Abstract
A defect can easily been spot or simply exist without you notice it and this can become a big problem in building construction industry. Large amount of money been spent to rectify the building defects. The paper tends to expose the typical building defects either it latent or non-latent by identifying the defects from the real rectification projects accumulated from the real practice. The objective of the paper other than identifying the most common defects happened is also to guide the practitioners within the building industry from doing the same mistake. A total of 5,243 building defects has been identified from the data gathered from Specialist Waterproofing Contactors’ (SWC) real projects of about 100 totals of buildings been analysed. Mix methods combining the qualitative and quantitative is used to gather the nominal and ordinal data with the empirical research approach been formulated. The paper found out that most defects happened caused by water seepage with concrete flat roof lead the way. Most of the defects affected mostly to government office buildings. Lack of proper maintenance is the most problematic factor affected the roofing component. The wet areas such as the toilet areas is the most problematic space within the building interior. As a conclusion, a central data base accumulating all the building defects must be formulated to become as a direct reference point for the building industry players to refer to in order to obtain a defects-free building in the future.
Keywords: Building defects, construction defects, interior defects, building waterproofing
Introduction
Construction industry all over the globe is getting more sophisticated, advance and growing every day. Despite the development, building industry is dealing with one major problem i.e. building defects. Building industry players are always striving to overcome challenge of defects in buildings but it is not easy to deal with it completely (Singh & Kaur, 2019). With Fourth Industrial Revolution (IR 4.0.) on hand and expected to change how we work, live and communicate to each other; construction industry in Malaysia seems to be in stagnant mode instead of making the construction industry’s defects tackling scenario in positive mode; targeted on the industry players to work efficiently and systematically in handling the seen and un-foreseen building defects. However, millions of Ringgits still need to be spent yearly and annually in order to tackle the rigorous building’s defects.
Figures spending on defects maintenance
In 2011, the Malaysia government spent RM514 million to rectify defects to 5,555 blocks of classrooms within to the 2,202 number of schools around the country. In 2017, the state government of Johore allocated RM25 million per year to maintain and repair on the building defects of 73 PDK; Community Rehabilitation Centre located scattered around the state. In a recent report, since 2008, Penang State government spent as high as RM173 million, just to maintain and doing the rectification works on building defects for the identified old government own public housing buildings (Dermawan, 2019). In 2006, the defect costs are about Australian $1 billion per annum in considering the annual turnover of the state of Victoria residential construction industry was Australian S18 billion (Mills, Love, & Williams, 2009). That’s represent a huge 5.5% of the annual defects construction cost solely allocated to do the rectification works and it is a big issue unfortunately.
Conceptual framework on research activities
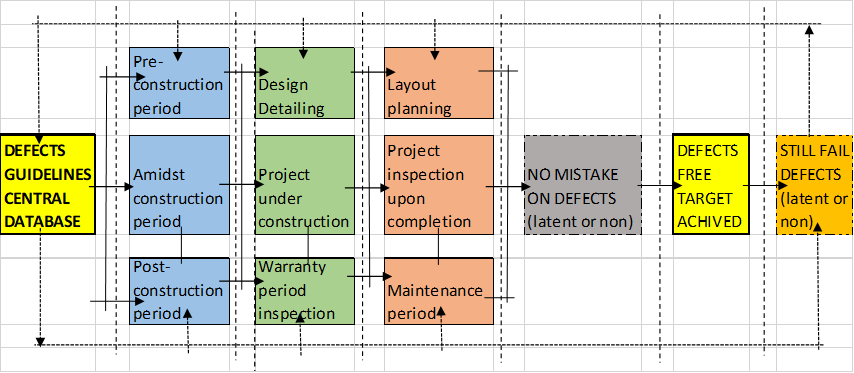
Figure 1 above showing the conceptual framework formulated to tackle on the research. In order to improve the ability of researchers to successfully conduct research in built environment, understanding of its fundamental may help researchers in enhancing their knowledge (Bakar, Roosli, Kamal, & Rashid, 2017). The process basically running into 3 phases: the pre, mid and post-construction period, the design, construction and warranty period and during the maintenance phase period. The conceptual framework was formulated targeted to achieve defects free building construction product scenario. If there are still certain defects can be resolved, the process need to refer to the defect’s guidelines central data stage during the earlier point.
Problem Statement
A list of problem statements has been identified to understand the project issues that need to be addressed toward developing the solutions and how to tackle the study. Those are as follows:
- No central compilation on defects found and can be properly referred.
- No comprehensive defects reference guidelines ever documented as evidence properly recorded to identify latent defects.
- There is no proper record and centrally documented on repeated defects; something that the industry players can be referred.
- No centralize data been found segregating the defects cause pattern on building defects: latent or none.
- At least 10% of building maintenance cost contributed to solve latent and non-latent defects.
Research Questions
These are the research questions outlined in relation to project as the fundamental core to run the research. Those are:
- What is the most type of defects found in construction industry in Malaysia; either latent or non-latent?
- How to identify latent defects in order to solve the problem with unidentified building defects problem?
- Why construction defects keep on happening although building industry already taken place half a century in modern Malaysia?
- What are the factors affecting the patterns of building defects regardless whether it’s latent or none?
- What is the impact on the Malaysia construction industry if building defects especially latent defects not resolve?
- How zero building defects concept can contribute to sustainable building scenario in Malaysia
Purpose of the Study
These are the goals why the study is being conducted. Those are as follow:
- To identify the most type of defects found in Malaysia construction industry either during pre, current or post-construction period (maintenance period).
- Identified latent defects will help the industry players in solving the defects problems efficiently.
- To identify on the type of defects always happened and from keep on repeating hence reducing the defects number in Malaysia construction scene.
- To identify the factor affected the defect patterns on Malaysia construction; pre, present and past period.
- To elevate to the highest level on construction quality in Malaysia thus putting construction cost in efficient mode.
Research Methods
Figure 2 below presents the methodological framework approach in doing this research. There are 3 stages identified with literatures to be reviewed, data collection phase other than to come up with the proper report after analysing the data. Therefore, research must be conceptualised carefully and with rigour in the formulation of methodology and method which could contribute to the body of knowledge for built environment on wider scale (Bakar et al., 2017). The research is using mix method with qualitative and quantitative research modes employed. 67 Likert scales questionnaires has been identified and formulated as part of the quantitative approach method of the research.
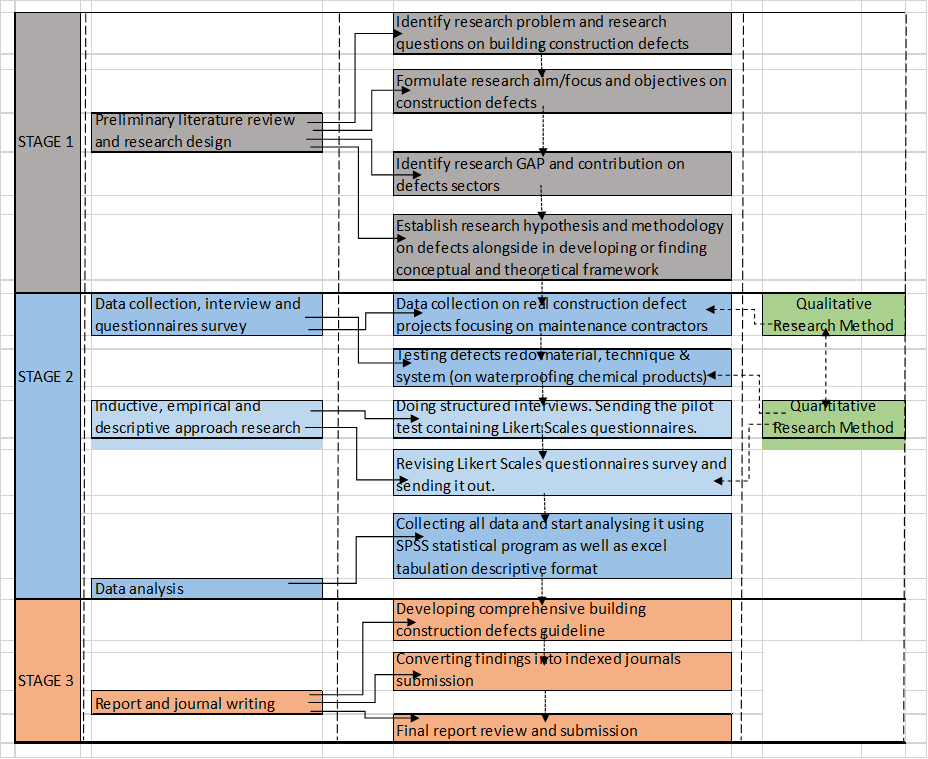
Quantitative method approach on respondents and Likert Scale
Final set of questionnaires is to be modified after a batch of pilot test questionnaires been done as well as to quest responds from the structured interview questions been analysed and reviewed. Targeted to 50 respondents has been identified to run the pilot test and targeted 150 respondents has been marked for the real Likert scales questionnaires exercise. Expertise from the construction industry players ranging from architect, interior architects, specialist waterproofing contractors (SWC), project managers as well as facilities manager are targeted to respond on the structures interviews, the pilot test and importantly for the Liker Scales exercise. Like nominal data, ordinal data based on the calculation of things assigned to specific categories. The most obvious sample of ordinal data comes from the use of questionnaires in which respondents are required to respond on five or seven-point scale such as the Likert scale (Denscombe, 2010).
Qualitative method approach on real defects projects
As far as the qualitative approach of the research concern, a total of 3,131 defects especially affected the building’s interior has been identified focusing on water originated defects pertaining to the range of government buildings over a period. Furthermore, 1,209 defect cases have been calculated on 8 defect factors and 903 total roof defects identified for the exercise. Friedman (2017), stressed regarding building interior troubleshooting on how to inspect, diagnose problems and repair all components of building interiors including the ceilings, floors, walls, trims, doors and windows must be addressed correctly and inspected systematically.
Findings
As indicated in Table 1 above, there are 3,131 total of building defects has been accumulated focusing on water originated defects ranging from building envelope, material deterioration, leakage from flat concrete roof, window and door seepage and lastly from the water tank leaking. As stated in the first row of the table indicated a total of 86 defects derived from the moisture and thermal vapour problems from the identified 21 types of buildings still exist. Stated in Part VI in constructional requirements; 84 (1) Suitable measures shall be taken to prevent the penetration of dampness and moisture into the building (2) Damp proof courses where provided shall comply with BS 743 (Material for Horizontal D.P.C) clearly stated as code regulation to be followed (Legal Research Board of Malaysia, 2005).
This paper research somehow focusing on government buildings category such as government hospitals, TNB’s substation buildings to the government quarters and to the government owned airport hangar (see Table 1 above). The data for this exercise has been sourced with the kind cooperation from the identified waterproofing specialist contractors operating at offices within the Klang Valley location as well as in Pulau Pinang, Malaysia. A total of 4 main specialist waterproofing contractors (SWC) has been identified but only to focus on actual waterproofing specialist projects done for the selected government buildings. For data information the projects calculated happened range from the current project including from the last 10 years circa year 2009. A total of the highest defects found with 282 originated from the problem of flat concrete roof. Mahli, Che-Ani, Yahaya, Tawil, and Mydin (2014), research finding on school buildings stated the most defect found is on the building’s wall part with 18%. For this research, the lowest is 37 defects concerning leakage from the swimming pool located on top of the roof typically located on top of the annex block. Interestingly, 39 defects detected from the leaking of the air-conditioning wastewater seeping through the interior of the building and for this case happened to the government office buildings. According to Ching (2018), people spend major portion of their life indoors; with- in the interior spaces hold by the structures and skins of buildings.
It is from the same category of the government office building mostly located at Putrajaya Government Precinct having with 429 water-based defects concerned. The least defects total with only 34 defects leaking through several building storing weapons located at Gemas Army camp in Negri Sembilan and at weapon storage block at the Subang Royal Air Force building. It can be concluded with the good total of 21 selected government building types ranging from hospital to courthouse building; 149 water originated building defects are summarised during a period of 10 years with 14 defects per year per building type. Obviously, more defects happened during the last 3 years compare to the earlier years when the building start with the defective reconstruction.
It is interesting to notice the rectification works of the waterproofing defects affected from the newly finished buildings especially those located at the Putrajaya Government Precinct to the heritage building of the Kuala Lumpur courthouse aged circa 80 years of age. It is interesting to note that the age of the buildings range for example the Hospital Pulau Pinang aged 100 years compared to Hospital Serdang aged 25 years. As for the university buildings; the statistics involved buildings from Universiti Malaya’s student housing di Kuala Lumpur to faculty and student housing buildings Universiti Sains Malaysia in Pulau Pinang as well as administrative buildings from private Multimedia University in Cyberjaya, Selangor. It is estimated that 85% of these buildings located inland leaving about 15% of the researched buildings located at the coastal vicinity. Talib and Sulieman (2011), addressed building located on the coastal area will require more maintenance and expose to further defects compare to buildings located further inland due to the salted effect of sea water.
Focusing on typical roofing defects
Table 2 below presents the factors affecting the specialist waterproofing contractor in handling the defects rectification works in relation to the typical roofing leakage. The identified roofing defects ranged from concrete flat roof, metal roofing, tile roof and asbestos roofing including problem with Rain Water Down Pipe (RWDP, flashing and air-conditioning piping leakage. However, the entire of building is subjected to the various forms of defects, failures, deteriorations and variations (Bakri & Mydin, 2014). A total of 903 of the defects found from the study of the project listing of 4 specialist waterproofing contractors operating in Kuala Lumpur, Selangor and Pulau Pinang area. Within the period of 10 years (2009 until now 2019). A total of 472 of first-time defects have been detected and 424 repeating defects was total-up. With 111 total defects accumulated for the poorly joint tasks on the asphalt make-over for the concrete flat roof category with 32 of them represent the highest defects on lacking proper maintenance schedule taken. It can be summarised that with poor asphalt joint works combined with poor maintenance done is the key factor affecting the highest number of defects occurred for this category. The minimum total defects with 24 defects represent on the building movement potentially due to loading factor thus affect ting on the roof part of the building. It is interesting to note that there are still cases having buildings using asbestos as the main roofing material even though asbestos already been identified hazardous material to human thus need to be removed ideally. A total of 122 asbestos roofing defects has been identified during this qualitative research data collection method. Due to health risk, do not maintain and keep using asbestos roof. Total replacement is required, and it is highly recommended to replace it with asbestos-free roofing material with-in an immediate mode (Talib, Ahmad, & Sulieman, 2015a).
Tackling future defects problem
Most building defects are avoidable. However, the defects be able to occur, not through a lack of basic knowledge but by non-application or misapplication of it (Douglas & Ransom, 2013). However, each defect has its own character and unique cause; and the produce of the right remedial material can eliminate the defects to re-occur again (Talib, Ahmad, & Sulieman, 2015b). Table 3 however shows that a total of 1,209 accumulated concluded defects have been identified pertaining to building defects relating to the building component. 234 total defects have been summarised as the highest number of defects found in relation of lacking on the creative method in solving defect problems. On the other hand, only 47 building defects identified under the category of not following the building occupancy requirements represent 4% of the total defects which is the lowest one.
Defects appear due to the task was not carried out in a good and superior workmanship in accordance to reliable practice or practical design or due to wrong materials have been selected and used (Pinsent Masons LLP, 2011). 90 number of defects are identified representing the roof eaves and air-conditional piping part of the future defects problem uncover. 8 X-categories of the component can be called as the future defects has been categorised ranging from design matters to not following the building occupancy requirements. The Y factors have been segregated to start with the roofing components; floor, wall and ceiling portion; expansion joint and sealant part and lastly on the wet areas including the toilet part of the building. Holden and Liversedge, (2011) theorised ideally that brick wall is best designed and detailed to cast-off water, to deal with splash-back and capillary flow of water from the ground, to cope with hot and cold of day and night, and to protect against structural damage.
Conclusion
A total of 5,243 various types of building defects regardless latent or non-latent has been identified from the study extracted from Figure 1, 2 and 3. The defects data is accumulated from the pain-staking digging from 4 selected active specialist waterproofing contractors (SWC) whom the author familiar with practiced mostly doing the building waterproofing rectification work in the Klang Valley, Putrajaya, Melaka, Negri Sembilan as well as in Pulau Pinang, Perak and Kedah. The rigorous task in identifying the defects data by tracing the related works within 10 years period starting from 2009 until 2019 turn out to be good for defects comparison study purposes. 80% of the buildings identified are 100% government owned or owned by GLC; companied related to the government and the remaining of the building in this qualitative data collection exercise belong to the private companies. Chong and Low, (2006) indicated that most of building defects visible 2 years after occupancy. Next, 80% of the buildings identified for this research, aged between 0 to10 to 40 years old, 15% of them aged 60-80 years old and the remaining 5% aged roughly between 90- 125 years of age and considered heritage buildings. The sample of these buildings have been identified as shown in Figure 1 ranging from the vernacular style of Hospital Pulau Pinang, International style with Le Corbusier influence style of Hospital Kuala Lumpur to the modern style design of Hospital Serdang in Selangor.
It can be concluded that the main problem of building defects during the post completion phase i.e. during the maintenance period is cause by water seepage. 19 identified main causes have been identified as the main factors affecting the building structures through water seepage problem. 21 building types have been identified through various waterproofing projects done on the rectification works and within these building type consist several numbers of building within the same category. Building with the flat concrete roof design having the most problematic with building leakage defects. However, it is not the case of the building material giving the problem of the defects, but it seems the problems coming from poor maintenance schedule been done to the building. The second factor affected on this matter is due to most of the contractor especially to the specialist waterproofing contractors’ poor labour workmanship in performing the rectification of the defect works. There are 8 identified factors concerning what to be considered the aspects to be taken seriously in tackling future building defects. Most of the contractor’s rectification works typically come with minimum 10 to maximum 15 years warranty period. In this case, the rectification works done by them must be at its best performance and using the best possible solution to ensure no rectification work to be done after the initial rectification work done (Talib, Sulieman, Ahmad, & Boyd, 2015c). Talib, Boyd, Hayhow, Ahmad, and Sulieman (2015d) furthermore indicated that other than warranty and rectification problem, materials are often to blamed for defects when the cause lies in the choice of unsuitable materials and/or when their limitations are not recognized and not considered in design and design detailing. It seems like lacking creative method in solving the defects problem whether the defects are latent or non-latent impacting the most on defects caused. Construction industry with these much of identified building defects still need to be tackled seriously in order to reduce the burden of the building owner especially the government as the taxpayer money being used to pay for the defects rectification works.
Acknowledgments
The author would like to thank USM RCMO through grant no 1001/PPBGN/9016034 for the funding in publishing this research.
References
Bakar, A. H. A., Roosli, R., Kamal, E. M., & Rashid, Z. Z. A. (2017). A complete guide to academic research in built environment and engineering. Retrieved from https://books.google.com.my/books?id=UaxoDwAAQBAJ&pg=PT4&lpg=PT4&dq=complet
Bakri, N. N. O., & Mydin, M. A. O. (2014). General building defects: Causes, symptoms and remedial work. European Journal of Technology and Design, 3(1), 4–17.
Ching, D. K. F. (3rd Ed.). (2018). Interior design illustrated. Retrieved from https://www.slideshare.net/Preciousgu776h/pdf-download-interior-design-illustrated-by-francis-d-k-ching-full-books
Chong, W. K., & Low, S. P. (2006). Latent building defects: Causes and design strategies to prevent them. Journal of Performance of Constructed Facilities, 20(3), 213-221.
Denscombe, M. (2010). The good research guide: for small-scale social research projects. Retrieved from https://books.google.com.my/books?id=woS5P2Y6HFUC&dq=good+research+guide+for+small+scale+social+research+Martyn+denscombe&hl=en&sa=X&ved=0ahUKEwiS-JKiysfiAhWJpo8KHSZVBagQ6AEIMjAB
Dermawan, A. (2019, April 30). 5 public housing schemes in Penang identified for urban regeneration. News Straits Times, Media Prima Group, p. 1. Retrieved from https://www.nst.com.my/news/nation/2019/04/484342/5-public-housing-schemes-penang-identified-urban-regeneration
Douglas, J., & Ransom, B. (4th Ed.). (2013). Understanding building failures. Retrieved from https://www.routledge.com/Understanding-Building-Failures-4th-Edition/Douglas-Ransom/p/book/9780415508797
Friedman, D. (2017). Building interiors finishes and materials. Retrieved June 2, 2019, from https://inspectapedia.com/interiors/Building-Interiors.php
Holden, R., & Liversedge, J. (2011). Construction for landscape architecture. London UK: Laurence King Pub.
Legal Research Board of Malaysia. (2005). Uniform Building By-Laws 1984 [G.N. 5178/85]: (as at 1st March 2005). Retrieved from https://books.google.com.my/books?id=uPhrAQAACAAJ&dq=Uniform+building+by-laws+international+law+book+services&hl=en&sa=X&ved=0ahUKEwjduNfwh8jiAhWBNo8KHZO7AwwQ6AEIKjAA
Mahli, M., Che-Ani, A., Yahaya, H., Tawil, N. M., & Mydin, M. A. O. (2014). School building defect pattern. MATEC Web of Conferences, 15, (01007), 1-5.
Mills, A., Love, P. E., & Williams, P. (2009). Defect costs in residential construction. Journal of Construction Engineering and Management, 135(1), 12–16.
Pinsent Masons LLP. (2011). Defective work in construction projects. Retrieved June 2, 2019, from Out-Law.com website: https://www.out-law.com/en/topics/projects--construction/construction-claims/defective-work-in-construction-projects/
Singh, J., & Kaur, K. (2019). Defects in buildings causes and remedies. Retrieved June 2, 2019, from NBM&CW website: https://www.nbmcw.com/tech-articles/tall-construction/29714-defects-in-buildings-causes-and-remedies.html
Talib, R., & Sulieman, M. Z. (2011). Towards more manageable coastal building; Initial coastal building construction guidelines. American Journal of Engineering and Applied Sciences, 4(2), 307-313.
Talib, R., Ahmad, A. G., & Sulieman, M. Z. (2015a). Classification of factors contributing to roof leaking focusing on clay tile roof and asbestos roof on Malaysia heritage buildings. Advances in Environmental Biology, 9(5), 11-14.
Talib, R., Ahmad, A., & Sulieman, M. Z. (2015b). Building design failure. Why did it fail? How it could have been avoided? International Journal of Chemical, Environmental & Biological Sciences, 3(5), 372–378. http://www.isaet.org/images/extraimages/P815220.pdf
Talib, R., Sulieman, M. Z., Ahmad, A. G., & Boyd, D. (2015c). Classification of factors contributing to roof leaking on Malaysia heritage buildings focusing on concrete flat roof and metal roofing. 21st Annual Pacific-rim Real Estate Society Conference. http://www.prres.net/papers/Talib_Classification_of_Factors_Contributing_%20Roof_Leaking.pdf
Talib, R., Boyd, D., Hayhow, S., Ahmad, A. G., & Sulieman, M. Z. (2015d). Investigating effective waterproofing materials in preventing roof leaking; Initial comparative study: Malaysia, U.K. Procedia Manufacturing, 2, 419-427.
Copyright information
This work is licensed under a Creative Commons Attribution-NonCommercial-NoDerivatives 4.0 International License.
About this article
Publication Date
26 December 2017
Article Doi
eBook ISBN
978-1-80296-950-4
Publisher
Future Academy
Volume
2
Print ISBN (optional)
-
Edition Number
1st Edition
Pages
1-882
Subjects
Technology, smart cities, digital construction, industrial revolution 4.0, wellbeing & social resilience, economic resilience, environmental resilience
Cite this article as:
Talib*, R. B., & Sulieman, M. Z. B. (2017). Behind Construction Fence: What Should We Do To Practice Zero Building Defects?. In P. A. J. Wahid, P. I. D. A. Aziz Abdul Samad, P. D. S. Sheikh Ahmad, & A. P. D. P. Pujinda (Eds.), Carving The Future Built Environment: Environmental, Economic And Social Resilience, vol 2. European Proceedings of Multidisciplinary Sciences (pp. 834-845). Future Academy. https://doi.org/10.15405/epms.2019.12.85