Collaborative Mitigation Strategies And Supply Chain Risk Management: Information Processing Theory Perspective
Abstract
Although recently there has been great interest in supply chain risk management (SCRM), little is known about in the field of risk management why some supply chains perform well, whereas others do not. For this reason, this study focuses on variables that can improve SCRM performance. Collaborative risk mitigation strategies, namely, risk information sharing, decision synchronization, goal congruence, resource sharing, and collaborative communication have been rarely theoretically analyzed in relation to SCRM performance by considering the moderating effect on relational risk in the field of SCRM literature. Therefore, to enhance information processing theory (IPT), the purpose of this study is to investigate the effect of collaborative risk mitigation strategies on SCRM performance with considering the effect of relational risk. This study develops a conceptual model encapsulating interrelationships between collaborative risk mitigation strategies and SCRM. By using IPT, this paper investigates how collaborative risk mitigation strategies can influence SCRM performance by considering the moderator effect of relational risk. Findings of this study propose that (1) collaborative risk mitigation strategies are positively related to SCRM performance (2) relational risk moderates the relationships between collaborative risk mitigation strategies and SCRM performance. This paper renders contribution to SCRM literature by presenting a model of interrelationships among collaborative risk mitigation strategies and SCRM performance.
Keywords: Supply chain risk managementmitigation strategyrelational riskinformation processing theory
Introduction
Recently, there has been a rapid increase in unpredictable and unexpected disruptions that escalate uncertainties and risks of supply chain because of the globalization of the market, uncertainties in supply and demand the increased use of logistics partners concluding in obscure international relationships (Christopher & Lee, 2004). Due to the increased risks, management of supply chain risk is emerging as a fundamental difficultness to supply chain management. Therefore, SCRM is an area of ascending significance and is purposed at improving approaches to the identification, evaluation, analysis, and mitigation of risk in supply chain (Trkman & McCormack, 2009).
To respond the dynamic market needs and deal with supply chain risks, firms need to collaborate with supply chain partners outside their organizations (Cao & Zhang, 2011). Collaboration in supply chain means that multiple organization working together for planning and executing supply chain operations with the aim of eliminating redundant functions, increasing responsiveness, reducing transaction costs (Simatupang & Sridharan, 2005). Furthermore, it provides an opportunity for the development of synergies between members, motivates real-time informationinterchange, and facilitates joint planning against disruptions (Scholten & Schilder, 2015). In substance, supply chain collaboration could provide advantages to all members by decreasing uncertainty and risk and enhancing efficiency and productivity and (Cao & Zhang, 2011).
Collaboration among supply chain members seems to carry great opportunity, yet more research is needed to comprehend its value (Cao & Zhang, 2011), especially in the context of SCRM. Nevertheless, while most studies have discussed or investigated the impact of collaboration on supply chain performance (Ryu, So, & Koo, 2009) or manufacturing performance (Vachon & Klassen, 2008), little is known about the effect of collaborative risk mitigation strategies on SCRM. In this study, we based on the information processing perspective to examine how collaborative risk mitigation strategies affect SCRM performance. The aim of this conceptual paper is to emphasize the importance of collaborative risk mitigation strategies on SCRM performance. It propounds logical arguments and proposes new relationships among constructs rather than testing them empirically.
The overall structure of this paper is organized around four sections. Following the introduction, theoretical background is provided in section
Literature Review and Theoretical Background
Supply chain risk management
Lean production practices, enhancing outsourcing, short-term product life cycles, ascending competition, changes in technology, natural disasters, and terrorism have made the supply chains more vulnerable to risks. Because such unexpected incidents impact not only a company alone but the whole supply chain as well. For example, the fire that broke out at the Philips plant in 2000 in New Mexico, disrupted both Nokia’s and Ericsson's supply chains. (Kauppi, Longoni, Caniato, & Kuula, 2016). Yet, with the understanding of the impact of such events, risk management throughout the supply chain has become an important topic for business enterprises. In general, a supply chain risk can be defined as the possibility of a negative and unexpected event that could directly or indirectly lead to a disruption of a supply chain. SCRM is a combination of strategies, policies, and methods to identify, assess, and manage supply chain risks (Jüttner, 2005). Thus, SCRM is the intersection of SCM and risk management. The purpose of SCRM is to perceive the risks and their impacts, to take preventive actions, and to determine the plans to be implemented when risky events occur (Fan, Li, Sun, & Cheng, 2017). The literature on SCRM demonstrate that SCRM process generally consists of three basic processes. These stages include risk identification, risk evaluation, and risk mitigation (Fan et al., 2017; Kern, Moser, Hartmann, & Moder, 2012). The risk identification phase is described as the process to determine the risks that may directly or indirectly affect the supply chain and the sources of these risks (Giannakis & Louis, 2011). The aim of risk identification phase is to discover all relevant risks (Kern et al., 2012). The probability and effects of all identified potential risks are analyzed in the risk assessment phase (Giannakis & Louis, 2011). Risk assessment phase can be defined as an evaluation of the probability of occurrence and an estimation of the possible impact in risky events (Kern et al., 2012). Finally, the risk mitigation phase consists of the impact of the risks that bring about negative consequences for the enterprises and the reduction of the probability of occurrence. In order for all these sub-dimensions to operate effectively, enterprises should have sufficient information processing capabilities (Fan et al., 2017).
Supply chain risk mitigation
Supply chain risk mitigation strategies describe to firm actions purposed at decreasing the probability of formation and unfavourable effects of risks. Up to the present, researchers have recommended various strategies for mitigating supply chain risk such as encouraging collaboration among supply chain partners Jüttner, Peck, & Christopher, 2003), increasing supply chain flexibility (Chang, Ellinger, & Blackhurst, 2015). Table
The prevalently known risk mitigation strategies classification in the literature is the categorization of (Jüttner et al., 2003). Jüttner and his colleague’s (2003) distinguish risk mitigation strategies which associated with supply chain context from general risk mitigation strategies as a four categories: (1) avoidance, (2) control, (3) cooperation, and (4) flexibility. The first strategy, namely avoidance refers to abandon specific products/geographical markets/supplier and/or customer organizations when face severity risks which firm cannot deal with. Jüttner et al., (2003) highlight that the second strategy called as control were mostly widespread strategy amongst the organizations interviewed in the research. Vertical integration and increased stockpiling are examples of the control strategy. The third strategy, namely cooperation refers to share risk-related information and prepare supply chain continuity plans with supply chain partners. Cooperation can be evaluated synonymous with collaboration. Lastly, multiple sourcing, postponement, and localized sourcing are an example of flexibility strategies (Jüttner et al., 2003). The aim of the flexibility strategies is to respond unexpected events and disruptions.
The other prevalently known classification of risk mitigation strategies is that: reactive and proactive mitigation strategies. In a reactive strategy, there is no action which taken before the generation of a risky incident but it is performed to mitigate the effect and/or possibility after it occurs. In these types of strategies, there is no scenario to diminish the risk probability. Nevertheless, there are plans to decrease the effect, they are performed after the occurrence of the risky incident. In a proactive strategy, plans/ scenario are performed in order to mitigate the risks before they occur. (Kırılmaz & Erol, 2017). For each relevant risk, an appropriate mitigation strategy requires to be developed and performed in order to cope with these risks (Kern et al., 2012).
Informatıon processing theory
Based on the theory of organization regarding its origin, the information processing theory has recently been investigated frequently in the areas of supply chain management, procurement, and production. Information processing theory considers enterprises as information processing systems (Galbraith, 1973). According to this theory, enterprises are constantly faced with information on uncertainty and equivocality (DuHadway, Carnovale, & Hazen, 2017). This theory argues that enterprises need to increase their information processing capabilities for combating such uncertainties. Information processing capacity can be conceptualized as collecting, processing and distributing information (Fan et al., 2017). IPT generally includes a three-stage approach: 1) The need for information processing enhances as the uncertainty faced by firm increases. 2) Firms need to be capable of processing sufficient information to process large amounts of information effectively. 3) The information processing requirements of a company and its information processing capability must be compatible with each other (Fan, Cheng, Li, & Lee, 2016). According to this theory, a risk will arise respectively, if there is a difference between the need for information processing and the capability of information processing (Galbraith, 1973). If one’s balance deteriorates, the degree of risk will increase as well. As a result, the information processing theory can offer a suitable lens for researches the supply chain disruption/risks that are difficult to predict in advance. Some studies in this area have also used the information processing perspective to identify strategies to combat supply-chain disruptions (e.g. Bode & Macdonald, 2016).
The fundamental issue of risk management is the unpredictability of the environment and the deficiency of trustworthy information needed to make planning. From the perspective of information processing, two types of strategies can be developed for such problems: the first one is a reactive strategy, which aims to reduce the need for information. The companies that implement this strategy tend to apply risk management practices that will reduce the information processing requirements. In short, such enterprises have been implementing strategies called buffering. These buffering strategies consist of increasing the stock level or applying to multiple/backup suppliers (Newman, Hanna, & Maffei, 1993). However, in fact, such practices are costly and may not be sufficient to effectively respond to the relevant risks (Srinivasan & Swink, 2018).
The second strategy, namely the proactive strategy, aims for increasing information processing capacity by investing in information sharing. In this strategy, enterprises aim to increase the information processing capability of the organization both inside and outside (such as customers and suppliers) the boundaries of the organization (Kauppi et al., 2016). In other words, companies that desire to improve their information processing capabilities should invest in both internal integration and external integration. Hence, thanks to the current and valuable information, which has been established with these relationships, businesses can quickly and effectively implement new plans by processing information efficiently and wisely (Srinivasan & Swink, 2018).
As a result, businesses will need information processing capabilities when tackling uncertain and risk-involved facilities. A more proactive approach to risk management has already been observed in recent studies.
Conceptual model development
Collaborative risk mitigation strategies
Collaborative risk mitigation strategies are a fundamental ingredient of collaborative risk management activities. Collaborative risk management can be defined as an interactive procedure on the basis of reciprocal commitment among organizations with a mutual goal for combining effort and mitigate supply chain risks and uncertainties via sharing of resources and co-development of strategic relational capabilities (Friday, Ryan, Sridharan, & Collins, 2018). Such collaborative activities of organizations render efficient access to the required information, faster response times than the competitors, and more susceptibility towards the needs and desires of the customers (Sezen, 2008). Although collaborative activities among supply chain members are the core notion of SCRM, the literature on SCRM lacks empirical comprehensions beyond the single organization perspective (Scholten & Schilder, 2015). Especially, collaborative risk mitigation strategies have great importance for dealing with supply chain risk and it can be rooted in a paradigm of collaborative advantage. Collaborative paradigm asserts that a supply chain is comprised of a sequence of interconnected relationships improved via strategic collaboration and alliances (Cao & Zhang, 2011). Synthesizing the literature, this study defines collaborative risk mitigation strategies as five interconnecting components: risk information sharing, goal congruence, decision synchronization, resource sharing, and collaborative communication. These five dimensions are expected to add value to SCRM performance by reducing risks, leveraging resources, and improving resilience.
Risk information sharing and SCRM
Every supply chain member needs quality information to deal with the uncertainties and risks in a business environment and enhance their decision-making process. These uncertainties and risks augment decision complexity and in pursuit of effect the need for information related to risks (Song, Yu, Ganguly, & Turson, 2016). Therefore, sharing risk information in the supply chain is gaining great importance among supply chain members. Information sharing in a supply chain can be defined as the extent to which crucial information is communicated to one’s trading members and a willingness to make tactical and strategic data available to other partners. With the help of information sharing, each partner receives accurate, undistorted, up-to-date information that is beneficial for making timely production, inventory, and logistics management decisions (Huong Tran, Childerhouse, & Deakins, 2016). Unfavourably, a lack of information-sharing is often emphasized as a common entail of uncertainty in supply chain planning (Jonsson & Gustavsson, 2008). In this study, risk information sharing implies the process that supply chain members share proprietary and critical information related to SCRM (Fan et al., 2017). Extant literature has highlighted the crucial role of information sharing in the SCRM process (Fan et al., 2017; Christopher & Lee, 2004). Moreover, according to several authors, information sharing is critical for augmenting the performance of supply chain (Kembro & Selviaridis, 2015; Hult, Ketchen, & Slater, 2004). The empirical studies of supply chain management also have shown that there is a positive and direct relationship between information sharing and supply chain performance (e.g. Sezen, 2008). Furthermore, in the field of SCRM, some empirical studies have found that risk information sharing effect on operational performance (Fan et al., 2016) and financial performance (Li, Fan, Lee, & Cheng, 2015). Therefore, in line with SCRM perspective and literature, we posit the following proposition:
P1. Risk information sharing in supply chain has a positive effect on SCRM performance.
Goal Congruence and SCRM
In the researches, congruence is also mentioned as fit, compatibility, or similarity. Previous studies alleged that there should be a fit among the organizational ingredients of business, people, official and unofficial organization, and resources for gaining internal effectiveness within a firm (Angeles & Nath, 2001). Goal congruence among supply chain members is the extent to which supply chain members comprehend their own aims are satisfied by achieving the supply chain aims. It is the degree of purpose agreement between supply chain members (Cao & Zhang, 2011). Ding, Dong, Liang, and Zhu (2017) stated that their research findings support that cost efficiency is high in firms which provide goal-congruent. They assert that when the purposes of various production departments can be well aligned with organizational plans, firms will realize its purpose more effectively and perform better. Yamoah (2014) state that goal congruence is very crucial for attaining a firm's strategic purpose and provide the collaboration and motivation of all supply chain partners concerned. This means that if goal incongruence is not ceased in time, it may promote supply chain partners to pursue individual aims at the expense of the supply chain' goals. In this study, we conjecture that having common goals related to deal with supply chain risk among supply chain members impact on SCRM performance, and posit the following hypothesis:
P2: Goal congruence in supply chain has a positive effect on SCRM performance.
Decision Synchronization and SCRM
Decision synchronization is referred to as participatory, collective, or joint decision making on risk management (Friday et al., 2018). The significance of decision synchronization lies in the fact that supply chain partners have different decision rights and specialty on supply chain operations. For instance, a retailer may have the decision right to designate order amount yet not the order delivery. For taking certain decisions, virtual discussion forums and face-to-face meetings are examples of ways to perform decision synchronization (Simatupang & Sridharan, 2005). We may assume that decision synchronization is related positively to SCRM.
P3: Decision synchronization in supply chain has a positive effect on SCRM performance.
Resource sharing and SCRM
When supply chain members collaborate each other, they open their assets resources to their partners (Ryu et al., 2009). Cao and Zhang (2011) define resource sharing as a process of leveraging capabilities and properties and funding in capabilities and properties with supply chain members. Resources comprise of physical resources, such as facility, technology, and manufacturing equipment. Maghsoudi and Pazirandeh (2016) provide empirical evidence that in humanitarian supply chains, resource sharing has a positive impact on organizational performance. In this study, resource sharing refers to the jointly using of resources by supply chain members to deal with risk. Since SCRM is a holistic activity, integrated use of resources by partners for this purpose will affect the performance of the SCRM. Therefore:
P4: Resource sharing in supply chain has a positive effect on SCRM performance.
Collaborative Communication and SCRM
Collaborative communication is crucial due to the fact that it signals the partner firms’ present plan and future intentions (Sambasivan, Siew-Phaik, Abidin Mohamed, & Choy Leong, 2011). According to Mohr, Fisher and Nevin (1996), collaborative communication may have a differential effect on outcomes under different governance mechanism. It may be concluded that collaborative communication does not produce the same results under all conditions. For example, Jonsson and Gustavsson (2008) emphasized that communication processes, qualified by high frequency and high level of contact among the members as one of the most significant supply chain management themes. Sambasivan et al. (2011) state that communication among supply chain partners have great importance to strategic alliance performance because it provides the partners’ competencies for behaving independently in sustaining the relationship over time.
Based on the above arguments, we posit:
P5: Collaborative communication in supply chain has a positive effect on SCRM performance.
The effect of relational risk
Liu, Li, Tao, and Wang (2008) describe relational risk as “the potential for one party's loss arising from its partner's cheating, stealing information or key employees, shirking or not fulfilling commitment and tasks, etc.” Relational risk can be classified as two types: risks related to collaboration and risks related to the partner’s behaviour (Jia & Rutherford, 2010). Namely, the relational risk is the likelihood and consequence of not having satisfactory collaboration or as the likelihood and consequence of opportunistic behaviour by the members (Delerue, 2005). Especially, to be successful in a supply chain, collaborative activities and behaviour need to be improved for managing relational risk among partners. Furthermore, risk management in the supply chain is important strategies for conserving good relationships among supply chain members and decreasing the possibility of relational risk (Cheng & Chen, 2016). The earth of an inter-organizational relationship hinges on the kind of collaboration involved: from ordinary purchase and sales interaction to close collaborative product development. Therefore, while organizations develop inter-organizational relationship, they confront multiple relational risks which might reflect any kind of unexpected negative outcomes from a cooperative relationship (Liu et al., 2008). Although previous literature has emphasized investigation into the positive and negative antecedents of relational risk (e.g. Liu et al., 2008; Cheng & Chen, 2016), there has been seldom investigation any possible or negative consequences of relational risk, such as the impact on SCRM performance. We propose that relational risk moderates the collaborative risk mitigation strategies-SCRM performance link, which empirically we know little about so far. Based on the above arguments, we posit the following hypothesis:
P6: Relational risk moderates the relationship between collaborative risk mitigation strategies and SCRM performance.
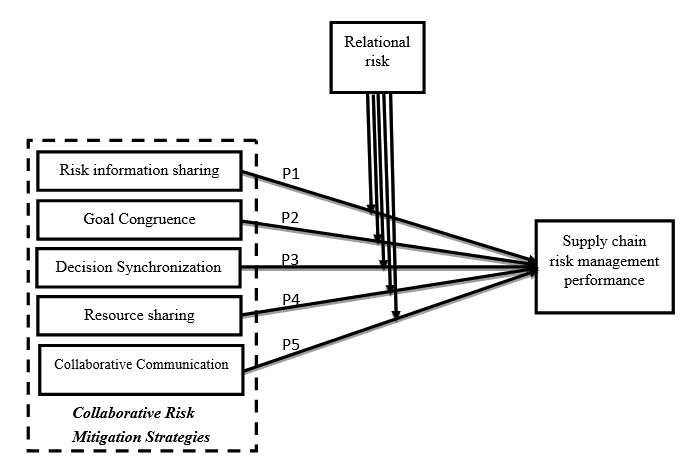
Concluding Remarks
The study contributes to our knowledge on SCRM by providing theoretical insight and conceptual model. By highlighting the role of relational risk, collaborative risk mitigation strategies in influencing SCRM performance, this study provides a framework for researchers and practitioners to visualize and understand the relationship between collaborative risk mitigation strategies and SCRM performance, thus enhancing IPT researches in the context of SCRM field. Specifically, this study makes two contributions to the SCRM literature.
Firstly, this study theoretically showed the effects of five collaborative risk mitigation strategies (encompassing risk information sharing, goal congruence, decision synchronization, resource sharing, and collaborative communication) on SCRM performance, underpinned by the information processing theory (IPT) in SCRM context. Previous research on IPT focuses on SCRM process (Fan et al., 2017), but seldom on the SCRM performance. This conceptual paper endeavours to fulfil this gap by developing a model. From a managerial perspective, our propositions provide an aggregated insight on SCRM performance to guide decision making on relevant supply chain members relational practices that enhance SCRM.
Secondly, while previous studies argued that resource sharing, in general, and information sharing in particular, has been addressed as a key factor for effective coordination (Maghsoudi & Pazirandeh, 2016). This study highlights the existing relationships of five important collaboration risk mitigation strategies and SCRM performance through a holistic view. In this context, our study provides research on collaborative strategies and SCRM performance a more extensive view.
Furthermore, this study stimulates the opportunity for future research. First, since SCRM literature misses the empirical investigation of the relationship between collaborative risk mitigation strategies and SCRM performance, in particular, the proposed theoretical model assures an empirical investigation. Second, in this study, the presented model does not comprise the mediators which might positively effect on the relationships between collaborative risk mitigation strategies and SCRM performance such as trust and risk management culture, and thus future researches may be extended to include these possible mediating effects. Three, future researches may encapsulate alternative antecedents and consequences to the model. The interrelationships between collaborative risk mitigation strategies should be empirically tested to achieve a developing a richer framework for the research. Further, future researches should focus on different risk mitigation strategies, or compare different mediating and moderating effects of variables. Finally, this research mainly analyses the impact of collaborative risk mitigation strategies on SCRM performance. Other mitigation strategies, may be called as “structural risk mitigation strategies”, such as supply chain resilience, supply chain responsiveness or supply chain agility should be part of future researches.
References
- Angeles, R., & Nath, R. (2001). Partner congruence in electronic data interchange (EDI enabled relationships. Journal of Business Logistics, 22(2), 109-127.
- Behzadi, G., O’Sullivan, M. J., Olsen, T. L., & Zhang, A. (2017). Agribusiness supply chain risk management: A review of quantitative decision models, Omega, 79, 21-42.
- Bode, C., & Macdonald, J. R. (2016). Stages of Supply Chain Disruption Response: Direct, Constraining, and Mediating Factors for Impact Mitigation. Decision Sciences, 48 (5), 836-874.
- Braunscheidel, M. J., & Suresh, N. C. (2009). The organizational antecedents of a firm’s supply chain agility for risk mitigation and response. Journal of operations Management, 27(2), 119-140.
- Cao, M., & Zhang, Q. (2011). Supply chain collaboration: Impact on collaborative advantage and firm performance. Journal of operations management, 29(3), 163-180.
- Chang, W., Ellinger, A. E., & Blackhurst, J. (2015). A contextual approach to supply chain risk mitigation. International Journal of Logistics Management, 26(3), 642-656.
- Cheng, J. H., & Chen, M. C. (2016). Influence of institutional and moral orientations on relational risk management in supply chains. Journal of Purchasing and Supply Management, 22(2), 110-119.
- Christopher, M., & Lee, H. (2004). Mitigating supply chain risk through improved confidence. International journal of physical distribution & logistics management, 34(5), 388-396.
- Delerue, H. (2005). Relational risk perception and alliance management in French biotechnology SMEs. European Business Review, 17(6), 532-546.
- Ding, J., Dong, W., Liang, L., & Zhu, J. (2017). Goal congruence analysis in multi-Division Organizations with shared resources based on data envelopment analysis. European Journal of Operational Research, 263(3), 961-973.
- DuHadway, S., Carnovale, S., & Hazen, B. (2017). Understanding risk management for intentional supply chain disruptions: risk detection, risk mitigation, and risk recovery", Annals of Operations Research, 1-20.
- Fan, H., Cheng, T. C. E., Li, G., & Lee, P. K. (2016). The effectiveness of supply chain risk information processing capability: An information processing perspective. IEEE transactions on Engineering management, 63(4), 414-425.
- Fan, H., Li, G., Sun, H., & Cheng, T .C. E. (2017). An information processing perspective on supply chain risk management: Antecedents, mechanism, and consequences. International Journal of Production Economics, 185, 63–75.
- Friday, D., Ryan, S., Sridharan, R., & Collins, D. (2018). Collaborative risk management: a systematic literature review. International Journal of Physical Distribution & Logistics Management, 48(3), 231-253.
- Galbraith, J. R. (1973). Designing Complex Organizations. Boston, MA: Addision-Wesley Longman Publishing.
- Giannakis, M., & Louis, M. (2011). A multi-agent based framework for supply chain risk management. Journal of Purchasing & Supply Management, 17, 23–31.
- Hult, G. T. M., Ketchen, Jr. D. J., & Slater, S. F. (2004). Information processing, knowledge development, and strategic supply chain performance. Academy of management journal, 47(2), 241-253.
- Huong Tran, T. T., Childerhouse, P., & Deakins, E. (2016). Supply chain information sharing: challenges and risk mitigation strategies. Journal of Manufacturing Technology Management, 27(8), 1102-1126.
- Jia, F., & Rutherford, C. (2010). Mitigation of supply chain relational risk caused by cultural differences between China and the West. The International Journal of Logistics Management, 21(2), 251-270.
- Jonsson, P., & Gustavsson, M. (2008). The impact of supply chain relationships and automatic data communication and registration on forecast information quality. International journal of physical distribution & logistics management, 38(4), 280-295.
- Jüttner, U. (2005). Supply chain risk management: understanding the business requirements from a practitioner perspective. The International Journal of Logistics Management, 16 (1), 120-141.
- Jüttner, U., Peck, H., & Christopher, M. (2003). Supply chain risk management: outlining an agenda for future research. International Journal of Logistics: Research and Applications, 6(4), 197-210.
- Kauppi, K., Longoni, A., Caniato, F., & Kuula, M. (2016). Managing country disruption risks and improving operational performance: risk management along integrated supply chains. International Journal Production Economics, 182, 484–495.
- Kembro, J., & Selviaridis, K. (2015). Exploring information sharing in the extended supply chain: an interdependence perspective. Supply Chain Management: An International Journal, 20(4), 455-470.
- Kern, D., Moser, R., Hartmann, E., & Moder, M. (2012). Supply risk management: model development and empirical analysis. International Journal of Physical Distribution & Logistics Management, 42(1), 60-82.
- Kırılmaz, O., & Erol, S. (2017). A proactive approach to supply chain risk management: Shifting orders among suppliers to mitigate the supply side risks. Journal of Purchasing and Supply Management, 23(1), 54-65.
- Li, G., Fan, H., Lee, P. K., & Cheng, T. C. E. (2015). Joint supply chain risk management: An agency and collaboration perspective. International Journal of Production Economics, 164, 83-94.
- Liu, Y., Li, Y., Tao, L., & Wang, Y. (2008). Relationship stability, trust and relational risk in marketing channels: Evidence from China. Industrial Marketing Management, 37(4), 432-446.
- Maghsoudi, A., & Pazirandeh, A. (2016). Visibility, resource sharing and performance in supply chain relationships: insights from humanitarian practitioners. Supply Chain Management: An International Journal, 21(1), 125-139.
- Mohr, J. J., Fisher, R. J., & Nevin, J. R. (1996). Collaborative communication in interfirm relationships: moderating effects of integration and control. Journal of Marketing, 60(3), 103-115.
- Newman, W. R., Hanna, M., & Maffei, M. J., (1993). Dealing with the uncertainties of manufacturing: flexibility, buffers and integration. International Journal Operations & Production Management, 13(1), 19–34.
- Petersen, H. L., & Lemke, F. (2015). Mitigating reputational risks in supply chains. Supply Chain Management: An International Journal, 20(5), 495-510.
- Ryu, I., So, S., & Koo, C. (2009). The role of partnership in supply chain performance. Industrial Management & Data Systems, 109(4), 496-514.
- Sambasivan, M., Siew-Phaik, L., Abidin Mohamed, Z., & Choy Leong, Y. (2011). Impact of interdependence between supply chain partners on strategic alliance outcomes: role of relational capital as a mediating construct. Management Decision, 49(4), 548-569.
- Scholten, K., & Schilder, S. (2015). The role of collaboration in supply chain resilience. Supply Chain Management: An International Journal, 20(4), 471-484.
- Sezen, B. (2008). Relative effects of design, integration and information sharing on supply chain performance. Supply Chain Management: An International Journal, 13(3), 233-240.
- Simatupang, T. M., & Sridharan, R. (2005). An integrative framework for supply chain collaboration. The International Journal of Logistics Management, 16(2), 257-274.
- Song, H., Yu, K., Ganguly, A., & Turson, R. (2016). Supply chain network, information sharing and SME credit quality. Industrial Management & Data Systems, 116(4), 740-758.
- Srinivasan, R., & Swink, M. (2018). An Investigation of Visibility and Flexibility as Complements to Supply Chain Analytics: An Organizational Information Processing Theory Perspective. Production and Operations Management, 27 (10), 1849-1867.
- Trkman, P., & McCormack, K. (2009). Supply chain risk in turbulent environments—A conceptual model for managing supply chain network risk. International Journal of Production Economics, 119(2), 247-258.
- Vachon, S., & Klassen, R. D. (2008). Environmental management and manufacturing performance: the role of collaboration in the supply chain. International Journal of Production Economics, 111(2), 299-315.
- Yamoah, E. E. (2014). Relevance of Goal Congruence and its Implications to Managers. European Journal of Business and Management, 6(12), 1997-1999.
Copyright information
This work is licensed under a Creative Commons Attribution-NonCommercial-NoDerivatives 4.0 International License.
About this article
Publication Date
30 October 2019
Article Doi
eBook ISBN
978-1-80296-070-9
Publisher
Future Academy
Volume
71
Print ISBN (optional)
-
Edition Number
1st Edition
Pages
1-460
Subjects
Business, innovation, Strategic management, Leadership, Technology, Sustainability
Cite this article as:
Sağlam*, Y. C., Sezen, B., & Çankaya, S. Y. (2019). Collaborative Mitigation Strategies And Supply Chain Risk Management: Information Processing Theory Perspective. In M. Özşahin (Ed.), Strategic Management in an International Environment: The New Challenges for International Business and Logistics in the Age of Industry 4.0, vol 71. European Proceedings of Social and Behavioural Sciences (pp. 9-19). Future Academy. https://doi.org/10.15405/epsbs.2019.10.02.2