Abstract
This paper outlines research carried out into geo-ecological technology for the treatment of water to remove oil particles in conditions resulting from accidental oil spills during off-shore petroleum operations. A conceptual diagram for the treatment of oil and water mixtures in the clean up of accidental oil spills and a basic process diagram for the removal of oil particles from water is proposed. The technological flow of operations is described for the primary treatment of water containing oil. In order to improve the efficiency of the process for the treatment of oil and water mixtures, a diagram has been developed which combines flotation units and refitted sedimentation units for the implementation of treatment processes by absorption. A scheme using interconnected filters is also considered, which provides more efficient use of the adsorption layer. A process has been proposed using an advanced sedimentation device to enable the device to incorporate absorption processing processes. The basis of the theoretical rational are the results of research into the dispersion phase behavior of mixtures of oil products and water, which have been taken from the surface of a body of water in accidental spill clean up operations. The proposed method allows the use of coagulation as a means of purification of water subjected to processing, to increase the efficiency of sedimentation.
Keywords: Geo-ecological technologyoff-shore petroleum operationsoily mixturesoptimisation of water treatment processeswater treatment
Introduction
One of the most pressing problems in exploration and development of off-shore oil and gas fields and the marine transport of oil, is that of ensuring ecological safety. The particularities of modern technology and the equipment used, to a large extent, are determined by the safety level required by the organisation in the carrying out of these operations. At the same time, it is understood that any technological process is characterised by a particular level off risk, which cannot be totally eliminated (Alkhimenko, 2012). It is only possible to ensure an acceptable level of probability of an accident occurring, that is hand in hand with developing and implementing measures to ensure the required level of probability of an accident occurring, it is also necessary to be prepared to deal with any accident which might occur, and to deal with its consequences (Aibulatov, 2015; Minin & Krupnov, 2010).
Current thinking on ensuring ecological safety during the carrying out of petroleum operations in off-shore conditions is, in general, is reflected by an understanding of the necessity of implementing a range of organisational and technological measures to eliminate accidental spills, that is a transfer of oil or oil products to the surface of the water (Fay, 1971; Kachala, 2007; Krupnov, 2004, Standard, 2010).
The basic methods for the treatment of water that has been contaminated by oil, which have been most widely accepted in current day processes are sedimentation, flotation, adsorption and oxidisation. Furthermore, in order to raise the efficiency of treatment processes, methods such as coagulation and coalescence are used to process the water (Zhigulskii, 2009; Reshnyak, & Zhigulskii, 2006). The choice of and rationalisation for treatment process diagrams, assume the choice of the treatment method which is both most efficient and least expensive. Therefore the optimisation of treatment processes is an essential part of the computation of these processes.
At the present time, in oil spill clean up operations, water which has been contaminated with oil is transported to treatment units, which, in general, are not economically justifiable, taking into account the fact that the accidental spill may have taken place in regions which are far from the treatment units. Technology for the treatment of water which has been contaminated with oil must guarantee a quality of treatment which enables the water to be returned immediately to the body of water from which it was taken. When the task of rationalising the choice of technology for the treatment of water which has been contaminated by oil is stated thus, the expenditure on the cleaning up of accidental oil spills can be reduced. The implementation of these tasks requires that the treatment processes be optimised, and that technology end engineering proposals be developed, which ensure the required quality of treatment of the water, with minimum expenditure, and which can be used in carious forms such stationary treatment units, movable treatment units and floating treatment systems.
Problem Statement
According to the results of the system analysis, to propose effective methods to eliminate and prevent emergencies during the development of offshore oil and gas fields. In order to eliminate the consequences of emergency oil spills during the development of offshore oil and gas fields, it is necessary to investigate and substantiate the geo-ecological technologies for processing the oil / water mixture and create a methodology for optimizing the parameters of sedimentation devices for cleaning the oil and water mixture.
Research Questions
The main research questions in accordance with the purpose of the study are:
systematization of the operation of extracting and cleaning the mixture of oil and water, creating a concept for cleaning the oil and water mixture in order to eliminate the consequences of an emergency spill;
study of the layers of water and oil, which are subsequently formed by an emergency spill, the study of local areas representing a dispersed system with desired properties, the technology of processing a mixture of oil and water formed during an accident, which must be selected depending on the properties of dispersed systems;
development of geoecological technology and oil-water mixture purification schemes.
Purpose of the Study
The main goal of the work is to research and propose a geo-ecological water treatment technology to remove oil particles from oily water, subsequently formed as a result of oil spills.
Research Methods
The study uses methods of system analysis (Kachala, 2007; Reverberi, 2016), methods for cleaning and processing oil / water mixtures (Nazarov, 1996), methods for treating water treatment using sedimentation, absorption and coagulation methods (Zhigulskii, 2009; Aliyev, 1981), optimization methods and statistical data processing methods, as well as constructing graphical dependencies (Chernorutskiy, 2011; Steuer, 2015; Gmurman, 2006).
Findings
The main aim in accidental oil spill clean up operations which have occurred during off-sure petroleum operations, is to maximise the reconstitution of the initial components of the mixture, ie the water and the oil, or the utilisation of these comments.
Analysis of the principle of movement and construction types of oil recovery vessels, as well as the results of research into the models for oil slicks and their adjoining area leads us to propose the following technology for the treatment of oil and water mixtures.
The primary separation of the mixture can be effectively carried out in so-called aquatic operations, that is simultaneously with the removal of the oil from the surface of the body of water (see Figure
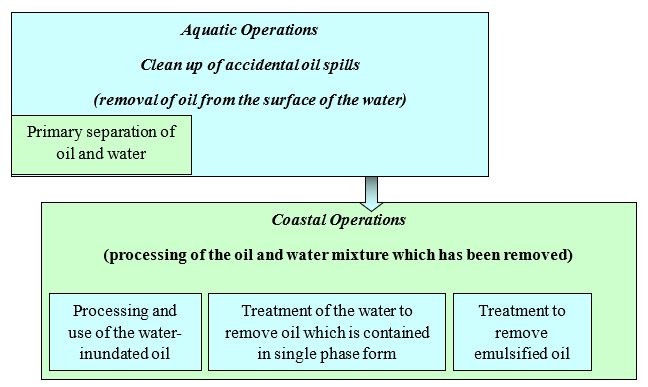
Taking into account the fact that the water mixture which has been removed contains oil or oil products, which are present in the water in single phase form, as well as in an emulsified form, the following operations are required in the technological process of its treatment:
operation to remove oil or oil products, which are present in a single phase form, from the water;
operation to remove emulsified oil from the water. Water, which has been treated to the required standards, is returned to the body of water from which it was taken. The volume of water contaminated by oil which requires treatment, and the oil, depending on the type of oil recovery vessels used, may make up, up to 90-95% of the total volume of oil and water mixture collected from the surface of the water. The final design of the process diagram for the treatment process is determined by the requirements for the return of treated water to natural bodies of water.
Effective methods of treatment of water which contains oil in single phase form and large drops include sedimentation, absorption and flotation (Kurinkov, 2002; Timofeyev, 1982). Equipment required for absorption and sedimentation methods is sufficiently simple to construct and these are the most economically treatment methods.
For the removal of emulsified oil, the most effective method is adsorption (Reshnyak, 1985, Koganovskii, 1991). Furthermore, the treatment technology must allow for the possibility of working when the water contains suspended particles, which may reduce the efficiency of the adsorption filters. In order to remove suspended particles, it is recommended that filtering is used, for example using filters made from polymers.
In cases where the water has a high oil content (up to 40-70%), most of the water can be separated by treating the oil by filtration using layers of material which absorb water but allow oil to pass through. This method is recommended for the separation of mixtures where the water is formed as small dispersion particles. If the water content is present as large drops or single phase, then sedimentation or separation cone methods can be used, which are also reliable and inexpensive means of separating oil and water.
The oil treatment methods which have been considered are relatively inexpensive and provide for reliable treatment to remove water from the oil reducing the water content to 15-25%, that is, to a particular level of water content, which allows for the efficient burning of the water-inundated oil.
In this way, based on an analysis of the results of the research into the processes taking place in oil slicks and resulting in the formation of various types of dispersion systems in different parts of the layer, processes for treating the oil and water mixture, which is removed from the surface of the body of water in oil clean up operations, have been proposed. As a whole, such processes should include operations for the primary separation of the oil and water mixture, treatment of the water to remove oil, and also preparation of the water-inundated oil for use.
Generally speaking, water treatment processes have a particular sequence and include operations for the cleaning, treatment and decontamination of water (Shevchenko & Lizunov, 1990; Kulskii, 1980).
The composition of the above-named types of operations is determined by the following factors: the quantity and quality requirements for the water after treatment (Kasatkin, 2016). The quality of the treated water is characterised by the concentration of pollutants and the state of the pollutants.
Pollutants in the water being treating may be found in one of two basic forms: dispersed, that is the form of the dispersion phase, and in solution. The dispersion form is characterised by dispersion particles of the pollutant.
The oil contaminated water which is being cleaned, consists of a mixture of oil and water, in which the oil may be in single phase form (layer) and large drops, and also in the form of emulsified particles. Furthermore, the water which is undergoing treatment may contain suspension particles.
From all the above, it follows that the process for the treatment of oil-containing water must include:
means of removing oil which is present in a separate layer and large drops (primary treatment);
means of removing emulsified oil products (deep cleaning);
means of removing suspended particles.
In this way, the fundamental process diagram for the treatment of oil-containing water can be shown as in Figure

In addition to this, the process diagram for the cleaning must include the means of treating the water for the intensification of the specified means of cleaning.
For the primary treatment, it is recommended to use sedimentation, which requires simple equipment and is a reliable cleaning method. The dependence of the speed of sedimentation (see Figure
Treatment by sedimentation to remove smaller particles, is possible, but requires a greater outlay of time, which, on the whole, leads to a lowering of the treatment effectiveness, when considering both economic and ecological parameters.
The efficiency of the sedimentation can be increased, if the water is processed using such treatment methods as coagulation. In this case, viable treatment by sedimentation can be carried out in two stages and with coagulation being provided prior to secondary sedimentation.
The combination of sedimentation and coagulation has the following effect. At the primary sedimentation stage, oil, which is present in the form of a separate layer or large drops which have dimensions more than 0.5mm – 1mm is removed from the water which is being treated.
During the coagulation operation, the oil which is in the form of particles measuring less than 0.5mm-1mm are enlarged resulting in particles. Such particles are able to be separated quickly enough, from the rest of the water being treated, during the secondary sedimentation process (Orazbayev, Karabalin, & Serikov, 2018).
In order to remove oil and oil products which are present in single phase form or as large bodies from water, an absorption method of treatment is recommended. Such a method can be carried out using simple technology, which can be implemented inside a sedimentation device. In order to organise the absorption process it is recommended that oil and oil products which have been removed from the water being treated, be used as an absorptive layer.
Figure
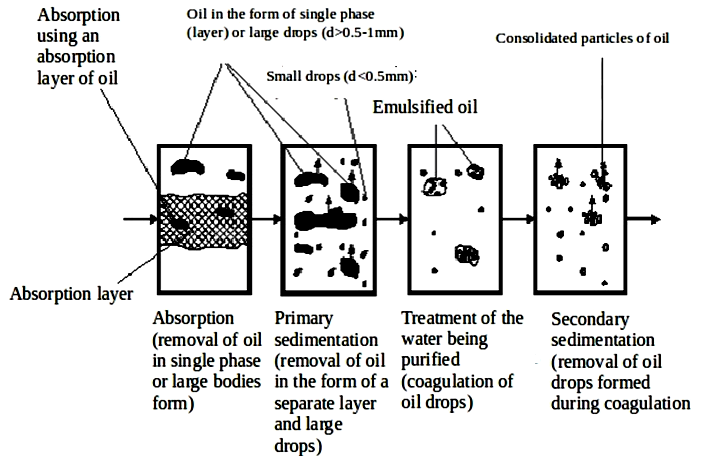
Currently, pressure flotation is generally used, either single flow or recirculating. Flotation allows for a recovering of dispersion particles with dimensions of up to 20-50µm (Bruselnitskii, 1986; Zhukov, Mongait, & Rodziller, 2007). Therefore flotation is the method recommended for use after sedimentation, primary and secondary. The effectiveness of the treatment by flotation is increased if, prior to flotation, coagulant is added to the water being treated.
An analysis of various approaches which have been used for treatment in order to remove emulsified oil in various fields, shows that emulsified oil can be removed using a variety of methods (Kulskii, Goronovskii, Koganovskii, & Shevshenko, 1990; Tuv & Lahov, 2018). The most effective method using the simplest technology is that of adsorption.
Adsorption can be carried out as a multi-stage operation using several consequential filters. In using this combination of adsorption filters, any combination of their connection must be provided for.
The rationality for the viability of such a technological diagram for deep cleaning using an absorption method is determined the peculiarities of the adsorption process and is detailed below.
The functioning of adsorption filters is characterised by a curve С=С(Н) for changes in concentration of pollutants against the height of the adsorption layer. As the filter works, its adsorption reduces layer by layer, which is reflected in the path of the curve С=С(Н) according to the height of the adsorption layer. This simultaneously leads to an increase over time in the concentration of oil products in the water being treated, for example at point h1. This change in concentration is shown in Figure
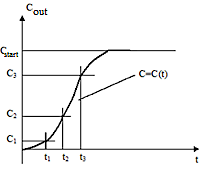
In the section of the adsorption layer for which С(Н) has reached the value of Сstart (i.e. the initial value) or С (С is the concentration which is equal to the required degree of cleaning), the cleaning process is terminated, and the relevant part of the layer is replaced. That said, another section of the layer may still be functioning. However, if constructional, the whole adsorption layer is loaded into one filter, then the whole unit must be changed, which leads to inefficient use of the adsorption materials.
Therefore it is recommended that the unit consist of several filters, distributed so as to give a total height Н of the adsorption layer using several filters. The proposed method of connecting filters allows for the effective use of the total height of the complete adsorption layer.
The water being cleaned may contain suspension particles which on entering the adsorption filters, become stuck in them. In this event the adsorption capacity of the filter will be reduced, and the adsorption filter will not be being used as intended. In order to avoid this negative effect, it is possible to provide for the filtering out of suspension particles in the treatment process diagram.
In order to implement the above, we are proposing a package of process and technical solutions for the treatment of water which has become contaminated with oil. We consider the process flow for the treatment of ballast water and water from other off-shore sources on flotation units. Flotation units are in themselves complex devices, in which several different, both in purpose and process, treatment devices are constructed together. Water enters such a device through suction pipe (1) (Figure
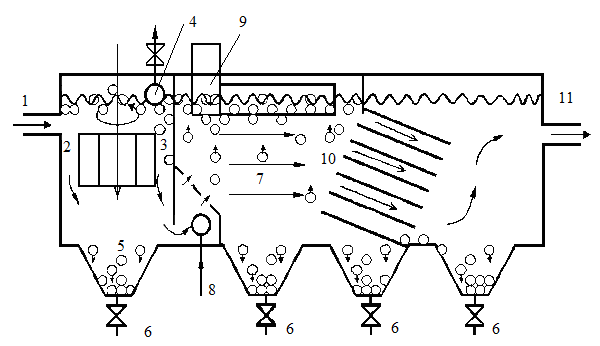
For more thorough mixing of the reagents with the water being treated and coagulation, the polluted water being treated is mixed with a bladed mixer (3). Part of the impurities (3) float up to the upper part of the chamber and are drawn off through the device (4). Part of the impurities (5) precipitate in one of the catch basins (6) from which they are periodically drawn off. Thereafter, the water enters the flotation chamber (7), into which air-saturated water is supplied via a pipe (8). The flotation chamber is equipped with a device (9) to remove foam and impurities from the flotation chamber. Leaving the flotation chamber, the water flows through a device (10) for fine-grained sedimentation. This device is formed of a block of parallel and plates, positioned at an incline. A collection tank for the collection of pollutant sediment, from which it is periodically removed, is provided in the lower section of the flotation unit. The treated water leaves the flotation unit by a pipe (11).
The process flow provides for two stages of treatment by flotation and by fine grade sedimentation. This is implemented by constructing two flotation units which are combined sequentially. Such a proposal is connected with the fact that the bottom water is more heavily polluted by oil and oil products than the storm drain water. Having said that, the requirements for the treated bottom water are higher, since, the disposal conditions mean that this treated water is returned to the sea.
The follow process flow chart is intended for the treatment of ballast water and polluted water from marine sources, and completes the previous process diagram (see Figure
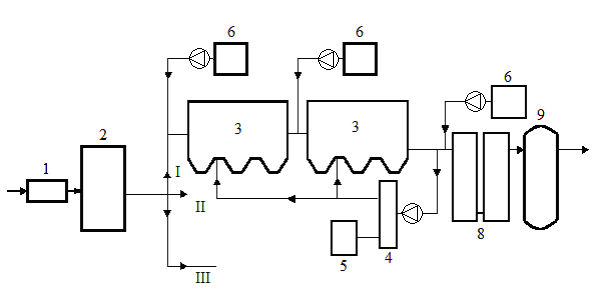
The process line includes combined flotation units, which in principle are no different from the flotation units on the second line. During the treatment of the ballast water and the polluted water from marine sources, sand traps and collection tanks, the concentration of oil products and suspended particles are reduced accordingly to Сop=150 mg/l or Сsp=100 mg/l.
After the 1st stage of flotation and fine-grain sedimentation, the concentration of oil products in the water being treated is Сop-70-80 mg/l and the concentration of suspended particles Сsp=40 mg/l. After the 2nd stage of flotation and fine-grain sedimentation the concentration of oil products in the water being treated is Сop=10 mg/l and the concentration of suspended particles is Сsp=10 mg/l. After the 1st stage of pressure filtration, the concentration of oil products in the water being treated is Сop=5-7 mg/l and the concentration of suspended particles is Сsp=3-5 mg/l. After the 2nd stage of pressure filtration the concentration of oil products in the water being treated is Сop=1-3 mg/l and the concentration of suspended particles is Сsp=3-5 mg/l.
After the adsorption filters, that is at the end of the water treatment process line, the concentration of oil products in the treated water is Сop=0.05 mg/l and the concentration of suspended particles is Сsp=1-2 mg/l.
The refitted sedimentation unit for the provision of treatment processes by absorption. In order to remove oil and oil products from water, in cases that a considerable volume of oil and oil products are present in the water in a single phase form, it is recommended that an absorption process is used for treatment. This process is sufficiently effective and can be implemented in any chamber, for example in a sedimentation unit. Sedimentation units can be refitted, without a great deal of expenditure, in order for them to provide the process of treatment by absorption. Such a piggybacking of treatment processes (absorption and sedimentation) within one device, does not impact their effectiveness, but allows for a cost reduction when compared to the cost of producing separate devices for these processes. The following simple solution specified below is then reached.
The sedimentation unit (1) (see Figure
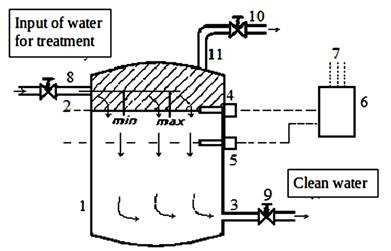
The sedimentation unit is equipped with a pipe for the removal of oil and oil products (11). When the sedimentation unit is functioning in cleaning mode, oil is collected in a container. In this regime valves 8 and 9 are open. The oil-water separation limit, as oil is collected, becomes lower, and reaches the lower level sensor, which is positioned at the point of maximum collection of oil.
The lower level sensor (5) reacts to the oil and provides a signal to the control unit (6), which, via the control system (7) closes valve 9 and opens value 10 which is on the oil removal pipe. At that moment the sedimentation device begins to function in the oil removal mode. Oil is removed from the unit via pipe 11. In this way the oil-water limit rises, and within a specified time reaches the level of the upper level sensor (4), which is located at the point of minimum collection of oil. This point must be lower than pipe 2, the pipe which delivers water for treatment. Such relative positioning of sensors 4 and 5 and pipe 2 allows for the presence of an absorption layer of oil, through which the water being treated flows, and which will remove any oil which is present in the water in single phase or large drop form. The thickness of the layer will vary between a minimum value, as shown in Figure
Such a method of refitting a sedimentation unit, may find wide use in local treatment units, used for the treatment of oil-water mixtures, for example in clean up operations following accidental spills of oil or oil products. In this manner, without notable expense, the treatment units can be improved with the addition of an additional treatment process.
Conclusion
This paper concerns the processes for the treatment of oil-contaminated water which is found in accidental spill clean up operations. The basis of the theoretical rational are the results of research into the dispersion phase behaviour of mixtures of oil products and water, which have been taken from the surface of a body of water in accidental spill clean up operations, and also on an analysis of the peculiarities of the processes of sedimentation and adsorption.
The process diagram for treatment which we are proposed as basic options are treatment by absorption, sedimentation, flotation and adsorption. The aim of each of the proposed operations is the removal of oil, which is present in a particular dispersion phase, from the body of water being cleaned. Furthermore, the process which is being proposed allows for the use of coagulation as a means of treating the water undergoing treatment, in order to increase the effectiveness of the sedimentation. We have also considered a scheme using inter-connected filters which provides for a more efficient use of the adsorption layer. In order to remove oil products from oil-contaminated water, where there is a considerable amount of oil present in single phase form, we have proposed a technological process using a refitted sedimentation device in order to allow the unit to include processes for treatment by absorption, which results in a cost reduction as compared to the cost of production of separate devices for these two processes.
According to the results of research which we have carried out and shown here, we can conclude that:
1. A layer of oil products which is formed during a spill, and the water which is situated above the layer is characterised by a particular structure, which can be sub-divided into separate zones. Each of these zones is in itself a dispersion system which behaves in a particular way.
2. The behaviour of a particular type of dispersion system will determine the processes for the treatment of water and oil product mixtures which have formed as the result of an accidental spill. The treatment process should include operations for the initial separation of the oil and water mixture, removal of oil from the water and preparation of the water-saturated oil for use.
3. The initial separation of oil products from water should be carried out as the oil products are being removed from the surface of the body of water.
4. Based on the dispersion phase behaviour of the water being treated, we are suggesting and providing rationalisation for a water treatment process flow chart for water containing oil products and suspension particles. The proposed process includes the following units of basic operations: a group of means of primary removal of oil products which are present in the water being treated in the single phase form, as well as of large dispersion particles of oil products and substances in suspension; means of deep cleaning to remove emulsified oil and means of treatment of the water with the aim of increasing the effectiveness of the primary cleaning.
References
- Aibulatov, N. A. (2015). Russian Activities in the Near-shore Area of the Sea and Ecological Problems. Moscow: Science. [in Russ.].
- Aliyev, N. A. (1981). Prevention of sea pollution in the development of offshore oil fields. Moscow: Nedra. [in Russ.].
- Alkhimenko, A. I. (2012). Accidental Oil Spills into the Sea, their Prevention and Control. Saint Petersburg: OM Press. [in Russ.].
- Bruselnitskii, Y. M. (1986). Marine Equipment for the Treatment of Bilge and Ballast Water to Remove Oil Products, Marine Construction. Leningrad: Sudostroenie. [in Russ.].
- Chernorutskiy, I. G. (2011). Optimization methods. Sankt-Petersburg: BKHV-Peterburg. [in Russ.].
- Fay, J. A. (1971). Physical processes in the spread of oil on a water surface. In Prevention and Control of Oil Spills: Proceedings of Joint Conference (pp. 463-467). Washington, American Petroleum Institute.
- Gmurman, V. Y. (2006). Probability theory and mathematical statistics (12th ed.). Moscow: Vyssheye obrazovaniye. [in Russ.].
- Kachala, V. V. (2007). Fundamentals of the theory of system analysis. Moscow: Goryachaya liniya-Telekom. [in Russ.].
- Karabalin, U. S., Orazbayev, B. B., & Serikov, F. T. (2009). Systems to prevent and clean up Accidents occurring in the development of Oil and Gas fields, the Ecological Safety of the Caspian Sea. Research in the Scientific Journal, MES of the RK, 3, 151-156. [in Russ].
- Kasatkin, A. G. (2016). Foundational Processes and Equipment for Chemical Engineering. Moscow: Chemistry. [in Russ.].
- Koganovskii, A. M. (1991). Adsorption Processes for Waste Water Treatment. Kiev: Technica.
- Krupnov, O. R. (2004). Models for the Monitoring of Accidental Oil Spills into the Aquatic Water Systems of the Gulf of Finland (Candidate Dissertation). Retrieved from https://www.dissercat.com/content/modeli-dlya-monitoringa-avariinykh-razlivov-nefti-na-akvatorii-vodnoi-sistemy-neva-finskii-z. [in Russ.].
- Kulskii, L. A. (1980). A Theoretical Basis for Water Treatment Processes. Kiev: Science House.
- Kulskii, L. A. (2010). A Theoretical Basis for Water Treatment Processes. Kiev: Science House.
- Kulskii, L. A., Goronovskii, N. T., Koganovskii, A. M., & Shevshenko, M. A. (1990). Reference Guide for the Properties, Analysis Methods and Treatment of Water. Kiev: Science House.
- Kurinkov, A. S. (2002). The Improvement of Systems for Ensuring the Habitability and Raising the Ecological Safety of Bodies of Water, Based on the Use of Oxidation Processes (Doctoral Dissertation). Retrieved from https://www.dissercat.com/content/sovershenstvovanie-sistem-obespecheniya-obitaemosti-i-povyshenie-ekologicheskoi-bezopasnosti. [in Russ.].
- Minin, V. V., & Krupnov, G. K. (2010). Tanker Systems for the Transportation of Hydrocarbons. Oil Gas Industry, 2, 24-26. [in Russ.].
- Nazarov, V. D. (1996). Purification of oily water (Doctoral Dissertation). Retrieved from http://library.gpntb.ru/cgi/irbis64r/gpntb/cgiirbis_64.exe?C21COM=S&I21DBN=RSK&P21DBN=RSK&S21FMT=fullw&S21ALL=(%3C.%3EA%3D%D0%9D%D0%B0%D0%B7%D0%B0%D1%80%D0%BE%D0%B2%20%D0%92.%D0%94.%3C.%3E)&Z21ID=&S21SRW=dz&S21SRD=&S21STN=1&S21REF=4&S21CNR=20. [in Russ.].
- Orazbayev, B. B., Karabalin, U. S., & Serikov, F. T. (2018). The Optimisation of Device Parameters for the Treatment of Oily Mixtures by Sedimentation. Journal of the Atyrau Institute of Oil and Gas, 16, 427-432. [in Russ.].
- Reshnyak, V. I. (1985). The Treatment and use of Oil Containing Waste Water (Doctoral Dissertation). Retrieved from https://www.dissercat.com/content/sovershenstvovanie-tekhnologii-ochistki-sudovykh-neftesoderzhashchikh-vod-sposobom-elektroag. [in Russ.].
- Reshnyak, V. I., & Zhigulskii, V. A. (2006). A Theoretical Basis for the Process of the Treatment of Oil and Water Mixtures in the Clean up of Accidental Spills. St. Petersburg: Science. [in Russ.].
- Reverberi, A. P. (2016). System Analysis of Chemical Methods in Metal Nanoparticles Synthesis. Teoreticheskie Osnovy Khimicheskoi Tekhnologii, 50(1), 59-66. [in Russ.].
- Shevchenko, M. A., & Lizunov, V. V. (1990). Water Treatment Technology. Kiev: Budivelnik.
- Standard. (2010). Construction Norms and Standards 12.04.03-85 Equipment Design for Waste Water Treatment. Moscow: Stroiizdat. [in Russ.].
- Steuer, R. E. (2015). Multiple Criteria Optimization: Theory, Computations, and Application. New York: John Wiley & Sons, Inc.
- Timofeyev, D. P. (1982). Adsorption Kinetics. Moscow: Academy of Sciences of the USSR Press. [in Russ.].
- Tuv, I. A., & Lahov, A. V. (2018). The Treatment at Depots of Water which Contains Oil. River Transport, 3, 37-39.
- Zhigulskii, V. A. (2009). Geological Technology for the Treatment of Oily Mixtures in the Clean up of Accidental Spills (Candidate Dissertation). Retrieved from https://www.dissercat.com/content/tekhnicheskie-metody-i-sredstva-bezopasnoi-utilizatsii-neftevodyanykh-otkhodov-pri-likvidats. [in Russ.].
- Zhukov, A. I., Mongait, I. L., & Rodziller, I. D. (2007). Methods for the Treatment of Industrial Water Sources. Moscow: Stroizdat. [in Russ.].
Copyright information
This work is licensed under a Creative Commons Attribution-NonCommercial-NoDerivatives 4.0 International License.
About this article
Publication Date
31 December 2019
Article Doi
eBook ISBN
978-1-80296-076-1
Publisher
Future Academy
Volume
77
Print ISBN (optional)
-
Edition Number
1st Edition
Pages
1-1056
Subjects
Industry, industrial studies, project management, sustainability, business, innovation
Cite this article as:
Saitova, R., Abisheva, A., Orazbayeva, K., Santeyeva*, S., & Orazbayev, B. (2019). Geoecological Technologies For Water Purification From Oil Mixture. In I. O. Petrovna (Ed.), Project Management in the Regions of Russia, vol 77. European Proceedings of Social and Behavioural Sciences (pp. 182-193). Future Academy. https://doi.org/10.15405/epsbs.2019.12.05.22