Abstract
The authors examined the issues of digital transformation processes for enterprises in discrete engineering, the task of creating digital twins of the objects of industrial production. Digital twin must have the capacity to quickly respond to emerging internal and external changes, while maintaining system operational functions. The features of manufacture organization at a machine building enterprise are defined. It is determined that sustainable development of one of the technological ways can be achieved only under the condition of all components of human society balanced development, the harmonious interaction between all external and internal variables of the “people and the environment” system. Businesses have always sought to improve the production process to reduce costs and accelerating approach to market. It is shown that for machine-building enterprises the purpose of creating the digital twin is the improved company resource base utilization to increase the volume of the exhaust product at the lowest cost value. The basic steps determining the required volumes of digitalization for the engineering company are set up. A unified methodology of estimation of costs required to implement the above tasks is proposed. The structure of the method of the digitalization cost estimation for the engineering enterprise is determined. It is concluded that a profound and systematic study of the basic methods and tools, as well as the development of new methodologies for assessing the potential of a digital transformation of manufacturing companies is the determining factor in the activities of the digital economy project initiators.
Keywords: Production enterprise digitalisationengineering companiesdigital twinsdigital modellingcost estimate
Introduction
The enterprises of the domestic machine-building complex have always occupied the most important place among other companies in the industrial sector of the economy, however, over time, the problems of ensuring their competitiveness are most acute. The existing scientific and methodological base is on the verge of depletion, the costs of applied research often require large amounts of investment, and the production and management structure require the introduction of optimization projects and scientific and technological development (Tsvetkov, 2016).
The formation and improvement of the competitive potential of machine-building production in Russia in the medium and long term will depend on the amount of investment in updating the material and technical base of enterprises and the level of competitiveness of products in the domestic and foreign markets. The main factor in the formation of demand for engineering products will be the investment activity of consumers. And as a result of the intensification of innovation in engineering, the level of competitiveness of the industry should increase both in the domestic and foreign markets (Borovkov & Ryabov, 2017).
The positive results of the proposed scenario for the innovative development of the industry should include:
an increase in the number of innovation-oriented enterprises in the engineering industry;
reducing the time range for the creation and development of new products through the implementation of research and development results;
increase in the co-financing share from extrabudgetary sources;
increasing the probability of the investment projects implementation effectiveness the feasibility of choosing priority areas of research and development.
From the perspective of the production organization, a machine-building enterprise is characterized by the following features:
long production lags, which begins with the stage of product design and ends with mass production;
various production scaling (from small-scale to large-scale);
a wide range of manufactured units and parts;
complex logistics (long delivery time);
the need to attract intermediary services, etc.
In this study, the authors would like to consider the problems of digital transformation of a machine-building complex enterprise in modern economic conditions and evaluate the costs necessary for this.
Problem Statement
The formation and dynamics of one of the technological structures should be considered as a mechanism to advance towards the next structure. At the same time, it is necessary to satisfy current socio-economic needs, taking into account the projected trends in the development of human society. Today, there are a number of different kinds of changes, both in the social and economic aspects. Sustainable development of one of the ways can be achieved only if the balanced development of all components of human society, the harmonious interaction among all external and internal variables of the system: a human being → the environment.
Observing the evolution of the economy during the formation of the fifth structure, it is possible to establish a clear tendency for innovation to penetrate - the emergence of new industrial sectors and the development of new types of products. The emergence of new equipment with programmed numerical control contributed to an increase in productivity and efficiency, as well as an increase in added value in individual sectors of the economy (Kovalchuk & Stepanov, 2017).
From the authors' point of view, digitized information systems can become an aggregated mechanism of a common technological breakthrough. At the same time, industrial companies will act as only one of the platforms for modern industrial development. In the domestic economy, at the present stage digitalization in industry, including the machine-building complex, is still at the stage of diffusion and testing. According to experts (Kovalchuk & Stepanov, 2016), in the Russian Federation there has recently been some positive dynamics regarding the introduction of advanced technologies, but this mainly concerns the extractive industries, while in engineering these processes are not active enough.
Considering the evolutionary processes of the development of modern production, we can conclude that enterprises have always sought to improve the production process in order to reduce costs and accelerate market entry. Previously, companies focused on improving the efficiency of single processes. In the Program “Industry 4.0”, the concept of process improvement is focused on the integration of processes within the organization, the supply chain and the product life cycle (Stefanova & Pochebut, 2017). This is due to the new idea of using smart tools at every stage of the value creation chain.
Research Questions
There are many points of view regarding the introduction of digital transformation in discrete machine-building enterprises and the tasks of creating digital twins of industrial production facilities; directions of improving the production process in order to reduce costs and accelerate market entry. All this actualizes the study and development of new methods and tools for assessing the digital transformation potential of manufacturing companies.
Purpose of the Study
The purpose of this research is to study the essential content of the problem of digital transformation of an enterprise of a machine-building complex in modern economic conditions and to assess the necessary costs.
Research Methods
A digital twin is a virtual copy of a real object, repeating its behaviour and describing electronically all internal processes and relationships. In other words, the digital twin makes it possible to evaluate and analyse the functioning of the studied object in order to predict its actions and visualize the operation of the entire system. One of the main tools for creating such a twin is simulation modelling (Semenova, 2017).
To create a digital twin of a single industrial enterprise, it is necessary to use the project approach, within which the main goals and objectives should be formulated and implemented. These tasks include visual acquaintance with the main production, identification of the main modelling products, obtaining and analysing the source data for further modelling, development of the digital model itself, formation of a process road map for the functioning of this model. At the same time, one of the important stages is the need to assess the costs of carrying out work on the implementation of these tasks (Avdeeva, 2017).
For a machine-building enterprise, the goal of creating a digital twin (3D clone) will be improvement of the effectiveness of using the company's resource base to increase output volumes at a minimum cost. To the tasks of building a digital simulation model of the enterprise, we consider it possible to include:
use of system analysis to build a model of capacity utilization;
assessment of the production potential of the enterprise in order to determine the maximum possible volume of products;
identification of necessary extra capacities;
calculation of optimal launch lots;
identification of “bottlenecks” in the entire technological chain;
expansion of the finished products volume.
The functions of a digital twin include identifying critical areas in an enterprise where monitoring devices capable of measuring, then processing, transmitting, and storing large volumes of incoming information (Big Data) should be located.
In addition to the description of the existing object (industrial enterprise), the digital twin should have the ability to quickly respond to emerging external and internal changes, while maintaining the working functions of the system. For example, to respond flexibly to currency fluctuations, or unexpected actions of competitors.
Analysing the experience of the Engineering Centre “Centre of computing engineering” of Peter the Great St. Petersburg Polytechnic University (SPbPU) we can conclude that one of the mandatory elements for the development of digital twins is the compilation of a multi-level matrix of assessment criteria and resource constraints (Aksyonov et al., 2018). Such a matrix is designed to implement a certain balance of a significant amount of available data about the analysed object, which often conflict with each other. To compile such a matrix, it is necessary to create digital platforms that provide the necessary degree of automation of ongoing development processes. All this entails the digitalization of control systems and the further integration of digital platforms and economic systems into a single space (Ereshko & Medyannikov, 2018).
Undoubtedly, the implementation of the above-mentioned trends in real life should be supported by relevant regulatory documents and legislative framework. This requires the development of relevant standards and regulations, as well as the necessary teaching materials that will ensure the adequate implementation of all processes.
From the point of view of leading economists (Borovkov et al., 2018), the digital twin is a family of complex multidisciplinary mathematical models with a high level of adequacy to real objects.
Creating a 3D model of the enterprise is carried out in order to use it as a source of real information that makes it possible to plan the territory of the plant and production, to draw up a specification of production and auxiliary equipment, engineering and architectural and construction parts. In addition, the generated model will contribute to a number of functions:
analysis and optimization of the main production location;
analysis and optimization of production logistics;
express assessment of modernization (reengineering) options for production;
verification of technical and managerial decisions made.
Therefore, the created model of the enterprise will be the basis for reconstruction and expansion of production, a kind of layout “foundation” for the subsequent modelling of business processes within the enterprise and the development of a production simulation model. Such a model will be intended for the preparation of visual and graphic documentation for all objects within the enterprise, including modelling of the main production buildings and structures, railways, and highways. This will help optimize inter-workshop and intra-workshop logistics and increase the efficiency of production facilities.
Modelling of technological operations is carried out in order to refine the technology used and verify the application of operations based on the developed supporting documentation. The optimized parameters of a machine-building enterprise may include the following: equipment parameters, trajectories of the premises, assembly sequence of units, labour input, etc. (Popov & Semyachkov, 2017). This raises the question of the possibility of assessing the volume of digitalization in an industrial enterprise and assessing the necessary costs.
In order to determine the amount of digitalization for a discrete machine-building enterprise, it is necessary to carry out the following steps:
make a list of all objects included in the structure of the analysed enterprise (their list and quantity);
form technologies necessary to use within the framework of “Industry 4.0”;
collect the necessary data to determine the desired parameters (to be digitized);
identify key metrics and assessment drivers;
analyse the costs distribution;
make the selection of relevant tools;
draw up a road map.
Findings
After determining the necessary volumes of digitalization, the question arises how to correctly assess the necessary amount of investment. Since today there is no single approved assessment methodology, the authors made an attempt to develop the proposed calculation methodology. Figure
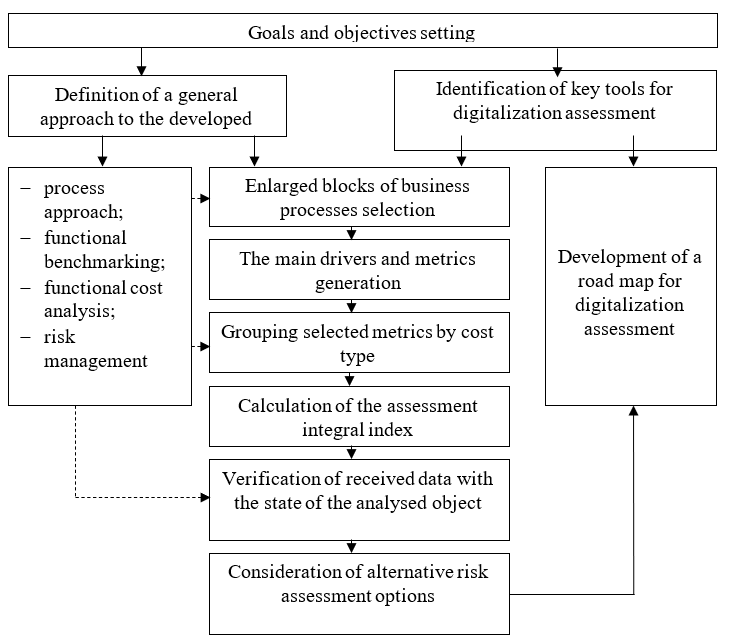
The following is the structure of the methodology for estimating the costs of digitalization for a machine-building enterprise.
The content of the estimation methodology.
1. Problem statement.
1.1. General Provisions. The purpose of the document.
1.2. Terms and Definitions.
2. Definition of a general approach to the methodology being developed.
2.1 Methodology of digitalisation assessment.
2.2 Functional Benchmarking Methodology.
3. Identification of key assessment tools.
3.1 Determination of the readiness index of the enterprise to work in digitalization environment based on international experience
3.2. Using a process approach
3.2.1 The choice of the composition of the evaluated business processes enlarged blocks
As groups of factors, a breakdown of business processes is carried out into enlarged groups, each leading to an increase in the efficiency of the enterprise:
production and technological business processes;
financial and economic business processes;
organizational business processes.
3.2.2. Factor analysis of assessment issues. A set of variable factors affecting the performance of the production system (expert assessment method).
3.2.3. Metric system development In the context of each group of the business process of the digitalization object, a system of metrics should be developed that assess the impact of each key factor on the cost. Evaluation and analysis of the mismatch of actual indicators with the planned ones allows to identify the direction and characteristics of the control actions, which should return the values of the indicators into the tolerance limit. Thus, the dynamics can be monitored for the evaluation criteria of the digitalization of the enterprise and a mechanism to ensure the conditions for the implementation of this methodology formed.
3.2.4. Formation of cost groups by type:
labour costs,
time costs,
value costs.
(source: company reporting forms (based on the example of a particular enterprise) on fixed assets, working capital, personnel, production cost, investments, profit and loss, balance sheet)
This refers to any abstract enterprise as part of a discrete mechanical engineering complex.
3.3. Calculation of the assessment of digitalization integral indicator (based on established metrics)
3.4. Cost optimization options. Applying functional cost analysis
The main steps:
Divide the evaluated object into main blocks (system - subsystems)
Calculate the averaged costs: materials, fuel, energy, etc.
Choose one of all blocks and take it as a standard, then adjust the rest ones to the standard with the developed coefficients
The coefficients will be developed based on Federal State Statistic Service data and the standard coefficients used for in-line production, taking into account amendments approved by the Ministry of Industry and Trade of Russia in modern conditions. At the same time, using the example of one block, it is possible to optimize costs due to the FSA (to determine the directions for reducing the block cost due to individual nodes or large parts).
3.5. Development of a road map for digitalization assessment.
3.6. Verification of the obtained results with the state of the analysed object - functional benchmarking. Using the express method for determining the enterprise readiness index in digitalization based on calculated indicators.
3.7. Consideration of alternative assessment options using risk management techniques based on the volatility of foreign markets.
Conclusion
Currently the development of human society and the available amount of knowledge and technologies used, creating a picture of the future digital society, and predicting the results of the implementation of the proposed scenarios for the development of the digital economy seems rather difficult. Nevertheless, the digitalization processes in all areas of the national economy as part of a change in technological patterns is an inevitable and logical process. Consequently, a deep and systematic study of the basic methods and tools, as well as the development of new methods for assessing the digital transformation potential of production companies, including the engineering complex, is becoming one of the most important moments in the activities of initiators of digital economy projects. Thus, enterprises in the industrial sector should actively participate in the implementation of such projects, become initiators of the development of programs to digitalize enterprises in the framework of increasing their competitiveness in the domestic and foreign markets.
References
- Aksyonov, D. A., Kuprikov, A. P., & Sahakyan, P. A. (2018). Napravleniya i osobennosti primeneniya blokcheyn-tekhnologii v ekonomike [Directions and features of the blockchain technology use in the economy]. St. Petersburg State Polytechnical University Journal. Economics, 11(1). https://doi.org/10.18721/JE.11103
- Avdeeva, I. P. (2017). Analiz perspektiv razvitiya tsifrovoy ekonomiki v Rossii i za rubezhom [Analysis of the prospects for the development of the digital economy in Russia and abroad]. In A.V. Babkin (Ed.), Scientific and Practical Conference with International Participation on Digital Economy and “Industry 4.0“: Problems and Prospekts (pp. 19-25). SPbPU. [in Rus]
- Borovkov, A. I., Ryabov, Yu. A., & Maruseva, V. M. (2018). Novaya paradigma tsifrovogo proektirovaniya i modelirovaniya global’no konkurentosposobnoy produktsii novogo pokoleniya. Tsifrovoe proizvodsnvo. Metody, ekosistemy, tekhnologii [The new paradigm of digital design and modelling of globally competitive products of the new generation. Digital production. Methods, ecosystems, technologies]. Department of corporate training of the Moscow School of Management. SKOLKOVO. [in Rus]
- Borovkov, A. I., & Ryabov, Y. A. (2017). Perspektivnye napravleniya razvitiya peredovykh proizvodstvennykh tekhnologiy v Rossii [Perspective directions of development of advanced production technologies in Russia]. In E.G. Yasin (Ed.), XVIII April International Academic Conference on Economic and Social Development, Vol.3, (pp. 381-389). HSE. [in Rus]
- Ereshko, F. I., & Medyannikov, V. I. (2018). Formirovanie tsifrovoy platformy APK [The formation of the digital platform of the agricultural sector]. In Proceedings of the 1st International Conference on Futurity designing. Digital reality problems (pp. 65-73). https://doi.org/10.20948/future-2018-10http://keldysh.ru/future/2018/10.pdf [in Rus].
- Kovalchuk, Y. A., & Stepanov, I. M. (2017). Tsifrovaya ekonomika: transformatsiya promyshlennykh predpriyatiy [Digital economy: the transformation of industrial enterprises]. Innovation in management, 11, 32-43. [in Rus]
- Kovalchuk, Y., & Stepnov, I. (2016). Novaya organizatsionnaya real’nost‘: sistema pokazateley ili proektny ofis? (o soderzhanii organizatsii proizvodstva v XXI veke [New organizational reality: system of indicators or design office? (about the maintenance of the production organization in the XXI century)]. In S.G. Falko (Ed.), VII International Congress on Controlling Services (pp. 118-124). NP “Association of controllers”. [in Rus]
- Popov, E. V., & Semyachkov, K. A. (2017). Osobennosti upravleniya razvitiem tsifrovoy ekonomiki [Features of managing the digital economy development]. Management in Russia and Abroad, 2, 54-61. [in Rus.]
- Semenova, Y. A. (2017). IT-ekonomika v 2016 godu i cherez 10 let [IT economy in 2016 and in 10 years]. Economic strategies, 1(143), 126-135. [in Rus.]
- Stefanova, N. A., & Pochebut, V. A. (2017). Mify i realii tsifrovoy ekonomiki v Rossii [Myths and realities of the digital economy in Russia]. Topical issues of the modern economy, 4, 13-17. [in Rus.].
- Tsvetkov, V. A. (2016). Realizatsiya strategiy novoy industrializatsii ekonomiki [Implementation of the strategies of the economy new industrialization]. Humanities and Social Sciences. Bulletin of the Financial University, 6(96), 19-30. [in Rus.]
Copyright information
This work is licensed under a Creative Commons Attribution-NonCommercial-NoDerivatives 4.0 International License.
About this article
Publication Date
21 October 2020
Article Doi
eBook ISBN
978-1-80296-089-1
Publisher
European Publisher
Volume
90
Print ISBN (optional)
-
Edition Number
1st Edition
Pages
1-1677
Subjects
Economics, social trends, sustainability, modern society, behavioural sciences, education
Cite this article as:
Komissarova, M. A., Razorenova, E. Y., Storozhuk, I. N., & Guzenko, N. .. (2020). The Possibility Of Industrial Enterprises Transformation In The Digital Environment. In I. V. Kovalev, A. A. Voroshilova, G. Herwig, U. Umbetov, A. S. Budagov, & Y. Y. Bocharova (Eds.), Economic and Social Trends for Sustainability of Modern Society (ICEST 2020), vol 90. European Proceedings of Social and Behavioural Sciences (pp. 419-427). European Publisher. https://doi.org/10.15405/epsbs.2020.10.03.47