Abstract
The article examines the methodology for establishing cost management systems in complex industrial complexes. In the article, the authors pointed out that calculating the cost of coatings produced in an industrial enterprise should not be reduced only to calculating the cost of a planned order. Actual data for the period in question must also be reflected in parallel. The authors present the development of declarative representation of information system of management production accounting in the form of its sub-item model, defining a set of objects of cost allocation in the system of management accounting and their attributes. This model will ensure the participation of process specialists (not programmers) both in the development of the system and in its adjustment in the process of changing operating conditions. The described author's approach by analogy can be used to assess the efficiency of auxiliary materials, energy carriers in paint and varnish production, when calculating the planned direct costs by type in order to compare them with actual costs and assess the deviations that arise.
Keywords: Management accounting system, cost management, metagraph model
Introduction
In modern economic environment as a result of increased competition and the need to adapt as quickly as possible to the constantly changing market environment is becoming increasingly urgent problem of formation, analysis and management of costs in industrial enterprises in order to reduce production costs of goods, works and services.
Cost management is one of the most pressing and important economic problems of industrial enterprises in modern conditions, the successful solution of which provides both an increase in the competitiveness of products and the economic potential of production systems in the transition to an innovative economy, in particular, in continuous production. This problem can be solved by creating information systems of production management accounting (PMA) at industrial enterprises, implementing such functions as the calculation of planned production costs, identifying deviations from established norms, standards, estimates, as well as assessing and analyzing the efficiency of material resources and production equipment in order to identify bottlenecks in the paint and varnish production. Improving the efficiency of these functions involves continuous improvement of all components of the UPS systems, through the use of new business models and procedures for the organization of UPS in complex production complexes based on the application of the process approach, graph models and methods of object-oriented design.
Studies of the problems of solving the problems of management accounting are considered in the works of famous Russian and foreign economists (Drury, 2013; Etrill & McLainey, 2012; Kalinovsky, 2013; Kaverina, 2015; Kizilov & Bogatii, 2015; Sycheva, 2011; Weisfeld, 2014; Vakhrushina, 2014, etc). Successful experience that has passed the test of time and the practice of organization of cost management at domestic enterprises already exists. Domestic practice deeply elaborated issues related to calculating, accumulated a wealth of theoretical and practical experience in the field of the normative method of cost accounting. Until now, practical tools for the formation and management of costs, taking into account the specifics of a particular industrial sector and production, including in the paint and varnish industry, which has a continuous production cycle, are not fully developed.
Problem Statement
Modern cost management tools at industrial paint and varnish enterprises of the continuous cycle must complement the information system of management production accounting with a metagraphic model. It is this model that allows the most adequate reflection of the complexity and versatility of the process of formation and accumulation of costs on technological operations of business processes of an industrial enterprise, in particular, concerning management at paint and varnish enterprises (Suprunova, 2013).
As noted above, the development of cost management methodology in complex production complexes is provided by applying modern forms of business models using a process approach in combination with object-oriented design methods. The example of building a metagraphic model for such an important task as building an information system of management production accounting in calculating the planned cost of finished products with elements of cost analysis of manufactured products at a continuous, paint and varnish, production facility.
Research Questions
Before we start calculating the planned cost of producing paint products in an industrial enterprise, it is worth mentioning two main points that can be solved in the manufacture of paint materials:
- reducing the cost of individual components of the product without reducing its production and sales. Here we mean the cost of purchasing raw materials and materials, in different periods and from different suppliers, and a slight adjustment of the specification (formulation) of the products;
- improvement of functional parameters of products at minimum cost. In this case we are talking about the development of a new formulation with more improved characteristics (parameters) of the operation of paint and varnish products.
We would also like to note that the cost of production is an important financial and economic indicator of the industrial enterprise. The cost of production is understood as the costs expressed in monetary terms for its production and sale. Speaking about the cost of manufactured products, it is worth noting that it is divided into:
- planned - determine the average cost of production for the planned period, that is, contains future costs;
- normative - based on the rates of consumption of raw materials and materials, other costs in force in the planning period;
- actual - compiled on the basis of actual costs (Borisovskiy & Sukhov, 2012).
Purpose of the Study
At the end of each period (month, quarter, etc.) the calculation of the cost of production at the industrial enterprise should not be reduced only to the calculation of the cost price of the planned order, the actual data for the period under consideration should also be reflected, i.e. it is necessary to calculate the actual cost price of the finished products. (Zagidullin, 2011). This will allow to determine the deviations between the indicators of planned and actual production costs, which in turn will allow to see (calculate) the idle time/processing of the used equipment, i.e. the efficiency of the use of production equipment, and the actual labor rate of the production personnel for the period under consideration.
Research Methods
As noted above, the development of the methodology for creating systems of value analysis and cost management in complex production complexes can be achieved through the use of new business models based on the application of the process approach and methods of object-oriented design. Let's consider these issues in more detail on the example of building a metagraph model for such an important task of PM as calculation of the planned cost of finished products with elements of cost analysis of manufactured products at continuous, paint and varnish, production.
Findings
The task of the PMA on calculation of the planned production cost of the manufactured paint-and-lacquer products with the elements of the cost analysis is solved on the basis of the control of the formation process and accrual of costs in the continuous production within a specified planned time period by the cost centers preliminary selected for this production and allows to receive general estimates of production costs for the manufacture of paint-and-lacquer products that are the basis both for choosing the nomenclature of the manufactured paint-and-lacquer products and for detecting technological redistribution, where As a rule technological phases may include other phases or be elementary phases (О6, О11, О18) of technological process (Figure 1).
If Оi is some phase, then Оm, ..., Оk are phases connected with phase Оi by arcs oriented from Оi. Also note that phase Oi is complete if all phases Om, ..., Ok are completed. The beginning of phase Oi is determined by the beginning of the execution of one or more phases Om, ..., Ok, and the end, respectively, by the end of the last phase Om, ..., Ok.
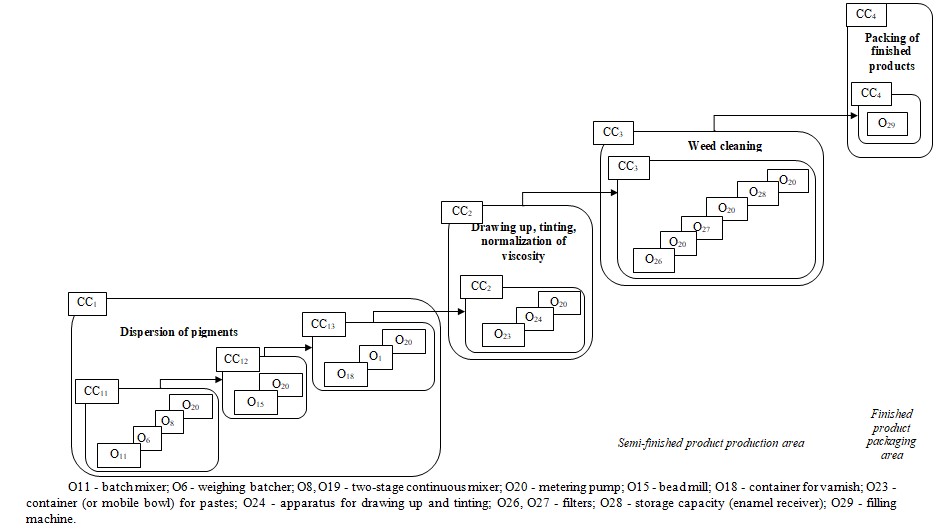
Obviously, taking into account the previously highlighted features of the process approach in the tasks of cost analysis and cost management, the scheme of solving the problem of calculating the planned cost of production should be based on a sequential traversal of the vertices of the cost centers graph in continuous production, starting from its terminal vertices. The object-oriented representation of this graph forms the core of the structural (declarative) component of the task of calculating the planned prime cost of manufactured paint and varnish products in continuous production.
As noted above, this structural component of the problem under consideration includes the definition of such classes as:
- classes of objects that characterize the basic production concepts, in particular, such as "delivery", "volume and periodicity of delivery", "structural units of the enterprise (shops, sections)", as well as directories of such objects as "set of cost centers", "technological NMA", "current resources", "personnel", etc.;
- classes of objects that characterize the basic production concepts, in particular, such as "delivery", "volume and periodicity of delivery", "structural units of the enterprise (shops, sections)", as well as directories of such objects as "set of cost centers", "technological NMA", "current resources", "personnel", etc.
Without dwelling on a detailed description of all of the highlighted object classes, they are discussed in (Perepelitsa, 2012; Sidorova & Gordeeva, 2014), consider the formation of the structure of classes of situations (meta-vertexes of the metagraph of the problem), revealing the scheme of accounting production costs in the cost, as well as the set of connections of classes of situations with each other (edges and meta-vertexes of the metagraph of the problem), characterizing directly the process of formation and accrual of costs. (Sychev & Semyonicheva, 2016).
We will take into account the fact that the process of cost formation in continuous, paint and varnish, production begins with cost accounting in the terminal vertices of the cost point graph for this production (Figure 1), which, in particular, includes the cost center CC11, associated with the cost center of the dispersion phase CC1 included in the work of the "semi-finished products" production area, where batch mixer (O11), weight batcher (O6) and two-stage continuous mixer + dosage pump (O8 + O20) are located. Denoting the metaverse of this cost center as CC11 (Cost Centre11 - current costs of CC1 "pigment dispersion"), we note that the CC11 metaverse consists of many other metaverses characterizing the following situations that occur in the process of calculating costs for this center: "CC11. Plan_task - identification of the current planned task", "СС11. Cost_Material - accounting of direct costs for raw materials and supplies", "СС11. Cost_Energy - accounting of direct energy costs", "СС11. Cost_Auxil_Material - accounting of direct costs of auxiliary materials (recycled water, etc.)", "СС11. Cost_Salary - accounting of direct costs of production personnel salary and social contributions" (Figure 2). Thus, the presented in Figure 2 the general data structure of the CC11 Cost Center metaverse is a composition (strict aggregation), i.e. the relationship between classes when one class is part of another.
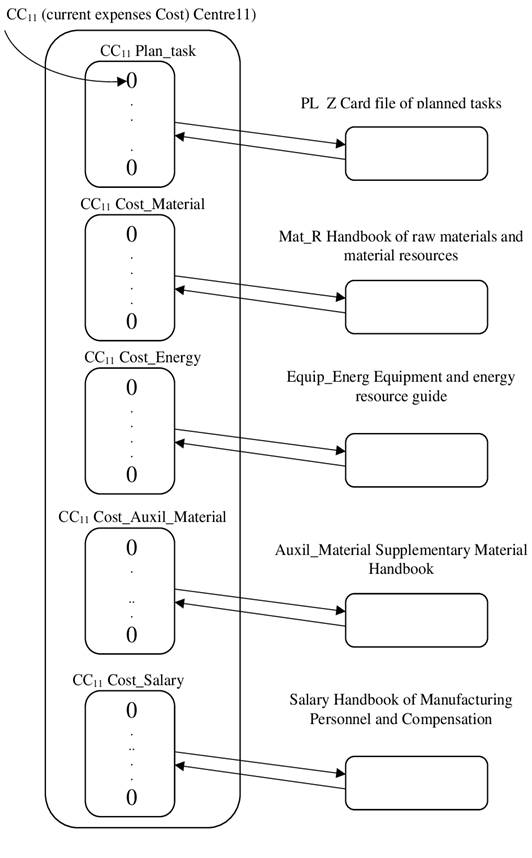
By analogy the corresponding metaverses for all cost centers (CC12, CC13, CC1, CC2, CC3, CC4) are determined. In this case the metaversion mv'12 for SS12 will include the metaversion mv'11 for the cost center SS11, which allows to estimate the current total direct costs for the center SS12, taking into account the process of value accretion, etc. (Figure 3).
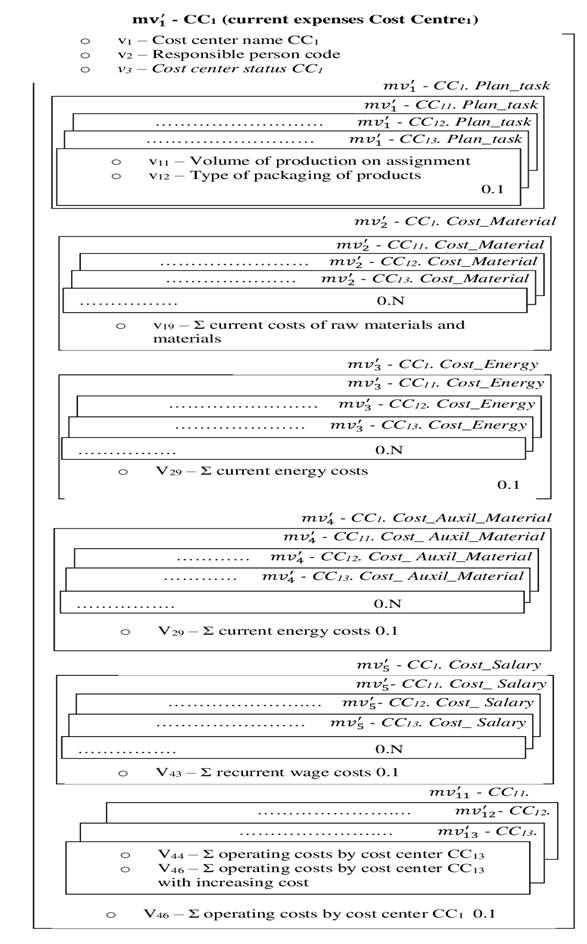
The developed metagraphic model of cost centers of PMA system allows to conduct differentiated accounting of expenses in various slices with their binding to time, nomenclature of let out production, technological operations, types of expenses, places of their origin, etc., thus it is possible to diagnose bottlenecks at paint and varnish enterprise. Also presented metagraphic model is more understandable for engineers-economists (not for programmers) and allows to reflect almost all variety of both technological and structural features of business process.
Analyzing the cost of paint and varnish products produced at the enterprise it is possible to obtain data on the efficiency of manufacturing a separate type of product, product group, the work of the whole technological line. In this work, to assess the accuracy of the calculation, as the main method of calculating the cost of manufactured paint and varnish products the marginal approach is used, based on the developed model of direct cost accounting. In this case, we note that, if necessary, the proposed metagraph approach by analogy can also be used to calculate the full cost of production of paint and lacquer. The indicator of marginal profitability, defined as the difference between the sales revenue of the products produced or the cost of the products produced and direct costs, relative to the UPS system to the class of "direct-costing" systems. This class of systems makes it possible to evaluate the dependence between the volume of production, costs (cost) and revenues more quickly, to classify the output products better and to orient the enterprise to the transition to the output of products with higher marginal profit. However, it is necessary to take into account the important circumstance that taking into account the specifics of continuous, paint and varnish, production, for it should be calculated not just the index of marginal income per unit of output, but the index of marginal income taking into account the limiting circumstances, in particular, the equipment operating time (Drury, 2013).
The developed metagraphic model is expedient to use in the tasks of cost management on deviations, carrying out, in particular, calculation for paint and varnish production of planned direct costs by selected types of costs for their subsequent comparison with actual costs and evaluation of the obtained deviations. In this case to assess the planned costs for one or another type it is necessary to allocate from the built metagraph for cost centers a tree of formation of planned costs using which it is easy enough to get estimates of both total costs and costs for individual technological transitions, which comparison with the actual cost data will indicate the bottlenecks in production.
In addition to obtaining estimates of production costs for the production of paint products, which are the basis for choosing the range of output paint products, developed above metagraphic model is appropriate to use in the tasks of cost analysis and management costs of deviations, carrying out, in particular, the calculation for continuous production of planned direct costs for the above types of costs for their subsequent comparison with actual costs and assess the deviations obtained.
In this case, to assess the planned costs for one or another type, such as raw materials, you need to extract from the constructed metagraph for the cost centers of continuous production of paint and varnish materials, tree formation of planned costs for raw materials, using which is easy enough to get estimates as total costs for raw materials and supplies, and costs for individual technological transitions, which comparison with actual cost data will point to bottlenecks in production. A fragment of such a tree of formation of the planned costs of raw materials (is shown in Figure 4).
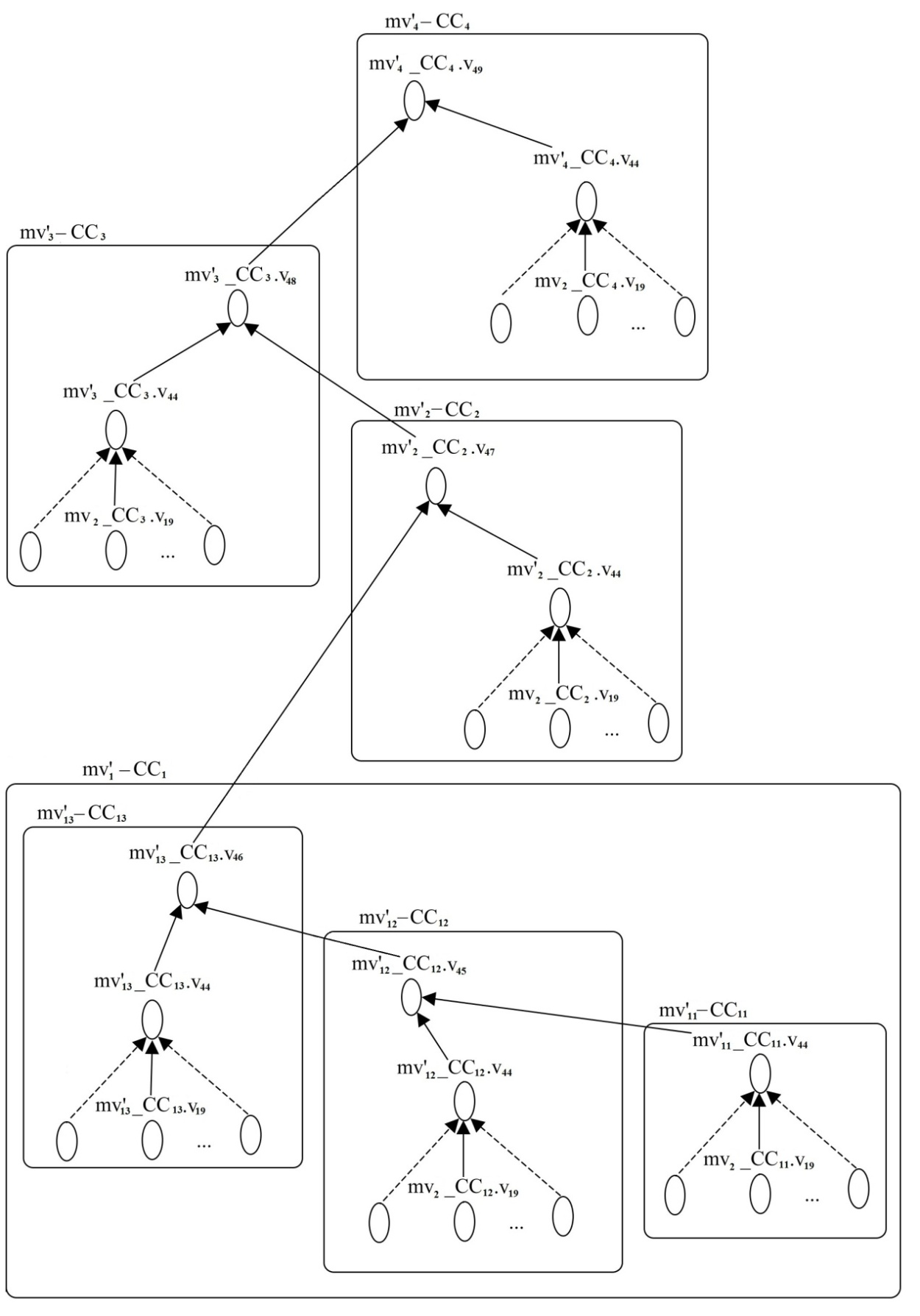
Note that the structure of operating registers used to account the actual costs of raw materials in the paint shop management system may have a similar appearance. Similarly, in the operating registers can be organized the final accounting of planned and actual costs and other types, as well as the total values of the planned direct costs associated with the implementation of a planned task. The organization of maintenance of the above registers makes it possible to solve the problem of comparing planned costs with actual costs and to obtain estimates of their discrepancies for analysis.
Conclusion
Developed new conceptual schemes of the organization of cost accounting in the process of formation by cost centres at the industrial enterprise will allow to control the process of formation and increase of expenses in the analyzed business process, and also to solve a problem of the evaluation of the general prime cost of the production, to reveal technological divisions with unreasonable expenses, to plan the requirement of the basic raw materials and materials on technological operations, to plan the requirement of energy resources, the production equipment and manufactures
Summarizing the above, we can say that the presented structural and calculated representation of the task of calculating the planned cost of production in a continuous production, including the production of paint products, is the necessary basis for the practical implementation of the PMA system at the paint company.
In the process of this study, a methodical approach was developed within the framework of the development of the methodology for organizing the system of cost analysis and cost management in complex production complexes using new business models based on the application of the process approach and methods of object-oriented design, the implementation of which involves solving the following problems:
- calculation of the planned production cost of paint products with elements of cost analysis of paint products in continuous production;
- evaluate and analyze the efficiency of the production equipment used;
- assessment and analysis of the efficiency of basic material resources used.
As part of the implementation of the task of calculating the planned cost of production offered a new structural representation of the PMA system in the form of its metagraphic model defining the set of objects of reference costs and their attributes in the representation of business processes in a hierarchical model that reflects the process of formation and accumulation of costs for technological operations. With the use of metagraphs new formalized description of the calculated component of the PMA system in relation to the tasks of calculating the planned cost of production, assessment and analysis of the efficiency of the use of production equipment and material resources with the presentation of computational procedures was proposed.
The developed metagraphic model of the planned prime cost calculation allows to carry out the differentiated account of expenses in various slices with a binding to their time, the nomenclature of let out production, technological operations, kinds of expenses, places of their occurrence that in turn gives the chance to diagnose "bottlenecks" at the paint and varnish enterprise. It is reasonable to use this metagraphic model in the tasks of cost analysis and cost management by deviations, in particular, calculation of planned direct costs by type in order to compare them with actual costs and assess the obtained deviations.
References
Borisovskiy, I., & Sukhov, G. (2012). Technology of statement of management accounting in the company. The main stages and nuances. TopS Business Integrator, 2. http://www.topsbi.ru
Drury, K. (2013). Introduction to management and production accounting. UNITI.
Etrill, P., & McLainey, E. (2012). Financial management and management accounting for managers and businessmen. Alpina Pabl.
Kalinovsky, S. A. (2013). Management accounting and analysis of the use of technological equipment. NITs INFRA-M.
Kaverina, O. D. (2015). Organization of management accounting: problems and judgments. Audit statements, 8, 1-7.
Kizilov, A. N., & Bogatii, D. V. (2015). Practical aspects of setting the management accounting and control system in commercial organizations. Accountant and Law, 2, 21-34.
Perepelitsa, V. A. (2012). Multicriterial models and methods for discrete optimization problems on graphs. LAP LAMDERT Academic Publishing.
Sidorova, M. I., & Gordeeva, E. I. (2014). Management accounting and management: issues of cross-functional interaction. International accounting, 35(329), 2-15.
Suprunova, E. A. (2013). Problems of development of management accounting in Russia at different levels of the economic system. Problems of Economics, Organization and Management in Russia and the World, 457-461.
Sychev, V. A., & Semyonicheva, M. A. (2016). Business modelling in management accounting problems in paint and varnish production. Bulletin of the South Russian State Technical University (NPI), Series: Socio-economic sciences, 3, 28-38.
Sycheva, G. I. (2011). Cost accounting methods in the tasks of industrial enterprise management. Bulletin of the South Russian State Technical University (NPI). Series: Socio-economic sciences, 3, 32-36.
Vakhrushina, M. A. (2014). Problems and Prospects for the Development of Russian Management Accounting. International accounting, 33, 12-23.
Weisfeld, M. (2014). Object-oriented thinking. Peter.
Zagidullin, R. R. (2011). Machine-building production management using MES, APS, ERP systems. Stary Oskol: TNT
Copyright information
This work is licensed under a Creative Commons Attribution-NonCommercial-NoDerivatives 4.0 International License.
About this article
Publication Date
25 September 2021
Article Doi
eBook ISBN
978-1-80296-115-7
Publisher
European Publisher
Volume
116
Print ISBN (optional)
-
Edition Number
1st Edition
Pages
1-2895
Subjects
Economics, social trends, sustainability, modern society, behavioural sciences, education
Cite this article as:
Komissarova, M. A., Storoguk, I. N., Guzenko, N. V., & Semenicheva, M. A. (2021). Formation Of A Metagraphic Model For Production Cost Accounting. In I. V. Kovalev, A. A. Voroshilova, & A. S. Budagov (Eds.), Economic and Social Trends for Sustainability of Modern Society (ICEST-II 2021), vol 116. European Proceedings of Social and Behavioural Sciences (pp. 2272-2282). European Publisher. https://doi.org/10.15405/epsbs.2021.09.02.254