Abstract
The article defines the role of training in the field of innovative management of petrochemical production. The trend in the training of specialists in primary and secondary vocational education is revealed. It is determined that the transition to" smart " production in the conditions of digitalization inevitably reduces the number of jobs in the workshops and increases the number of specialists and workers engaged in the preparation and creation of high-performance automated production. The main directions of personnel development in the transition to the digital economy are defined. Integrating human resource management into the strategic planning process allows you to create and develop the necessary skills and competencies to achieve effective results, opportunities and competitive advantages. The introduction of more efficient and faster production systems and innovative technologies allows you to reduce production processes, accelerate the entry of new products and services to the market, as well as the associated delivery times, reduce production stages and increase the ability to differentiate products. It is concluded that the restructuring of the university's activities should include the creation of a system of training specialists for the digital and innovative economy based on and taking into account the forecast of the directions of development of critical technologies, research topics within the framework of new technical tasks.
Keywords: Intelligent (smart) production, digitalization, staffing, competencies
Introduction
The issues of the transformation of the management system and personnel support in the context of the implementation of Industry 4.0 and intelligent production require a thorough analysis and identification of areas for optimizing and improving the management system of petrochemical enterprises' human resources. One of the tasks of the analysis is to assess the impact of the digital economy on the formation of the management system and staffing of domestic petrochemical enterprises.
One of the key places in the success of the process of digitalization of industry, in addition to the introduction of innovations, the implementation of sustainable development, which should be understood as interrelated elements of one whole, is occupied by personnel. Innovative and digital technologies are a powerful incentive for the creation and development of intelligent production systems, but their implementation must be carried out within the framework of a conscious innovation path.
Problem Statement
Mittal et al. (2019) conducted a structuring of various characteristics, technologies and stimulating factors associated with intelligent production, a comparative review with similar concepts as Industry 4.0, cyberphysical production systems, smart factory, advanced production; the authors also evaluate the resulting structure by comparing the characteristics and technological clusters of intelligent production with the design principles of Industry 4.0 and cyberphysical systems. Theoretical approaches to the digital transformation of the economy are revealed in the studies of (Davidenko, 2018; Shinkevich et al., 2019; Shinkevich et al., 2020a, 2020b, 2020c, 2020d). The author describes a model of organization of work on the transition to digitalization of the information services management system of a petrochemical enterprise. Recommendations are given to simplify the transition to a new look of the economy of the industrial integrated complex in the context of modern challenges. It is proved that the transition of the economy to a new technological level can increase the efficiency of production by processing a large amount of information with the construction of "smart" systems. In the study of Kravchenko (2019) proposed strategies for personnel development in order to develop new effective management tools for intelligent production systems. Fedorov et al. (2015) in their work identified the features and advantages of software platforms in intellectual production based on the knowledge and competencies of personnel. At the same time, both in foreign and domestic industry, when introducing innovations and switching to intelligent production systems, the capabilities of personnel are not fully evaluated, while highly qualified personnel are the source and tool for modernizing petrochemical production.
Research Questions
In modern conditions of digitalization of petrochemical industries, highly qualified specialists are required at all levels of management. Human resource potential is one of the most important factors in the development of a resource-saving strategy for a petrochemical enterprise, and in this regard, labor efficiency is beginning to become dominant for improving the efficiency of managing petrochemical production, despite its capital intensity.
Purpose of the Study
The aim of the research is to form an effective management system and personnel support in the conditions of innovative management of petrochemical production. As well as the creation of a solid system of knowledge expansion in the enterprise, based on the identification of skills deficiencies and the definition of training methods to address these shortcomings at the initial stage for both high and low-level specialists. For the effective operation of the enterprise, it is necessary to expand the capabilities, and above all, to involve employees in continuous improvement in order to make them universal in performing various tasks.
Research Methods
The issue of staffing and the educational component are among the key areas of the national program along with the formation of research competencies and technical reserves, regulatory regulation, information infrastructure and information security, within the framework of which, by 2024, the constantly updated human resource potential of the digital economy and the competence of citizens should be provided. In the dynamics of training of specialists in primary vocational education (skilled workers and employees), there is a tendency to reduce the number of graduates in professions in industry for 2010-2015 by 31.5%, and a decrease in the number of graduates in the specialty "Computer Science and Computer Engineering" for 2016-2019 by 19.8% (Figure 1).
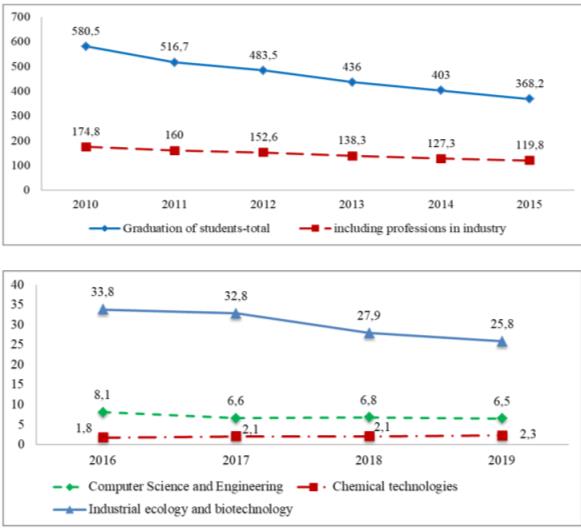
Digitalization of production processes and the introduction of information technologies is impossible without qualified personnel with all the necessary knowledge and skills to work in production facilities in the conditions of 5 and 6 technological structures. In this regard, special attention is paid in the country to the training of personnel for industry and the development of human resources in general.
This trend is associated with changes in the education system, according to which primary vocational education is equated with secondary vocational education in programs for training qualified workers (employees).
A different trend is observed in the dynamics of the output of middle-level specialists (Figure 2). So, although in 2010-2015 the total number of graduates decreased by 23.3% (from 535.7 thousand people in 2010 to 410.9 thousand people in 2015), the output in the direction of training "Computer Science and Computer Engineering" increased by 9.0%.
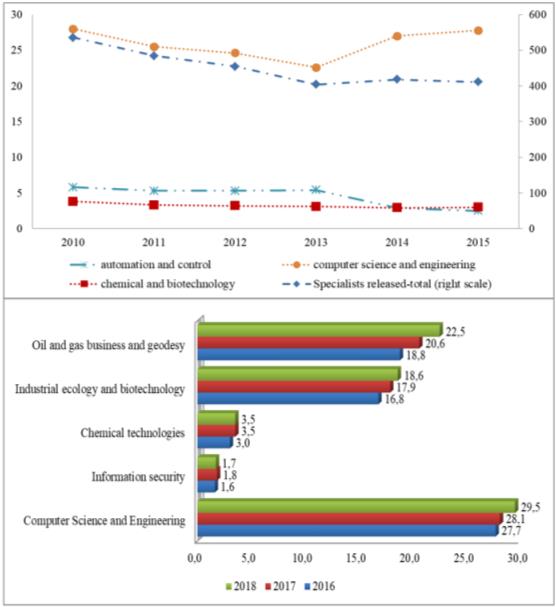
In 2016-2018, the total number of graduates increased by 13.4%, including in the areas of training "Computer Science and Computer Engineering" by 6.5%, "Chemical Technologies" – 16.7%, "Oil and Gas Business and Geodesy" – 19.7%.
The largest student output among the studied areas of training in the higher education system is observed in the profile "computer science and computer engineering" – 28.2 thousand people according to 2019 data, which is 26.5% higher than in 2010. The increase in the direction of "Chemical technologies" is insignificant and amounts to 4.3%. It should be noted that in recent years, there have been relevant areas of training in the context of digitalization "Computer and Information Sciences", the output of which is 3.1 thousand specialists, "Management in technical systems" – 11.5 thousand people.
According to the research of Shinkevich et al. (2020a), it was revealed that the transition to "smart" production in the conditions of digitalization inevitably reduces the number of jobs in the workshops and increases the number of specialists and workers engaged in the preparation and creation of high-performance automated production. At the enterprises of the petrochemical complex of the Republic of Tatarstan, against the background of an increase in the technological level of production, every fifth employee was reduced. For certain types of petrochemical production activities, the maximum reduction in the number is observed in oil and gas production enterprises and in the production of petroleum products (the rate of decline is 61-67%). About 20% of employees are released at the enterprises for the production of rubber and plastic products. The reverse situation of an increase in the number of 7.6% is observed in chemical production, which can be explained by the introduction of new production facilities.
Digitalization has an impact on production processes, productivity, and business models, defined as a system of interrelated and interdependent activities that determine the way an enterprise works with its customers, partners, and suppliers. The introduction of more efficient and faster production systems and innovative technologies allows you to reduce production processes, accelerate the entry of new products and services to the market, as well as the associated delivery times, reduce production stages and increase the ability to differentiate products.
In the context of digitalization, intelligent manufacturing covers an important part of the innovative issues identified as priority areas of development. In particular, the digitalization of enterprises focuses on new technologies, such as the Internet of things, machine learning, industrial infrastructure, big data, and additive technologies. New business models are focused on resource conservation, increasing labor productivity, and improving the environmental situation. If the principles and best practices of smart manufacturing are fully implemented, businesses will be able to maximize the synergy between digitalization and the economy. In this way, it will maximize the reuse of resources, reduce waste, save capital, recycle products, components and materials in order to increase overall sustainability and profit.
Within the framework of the federal project "Personnel for the Digital Economy", residents of Russia are given the opportunity to develop digital competencies for a successful professional future, within which they can receive a personal certificate for free training in advanced training programs on the competencies of the digital economy. So, for 2019-2020, the results showed that people of all ages and professions are ready for digital changes. More than 40% of the students are young people from 25 to 34 years old. Most of the certificate recipients planned to develop their existing career or completely change their profession – this motivation was indicated by 39% and 38% of the students, respectively. 17% wanted to increase their income level through new skills, 4% wanted to keep their current job, and only less than 1% took courses for self-development and advanced training.
Courses were provided by educational organizations - both public universities and commercial platforms-in 22 areas of the digital economy for beginners, basic and advanced students: artificial intelligence, programming, cybersecurity, big data, digital marketing, digital design, and others (Figure 3).
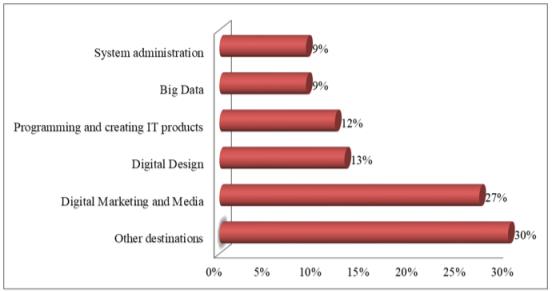
The most popular course among teachers was digital design and interactive educational technologies. Also among teachers, such programs as "Digital services and interactive environments of remote interaction in a complex sanitary and epidemiological situation", "Digital education technologies", "Digital literacy of the teacher", "Creating websites on the Tilda platform", "Digital tools and design in the professional activities of a teacher and a business coach", "Information and communication Technologies in teaching activities", "Using digital technologies in everyday life" and "Graphic Design" were in high demand.
According to Yulia Goryachkina, Deputy Director for Personnel for the Digital Economy of the Digital Economy organization, the digital certificate program is a unique collaboration of the state, universities and business to improve the digital literacy of the population and develop the competencies of the digital economy among citizens. Additional education programs help people develop skills that are in demand in the context of the unprecedented development of the IT industry with universal digitalization. Together with other initiatives of the federal project "Personnel for the Digital Economy", this will help reduce the shortage of qualified personnel in the labor market.
Findings
In order to effectively manage personnel, it is necessary to systematize the basic principles of managing the personnel subsystem of the enterprise in the conditions of digitalization of production and business processes. The principles that must be observed in the formation of a personnel management system in production during the transition to digital technologies include (Lubnina et al., 2018): compliance of personnel management functions with production goals; optimal ratio of managerial orientations; principles of progressiveness, perspective, complexity, simplicity, scientific, consistency. Compliance with the principles contributes to the creation of an effective personnel management system that allows you to function in the transition to automated production, maintain the basis of labor resources and have sufficient readiness to expand the number of high-performance jobs, which requires appropriate qualifications of employees.
The analysis of numerous studies allows us to conclude that there is a need to change the requirements for the quality and methods of obtaining education, the presence of problems in training personnel for the digital economy at the regional level, due to the inequality of access to IT technologies, different levels of training of universities, the inconsistency of standards and other regulations with the realities. In this regard, it is necessary to develop and implement directions for improving the effectiveness of training personnel that correspond to the popular professions of the digital economy (Figure 4).
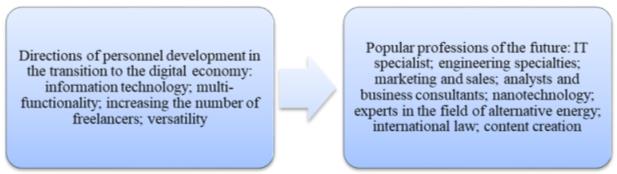
The restructuring of the university's activities should include the creation of a system of training specialists for the digital and innovative economy based on and taking into account the forecast of the directions of development of critical technologies, research topics within the framework of new technical tasks.
Conclusion
The goal of providing effective training is to implement new strategies. Processes for managing organizational development and preparing staff for the implementation of new initiatives and programs are being developed. After identifying the capabilities of employees necessary for the effective operation of the enterprise, it is possible to identify, design, develop and conduct seminars that will complement the missing skills and competencies of employees. By evaluating the skills and knowledge before and after training, you can assess the readiness of employees to implement new strategies.
Thus, in the conditions of digitalization of production, enterprises need highly qualified specialists of all levels and directions: managers, engineers, craftsmen, workers. Managers of industrial enterprises need to understand the need for continuous professional development of employees, as is done in developed countries. The received basic education cannot be considered as final, it is necessary to constantly improve knowledge and skills, to acquire new competencies. An employee of a modern industrial enterprise should have the ability to master high-tech equipment, information technologies, master related professions, and interact with representatives of foreign industries.
References
Davidenko, L. (2018). Digital transformation of the industrial complex economy. Grand Altai Research & Education, 2, 13-19.
Fedorov, A., Shkodyrev, S., & Zobnin, V. (2015). Knowledge based planning framework for intelligent distributed manufacturing systems. Lecture Notes in Computer Science, 9141, 300-307.
Kravchenko, A. (2019). Workforce training and management challenges in the contemporary smart manufacturing (SM). Economic and management issues, 4(20), 29-32.
Lubnina, A., Shinkevich, M., Yalunina, E., Gaidamashko, I., Savderova, A., & Komisarova, M. (2018). Innovative strategy for improving the efficiency of industrial enterprises management. Espacios, 39(9), 25.
Mittal, S., Khan, M., Romero, D., & Wuest, Th. (2019). Smart manufacturing: Characteristics, technologies and enabling factors. Proceedings of the Institution of Mechanical Engineers Part B Journal of Engineering Manufacture, 233(5), 1342-1361.
Russian Statistical Yearbook. (2020). Stat. sat. /Rosstat 700.
Shinkevich, A., Barsegyan, N., Dyrdonova, A., & Fomin, N. (2020a). Key directions of automation of petrochemical production. Journal of Physics: Conference Series, 1515, 022016.
Shinkevich, A., Kudryavtseva, S., & Ershova, I. (2020b). Modelling of Energy Efficiency Factors of Petro-chemical Industry International. Journal of Energy Economics and Policy, 10(3), 465-470.
Shinkevich, A., Shaimieva, E., Malysheva, T., & Gumerova, G. (2020c). Information system of decision support in the management environment of ecological project. Academy of Strategic Management Journal, 19(5), 1-11.
Shinkevich, M., Vertakova, Yu., & Galimulina, F. (2020d). Synergy of digitalization within the framework of increasing energy efficiency in manufacturing industry International. Journal of Energy Economics and Policy, 10(3), 456-464.
Shinkevich, A., Barsegyan, N., Shinkevich, M., Ostanina, S., Galimulina, F., & Nadezhdina, M. (2019). Reserves for improving the efficiency of petrochemical production on the basis of "Industry 4.0". International Scientific and Technical Conference Smart Energy Systems, 04006.
Copyright information
This work is licensed under a Creative Commons Attribution-NonCommercial-NoDerivatives 4.0 International License.
About this article
Publication Date
25 September 2021
Article Doi
eBook ISBN
978-1-80296-115-7
Publisher
European Publisher
Volume
116
Print ISBN (optional)
-
Edition Number
1st Edition
Pages
1-2895
Subjects
Economics, social trends, sustainability, modern society, behavioural sciences, education
Cite this article as:
Nurgaliev, R. (2021). Training Of Personnel In The Conditions Of Innovative Management Of Petrochemical Production. In I. V. Kovalev, A. A. Voroshilova, & A. S. Budagov (Eds.), Economic and Social Trends for Sustainability of Modern Society (ICEST-II 2021), vol 116. European Proceedings of Social and Behavioural Sciences (pp. 1801-1808). European Publisher. https://doi.org/10.15405/epsbs.2021.09.02.201