Abstract
The automotive industry is one of the main manufacturing industries and has a significant effect on the environment and society. SSCM procedures are specific practices that are implemented into the conventional supply chain and assist an industry transition to an SSC. Firms have a hard time finding the most beneficial practices and understanding how they interact. Unfortunately, no prior research has looked at how these practices interact in the car business, especially from an Indian viewpoint. The goal of this research is to gain a better knowledge of the interconnected influences across SSCM processes, with a focus on the automobile industry. Our study includes perspectives from a variety of stakeholders, including management, societal, environmental, and government organizations. Researchers offer a conceptual model for evaluating automobile industry SSCM practices in the rising Indian economy, based on the Validation Laboratory and Decision Making Trial technique. The researcher discovered interdependencies and the prevalence of the highlighted practices through a survey questionnaire of the above stakeholders. The cause units and effect groups of the practices are depicted in a prominent causal connection diagram. Particular stakeholder viewpoints and composite stakeholder viewpoints are compared and contrasted. According to the findings, the most important strategies for establishing SSCM are performance management to conservation and applying the triple bottom line method in strategic decision making. This research lays a platform for industrial executives to comprehend the interplay between practices, increasing the likelihood of effective SSCM implementation in the automobile industry.
Keywords: Automotive industry, business, supply chain management, sustainability
Introduction
Automobiles are one of India's and the world's most important industries. In the Indian economy, the automobile industry has developed as a bright spot. This industry plays a significant role in Indian society. This industry is regarded as a leader in terms of product, method, and technology. The automobile sector propels economic development, and its efficiency is a barometer of the economy's health. The automobile production process is facing today many challenges, including cost reduction stress due to customer anticipations, producing global brands at local prices, flawless finish product implementation without line halts to prevent massive penalties, capacity planning due to fluctuating demand, incorporation and ties with consumers at the new item growth phase due to extra resources and costs, and concerns in sharing personal data about the new ICT helps to improve speed and efficiency, transparency, precision, and flexibility, among other things.
Several studies on the use of communication and information technology (ICT) in various elements of logistics distribution operations were done (Gayialis et al., 2022; Shiralkar et al., 2021). The current condition of IT utilization and its effect on logistics service efficiency were investigated. Informed that information technology (IT) consists of software and hardware that collects and distributes data. Because SCM is described as a network of companies, these firms cannot create a network unless they have been linked through technology, leading in supply chain visibility and synchronizing supply chain processes with customer needs.
The automotive industry was widely recognized as a key driver of national economic progress and a substantial provider to the world economy (Chen et al., 2020). The automobile was defined as a product with "both shape and structure," having high levels of engineering and being marketed as a fashion item. Because it employs the outputs of practically all manufacturing sectors and supports downstream and upstream sectors, the industry is appropriately referred to as "the industry of enterprises." Electronics have replaced the chassis of assemblies – brake power system, driving, etc., built-in testing equipment, infotainment, and navigational system, and developments in design and materials have all been aided by technological advancements.
Brazil, India, and China are large emerging marketplaces with strong domestic demand and sufficient domestic investment (Enderwick, 2020). Because the sector is an asset, resource, and labour heavy, all stages of management must be involved in functional implementation and scheduling. Government initiatives were a main driving force for the growth of the automobile industry in U.S., China, Brazil, and South Korea, at the Incubation (Fu & Shi, 2023). However, automakers face difficulties in getting a competitive edge, particularly in emerging economies such As India, due to inefficient SSM practices. As a result, numerous aspects of vehicle supply chains in a rising market with its idiosyncrasies must be examined.
The automobile industry is vital to both the world and Indian economies. The global automobile sector (four-wheelers) accounts for 6% of the total manufacturing workforce, 14% of total industrial output value, and 9% of total industrial expenditure (Patole et al., 2021). This also provides US$612 billion to various countries' governmental revenue in the form of fuel, circulation, marketing, and register taxes. The worldwide auto sector has annual revenue of roughly US$6.54 trillion, which is equal to the world's 6th largest economy.
India produced 8 million vehicles in total, comprising 3.5 million passenger automobiles, accounting for 4% and 9% of global output, respectively (Jha et al., 2023). Another important factor in the Indian automotive sector is the auto-components business. India's exports in this industry increased from US$3 billion to US$2 3billion, accounting for 1% of global auto components commerce in current USD (Sheng & Nascimento, 2021). The passenger vehicles and utility automobiles, commercial trucks, two-wheelers, and tractors segments make up India's automobile industry.
The Indian auto market is estimated to be around Rs 550 billion and has been increasing at an annual rate of over 8% for the past several years (Borkhade et al., 2022). Due to a surge in motorcycle sales over the last 3 to 5 years, the two-wheelers segment has propelled total volume gain. However, due to significant discounts, reduced capital rates, and an increase in industrial production, the passenger car and commercial truck segments have recently enjoyed strong growth. The Indian automobile business is fairly consolidated, with two to three players controlling a large portion of overall sales in most categories. Similarly, Bajaj Auto, TVS Motors, and Hero Honda account for over 80% of total two-wheeler sales, while market leader Telco accounts for around 56% of total business vehicle sales (Jha et al., 2023). The auto components sector, on the other hand, is extremely fragmented, while several key categories have dominating competitors.
Automobile Industry Supply Chain
The automobile sector in India has a supply chain that is remarkably similar to the automotive sector in America and Europe (Dhaigude et al., 2021; Fernando, Walters et al., 2018). The industry's orders start at the bottom of the distribution network, with consumers, and work their way up through automakers and third-tier vendors. Instead, the products pass from the head of the supply chain to the customers, as they do in every conventional automobile business (Mathivathanan et al., 2018). Figure 1 shows the automobile industry supply chain. Automakers in India are critical to the supply chain and are in charge of the industry's products and creativity (Balakrishnan & Suresh, 2018; Kumar Singh & Modgil, 2023).
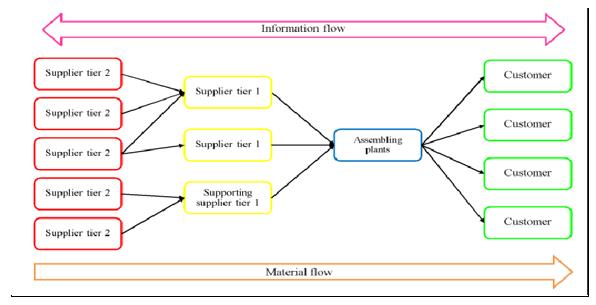
Parties Involved in the Automotive Supply Chain
Tier 3 Suppliers
These businesses supply second-tier suppliers with basic materials such as glass, rubber, plastic, aluminium and steel.
Tier 2 Suppliers
For 1st Tier Suppliers and OEMs, these businesses design car systems or bodywork. They work with designs supplied by first-tier vendors or original equipment manufacturers. They also offer engineering support for complex designs. Fabrication, welding, cutting, twisting, and other services can be offered.
Tier 1 Suppliers
These companies supply significant systems to assemblers immediately. These businesses have a global reach to lead their customers to different parts of the globe. They develop and create to give "black-box" solutions that meet their customers' needs. Suppliers create black-box solutions utilizing their systems to meet the speed and interface criteria set forth by assemblers. First-tier suppliers are in charge of not only putting parts together to make full units like the panel, seats, breaks-axel-suspension, and cockpit but also of managing second-tier providers.
Integration
Due to increased industry competition, automakers were observed focusing on overall supply chain management rather than enhancing specific functional areas (Li et al., 2022). Because the automobile business has a smaller customer base than, say, the FMCG industry, supply chain organisations in the automotive industry use highly visible collaborative forecasting techniques. The product development process is now including supply chain practises. A variety of reasons - world economic turbulence, identifying and responding to growing markets, growing competitive conflicts and customer preferences, and so on – harm achieving flexible practices. 'Lean' and 'agile' methods would help auto supply networks manage these issues, and a model for a 'Leagile' supply chain was been proposed, which emphasizes the importance of dynamically putting 'decoupling points.'
Supply Chain Problems
Visibility, risk assessment, rising customer demands, and globalization are the top 5 worldwide supply chain concerns. It's worth noting that automotive supply chains trail behind other supply chains internationally in these five metrics, showing the need for and scope of significant reforms to make them more efficient and reactive. Automotive supply chains must deal with unique challenges in India that are not found in developed countries. Multinational corporations entering India encounter a variety of hurdles, including cultural differences, pricing inequalities, and sourcing (Luthra & Mangla, 2018; Zhu & Sardana, 2020). Hyundai, for example, adapted successfully to the Indian market by designing the Santro with lower engine output and lower spare component prices. Only 54 percent of the staff is deemed to be of good quality, with a 39 percent attrition rate. Some large Tier-1 auto-component producers are investing in skill development, with Bosch Ltd, for example, using the BVC to provide training in reliability, security, and problem-solving strategies. According to a poll, boosting investment in information systems and process optimization (40 percent), vendor/dealer consolidation (31 percent), and upgrading internal infrastructure are the major measures for tackling SCM issues in the Indian car sector (10 percent). In the future, OEMs will increasingly outsource module assembling, scheduling, planning, and inventory control to logistics providers.
OEM-Supplier Synergy
Performance expectations, a lack of strategic engagement, and a lack of knowledge are all factors that put pressure on Tier-1 suppliers. Concerns about accountability for quality and design, as well as location, pricing, and modular design abilities, are at the heart of the OEM-auto component maker’s relationship. 'on-site' suppliers contribute significantly to entire supply chain performance by ensuring part uniformity and cost-effectiveness. Suppliers have taken on more responsibility in sub-assembly and assembly research and innovation as a result of OEM outsourcing, demanding broad technological progress. Global suppliers, in particular, confront logistical, local material and reliability, supplier innovation, reliability, and cost problems. Maruti Suzuki was one of the first companies in India to implement the VMI system with its element suppliers, resulting in significant inventory reduction and improved planning and shipping schedules. Tata Motors' 'One Part One Vendor' concept attempts to reduce the number of vendors significantly. Global OEMs and element makers want stable JIT suppliers who are close by and have a JIT material procurement and controlled material supply system in place. Although many Indian suppliers meet international industry requirements, lower–tier suppliers must be developed to ensure worldwide competitiveness.
Visibility and Leveraging Technology
Technology is commonly viewed as a supply chain facilitator, lowering levels of inventory and storage, decreasing lead times, and encouraging cooperation with vendors and distributors (Omar et al., 2020). In the majority of firms, IT managers report a "lack of congruence" between business objectives and IT deployment plans. Despite a high level of knowledge among Indian Tier-1 firms, the use of productivity-enhancing tools including such big data, ERP, and RFID is still limited, particularly among Tier 2 suppliers, based on cultural, economic, organizational, and technological constraints to overcome. Among car component manufacturers, TVS Industries makes extensive use of technology in its supply chain. Even while commodity costs and wage costs rose, lean production strategies at Sundaram-Clayton, a large auto component maker, resulted in a 2.5 to 5% reduction in product costs. In the Indian automobile sector, indigenization was essential to cost competitiveness.
Quality and Performance Measurement
In times of economic instability and diminishing demand, establishing practical, robust supply channel benchmarking and efficiency standards is critical for Indian automotive distribution networks, which may be driven to cut costs and, as a result, make "sub-optimal" supply chain actions. To be successful in a dynamic industry like automobiles, a periodic and comprehensive view of supply chain analysis is required. A 'rapid scan' technique used to analyze best practices among 20 European automakers' customers and suppliers, as well as Tier 1 and 2 suppliers, revealed the need to do much more in adopting best practices for developing a flawless supply chain and improving 'business systems engineering.'
These are thoroughly examined the applicability of several measuring performance models, such as the Balanced Scorecard and the SCOR model (Frederico et al., 2020) to the Indian automotive sector. The importance of adopting external and internal quality systems, which lead to "supplier loyalty, contentment, competitive edge, and organizational success," is revealed in empirical research on the function of quality in different production processes in the Indian automotive industry. Quality is still a big issue, with the Quality Control Process and Service Level Associations serving as "order qualifiers instead of order winners."
DEMATEL Application
The DEMATEL approach (Salehi Heidari et al., 2018; Singh & Sarkar, 2020) is used to extract raw information from the 3 stakeholder categories in the form of association matrices.
Step 1: Individual replies are grouped into 3 stakeholder categories (administration, government, and social/environmental). For each of the three perspectives, the aforementioned par value for each cell in the matrix is used to calculate the IDRM.
Step 2: To get the Normalized Relation Matrix, X, the Normalized Value, S, is considered and the IDRM, A, is split throughout by S. Each of the three stakeholder views' Normalized Relation Matrix.
Step 3: The Total Relation Matrix's column and row averages are calculated and shown in Tables 1–2. The total of the row variables is represented as D, and it calculates the sum of the impact given. The sum of column values is the total amount of influence received, which is denoted by R. In this situation, the threshold numbers were generated in each instance, and the Total Relation Matrix values greater than this were chosen for further study of the linkages between practices. The Total Relation Matrix highlights and displays these variables for each viewpoint.
Results and Discussion
The outcomes of the DEMATEL technique are shown in this section. Table 3 shows the combined viewpoint, which is the average of all the separate perspectives' outcomes. Positive D-R values suggest that the practices linked to these values are the most prevalent. The diagraphs in Figures 2–5 depict the causation and effect link between the practices in a visual representation. The prominent practices may be easily identified using the cause and effect categories described in the diagraphs. Because it illustrates the factors and shows the inter impacts, this is also known as an interrelation chart or Impact Relationship Map.
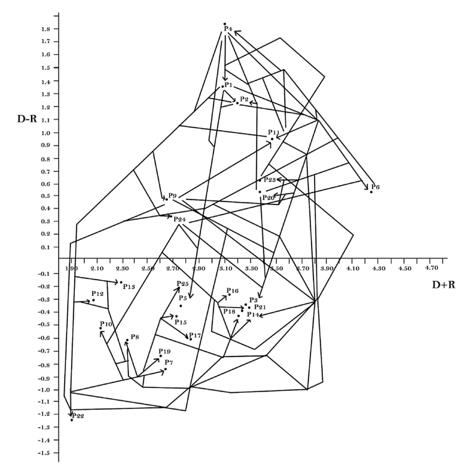
Figure 2 shows the management viewpoint on the importance and connection between the SSCM practices. The head of the arrow was usually at the practice that is the net recipient of the effect; the tail of the arrow is usually at the practice that exerts impact on the other practice. The influencing criteria are in the cause group, whereas the influenced criteria are in the impact group. The subsequent sections break down the findings into two sections: (1) contrast of individual results with merged perspective outcomes, and (2) contrast of individual statistics with merged viewpoint results. All figures and tables should be referred in the text and numbered in the order in which they are mentioned.
Similarities and variances from the perspective of multiple stakeholders
This table shows the most important practices in each viewpoint, and also the overall results. The cause group includes practices P2, P1, P6, P4, P11, P9, P24, P20, and P23 from all perspectives. Management support for SSCM is the greatest priority in each of the viewpoints (P4), suggesting that management engagement to move away from old traditional systems and practices is the first evidence of change. Other practices cannot be adopted without the commitment of management.
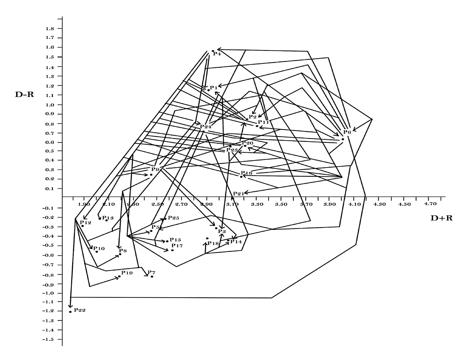
The triple bottom line approach (P1) is the 2nd item on the list of priority practices. The triple bottom line strategy ensures that all 3 aspects of sustainability are given equal weight in all key choices that the company makes, thereby embedding sustainability into the organization's foundation. The third item on the list is supply chain direction (P2). Each perspective's causal group of practices includes the same practices as the other viewpoints, except for a few rare practices. Table 4 highlights certain particular approaches. P16, Redesigning procedures for emissions reduction-related activities, was regarded as top importance in the governmental viewpoint, technology incorporation and worker protections and human rights were ranked as top importance in the sociological perspective. These are the activities that did not cut the influential list in the combined viewpoint; presumably, management and government respondents did not see these practices as critical to the change to SSCM. As a result of this finding, administration and government partners may place a higher value on economic benefits than human rights. Figure 3 shows the government viewpoint on the prominence and connection between SSCM practices.
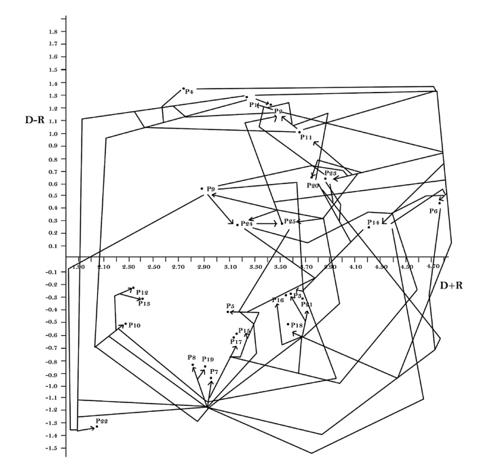
Individual perceptions versus the collective opinions of stakeholders
The average of the comments gathered from individual stakeholder viewpoints is made up of combined stakeholder perspectives. P1, P2, P4, P6, P9, P11, P20, P23, and P24 are the 9 components of the cause cluster that are comparable to the personal views from the combined viewpoint. Figure 4 shows a social perspective on the prevalence and relationship between the SSCM practices. We may conclude from this research that, while external stakeholders have an impact, SSCM techniques must be adopted from within the firm. One of the largest vehicle manufacturers in India is attempting to go toward SSCM on its initiative to get a competitive advantage over other companies. While compliance with obligatory rules enforced by the human rights and government motivates people to embrace SSCM practices, it is ultimately internal management practices that drive change. As a result, these are necessary practices that must be followed for other practices to be implemented successfully.
To attain sustainability, the automotive industry uses SSCM methods. While industrialized countries' strict legislation and government restrictions make it easy for businesses to embrace SSCM processes, emerging economies like India struggle to do so. They are having difficulty identifying the prominent practises that have a major impact on the adoption of SSCM by other practises. Once those important actions have been recognized and implemented, they serve as facilitators for a range of other practises, allowing the firm to fulfil all of the SSCM requirements. DEMA- TEL, a widely-known MCDM approach, is particularly suited to issues involving interdependencies among criteria. The connections between criteria are classified as influencing or being influenced using this way. DEMATEL is a revolutionary method for forming and analyzing cause-and-effect relationships between criteria, as well as inferring the interrelationships between them. We draw the following conclusions based on the findings of our investigation.
DEMATEL was used to investigate the prominence and influences of the 25 practices from multiple stakeholder viewpoints. Multi-stakeholder cooperation is a widely used aspect around the world, and increasing emphasis is placed on collaboration among multiple stakeholders for long-term success. Specialists from related domains in southern India are focused and their views were acquired through survey questionnaires due to the intricacy of the data and the accessibility of only qualitative information. The perspectives of government, management, and society stakeholders on SSCM implementation were investigated in this study.
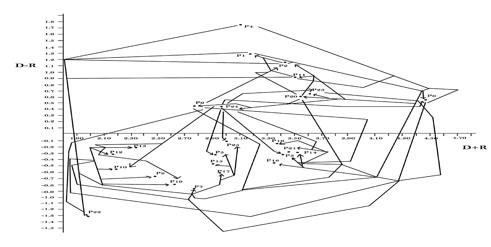
These three variables operate as catalysts for the remaining practices that will increase the firm's long-term viability. The effect group can be easily enhanced by enhancing the cause group. As a result, for better adoption of other practices and sustainability, these prominent practices should be concentrated on and preserved. In each of the 3 stakeholder views, as well as in the combined viewpoints, all of the top practices found are management-related practices. Figure 5 shows the SSCM practices' prominence and relationship—a combined viewpoint. This finding suggests that in developing countries like India, internal executive commitment (P4) is more important than governmental norms and regulations in determining the path to sustainability.
Conclusion
Although India's supply chain standards are still behind those of wealthy countries, there is a considerable possibility for national-level supply chain integration. The study identifies numerous developing outcomes in the car industry that will necessitate significant adjustments in automotive supply chain processes. External assistance in the form of supportive government legislation and policies, as well as infrastructural facilities, is also required. The interconnections between SSCM practices in the automobile industry have been investigated in this study from many stakeholder viewpoints against the backdrop of a rising economy, in India. Future research could look into other developing nations like Brazil or China, which were not addressed in this study. This research is based on the opinions of professionals. Its flaws could include a lack of focus on practical application and the fact that this study is dependent on empirical data and expert views from the automotive industry. There may be room for error in judgement. Another drawback is that the current study assesses the importance of an action based on its impact on other activities.
References
Balakrishnan, A. S., & Suresh, J. (2018). Green supply chain management in Indian automotive sector. International Journal of Logistics Systems and Management, 29(4), 502. DOI:
Borkhade, R., Bhat K, S., & Mahesha, G. (2022). Implementation of Sustainable Reforms in the Indian Automotive Industry: From Vehicle Emissions Perspective. Cogent Engineering, 9(1). DOI:
Chen, X., Wang, E., Miao, C., Ji, L., & Pan, S. (2020). Industrial Clusters as Drivers of Sustainable Regional Economic Development? An Analysis of an Automotive Cluster from the Perspective of Firms' Role. Sustainability, 12(7), 2848. DOI:
Dhaigude, A. S., Kapoor, R., Gupta, N., & Padhi, S. S. (2021). Linking supply chain integration to supply chain orientation and performance - a knowledge integration perspective from Indian manufacturing industries. Journal of Knowledge Management, 25(9), 2293-2315. DOI:
Enderwick, P. (2020). The competitive challenge of emerging markets: China and India. Cambridge Scholars Publishing.
Fernando, Y., Walters, T., Ismail, M. N., Seo, Y. W., & Kaimasu, M. (2018). Managing project success using project risk and green supply chain management: A survey of automotive industry. International Journal of Managing Projects in Business, 11(2), 332-365. DOI:
Frederico, G. F., Garza-Reyes, J. A., Kumar, A., & Kumar, V. (2020). Performance measurement for supply chains in the Industry 4.0 era: a balanced scorecard approach. International Journal of Productivity and Performance Management, 70(4), 789-807. DOI:
Fu, X., & Shi, L. (2023). Direction of Innovation in Developing Countries and its Driving Forces. SSRN Electronic Journal. DOI:
Gayialis, S. P., Kechagias, E. P., & Konstantakopoulos, G. D. (2022). A city logistics system for freight transportation: integrating information technology and operational research. Operational Research, 22(5), 5953-5982. DOI:
Jha, P. K., Mishra, P., & Singh, K. (2023). Automobile sector in India at the current juncture: Crisis and prospects (No. 216/2023). Working Paper.
Kumar Singh, R., & Modgil, S. (2023). Assessment of Lean Supply Chain Practices in Indian Automotive Industry. Global Business Review, 24(1), 68-105. DOI:
Li, X., Liu, D., Zhang, Z., Cheng, T., Liu, L., & Yuan, J. (2022). The impact of internal and external green supply chain management activities on performance improvement: evidence from the automobile industry. Heliyon, 8(11), e11486. DOI:
Luthra, S., & Mangla, S. K. (2018). When strategies matter: Adoption of sustainable supply chain management practices in an emerging economy's context. Resources, Conservation and Recycling, 138, 194-206. DOI:
Mathivathanan, D., Kannan, D., & Haq, A. N. (2018). Sustainable supply chain management practices in Indian automotive industry: A multi-stakeholder view. Resources, Conservation and Recycling, 128, 284-305. DOI:
Omar, I. A., Jayaraman, R., Salah, K., Debe, M., & Omar, M. (2020). Enhancing Vendor Managed Inventory Supply Chain Operations Using Blockchain Smart Contracts. IEEE Access, 8, 182704-182719. DOI:
Patole, A., Pawar, P., Pingle, Y., & Bhakay, J. (2021). India to gain regional leadership in manufacturing sector. Analysis of indian automobile sector: To gain regional leadership. Quest Journal of Management, 12(1), 9-24.
Salehi Heidari, S., Khanbabaei, M., & Sabzehparvar, M. (2018). A model for supply chain risk management in the automotive industry using fuzzy analytic hierarchy process and fuzzy TOPSIS. Benchmarking: An International Journal, 25(9), 3831-3857. DOI:
Sheng, L., & Nascimento, D. F. D. (2021). The BRI and Its Economic Corridors: Opportunities for Development. The Belt and Road Initiative in South-South Cooperation, 83-149. DOI:
Shiralkar, K., Bongale, A., Kumar, S., Kotecha, K., & Prakash, C. (2021). Assessment of the Benefits of Information and Communication Technologies (ICT) Adoption on Downstream Supply Chain Performance of the Retail Industry. Logistics, 5(4), 80. DOI:
Singh, P. K., & Sarkar, P. (2020). A framework based on fuzzy Delphi and DEMATEL for sustainable product development: A case of Indian automotive industry. Journal of Cleaner Production, 246, 118991. DOI:
Zhu, Y., & Sardana, D. (2020). Multinational enterprises' risk mitigation strategies in emerging markets: A political coalition perspective. Journal of World Business, 55(2), 101044. DOI:
Copyright information
This work is licensed under a Creative Commons Attribution-NonCommercial-NoDerivatives 4.0 International License.
About this article
Publication Date
06 May 2024
Article Doi
eBook ISBN
978-1-80296-132-4
Publisher
European Publisher
Volume
133
Print ISBN (optional)
-
Edition Number
1st Edition
Pages
1-1110
Subjects
Marketing, retaining, entrepreneurship, management, digital marketing, social entrepreneurship
Cite this article as:
Krishnan, S., & Chinna, P. R. (2024). Supply Chain Management Practices in the Automotive Industry in India. In A. K. Othman, M. K. B. A. Rahman, S. Noranee, N. A. R. Demong, & A. Mat (Eds.), Industry-Academia Linkages for Business Sustainability, vol 133. European Proceedings of Social and Behavioural Sciences (pp. 938-951). European Publisher. https://doi.org/10.15405/epsbs.2024.05.77