Abstract
The largest deposits of hydrocarbons (oil, gas and condensate) are located on the shelf of the Arctic seas, characterized by difficult natural climatic conditions (ice conditions, temperature, wind and currents) that limit access to the deposit during the year. This circumstance brings up-to-date and requires research and development in the search for alternative technical means of exploration of offshore hydrocarbon deposits for existing ones (floating production platforms, tankers, etc.). Year-round exploitation and transport of hydrocarbons from the offshore may be ensured by subsea pumping complexes (SPC). The subject of research in this article is SPC electrical mechanical systems of hydrocarbons transportation from offshore deposits. The main objective is to identify operation issues of existing electrical mechanical systems of pumping complexes of the continental pipelines, make up proposals how to handle them when used as a part of SPC to ensure high reliability and develop prospective structures and components of SPC electrical mechanical systems. Also, the article considers existing SPCs and projects where they are used to explore offshore hydrocarbon deposits.
Keywords: Offshoresubsea pumping complexelectrical drivemultilevel inverter distributed structuresubmarine high-voltage direct current line
Introduction
Times The most promising hydrocarbon deposits (oil, gas and condensate) are located on the continental shelf of the Arctic seas. The main complicating aspects of their development refer extreme natural climatic conditions and difficult ice conditions. These factors limit access of traditional technical facilities to the offshore deposits throughout the year. Year-round operation of hydrocarbon deposits of the Arctic seas requires special floating technical means (platforms, tankers and gas carriers) of ice class.
Thus, in 2014 OJSC “OC Rosneft” Company started exploration of hydrocarbon reserves on the offshore of the Kara Sea. Drilling was carried out in a relatively ice-free season during one month and a half. During this period one exploration well “Universitetskaya-1” was drilled. Further drilling, exploration and evaluation of the stock of this deposit will be performed in 2015 (Tolstov, & Mirzoyev, 2011; Durymanov, & Leontyev, 2010; Vasilev, & Mardashov, 2016; Menshov, & Ershov, 2000).
Upon completion of drilling works and creation of a system of exploration wells, the tasks of ensuring safety and efficiency of hydrocarbons collection and transportation become more important. In difficult ice conditions of the Arctic seas the most effective means of subsea offshore development are as follows: subsea pipelines (SP); subsea hydrocarbons collection and preparation complexes (SHCPC); subsea separators (SS); subsea pumping complexes (SPC) (Paula et al., 2015; Vedachalama et al., 2015; Parks, & Aminb, 2012; Hua, Falcone et al., 2012).
World oil and gas companies, including Russian, have vast experience in construction and operation of mainline and industrial SP. Industrial SP in the Russian Federation are used during offshore exploration of the Sakhalin Island. They are used to ensure underwater collection of hydrocarbons from several wells. Mainline SP network is based in the North Sea between Norway, United Kingdom and countries of continental Europe. One of the largest mainline SP “Nord Stream” connects the city of Vyborg and Greifswald and is used to transport Russian natural gas to Germany bypassing transit countries.
Methods
Currently, SHCPCs main element of which is manifold, are used to collect hydrocarbons in the sea bottom. The manifold is a “static” structure on the sea bottom (without any rotating parts), which combines several production wells with the help of industrial SP. Collected hydrocarbons with water and sand impurities, under exposure of reservoir pressure, flow into mainline SP or on production platform or transport vessel, where additional technological processes and further transportation are performed. In the Russian Federation manifolds are used in the field “Sakhalin-2” in the Sea of Okhotsk of the offshore of the Sakhalin Island in the sub-arctic conditions.
In extreme natural climatic conditions of the Arctic seas use of conventional cargo ships is extremely dangerous or impossible, and construction and operation of special cargo ice-class vessels require great financial and time costs. In these circumstances, it is preferable to use SPCs based on regulated electrical drives for subsea transportation of hydrocarbons (Parks, & Pack, 2013, Li, Gong et al., 2013).
Use of SPC will ensure: resource and energy efficiency on account of saving energy resources of floating technical facilities; technological efficiency on account of hydrocarbons transportation without use of any floating technical facilities; economic efficiency on account of reduced costs for production and exploitation of oil and gas ice-class fleet; environmental performance, which will reduce impact on the fragile ecosystem of seas in the Arctic Ocean.
Results
The structure of the subsea pumping complex. Issues and technical requirements for unit
SPC is built by mechanical principle, i.e. integration of various components in a single casing. SPC integrates a combination of technical controls (semi-conductor and microprocessor), electrical mechanical conversion (driven motor) and transportation (multiphase pumps) in a single sealed casing. The main function of SPC is to transport hydrocarbons and different impurities, if any. SPC structure is shown in Fig.
The main elements of SPC comprise adjustable driven electrical motor (3), one or several multiphase pump (10) integrated into a single sealed casing (2) and insulated from each other with a seal (4, 5). Electrical motor and multiphase pumps have a common shaft (8) with supports on magnetic bearings (6, 7 and 11). Also, complex casing integrates technical facilities of regulation, control, communication and SPC status control (1). Transported hydrocarbon stream is fed and discharged from SPC via nozzles (9).
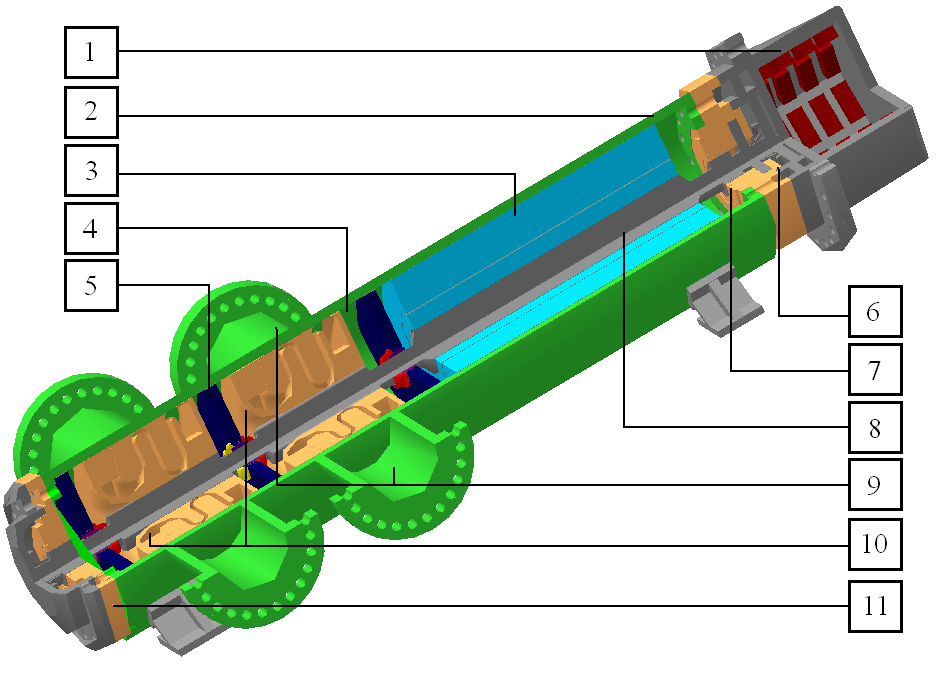
The main scientific and technical issue at establishment of an SPC is to en-sure high reliability of operation of all its elements, which will ensure smooth and safe transportation of hydrocarbons produced on the offshore. Here tasks of development of electrical and electrical mechanical equipment of SPC, as well as power supply, management and status control systems become the most important.
To create the most reliable and effective SPCs one should take into account all the experience of operation of high-voltage electrical driven pumping units at the facilities of the main pipelines on land, conditions of occurrence of causes and nature of damage of the major equipment, leading to malfunction and failure of the units. Table
Analysis of failure conditions shows that the largest part of electrical motor damage occurs during operation in static mode at operating supply voltage. This is caused by electrical aging of stator winding insulation, which occurs most in-tensely under exposure of higher harmonic components of supply current. An-other significant cause of damage is over-voltage of the stator winding.
Damage of high-voltage electrical drive stator insulation with high currents in dynamic modes is the biggest issue. During start-up of the unit the value of stator current exceeds rated value for 5-7 times. Duration of the start-up process leads to insulation overheating and accelerates its electrical aging and may cause thermal damage, which is also the main cause of electrical motor failure.
Reasons related to mechanical damages, occur due to impact loads, which may result in damage to bearing units of the assembly and increased vibration, which in its turn causes fluctuation of electromagnetic torque and occurrence of higher harmonic components of supply current.
To ensure high reliability and SPC operational and technical characteristics the following solutions may be used:
1. Use non-contact high-voltage asynchronous motor with squirrel-cage rotor (AMSC) or synchronous motor with permanent magnets (SMPM) as a driving motor of multiphase pumps of SPC. High reliability, ease of operation and guaranteed operation modes are the main advantages of this type of motor.
2. Use high-speed high-frequency AMSC in SPC that will allow improving weight and overall dimensions of driven machines and reducing area of the bot-tom plate, on which SPC is installed.
3. Use common shaft of the motor and pump in SPC, which enable eliminating reduction gear from the drive structure.
4. Use multiphase pumps (MPP), ensuring transportation of hydrocarbon impurities in the form of solid particles without special underwater preparation (or with minimal training).
5. Install several multiphase pumps driven by a single motor in SPC casing, which will ensure hydrocarbons transportation via several circuits of industrial SP without extra electrical technical equipment.
6. Use active magnetic bearings (AMB), which ensure SPC shaft rotation without rolling or plain bearings.
7. A set of active magnetic bearings will enable creating SPC without oil supply system.
8. Use multi-level semiconductor frequency converter (FC) of distributed (decentralized) structure with an active rectifier that will ensure electrical drive operation with power factor close to one unit to control electrical drive of SPC.
9. Use high-voltage DC power supply line (HVDC), which will significantly reduce losses on the line ensure high level of electromagnetic compatibility.
10. Use multi-structure automatic control system (ACS) on the basis of vector algorithms. This will ensure high accuracy of control.
11. Provide SPC with systems of monitoring, diagnosis and assessment of residual life of electrical equipment with regard to current status in real time mode, which will ensure fault monitoring and proactive safety measures. Table
Electrical mechanical system of SPC. Ensuring compatibility of electrical technical equipment of SPC
Reliability and efficiency of SPC, compatibility of electrical technical equipment and its power characteristics are mainly determined by the structure and composition of SPC electrical mechanical system. For that purpose you need to optimize complex structure and reduce the number of electrical elements of SPC, which are unattended in a submerged position and bring them on the surface. Flow diagram of the electrical mechanical system of perspective SPCs is shown in Fig.
The main features of the above structure of SPC electrical mechanical sys-tem refer to FC distributed structure and use of HVDC for electricity supply to underwater part of SPC. The reason for such a topology is as follows. During installation of FC switches (autonomous inverter (AI) and active rectifier (AR) on the on-shore power station, there is a well-known problem of “long cable”. This problem may be solved by installing additional filters close to driven electrical motor, i.e. in submerged position. FC of such a structure may not be used in SPC due to reduced reliability of the complex and increased overall dimensions. Installation of both FC switches submerged will lead to further reduction of the com-plex reliability and increased overall dimensions compared to the first option.
High requirements on ensuring compatibility in terms of its electromagnetic (FC compatibility with the network), electrical mechanical (FC compatibility with AMSC network) and power (ensuring brake modes of the electrical motor with energy recovery to the network) aspects are stipulated for the structure and algorithmic support of distributed FC switches of SPC.
At higher power of MPP, used AMSC should have appropriate capacity. As a rule, high-power electrical motors are made high-voltage to reduce currents and power losses. To ensure control over high-voltage electrical motor of SPC of higher power it is expedient to use a three-level AI, which ensures high reliability and electrical mechanical compatibility of FC with electric driven motor. Low distortion of AI sinusoidal output current (AMSC current stator) ensures low value of rotation frequency fluctuations and electrical magnetic torque, and reduces impact of non-sinusoidal currents on speed of electrical aging of electrical motor winding insulation and reduces its service life.
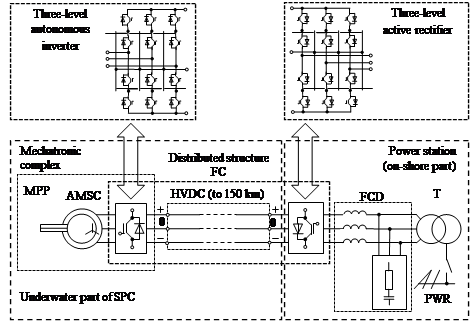
The major issue of SPC electrical mechanical system is ensuring brake modes of electrical driven motor. Using brake keys and resistances (choppers), which should be installed at AI input, due to their effect on SPC reliability, is impossible, but discharge of “brake” electrical energy should be ensure. Otherwise, it will lead to motor and AI overheating, which may lead to its failure. To solve this issue and ensure electrical compatibility of equipment of SPC electrical mechanical system, it is recommended to use three-level AR.
Use of AR will ensure electricity recovery to power supply network in the brake modes of SPC driven motor. Another significant effect from AR use in terms of SPC power supply is to keep a constant voltage level in underwater high-voltage direct current line, even at short-term interruptions in supply network. Use of AR will also ensure maintenance of power ratio of SPC asynchronous electric drive at level of one unit and sinusoidal shape of current consumed by electrical drive.
Conclusion
Norwegian companies FMC Technologies, Aker Solutions and GE Vetco (General Electric) are world leaders in designing and manufacturing of subsea technical facilities for various purposes, for offshore hydrocarbon deposits. Moreover, developments of subsea equipment and technology are performed by Siemens and MAN companies. The leader of the use of subsea technologies is a Norwegian oil and company Statoil, and in the Russian Federation these are OJSC “Gazprom” and OC “Rosneft”.
Today, in some fields of the Arctic seas SPCs are used for year-round operation of the deposits, regardless of ice conditions. For example, on the Asgard field SPCs have been used since 2013 (Fig.
At deposit Ormen Lange, located in the Barents Sea and settled in 2007, at the first stage of its development, while drilling of exploration wells each well mouth was provided with a bottom plate with drilling windows, and after injection of wells it was provided with SHCPC. In 2017 SPC has to be installed at the deposit. Statoil Company uses SPC to prepare recovered hydrocarbons for further transportation at Tordis deposit, located in the North Sea.
The first SPC with driven motor of 850 kW in power was created by GE Vetco Company, which was tested in 1992 at factory. Today development of these systems is ensured by leading electrical technical company. SPC MAN Hofim-type was tested in Norway, and in 2009 Siemens performed test of SPC ECO-II (Fig.
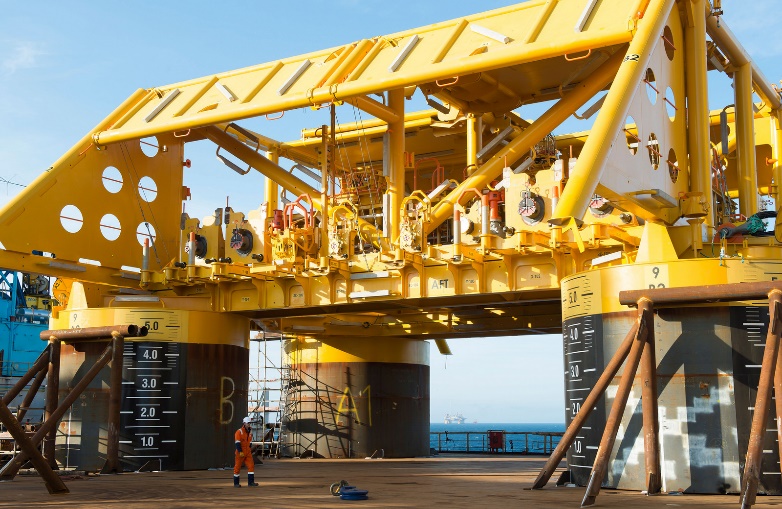
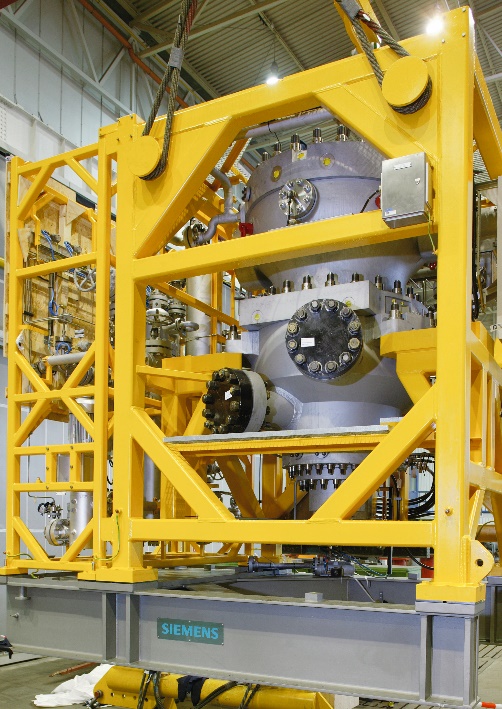
Table
High efficiency of SPC use opens up great perspectives for its vast use on the offshore of the Arctic seas. Today multinational oil and gas corporations in collaboration with international electrical technical companies experimentally prove efficiency of their development. This enables increasing their efficiency and competitiveness in the world hydrocarbons market significantly, creating a huge reserve for the future in development of offshore oil and gas technologies. To a large extent via development of high-performance technical facilities of the offshore exploration, multinational oil and gas corporations and governments of countries to which they belong, will have access to hydrocarbon deposits, regard-less of their location on the offshore territory of any state.
References
- Durymanov, V., & Leontyev, S. (2010). On land and under water: encapsulated compressor unit STC-ECO-II by Siemens. Turbines and diesels, 2, 10-15. (in Russian)
- Hua, G., Falcone, G., Teodoriu, C., & Morrison, G. (2012). Comparison of multiphase pumping technologies for subsea and downhole applications. Oil and Gas Facilities, 1 (1), 36-46.
- Li, W., Gong, J., Lu, X., Zhao, J., Feng, Y., & Yu, U. (2013). A study of hydrate plug formation in a subsea natural gas pipeline using a novel high-pressure flow loop. Petroleum Science, 10 (1), 97-105.
- Menshov, B., & Ershov, M. (2000). Electrical technical installations and complexes of oil and gas industry. Nedra, 487. (in Russian)
- Parks, D., & Aminb, R. (2012). Novel subsea gas dehydration process, the process plant and dehydration performance. Journal of Petroleum Science and Engineering, 81, 94-99.
- Parks, D., & Pack, D. (2013). Design concept for implementation of a novel subsea gas dehydration process for a gas/condensate well. Journal of Petroleum Science and Engineering, 109, 18-25.
- Paula, L., Storti, F., & Fortaleza, E. (2015). Sliding control applied to subsea oil and gas separation system under fluid transient effects. IFAC-Papers On Line, 48 (6), 33-38.
- Tolstov, S., & Mirzoyev, D. (2011). Underwater technology of hydrocarbon production - a key factor in the development of the Arctic offshore resources. Gas industry, 661, 12-18. (in Russian)
- Vasilev, B., & Mardashov, D. (2016). Electromechanical systems of subsea pumping complexes for hydrocarbons transportation from the offshore fields of the Arctic seas. Oil Industry, 1, 85-89.
- Vedachalama, N., Srinivasalub, S., Ramesha, R., Aarthia, A., Ramadassa, G.A., & Atmananda, M.A. (2015). Review and reliability modeling of maturing subsea hydrocarbon boosting systems. Journal of Natural Gas Science and Engineering, 25, 284-296.
Copyright information
This work is licensed under a Creative Commons Attribution-NonCommercial-NoDerivatives 4.0 International License.
About this article
Publication Date
20 July 2017
Article Doi
eBook ISBN
978-1-80296-025-9
Publisher
Future Academy
Volume
26
Print ISBN (optional)
Edition Number
1st Edition
Pages
1-1055
Subjects
Business, public relations, innovation, competition
Cite this article as:
Vasilev, B. U., & Zirin, V. V. (2017). Technologies for transporting hydrocarbons from offshore Arctic seas. In K. Anna Yurevna, A. Igor Borisovich, W. Martin de Jong, & M. Nikita Vladimirovich (Eds.), Responsible Research and Innovation, vol 26. European Proceedings of Social and Behavioural Sciences (pp. 977-984). Future Academy. https://doi.org/10.15405/epsbs.2017.07.02.126