developments will affect employment is another object of interest. Artificial intelligence (AI) can now drive cars, serve in restaurants, and defeat human champions in games and contests (Bostrom, 2014; DeCanio, 2016), in other words, AI has the potential to surpass the human ability. However, there are many different arguments in the literature regarding the future of work and employment. On the one hand, it is claimed that human labour will not lose its importance in the coming years, and technological advances will lead to an increase in employment (Rüßmann et al., 2015, Spath et al., 2013); on the other hand, it is estimated that some jobs will be lost due to digitalisation (Bowles, 2014).
Demirbağ and Yıldırım (2018) categorized academic publications on Industry 4.0 according to their themes and revealed that Industry 4.0 publications were grouped under five different themes: (1) status quo, trends, challenges and opportunities, and future directions, (2) business models/transformation, system integration, strategic management, process and/or production engineering, (3) education, (4) tools and technologies, and (5) organizational life. The publications, which were gathered under the theme of organizational life, have centred on issues such as human-centred design, hybrid organizations, human-robot interaction, and the future of the work (Demirbağ & Yıldırım, 2018). Mostly, blue-collars are taken into consideration in academic publications on the future of work (Haeffner & Panuwatwanich, 2017; Ras et al., 2017), and this is quite reasonable since robotics and automation will first be substituted with routine and manual tasks that require low skills (Autor et al., 2003). Nevertheless, robots will perform non-standardized and cognitive tasks in a very costly way (Decker et al., 2017), and substitutability cannot be limited to routine and manual tasks alone.
From this point of view, the impact of Industry 4.0 on white-collars should also be examined, and appropriate policies should be developed in areas such as education, labour, and employment security. In the next section of the study, the background of the current problem is presented in light of the relevant literature to limit this highlighted gap and reach a well-defined and precise research question.
Problem Statement
There has been some concern in the literature that automation and digitalisation, accelerated by Industry 4.0 wave, will increase unemployment (Arntz et al., 2016). On the other hand, it is argued that advances in technology create new jobs while making some jobs obsolete (Mashelkar, 2018).
Frey and Osborne (2017) examined the susceptibility of 702 occupations to computerisation to classify them as high-, medium-, and low-risk occupations and to investigate the expected effects of computerisation on the labour market. Their research shows that approximately 47% of the USA’s occupations are in the high-risk group, while the susceptibility of engineering and science occupations to computerisation is low since they require a high degree of creative intelligence. Presently, computerisation is not a substitute for creative science and engineering professions but will be complementary in the long run. Another noteworthy finding of the research is that education and wages show a negative relationship with the probability of computerisation (Frey & Osborne, 2017). Even though occupations that require low skills and low levels of education are in the high-risk group, professions that require high skills and creativity, such as engineering, are ultimately in danger of succumbing to computerisation.
While engineering is defined as designing objects, processes, and systems systematically and iteratively to meet the needs and desires of humanity, technology is a modified form of the natural and designed world to meet human needs and desires, in other words, technology is a product or process that arise from the application of engineering design processes (Quellmalz, 2014). In that case, will the technologies created by engineers, who are the key actors in advancing technology, ultimately take away their jobs? While technology is still complementary to engineering, developing appropriate plans and policies with a proactive approach is critical.
In the literature regarding Industry 4.0 and engineering, there is a limited number of academic publications that focus on the training and educating engineers for Industry 4.0 (Chen & Zhang, 2015; Golob & Bratina, 2018; Richert et al., 2016) and the new skills and competencies needed for Industry 4.0 (Motyl et al., 2017) although more attention needs to be paid to these issues.
Research Questions
The main research question of the current study is to be answered is: How will engineers who work in the Turkish white goods industry, which is one of the most digitally mature sectors in Turkey, be affected by Industry 4.0?
Also, related specific research questions are as follows.
How will the Industry 4.0 transformation affect the engineering job and work?
What are the new requirements for the education and training of engineers?
What are the new competencies and skills expected from engineers?
How will the Industry 4.0 transformation affect the job & task descriptions?
How will the Industry 4.0 transformation affect the number & variety of tasks?
How will the Industry 4.0 transformation change the depth & breadth of technical knowledge?
Will engineering work lose its value and dignity as a result of the Industry 4.0 transformation?
Purpose of the Study
The primary purpose of this study is to examine how engineers, who have an essential role in the emergence of the fourth industrial revolution, will be affected by Industry 4.0 through the case analysis method that is conducted in the Turkish white goods sector.
In line with the primary purpose, sub-objectives of the research are presented below.
Reveal the effects of the Industry 4.0 transformation on the engineering job and work.
Identify the new requirements for the education and training of engineers.
Identify the new competencies and skills expected from engineers.
Explore the impact of the Industry 4.0 transformation on the job and task descriptions of engineers.
Explore the impact of the Industry 4.0 transformation on the number and variety of engineers’ tasks.
Explore the impact of the Industry 4.0 transformation on the depth and breadth of engineers’ technical knowledge.
Explore the impact of the Industry 4.0 transformation on the value and dignity of engineering work.
Research Methods
In this paper, case study method that refers to “an empirical inquiry that investigates a contemporary phenomenon in depth and within its real-life context, especially when the boundaries between phenomenon and context are not clearly evident” (Yin, 2009) is used since case studies are usable when focusing on contemporary events, control of behavioural events is not required, and the form of research questions is “how” and “why” (Yin, 2009, p. 18). The research steps are presented in Figure
Since the white goods sector is one of the three sectors with the highest level of digital maturity (TUBITAK, 2017), it has been selected for research. In this regard, the interviews were conducted with the managers of two white goods companies, one of which is the supplier of the other.
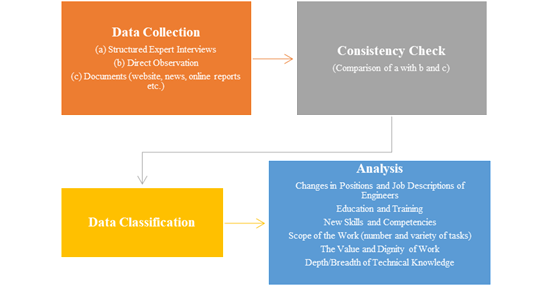
Firstly, the company managers were asked interview questions about the engineering work, and their answers were compared with the data obtained from direct observations and documents, such as the website of the company or related online news/reports, to check the consistency. Table
Findings
Information about the interview participants and the company is presented in Table
The answers given by the firms to the interview questions are summarized and presented below.
Changes in positions and job descriptions of engineers
Digital transformation will not negatively affect the engineering work; engineers are the luckiest ones if they are aware of digital transformation and Industry 4.0 and can keep up with technology.
The number of engineers will not decrease in the medium term, but some departments and positions will not be needed in the long run, such as production, quality, and production planning. On the other hand, R&D employees will not lose their jobs.
The production planning department will disappear because there is no need to plan when everything is visible. Quality engineers will also disappear. Production engineers will not disappear in the medium term but may disappear in the long term. Additionally, the number of maintenance engineers will be reduced, but the number of R&D engineers will surely increase.
Education and training
The company’s engineers join events and workshops regarding Industry 4.0 and received simulation training. As the company aims to increase robot investments, they provide engineers with simulation and offline robot programming training.
New skills and competencies
The scope of the work
The value and dignity of the work
Depth/breadth of technical knowledge
Conclusion
In this study, by the aim of collecting information about the implications of Industry 4.0 application on engineering jobs in manufacturing, face-to-face interviews were conducted with the managers of two white goods companies, and the effects of the fourth industrial revolution on the engineering work and the recent changes in the work of engineers of the companies were explored. All the questions addressed to the company managers were grouped under six topics: (1) changes in positions and job descriptions of engineers, (2) education and training, (3) new skills and competencies, (4) the scope of the work, (5) the value and dignity of the work, and (6) depth/breadth of technical knowledge. When companies were asked whether there were any changes in job descriptions and positions of engineers due to digital transformation, Company A stated that engineers started to work more interactively. On the other hand, the fact that the department of production technologies and Industry 4.0 has been established in Company B can be considered a striking change. Besides, the interviewee from Company B is the “production technologies and Industry 4.0 manager”; that is, there are employees and managers whose title is directly related to Industry 4.0 in Company B. Both companies believe that digital transformation will not reduce the number of engineers, and even complexity may increase the number of engineers needed. Nevertheless, those who cannot keep up with the technology, whether they are engineers or not, can lose their jobs. Both of the managers gave the same answers to the question about which engineering positions would eventually disappear. Production, quality, and production planning departments may disappear over time, but there is nothing to worry about R&D engineers. Company A believes that the level of education expected from engineers will increase and that Industry 4.0 should be given as a course at universities. Both companies have been training engineers or, at least, encouraging them to receive training for a while. Company B has established very systematic training programs for both white- and blue-collars as a large corporation, but Company A encourages its employees to participate in workshops and similar events. When asked what new competencies and skills expected from engineers, Company A stated that engineers should be versatile specialists, while company B thinks that only desire, effort, and enthusiasm are needed. Both companies expect changes in the scope of the work, i.e., the number and variety of tasks. Besides, Company B considers that the digitalisation of processes will make the boundaries of tasks and job descriptions more clear and role conflicts can be eliminated. According to the companies’ responses, the value and dignity of the engineering work will increase since Industry 4.0 will cause engineers who do not improve themselves to lose their jobs, and only the successful engineers will take centre stage. Lastly, companies agree that the depth and breadth of technical knowledge expected from engineers will increase.
The findings of the case study are parallel with the arguments and findings in the literature. As Frey and Osborne (2017) point out, it is unlikely that engineering work will be fully computerized in the short- or medium-term, because the engineering profession requires creative knowledge. Nevertheless, engineers who are insufficient in terms of creative and technical knowledge should not expect an optimistic scenario. Moreover, engineering positions in production, production planning, and quality departments may disappear over time, as they require routine work with less creativity, as stated in the paper of Autor et al. (2003). To lose their jobs in the short- or medium-term does not seem possible for engineers working in R&D positions, which require higher skills and creativity. With the elimination of routine tasks, changes in the job/task descriptions and scope of the work, and an increase in the depth and breadth of technical knowledge are expected. Henceforward, since engineering positions will be available only for well-educated and competent engineers, the value and dignity of the engineering profession will increase.
This paper focuses only on the white goods sector as it is one of the three sectors with the highest level of digital maturity in Turkey. Further research is needed in other digitally mature sectors of Turkey, such as automotive, computer, electronics and optical products, and materials (rubber and plastic) (TUBITAK, 2017). Besides, structured interviews were conducted with the managers of two white goods companies in this study. In the following study, it is planned to increase the number of interviews and to include both managers and expert engineers in the research. Finally, this research assumes that the companies interviewed have a high level of Industry 4.0 maturity due to the fact that they operate in the white goods sector. Expanding the scope of the next research is planned to measure Industry 4.0 maturity levels and present current Industry 4.0 applications of the companies.
Acknowledgments
This paper is based on the Ph.D. dissertation of Kübra Şimşek Demirbağ.
References
- Arntz, M., Gregory, T., & Zierahn, U. (2016). The risk of automation for jobs in OECD countries: A comparative analysis, OECD Social, Employment and Migration Working Papers, 189.
- Autor, D. H., Levy, F., & Murnane, R. A. (2003). The skill content of recent technological change: An empirical exploration, Q. J. Econ., 118(4), 1279–1333.
- Bostrom, N. (2014). Superintelligence: Paths, Dangers, Strategies. Oxford University Press.
- Bowles, J. (2014). The computerisation of European jobs–who will win and who will lose from the impact of new technology onto old areas of employment. Bruegel blog.
- Brynjolfsson, E., & McAfee, A. (2014). The second machine age: Work, progress, and prosperity in a time of brilliant technologies. WW Norton & Company.
- Chen, G., & Zhang, J. (2015). Study on training system and continuous improving mechanism for mechanical engineering. The Open Mechanical Engineering Journal, 9(1), 7-14.
- Danaher, J. (2017). Will life be worth living in a world without work? Technological unemployment and the meaning of life. Science and engineering ethics, 23(1), 41-64.
- DeCanio, S. J. (2016). Robots and humans –complements or substitutes? Journal of Macroeconomics, 49, 280-291.
- De Kok, A. (2016). The new way of working: Bricks, bytes, and behavior. In The Impact of ICT on Work (pp. 9-40). Springer.
- Decker, M., Fischer, M., & Ott, I. (2017). Service Robotics and Human Labor: A first technology assessment of substitution and cooperation. Robotics and Autonomous Systems, 87, 348– 354.
- Demirbağ, K. Ş., & Yıldırım, N. (2018, October). Industry 4.0: Literature Review and Thematic Analysis. In Proceedings of the International Engineering and Technology Management Summit (ETMS2018), (pp. 272-281).
- Frey, C. B., & Osborne, M. A. (2017). The future of employment: How susceptible are jobs to computerisation? Technological forecasting and social change, 114, 254-280.
- Golob, M., & Bratina, B. (2018). Web-based control and process automation education and industry 4.0. The International journal of engineering education, 34(4), 1199-1211.
- Haeffner, M., & Panuwatwanich, K. (2017, September). Perceived Impacts of Industry 4.0 on Manufacturing Industry and Its Workforce: Case of Germany. In International Conference on Engineering, Project, and Product Management (pp. 199-208). Springer, Cham.
- Kowang, T. O., Ying, Y. C., Yew, L. K., Hee, O. C., Fei, G. C., Long, C. S., & Saiful, M. (2019). Industry 4.0 Competencies for Production Equipment Manufacturers in Malaysia. International Journal of Academic Research in Business and Social Sciences, 9(2).
- Lackey, M. (2014). How will the 4th industrial revolution affect your business?. SAPInsider, 15(3).
- Lee, J. (2016). Drivers and Consequences in Transforming Work Practices. In The Impact of ICT on Work (pp. 71-92). Springer.
- Mashelkar, R. A. (2018). Exponential Technology, Industry 4.0 and Future of Jobs in India. Review of Market Integration, 10(2), 138-157.
- Motyl, B., Baronio, G., Uberti, S., Speranza, D., & Filippi, S. (2017). How will change the future engineers’ skills in the Industry 4.0 framework? A questionnaire survey. Procedia Manufacturing, 11, 1501-1509.
- Ng, H. S. (2020). Opportunities, Challenges, and Solutions for Industry 4.0. In Business Management and Communication Perspectives in Industry 4.0 (pp. 32-51). IGI Global.
- Quellmalz, E. (2014). Engineering and Technology: Assessing Understanding of Similarities and Differences between Them. Encyclopedia of Science Education, 1–5.
- Ras, E., Wild, F., Stahl, C., & Baudet, A. (2017, June). Bridging the skills gap of workers in industry 4.0 by human performance augmentation tools: challenges and roadmap. In Proceedings of the 10th International Conference on PErvasive Technologies Related to Assistive Environments (pp. 428-432). ACM.
- Richert, A., Shehadeh, M., Plumanns, L., Groß, K., Schuster, K., & Jeschke, S. (2016, April). Educating engineers for industry 4.0: Virtual worlds and human-robot-teams: Empirical studies towards a new educational age. In 2016 IEEE Global Engineering Education Conference (EDUCON) (pp. 142-149). IEEE.
- Rojko, A. (2017). Industry 4.0 concept: background and overview. International Journal of Interactive Mobile Technologies (iJIM), 11(5), 77-90.
- Rüßmann, M., Lorenz, M., Gerbert, P., Waldner, M., Justus, J., Engel, P., & Harnisch, M. (2015). Industry 4.0: The future of productivity and growth in manufacturing industries. Boston Consulting Group, 9(1), 54-89.
- Schwab, K. (2016). Dördüncü Sanayi Devrimi [The Fourth Industrial Revolution], Optimist Yayıncılık.
- Ślusarczyk, B. (2018). Industry 4.0: are we ready?. Polish Journal of Management Studies, 17(1), 232-248.
- Spath, D., Ganschar, O., Gerlach, S., Hämmerle, M., Krause, T., & Schlund, S. (2013). Produktionsarbeit der Zukunft—Industrie 4.0. Fraunhofer Verlag.
- TUBITAK. (2017). Yeni Sanayi Devrimi Akıllı Üretim Sistemleri Teknoloji Yol Haritası, v2. [New Industrial Revolution Intelligent Production Systems Technology Roadmap, v2.]. http://www.tubitak.gov.tr/sites/default/files/akilli_uretim_sistemleri_tyh_v2-03ocak2017.pdf
- Xu, L. D., Xu, E. L., & Li, L. (2018). Industry 4.0: state of the art and future trends. International Journal of Production Research, 56(8), 2941-2962.
- Yin, R. K. (2009). Case Study Research: Design and Methods (4th ed.). Thousand Oaks, CA: Sage Publications.
Copyright information
This work is licensed under a Creative Commons Attribution-NonCommercial-NoDerivatives 4.0 International License.
About this article
Publication Date
13 February 2021
Article Doi
eBook ISBN
978-1-80296-100-3
Publisher
European Publisher
Volume
101
Print ISBN (optional)
-
Edition Number
1st Edition
Pages
1-224
Subjects
National interest, national identity, national security, national consciousness, social relations, public relation, public organizations, linguocultural identity, linguistics
Cite this article as:
Şimşek Demirbağ, K., & Yıldırım, N. (2021). Can Technology Substitute Its Creator? Impact Of Industry 4.0 On Engineering Work. In C. Zehir, A. Kutlu, & T. Karaboğa (Eds.), Leadership, Innovation, Media and Communication, vol 101. European Proceedings of Social and Behavioural Sciences (pp. 142-151). European Publisher. https://doi.org/10.15405/epsbs.2021.02.13