Abstract
The article deals with the issue of quality management digitalization. The study identified factors that hinder the digitalization in quality management and opportunities implementing the system of digitalization. The process of digitalization is irreversible, and enterprises should pay attention to this aspect. Not all economic structures are ready for the implementation of digital technologies. Digitalization in the field of product quality management implies the achievement of strategic goals of the enterprise. The study identified primary tasks in this area. Their solution is associated with the use of modern technologies, the modernization of production facilities, the training of personnel, as well as the transition to a new stage of development in the field of quality management - digital quality or Quality 4.0. The article concluded that quality management professionals should use digital tools and build vital links between quality processes and the transformation and digitalization strategy of the company in order to improve the efficiency of the company. Quality management experts should stop being auditors and turn into process architects, actively finding new solutions to improve the quality standards of products.
Keywords: Digitalization, digital technologies, product quality, quality management
Introduction
World Quality Day is celebrated in November. In 2021, the motto was: “Quality will allow us to take new frontiers.” Nowadays, conquering any frontiers is impossible without digitalization, including in the field of quality control.
In the context of the transition to a digital economy and the use of digital technologies in various sectors of the economy, there is a need to revise the strategic goals of the enterprise and digitalize production processes. In the era of the digital economy, the competitiveness is determined by the use of innovative technologies and a rapid response to changes in the external environment. World Quality Day is celebrated on the second Thursday of November. In many countries, events are held to draw attention to quality problems. Quality is the key to success for enterprises and industries. The federal policy of the Russian Federation is aimed at the development of high-tech industries, the development of products that meet international quality standards (Novikova & Strogonova, 2020).
Quality 4.0 is being implemented by various companies. This concept implies that quality professionals manage process with the help of digital tools and build vital links between quality processes and the overall strategy of transformation and digitalization of the company in order to improve the effectiveness of the company.
Digital technologies can help improve quality in a variety of ways. First of all, this is the collection of real time data as well as their analytics to predict problems. Therefore, one of the first projects in the field of digitalization of quality control was an automated information system for online monitoring of product quality (Serenkov et al., 2015).
The Digital System for Online Monitoring of Product Quality is used by numerous Russian companies. The program records and controls all the production and management processes. Thanks to this system, the work is carried out in a single information environment without manually generating reports, which saves time and improves efficiency. The information environment allows you to collect data in one format from more than 200 enterprises, capturing a huge amount of data. This system accumulates and analyzes a large amount of data on the control of technological processes and can improve the quality of products (Borisova et al., 2020).
Demand for digital technologies creates supply. For example, there has been a need to control the personnel, which has created a demand for special programs. Demand, in turn, led to the emergence of employee time monitoring programs with the ability to broadcast what is happening on the employee's screen online (Kickldler, ActivTrak, Teramind, Hubstuff, Time Doctor).
Problem Statement
One of the main trends in the global economy is the development of an “economy with a new quality”. The gradual transition to this system is due to the globalization of markets, growing competition and consumer demand for better products. The coronavirus pandemic has given a new impetus to the existing trend and accelerated the process of implementing projects in the field of digitalization and automation of quality control. (Quality Control). Planned and systematic activities are carried to confirm that goods produced, services provided and processes performed comply with the established requirements and standards (Idigova et al., 2019).
Modern market mechanisms "force" enterprises to be active. The use of advanced technological solutions in the field of quality control can ensure the development of an enterprise, improve its image and reputation, and become a major competitive advantage in a world where consumers place high demands on product quality.
The problem of product quality is considered important, since it determines the prestige of manufacturers and the country in the world market, and the scientific and technical potential.
The problem of quality is acute for many reasons:
- Quantitative satisfaction of needs for the most important types of products needed by society.
- Increased level of competition.
- Limited raw materials.
- The generally recognized change in the role of product quality in assessing its competitiveness in the domestic and international markets.
Product quality control departments have subdivisions that are responsible for technical and technological aspects of quality control. At the same time, the organizational, economic and information functions of the departments are not clear. Many enterprises have the following problems:
- low throughput of control services and insufficient number of personnel, leading to disruption in the rhythm of production and sales of products, failure to perform quality control functions, the emergence of uncontrolled production sites;
- unreliability of control results, low exactingness and subjectivity in assessing product quality;
- lack of technical equipment and weak metrological support;
- imperfect measurement methods, duplication and parallelism in the quality assessment;
- low wages of employees;
- ill-conceived bonus systems for personnel, causing disinterest in the full and timely detection of defects.
Technical control, aimed at preventing disruptions in the production processes and deviations from the quality requirements contribute to the prevention of defects, detection at the earliest stages of technological processes and prompt elimination with minimal resources.
Quality control prevents the penetration of defects beyond the boundaries of manufacturers, helps to reduce the volume of low-quality products delivered to consumers, reduces the likelihood of additional unproductive costs and eliminates various defects in already assembled products, storage, shipment and transportation of low-quality products to consumers.
Research Questions
At the present stage of economic development, many well-known IT technologies are already being used in the quality management system of enterprises: electronic document management (EDM systems), enterprise resource planning (ERP systems), customer relationship management systems (CRM), management business processes (BPM), etc. The project "Quality Management" tells about the features of these technologies. However, these technologies require people, knowledge and abilities to ensure their use. Digital transformation needs to transfer manual operations of quality management into a digital form. There are many tasks in quality management that require significant human resources, such as collecting and analyzing data on products, processes and organizational systems, monitoring and controlling processes, making decisions based on evidence, scaling quality system requirements to changing processes, identifying and risk analysis (Figure 1).
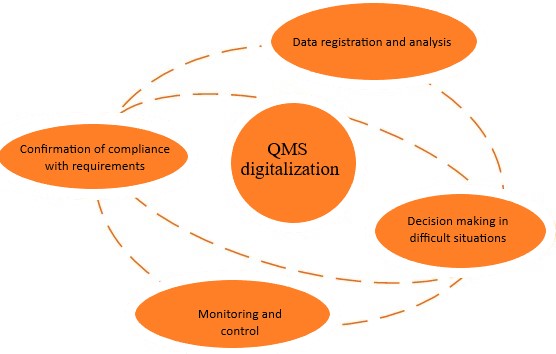
The main trends in the “digitalization” of the quality management system (QMS) are:
Data registration and analysis. This is one of the most time-consuming tasks of the QMS. Reducing the cost and increasing the speed of information storage and processing allows us to measure and record everything that can affect the quality of the product. The Internet of Things and various types of sensors have opened doors to new data sources. It has become possible to place sensors at any location. Big Data provides the ability to analyze these huge, complex and rapidly growing datasets from multiple sources.
Confirmation of compliance with requirements (regulatory documents, specifications, etc.). It is necessary to confirm the compliance with the established requirements (e.g., in pharmaceuticals, medicine, laboratory research). Blockchain technology allows you to have a secure, decentralized and system of proof of the fulfilled requirements. The creation of fictitious certificates or their substitution is excluded.
Monitoring and control. Various quality tools (statistical methods or expert assessments of specialists) are used to manage quality management processes. With the advent of deep learning algorithms for neural networks, it has become possible to use artificial intelligence for these purposes. A trained neural network detects trends and changes in processes more efficiently and faster than a person or automated systems based on the processing of statistical data.
Decision making in difficult situations. The quality management system requires rigidly prescribed algorithms. Algorithms are established in process maps or operating procedures. If the process is complex, and the execution of operations depends on changing parameters, it is necessary either to prescribe all possible options, or to rely on the expert decision. Any ambiguous situation can cause a crash or a stop. Digital transformation solves this problem through the use of predictive analytics.
The development of digital technologies expands the possibilities for quality management at enterprises by reducing the "human factor". However, digital transformation should not be equated with a reduction in human activities.
Purpose of the Study
The aim of the study is to consider the problems and prospects of digitalization in the field of product quality control. To achieve this goal, it is necessary to solve a number of tasks:
- to substantiate the relevance of digitalization of product quality control for the modern economy;
- to identify the main problems in the product quality control system;
- to assess the level of application of digital technologies to improve product quality;
- to analyze the level of application of digital technologies in the product quality control system.
Research Methods
The study used the methods of statistical and comparative analyses, as well as the methods of expert assessment, which made it possible to identify the main problems in the development of digitalization in the field of product quality control.
Findings
The traditional approach to product quality management ensures the implementation of the quality management system based on general or industry standards. With regard to the structure of any quality standard, a number of features can be distinguished:
the standard provides for end-to-end product quality insurance. Of particular importance is the stage of operation, at which the quality depends on the manufacturer and the operator, namely, on compliance with the prescribed operating rules and maintenance regulations;
the process approach: activities are presented as a set of interrelated processes. Performance indicators are determined for each process; they are calculated and subject to monitoring in order to maintain them at the required level;
the need to involve all employees in achieving the required level of product quality. One of the main tasks is to create an environment and communication channels for personnel;
Priority is given to the initial stages of the life cycle, in particular designing, at which the quality level is determined (Serenkov et al., 2018).
The digital format involves the automation of processes, which will help speed up the processing of incoming requests and increase the likelihood of orders. Company executives and CIOs have reasonable questions: what processes can be automated; what software solutions can be used to implement the standards? Some of the tasks can be solved with the help of products that are implemented by the enterprise (Idigova & Rakhimova, 2021).
If all the primary aspects such as design and technological preparation, production planning and standardization have already been digitized and the digitalization is in line, our recommendations are as follows.
1. Before initiating the process of digitalization, the quality management system should be developed, implemented and certified. This will create a verified basis for all internal procedures of the enterprise, which will be transferred to software products. Otherwise, there is a risk of incorrect interpretations of the standards.
2. After the certification audit has been completed, a digitalization project is required. Representatives of the company departments should develop the project.
3. Distribution of the internal processes by electronic systems: for example, requirements management is implemented in the PLM system, and product quality accounting - in the MRP system. The processes use horizontal links between the departments. It is possible that some departments will have to use software products that have not been used before. Accordingly, it is necessary to provide training procedures for employees.
Conclusion
The quality control digitalization is a non-standard task due to the large scope of activities regulated by quality standards. However, it is possible to automate this field. The gradual digitization of internal processes, the use of specialized software products will create an end-to-end product quality control system. Standards are changing; the number of requirements is increasing. There will be methods that depend on the skill level, experience of executors, but this work can and should be automated using software. Digital transformation removes the “routine” from many tasks in the field of product quality control. With the advent of digital technologies, the challenge is to redesign processes and procedures so that both people and digital devices can contribute to quality improvement.
References
Borisova, V. V., Tasueva, T. S., & Rakhimova, B. K. (2020). State support for digital logistics. In: Lecture notes in networks and systems. DOI:
Idigova, L. M., & Rakhimova, B. K. (2021). Current issues of digital transformation of the oil and gas industry. Problems of the economy and management of the oil and gas complex, 18–21. DOI:
Idigova, L. M., Tagaev, C. K., Tasueva, T. S., Israilov, M. V., & Magomadov, E. M. (2019). Modernization of regional industry on the threshold of digital economy. Social and cultural transformations in the context of modern globalism (pp. 2158–2166). Russian Acad. Sci., Complex Res. Inst. Kh. I. Ibragimov. DOI:
Novikova, N. V., & Strogonova, E. V. (2020). Regional aspects of studying the digital economy in the system of economic growth drivers. Journal of new economy, 76–93. DOI:
Serenkov, P. S., Gurevich, V. L., & Romanchak, V. M. (2015). Methods of quality management. Methodology councils. Infra-M.
Serenkov, P. S., Kuryan, A. G., & Volontey, V. P. (2018). Methods of quality management. Process approach. Infra-M.
Copyright information
This work is licensed under a Creative Commons Attribution-NonCommercial-NoDerivatives 4.0 International License.
About this article
Publication Date
25 November 2022
Article Doi
eBook ISBN
978-1-80296-127-0
Publisher
European Publisher
Volume
128
Print ISBN (optional)
-
Edition Number
1st Edition
Pages
1-742
Subjects
Sociolinguistics, linguistics, semantics, discourse analysis, translation, interpretation
Cite this article as:
Idigova, L. M., Plis, S. A., & Chaplaev, H. G. (2022). Quality Management Digitalization. In D. Bataev, S. A. Gapurov, A. D. Osmaev, V. K. Akaev, L. M. Idigova, M. R. Ovhadov, A. R. Salgiriev, & M. M. Betilmerzaeva (Eds.), Social and Cultural Transformations in the Context of Modern Globalism (SCTCMG 2022), vol 128. European Proceedings of Social and Behavioural Sciences (pp. 296-302). European Publisher. https://doi.org/10.15405/epsbs.2022.11.41