Improvement of Indonesian Automotive Component Firms’ Operational Performance via Knowledge Management Enabler
Abstract
The development of automotive component industry in Indonesia shows the development along with the increase of motor vehicle industry. If it compared with similar industries in ASEAN countries, Indonesia is still lagging behind Thailand. In order to compete, it is necessary to be more concentrate on operational performance of automotive component firms in Indonesia. There is some factors related to operational performance, such as use of operational cost, product quality improvement, speed of delivery of product, and flexibility of production process to change. In this regard, knowledge management is required as knowledge is the most important resource for any firms. Therefore, to be able use knowledge as a primary resource, is necessary to considering the readiness of the trigger factors of knowledge or knowledge enabler. Those factors are leadership style, human capital, organizational structure, and information technology. This study use SmartPLS 3.0 to examine the importance-performance matrix analysis (IPMA) from an antecedents of the knowledge management enabler variable as an endogenous variable. A quantitative research using questions was applied to get response from randomly automotive component firms in Indonesia. As the conclusion, it is known that information technology not to important compared with human capital, leadership, and organizational structure to improving the operational performance of automotive component firms in Indonesia.
Keywords: Operational performanceknowledge management enablerimportance-performance matrix analysisautomotive component firmsIndonesia
Introduction
Indonesian automotive sales in 2017 reach 1.06 million, compare to years before. The presence of automotive component industries has an important contribution as the suppliers for the automotive manufacturers, also the aftermarkets for meeting the needs of after sales, both for domestic and international markets. The automotive component firms in Indonesia can be described as the supply chains for the products of component industries which act as the suppliers of ready-to-use or finished products to consumers (Laraswati, Astuti, Budijanto, Yuniaristanto, & Sutopo 2014). Due to the Indonesian government policies about Low Cost Green Car (LCGC), the establishment of automobile manufacturers increased since 2013. In 2017, Indonesia succeed exporting the automotive component for 81 million compare to 6.2 million components in 2016 (Sidik, 2018). Indonesian automotive component industries have to build some strong strategies in management and development of the industry. One of the strategies that have been made by Indonesian government is Decree No. 114 in 2013, that Indonesian government will provide incentives for companies, include the automotive components companies.
Problem Statement
Automotive and its component industry in Indonesia dominated by foreign ownership enterprises, especially Japanese companies. Japanese multinational enterprises have invested in Indonesia due to the advantageous automotive markets and as the implication of it, technology in Indonesia’s automotive component industry is influenced by foreign companies. Indonesia earn the advantage from the transfer of knowledge and technology, but on the other hand, Indonesia cannot be independent, since to develop, Indonesia must be responsive to technologies and market changes.
Based on ASEAN Briefing (2017), Indonesia’s dependence on foreign investment in automobile sector and lack of component manufacturing industry will hinder manufacturing ability compare to manufacturing capacity in Thailand. The current condition is that Indonesia has no choice but to follow the Japanese pattern in managing the industries, called keiretsu. Purwaningrum (2013), mentioned that keiretsu as the strong connection between automakers and suppliers. In other words, Indonesia’s automotive component products mostly based on a request from the automotive industry, which dominated by Japanese automotive company.
To be independent and able to compete with other countries, Indonesia’s automotive component products must have strong strategies in term of cost, quality, delivery, and flexibility. According to Nurcahyo and Wibowo (2015), the factors in operating strategy literature, the local companies in Indonesia should focus on the competitive priorities which able to act as the strategic capabilities to help the organizations in creating, developing, and maintaining their competitive advantages, or known as operational performance. It can be defined as the ability of company in competitive priority of operational strategy in reducing management cost, order time, lead time, improving the effectiveness of raw material use and production capacity, delivery speed, and service quality (Chavez, Gimenez, Fynes, Wiengarten, & Yu 2013; Truong et al., 2017). While Arikan and Kirci (2015) mention that there are many factors which can be described as the operational performance, but the most basic are cost, quality, flexibility, and delivery.
However, todays, local industry is not capable yet to fulfil the needs of automotive sector, because of the existing resources cannot fulfil the standard quality. Further, Indra (2017), mentioned that the lack of resources causes those problems, and the upstream industry is not maximum yet in implementing the actual localization program of energy saving vehicle and affordable price. To improve the operational performance, organizations must have good inputs. In a modern organization, knowledge is known as a valuable resource compared to human and capital resources. Based on Ing and Jian (2014), managing knowledge or Knowledge Management (KM) become the main strategy in an organization for creating new business processes to achieve a superior organizational performance. Unfortunately, the knowledge in supply chain networks of automotive component industry in Indonesia does not flow freely. This makes industrial upgrades difficult since the first tier suppliers are usually tied to the Japanese Keiretsu system (Purwaningrum, 2013).
In general, Indonesian government support the growth of the industry, unfortunately, policies are not enough without support in infrastructure, technology, and investment. Therefore, this research will focus on knowledge management enabler factors in a firm. Knowledge management (KM) Enabler defined as the organizational mechanism done consciously and consistently to develop knowledge within organization, and become the mechanism to stimulate knowledge creation, protect knowledge and facilitate knowledge shares among the individuals in an organization (Aulawi, Sudirman, Suryadi, & Govindaraju 2009; Allameh, Zare, & Davoodi, 2011; Theriou, Maditinos, & Theriou, 2011; Yeh, Lai, & Ho, 2006). Ho (2009) view KM Enabler as the critical factor which puts concept of KM into practices in order to achieve the KM effectiveness. There are some factor describing KM Enabler, Allameh et al., (2011) mentioned that knowledge enabler through technology, structure and culture has a strong effect in processing knowledge effectiveness. While Magnier-Watanabe (2011) mentioned that organizational culture, leadership, organizational control, and work style in KM Enabler. To match the KM Enabler with the crucial factors in automotive component industry in Indonesia, this research will focus on centralised organizational structure, human capital, transformational leadership, and information technology (IT).
Centralised organizational structure refers to the hierarchical levels in an organization which have the authorities to make decision. The majority of the automotive component industries in Indonesia use the hierarchical organizational structure which is the centralised decision making system. According to that, the automotive component firms in Indonesia tend to be more paternalistic (Subroto & Sumarto, 2011), then this research use the centralised organizational structure. While human capital known as an employee competence which is refers to skill, training, education, experience, and value characteristics of an organization’s workforce (Ling, 2013). Since the automakers and their clusters are the potential industry in Indonesia, it means that human capital become one of the important factors. To manage people in an organization, it will need an appropriate leadership style. Most of the automotive component industry in Indonesia is working under control of Japanese automotive industry. To fulfil the product qualification, it will need to transfer the knowledge. So, in transferring the knowledge it fit with transformational leadership. According to Muenjohn and Armstrong (2008), transformational leadership display their behaviours associate with four characteristics such as Idealized influence, Inspirational motivation, Intellectual stimulation, and Individualized consideration. Last, this research use information technology as the enabler, because as a tools information technology will increase the achievement of the firms. Through information technology it will flows the knowledge and eliminates the barriers of communication among departments in an organization (Jeng & Dunk, 2013).
Since knowledge become the most important input factor in an organization for sustaining competitive advantage, then operational performance need to considering the KM Enabler as a foundation of the organization. Through KM Enabler, managers will able to find which enabler are critical for knowledge creation within organization (Lee & Choi, 2003).
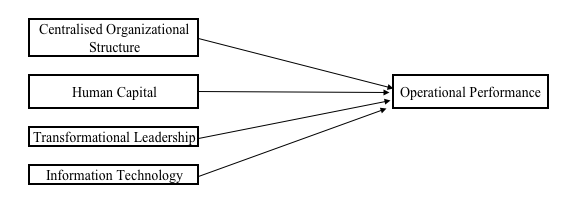
Knowledge is needed to build a good quality in automotive component industry, otherwise Indonesia will find difficulties to upgrade the industries and win the competition against other countries. As long as there are still restrictions of knowledge flows in the industries in Indonesia, it will be difficult for firms to upgrade their performance and will always depend on the Japanese technologies. The following hypotheses are thus formulated: (Figure
H1: there is no significant relationship between centralised organizational structure and operational performance.
H2: there is no significant relationship between human capital and operational performance.
H3: there is no significant relationship between transformational leadership and operational performance.
H4: there is no significant relationship between information technology and operational performance.
Research Questions
What kind of factors which has more effect to the operational performance on the automotive component Industry in Indonesia?
Purpose of the Study
To find all factors that effected to the operational performance on the automotive component industry in Indonesia.
Research Methods
As the target population for this study is automotive component industry which is located in Jakarta, Bogor, Tangerang, Karawang and Bandung area, with operational manager from each firm as the respondent. Questionnaire items were adopted and adapted from past studies and each item was measured using 5-point Likert scale. For data analysis, all the data from the questionnaire is calculated using Importance – Performance Analysis (IPMA) by SmartPLS 3.0.
Findings
Collected Data from a total 85 respondents shows that 72 respondents are male (84.7%) and 13 respondents are female (12.94%). In term of age, total of 60% are in the age range of 40 – 49 years old, 23.06% in 30 – 39 years old, and lastly 12.94% in 40 – 59 years old. Respondents Status found that most of them are married (84.70%) and the rest are still single (15.29%). Most of the respondents in this study have bachelor degree (65.88%), followed by diploma (30.58%) and senior high school (3.53%). In terms of working experience, majority of the respondents have work for 10 – 19 years (78.82%), followed by 20 – 29 years (14.12%), and 0 – 9 years (7.06%). Respondents also asked their experience working in current company, and most of them already work for 0 – 9 years (51.76%), followed by 10 – 19 years (42.35%), and 20 – 29 years (5.88%). Last, respondents asked their experience in current position as operation manager / production manager. Most of them already worked as operation manager / production manager for 0 – 4 years (52%), followed by 5 – 9 years (31%), and 10 – 15 years (18%). Data collected from a total 85 respondents show the following profile of respondents (Table
Next, the structure model was analysing through the use of the bootstrapping procedure where the path coefficients were determined. Table
Organizational structure is about how job tasks are formally divided and coordinated (Maduenyi, Oke, Fadeyi, & Ajagbe, 2015). Through centralised coordination, it assumes will make the production process easier, and at the end will improve the operational performance. In this research, the centralised organizational structure contributes the operational performance for 41.3%.
While human capital refers to the skill, training, education, experience, and value characteristics of an organization’s workforce (Ling, 2013). Through skills and all abilities from employee will improve the productivity, then improve the performance of the organization, and based on this research, human capital contribute the operational performance for 32.8%.
Transformational leadership behaviours inspire and motivate employees to commit to achieve a shared vision and transform employees into creators or innovators. Within this relationship, employees increase their performance and understand their potential due to the behaviours of leaders (Birasnav, 2014). An according to the previous study, transformational leadership affect the performance of the organization (Noruzy, Dalfard, Azhdari, Sirkouhi, & Rezazadeh, 2013). In this research, transformational leadership contribute the operational performance for 27.1%.
In this research, information technology become the only variable that not supported the operational performance, because as a tool, information technology will does not affect the operational performance directly. As a tool, Migdadi (2009) mentioned that information technology as an enabler will improve the knowledge management first then pursuit the performance (Table
To explain more about the hypotheses, this research uses the Importance – Performance Matrix Analysis (IPMA) analysis. The importance – performance matrix analysis (IPMA) extends the standard PLS-SEM results reporting of path coefficient estimates by adding a dimension to analysis that considers the average values of the latent variable scores (Hair, Hollingsworth, Randolph, & Chong 2017). (Table
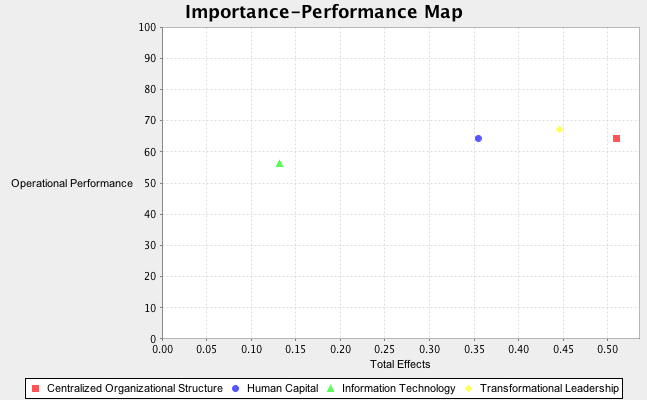
The analysis of IPMA was performed in SmartPLS and the results are illustrated in table
Conclusion
The aims of this research were to investigate the direct relationship of knowledge management enabler an operational performance of the automotive component industry in Indonesia. Specifically, the relationship between centralized organizational structure, human capital, transformational leadership, information technology and operational performance was examined. The research found that centralized organizational structure (41.3%), human capital (32.8%), and transformational leadership (27.1%) had significantly and positively relationship with operational performance, while information technology (9.4%) had no significant with operational performance.
Although, information technology is an important factor in an organization, but in this research there are other factors that more important and effected to increase the operational performance for the Indonesian automotive component industry. Those factor are centralized organizational structure, human capital, and transformational leadership. Therefore, Indonesian automotive component firms need to strengthen those factors, rather than adopting the technology from Japanese firms.
References
- Allameh, S. M., Zare, S. M., & Davoodi, S. M. R. (2011). Examining the impact of KM enablers on knowledge management processes. Procedia Computer Science, 3, 1211–1223.
- Arikan, C., & Kirci, S. (2015). Effects Of Organizational Structure At Outsourcing Companies To Operational Performance : A Practice In. International Journal of Arts & Sciences, 8(4), 263–272.
- ASEAN Briefing (2017). ASEAN Market Watch: Indonesia Automotive Market, Malaysia - India Trade, and ASEAN Manufacturing Sector. Retrieved from https://aseanbriefing.com/news/author/asean-briefing.
- Aulawi, H., Sudirman, I., Suryadi, K., & Govindaraju, R. (2009). Literature Review Towards Knowledge Enablers Which Is Assumed Significantly Influences Ks Behavior. Journal of Applied Sciences, 5, 2262–2270.
- Birasnav, M. (2014). Relationship between transformational leadership behaviors and manufacturing strategy, 22(2), 205–223.
- Chavez, R., Gimenez, C., Fynes, B., Wiengarten, F., & Yu, W. (2013). Internal Lean Practices and Operational Performance, The Contingency Perspective of Industry Clockspeed. International Journal of Operations and Production Management, 33(5), 562-588.
- Hair, J., Hollingsworth, C. L., Randolph, A. B., Chong, A. Y. L. (2017). An Updated and Expanded Assessment of PLS - SEM in Information System Research. Industrial Management and Data Systems, 117(3), 442 - 458.
- Ho, C. (2009). The relationship between knowledge management enablers and performance. Industrial Management & Data Systems, 109(1), 98–117.
- Indra, BP. (2017). Inilah Hambatan Pengembangan Industri Komponen Otomotif. Retrieved from http://www.imq21.com/news/read/420933/20170208/182253/Inilah-Hambatan-Pengembangan-Industri-Komponen-Otomotif.html
- Ing, L. W., & Jian, L .C. (2014). Knowledge Management Driven Firm Performance: The Roles Of Business Process Capabilities and Organizational Learning. Journal of Knowledge Management,18(6), 1141-1164.
- Jeng, D. J. F., & Dunk, N. (2013). Knowledge Management Enablers And Knowledge Creation In ERP System Success. International Journal of Electronic Business Management, 11(1), 49–59.
- Laraswati, L. D., Astuti, R. W., Budijanto, M., Yuniaristanto, & Sutopo, W. (2014). Effect of Vertical Restraint Strategy on Supply Chain Automotive Industry: A Case Study in Indonesia. Proceedings of the International MultiConference of Engineers and Computer Scientists, IMECS 2015, Vol. II.
- Lee, H., & Choi, B. (2003). Journal of Management Enablers , Processes , and Organizational Performance : An Integrative View and Empirical Examination. Journal of Management Information Systems, 20(1), 179–228.
- Ling, Y. H. (2013). The influence of intellectual capital on organizational performance — Knowledge management as moderator. Asia Pacific Journal Management, 30(1), 937–964.
- Maduenyi, S., Oke, A. O., Fadeyi, O., & Ajagbe, M. A. (2015). Impact of Organizational Structure on Organizational Performance. International Conference On African Development Issues (CU-ICADI, Social and Economic Models for Development Track, 354 - 358.
- Magnier-Watanabe, R. (2011). Getting ready for kaizen: organizational and knowledge management enablers. The Journal of Information and Knowledge Management Systems, 41(4), 428–448.
- Migdadi, M. (2009). Knowledge management enablers and outcomes in the small‐and‐medium sized enterprises. Industrial Management & Data Systems, 109(6), 840–858.
- Muenjohn, N., & Armstrong, A. (2008). Evaluating the Structural Validity of the Evaluating the Structural Validity of the Multifactor Leadership Questionnaire (MLQ), Capturing the Leadership Factors of Transformational-Transactional Leadership. Contemporary Management Study, 4(1), 3–14.
- Nurcahyo, R., & Wibowo, A. D. (2015). Manufacturing Capability, Manufacturing Strategy and Performance of Indonesia Automotive Component Manufacturer. Procedia CIRP (26). 653 - 657.
- Noruzy, A., Dalfard, V. M., Azhdari, B., Sirkouhi, S. N., & Rezazadeh, A. (2013). Relations Between Transformational Leadership, Organizational Learning, Knowledge Management, Organizational Innovation, and Organizational Performance: An Empirical Investigation of Manufacturing Firms. The International Journal of Advanced Manufacturing Technology, 64, 1073 - 1085.
- Purwaningrum, F. (2013). Knowledge Transfer Within an Organizational Cluster in the Jakarta Metropolitan Area. Working Paper Series 5, Institute of Asian Studies, Universiti Brunei Darussalam, Gadong 2013. Retrieved from http://ias.ubd.edu.bn/assets/Files/WORKING.PAPER.SERIES.5.pdf.
- Sidik, S. (2018). Menperin: Ekspor Komponen Otomotif Naik 13 kali Lipat di 2017. Retrieved from http://www.tribunnews.com/bisnis/2018/04/19/menperin-ekspor-komponen-otomotif-naik-13-kali-lipat-di-2017.
- Subroto, A., & Sumarto. (2011). Organizational Culture and Leadership Role for Improving Organizational Performance : Automotive Components Industry In Indonesia. International Journal of Innovation Management and Technology, 2(5), 383–389.
- Theriou, N., Maditinos, D., & Theriou, G. (2011). Knowledge management enabler factors and firm performance: An empirical study of the Greek medium and large firms. European Study Studies Journal, 14, 97–134.
- Truong, H. Q., Sameiro, M., Fernandes, A. C., Sampaio, P., Duong, B. A.T., Duong, H.H., & Vilhenac, E. (2017). Supply Chain Management Practices and Firms' Operational Performance. International Journal of Quality and Reliability Management, Vol. 34, No. 2, 176 - 193.
- Yeh, Y., Lai, S., & Ho, C. (2006). Knowledge management enablers: a case study. Industrial Management & Data Systems, 106(6), 793–810.
Copyright information
This work is licensed under a Creative Commons Attribution-NonCommercial-NoDerivatives 4.0 International License.
About this article
Publication Date
02 August 2019
Article Doi
eBook ISBN
978-1-80296-064-8
Publisher
Future Academy
Volume
65
Print ISBN (optional)
-
Edition Number
1st Edition
Pages
1-749
Subjects
Business, innovation, sustainability, environment, green business, environmental issues
Cite this article as:
Silvianita, A., & Ling, T. C. (2019). Improvement of Indonesian Automotive Component Firms’ Operational Performance via Knowledge Management Enabler. In C. Tze Haw, C. Richardson, & F. Johara (Eds.), Business Sustainability and Innovation, vol 65. European Proceedings of Social and Behavioural Sciences (pp. 594-602). Future Academy. https://doi.org/10.15405/epsbs.2019.08.60