Abstract
One of the main goals of any enterprise is to occupy a leading position in the market. Achieving this goal is possible with the introduction of lean production methods into production. In this regard, the methods and means of lean production are considered in the work, the analysis of the features of the introduction of lean production tools and methods at industrial enterprises of the agro-industrial complex is carried out, the mechanism of implementation is also presented. When implementing the concept of lean manufacturing, you may encounter problems of inefficient implementation, in order to avoid mistakes, it is necessary to take into account the experience of enterprises that have already implemented the system. The article develops a model for the integration of a quality management system and a lean production management system. Integration will allow you to combine systems, turning them into a single whole that will meet the requirements of the two standards, which will reduce the amount of documentation and duplication.
Keywords: Causes of costs and losses, customer satisfaction, lean manufacturing concept, lean manufacturing tools and methods, process optimization
Introduction
The main goal of each enterprise is to meet the needs of consumers and all interested parties. After all, the consumer provides a high demand for the goods and services provided, which contributes to the company's entry into a leading position in the market (Bondareva et al., 2021).
To date, this goal can be achieved by introducing the concept of lean manufacturing into the organization. Lean Manufacturing (LM) is an integrated approach based on optimizing processes, providing management infrastructure and changing the way of thinking and behavior of employees (Pozzi et al., 2021). The LM system is based on a constant desire to eliminate all types of losses and use only the necessary resources of the company. The use of tools and methods of the lean production concept makes it possible to reduce actions that do not add value to the product at the entire stage of its production Filatova et al. (2015), which ensures an increase in the quality of finished products, a reduction in equipment downtime, an increase in the production plan and a reduction in losses (Bondareva et al., 2022).
Problem Statement
The introduction and maintenance of lean manufacturing elements allow us to produce products that are in demand from interested parties, which contributes to the company's entry into a leading position in the market.
Currently, in order to significantly increase the efficiency and effectiveness of organizations, the concept of lean production is being introduced. The BP system allows you to eliminate the main causes of costs and losses in the organization, such as:
- overproduction of products;
- the appearance of excess stocks in warehouses;
- irrational transportation of finished products;
- moving production equipment;
- reduced waiting time;
- excessive processing of raw materials;
- the release of defective products for sale.
The advantages of applying the lean manufacturing concept are provided by:
- continuous improvement of product quality at all stages of production;
- cost savings on the production of raw materials;
- reduction of unnecessary space;
- involvement of employees of all departments;
- increasing the satisfaction of stakeholders;
- competitiveness in the market.
Research Questions
Research issues – introduction of lean manufacturing elements and integration of lean manufacturing system and quality management system at industrial enterprises of the agro-industrial complex.
Purpose of the Study
The purpose of the study: to analyse the features of the introduction of lean production tools and methods at industrial enterprises of the agro-industrial complex, to consider the mechanism of implementation, to develop a model for the integration of a quality management system and a lean production management system.
Research Methods
To achieve the goals of the company, the tools and methods of the lean production system are used.
Methods (tools) of the lean production concept (Yusuf et al., 2016):
1) standardization of work.
Standardization of work is a system of accurate description of all actions, rules of production activity, the establishment of their time, the algorithm of implementation. The method allows you to determine the necessary level of resources to achieve the goal.
The function of the method is to perform work with an appropriate level of quality, labor safety and productivity.
2) VSM – mapping of the value stream.
A method of creating a visual graphic scheme that displays information flows for the provision of a service or product. There are two states of value maps: current and future.
The main function of the method is to improve quality by reducing losses.
3) 5S – organization of the workspace.
5S is a system of steps designed to organize and maintain order on work surfaces. The method is applied from determining the source of problems to improving the workplace.
4) SMED – quick changeover.
A method consisting of a set of actions that are aimed at reducing the time during changeover. The main feature of a quick changeover is that actions when the equipment is not working (internal) are rebuilt into actions of the working (external).
The function of the method is to reduce the operating time of the equipment changeover processes.
5) kanban.
The information that appears on the production operation only when it is necessary to use the process. The system responds to the processes of the product life cycle based on the principle of pulling.
The main function of the method is the production of raw materials on time and in the right quantity when required by the consumer.
6) visualization.
A tool aimed at arranging materials, diagrams, details, documents, tables, graphs, etc. in such a sequence that each employee can analyze the state of the production system.
The main functions of the method are visual representation of information in the present tense; rapid response to problems.
7) Poka-Yoke – protection against unintentional errors.
A tool that does not allow more than one unintentional error in a production operation. The main tasks of the system are to detect a discrepancy before the start of the process to terminate the actions; to monitor the error if the process has been performed; to suspend the device so that the product does not go to the next stage. When an unintentional error is detected, the cause of its occurrence should be sought for its elimination and prevention in subsequent operations (Temasova et al., 2021).
8) TPM – universal equipment maintenance.
A system that reduces losses at the entire stage of the life cycle to increase the quality of equipment maintenance. The peculiarity of the method is that in order to reduce losses, all employees of departments should be involved in the work.
The main function of the method is to prevent and reduce losses that are associated with production equipment.
Introducing the concept of lean manufacturing, you may encounter problems of inefficient implementation. In order to avoid mistakes, it is necessary to take into account the experience of enterprises that have already implemented the system.
Findings
The system must be introduced into production consistently, observing each stage.
Let's consider the stages of implementation and their purpose for industrial enterprises of the agro-industrial complex.
Stage 1. Adoption by the top management of a strategic decision on the implementation of the lean manufacturing concept. Definition of the main objectives of the system application. Collecting data on the necessary resources to use tools and methods.
Stage 2. Team formation. Determination of the number of employees, distribution of powers and responsibilities according to the plan. Appointment of a project manager to monitor the execution of work.
Stage 3. Defining processes. The concept is applied in stages, at first, 1-4 processes are introduced that are less susceptible to change. At this stage, it is necessary to determine the chain of pulling and the execution time.
Stage 4. Staff training. Bringing to each employee the concept of principles, tools and goals of lean production. Establish feedback to adjust the implementation plan. To perform successful work, motivate employees.
Stage 5. Production alignment. First of all, it is necessary to align the production schedule, this cannot be done without the introduction of the SMED system. The system allows you to produce products in small batches and, in case of non-compliance, quickly respond to changes.
Stage 6. Implementation of "Poka-Yoke". The application of the self-monitoring method and the detection of an unintentional error must be used simultaneously with the alignment stage. Monitoring the process will help minimize the level of defective products.
Stage 7. Creating a continuous flow. Combining several sites will create a single process in which all the values for the finished product will be collected. Such a solution will ensure the elimination of the main types of losses.
Stage 8. Implementation of 5S. The use of the system will put the workplaces in order, distribute resources, clean up clutter in the room.
Stage 9. Pulling. The pulling system is impossible without using the Kanban method. All sorted resources will be used only when needed. Kanban (information) is transmitted to the next stage of production in the required quantity.
Stage 10. Data collection. After applying lean production tools and methods, all data must be collected and documented at each production stage.
Stage 11. Evaluation of results. The top management, after analyzing the data obtained, evaluates the result of the work and provides recommendations for corrective actions.
Stage 12. Corrective actions. Carrying out work to eliminate the discrepancy, if necessary.
Stage 13. Implementation on the following processes. Application of lean production methods and tools to the main and auxiliary production processes.
Stage 14. Continuous improvement of processes.
When developing an integrated management system (IMS), the main importance is the formation of its structure. The basis of the ISM model consists of general and specific requirements that can be found when they are integrated into the organization's management system.
The basis for the creation of an integrated management system is the ISO 9000 series standard, since it establishes the general principles and concepts of management (Leonov et al., 2020).
The work on the creation and implementation of ISM is formed from the construction of an organizational management structure. The top management appoints to perform the work:
- a representative of the management of the integrated system;
- responsible in structural divisions.
The integrated management system assumes:
- creation of auxiliary units;
- creation of a coordinating council;
- formation of a temporary working group.
General requirements apply to all management systems within an integrated system, and specific requirements apply only to one.
Integration of the quality management system and the lean production management system is carried out by creating a unified flow management system that provides planning, implementation, control and improvement of products or services with the necessary characteristics of quality, cost and time of product flow in accordance with the requirements of consumers and other stakeholders of the organization. The model of integration of the quality management system and the lean production management system developed for industrial enterprises of the agro-industrial complex is shown in Figure 1.
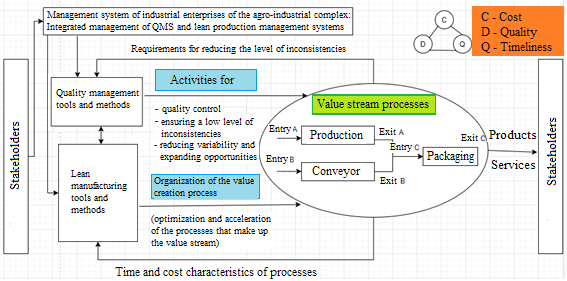
The specifics of the activity of a particular organization can be taken into account only when creating an integrated system by the efforts of its own employees and departments with highly qualified personnel.
Conclusion
In general, the integration of the quality management system and the lean manufacturing system will allow to combine the systems, making them a single whole that will meet the requirements of two international standards, which will reduce the amount of documentation and duplication. The QMS of an organization is a system that ensures stable quality of products or services. The quality of products must comply with legal and regulatory requirements, as well as meet the needs of stakeholders. All processes of the system must be constantly improved. The company's quality management system is developed on the basis of the ISO 9001 standard. The lean manufacturing system is designed to create the value of a product or service in order to increase the efficiency and effectiveness of the organization.
References
Bondareva, G. I., Temasova, G. N., Shkaruba, N. Zh., Leonov, O. A., & Vergazova, Yu. G. (2021). Ensuring the smooth functioning of the equipment during operation. AIP Conference Proceedings, 2402(1), 070022.
Bondareva, G. I., Temasova, G. N., Shkaruba, N. Zh., Leonov, O. A., & Vergazova, Yu. G. (2022). Assessing External Defects at Manufacturing Enterprises. Russian Engineering Research, 42(2), 151-154.
Filatova, K., Rabunets, P., & Zeremskaya, Y. (2015). Lean production principles in summer lean school in Tomsk Polytechnic university. Journal of Economics and Social Sciences, 6(6), 23-26. http://jess.esrae.ru/10-138
Leonov, O. A., Temasova, G. N., & Malykha, E. F. (2020). Methodology for assessing external losses of repair enterprises of the agro-industrial complex when implementing a quality management system. Journal of Physics: Conference Series, 1679(5), 52059.
Pozzi, R., Cannas, V., & Ciano, M. (2021). Linking data science to lean production: a model to support lean practices. International Journal of Production Research, 1946192.
Temasova, G. N., Leonov, O. A., Shkaruba, N. Zh., & Vergazova, Yu. G. (2021). Application of statistical methods for quality control of agro-industrial production processes. IOP Conference Series: Earth and Environmental Science, 839(2), 022026.
Yusuf, A. A., Peter, O., & Uma, K. G. (2016). Lean Concepts and Methods: 3P. International Journal of Scientific Research in Computer Science, Engineering and Information Technology 1, 20-24. https://www.researchgate.net/publication/314175406_Lean_Concepts_and_Methods_3P
Copyright information
This work is licensed under a Creative Commons Attribution-NonCommercial-NoDerivatives 4.0 International License.
About this article
Publication Date
29 August 2022
Article Doi
eBook ISBN
978-1-80296-126-3
Publisher
European Publisher
Volume
127
Print ISBN (optional)
-
Edition Number
1st Edition
Pages
1-496
Subjects
Economics, social trends, sustainability, modern society, behavioural sciences, education
Cite this article as:
Temasova, G., Leonov, O., Shkaruba, N., & Vergazova, Y. (2022). Introduction Of A Lean Production System At Industrial Enterprises. In I. Kovalev, & A. Voroshilova (Eds.), Economic and Social Trends for Sustainability of Modern Society (ICEST-III 2022), vol 127. European Proceedings of Social and Behavioural Sciences (pp. 243-249). European Publisher. https://doi.org/10.15405/epsbs.2022.08.27