Abstract
Aluminosilicates, namely, mica crystals, are unique crystalline bodies. They are characterized by changing physical properties due to their crystal structures. The consequence of the anisotropy of forces of interatomic bonds is the ability of mica crystals to split into thin plane-parallel plates of a large area, that is, they are characterized by an extremely pronounced anisotropy of mechanical properties. The layered distribution of particles causes high thermal conductivity along the layers. Peculiar sinuous voids and channels in the interpacket zones and densified barriers of atoms between them create distinctive conditions for ions moving along the cleavage and perpendicular to it. This creates different electrical properties of mica in two main directions. Thus, the anisotropy is a property of mica. It is necessary to take into account that there are both large and small values of certain characteristics of the crystal: it is enough to change the orientation by 90°. The basis of the crystal structure of mica is a flat double silica-oxygen package. On the outside, the packages are limited by the bases of silicon-oxygen tetrahedrons. The second representative of aluminosilicates is glass industry waste which refers to amorphous bodies with short-range crystalline structures. To develop a technology for the disposal of mica and glass industry waste, a resource-saving method for rational nature management was developed and implemented. The study of optimization processes and the development of rational methods are of scientific and practical interest.
Keywords: Micaglassaluminosilicatescompositewaste-free technology
Introduction
Nowadays there is no scientifically based method aimed to dispose mica and glass waste. In this regard, it is extremely necessary to create the industrial circulation technology, that would be eco-friendly and beneficial for national economy.
Today many researchers are engaged in the study of non-waste technology of the production of aluminosilicate mica-glass composition. This production technology presupposes the use of small-sized mica and glass waste and optimization of modes for components processing.
Therefore, the study of optimization processes and the development of a rational technology are of scientific and practical interest.
Problem Statement
Micalex is a solid product. It is obtained as a result of hot pressing of powdered mica compound with finely ground low-melting glass. This type of glass is produced with addition of zinc, boron oxides and barium (Asnovich, & Zabyrina, 1979).
The history of micalex production has more than a dozen years. In 1912–1952, in England, France, and Germany, five patents were issued for micalex materials (Fedoseev, 1961).
The research of mica and glass combination was conducted by Lomonosov conducted in 1745 (as cited in Lomonosov, 1940). In Russia, the production of micalex started in 1936. Such researchers as Fedoseev (1953), Bogoroditsky and Friedberg (1948) conducted the first research works of micalex properties and structure.
The source materials as well as the technology of production determine the physical properties of this material.
The dielectric permeability of micalex is higher than that of its components due to the fact that the amorphous phase content in new combination increases. Chemical resistance is determined by mica properties. Micalex is a dielectric withstanding complex treatment without destruction (Volkov, Zagibalov, & Metzik, 1971). We studied the possibility to produce the composition consisting of more cost-effective components, which can reduce the cost and improve the electro-physical properties.
Research Questions
The following tasks were set: to develop and study the glass binder based on recycled waste from the mica and glass industries; to prove the influence of the chemical composition of mica on the wetting with a glass binder; to produce a composite material based on fiberglass aluminosilicates with high electrical and mechanical characteristics; to identify phases of new crystalline structures in the transition mica-glass layer (Liopo & Metzik, 1990).
Purpose of the Study
During the mica enrichment, muscovite and phlogopite mica of 20 mm in size are not extracted and sent to the dump, although they make up 30–40 % of the total amount of mica. Annual mica losses are tens of thousands of tons. Mica content in the dumped rock mass is 3–5 %. The absence of a science-based technology for processing small-sized mica ores requires the development of a technology for producing composite materials based on aluminosilicates. The second main component of the glass binder of composite aluminosilicate is glass industry waste.
The purpose of the article is to study the material produced from recycled raw materials, develop a processing technology of enriched industrial mica and glass waste, study the mutual penetration into the structure of aluminosilicates and changes in the crystalline structure, identify and explain the interaction of mica and glass.
Nowadays one of the most paramount challenges is the improvement of quality of life.
This parameter is crucial for the social and economic development of any country. It is included in the strategy of national security of Russia. Life quality can be improved by ensuring personal security and high living standards.
Research Methods
The authors used the works of Russian and foreign scientists, publications in periodicals, materials of scientific and practical conferences as theoretical and methodological material in this research. In addition, they used modern scientific methods in order to determine a contact angle. Methods of thermal and X-ray diffraction analysis were used as well.
Findings
In order to recycle industrial waste (glass industry waste, substandard mica raw materials), we have developed a design of a cost efficient heater. The constituent part of which is a glass binder based on waste of glass production and additives (boric acid, barium nitrate, sodium silicofluoride, potassium nitrate, and small-sized muscovite mica). Table
Table
Explosive glass destruction is explained by the volumetric stress. Then, crushed glass waste was transferred to a vibrating screen for material segregation. The accelerations varied from minimum to maximum values according to the sinusoidal law. The size of the pieces exposed to the screening process was 30 mm. The next stage was magnetic separation aimed at eliminating metallic inclusions. A magnet was used for separation. Then we mixed the waste with chemical additives (40 % glass and 60 % additives) in order to reduce the softening temperature of glass.
The interaction is a contact under the influence of heating followed by the new phases’ recrystallization through the melt. The system of mica-glass is non-uniform. It has 3 phases: solid mica, liquid – molten glass, gaseous – air. During the crushing and grinding of mica, both molecular and atomic bonds are destroyed. Under the destruction of crystals of the solid phase, many atoms are on the surface because the degree of disorder in the crystal increases. In the crystal, disorder is a result of vacancies and interstitial atoms. On the surface, disorder is a result of the atomic relief. They arise due to the fact that with an increase in the temperature, atoms are in an adsorption state. When we heat the composition of mica and glass, the liquid phase of molten glass is injected into the gaps between the crushed particles of mica as a liquid lubricant. It facilitates the mutual movement of particles and leads to structure compaction. As a result of this process, free energy of glass decreases.
In the structure consisting of melt and solid-phase inclusion, the diffusion process occurs. The accelerated ion is introduced into the crystal through its surface, a defective region is formed in the crystal and the surface relief near this region becomes distorted. Between individual particles of mica, there are processes changing the distribution function of particle size. Chemical affinity and liquid and solid phase polarity as well as enantiotropic polymorphic transformations occur due to the temperature increase. The molten glass and the smallest particles of mica enter the incongruent melt. The thin layer is stretched by the forces of molecular attraction affecting mica. A thicker layer begins to move. All the drops become involved into the movement. When the equilibrium is reached, the layer merges with the main drop. The physicochemical impact on the interface determines the nature of wetting. The contact angle changes irreversibly. Hydration of mica occurs; the molecular attraction forces of mica and glass outperform the forces of glass molecular attraction. A new aluminosilicate compound is formed.
Thermal transformations of mica and glass with additives and their mixtures occur with temperature increase. The study of pure mica revealed that its mass loss during heating is explained by the dehydroxylation which has 3 stages: the output of water adsorbed at 1200; the allocation of interlayer, molecular water at 300 and 5000; the dehydroxylation at 9000.
In muscovite, the 3rd stage of mass loss occurs in the range of 700–10000 at a maximum temperature of 9000. At 850–10000 temperatures, we observed the endo effect at a maximum temperature of 8900.
Table
Thermal transformations are typical of glass thermal destruction with releasing gaseous products. The processes are dehydration and decarbonization. The stage of congruent glass melting and liquid phase formation was identified. The thermal characteristics of the sintered glass crystal composition are presented in Table
We recorded the diffraction of pure muscovite mica and thin sections of the longitudinal and perpendicular sections of composite material in order to study the aluminoborosilicate composition using the phase analysis of x-ray.
The study of the phase composition revealed that during the structural adjustment, under the influence of a temperature of 700–750 degrees, phases of the silicate group were formed. We found 2 polytypes of muscovite 2Mi 3T in the sintered and pressed composition of glass and mica. In perpendicular section, we found microcline and distene. In longitudinal section, microcline and distin, sillimanite and mullite were found. Intensity of the peaks of new phases is different. The results obtained proved that the composition was formed at the mica-glass interface, and the aforementioned silicates were formed. The development of new phases is related to the structure of mica. Muscovite polytypic species are determined by an interlayer cation and tetrahedral and octahedral components. The predominant orientation of powder leads to a significant increase in intense basic reflexes. Mica particles are formed by pressing the cleavage plane into the reflecting position. The probability of crystallographic plane reflection of the general position is significantly reduced. As a result, the intensity of the reflexes decreases (Figure
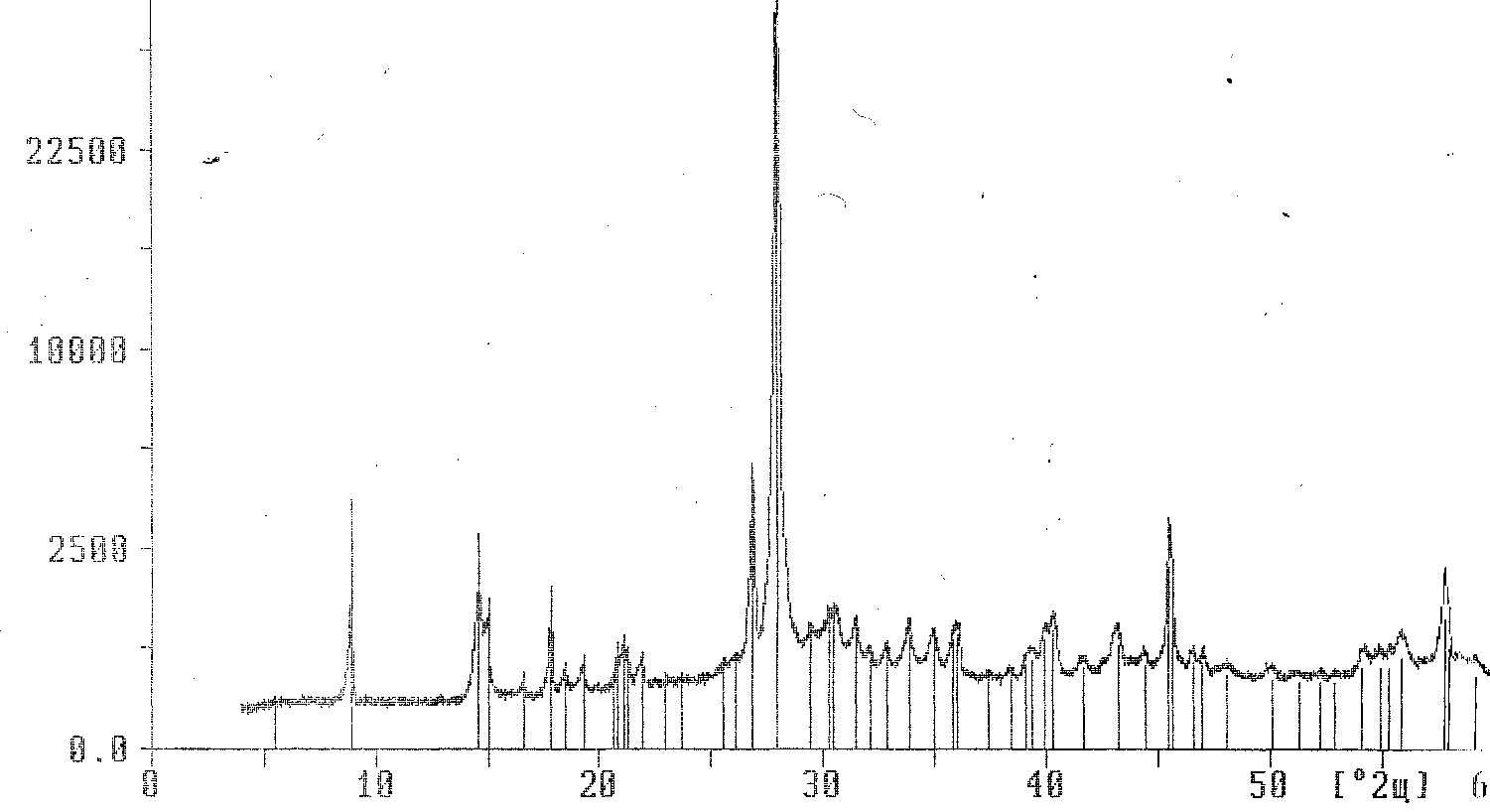
The process of the mica-glass interaction can be represented in the following way: the grains of mica are redistributed after melting. A layer of glass wetting liquid appears in between two closely spaced grains. It takes the form of a lens with a concave meniscus at the interface with the air. The forces of surface tension cause overpressure directed towards the center of curvature of the meniscus. The liquid is washed away from the contact zone by the pressure. As a result, solid grains become closer and have a denser particles’ packing and pores’ filling with glass.
However, the solid mica phase dissolves in liquid glass and, as it is saturated, the new phase crystallizes. The dissolution occurs at the contact points. There is a process of recrystallization through the melt: small crystals completely dissolve and larger crystals grow. The process of composite formation ends with the recrystallization of mica in glass and the termination of compaction. The formation of rigid frame takes place. The development of new phases is affected by pressure (300 kg/cm3) and the temperature of 750 degrees. The pressure on a heated, finely dispersed glass and mica briquette leads to plastic deformations of the crystals of mica and the entire composition. In this case, mutual redistribution of grains occurs, the contacts increase and the voids become filled. Therefore, we can observe the increase of sintered material density.
Conclusion
Thus, during the course of the research using thermography methods we determined the temperature range of releasing gaseous products (capillary water removal, dehydration, decarbonization) and the congruent melting interval which corresponds to the polymorphic transformation of the enantiotropic aluminosilicate component based on mica and glass. The use of x-ray phase analysis allowed revealing new compounds (potassium spar, sillimanite, mullite, distene and 2 muscovite polytypes).
References
- Asnovich, E. Z., & Zabyrina, K. I. (1979). Electrical insulation materials of high heat resistance. Moscow: Energy.
- Bogoroditsky, N. P., & Friedberg, N. D. (1948). Нigh-Frequency inorganic dielectrics. Moscow.
- Fedoseev, G. P. (1953). Micalex, its properties and application. Information message from the Technical Council and Technical Department of the Ministry of Building Materials Industry (p. 6). Moscow: Promstroyizdat.
- Fedoseev, G. P. (1961). Structural features of Micalex. Leningrad: Proceedings GIPRONIINEMETALLORUD.
- Liopo, V. A., & Metzik, M. S. (1990). Structural changes in mica crystals during laser irradiation. University News. Physics, 6, 21.
- Lomonosov, M. V. (1940). Collection of articles and materials. Moscow: Publ. house of the Acad. of Sci. USSR.
- Volkov, K. I., Zagibalov, P. N., & Metzik, A. I. (1971). Property, mining and mica processing. Leningrad: East Siberian book publ. house.
Copyright information
This work is licensed under a Creative Commons Attribution-NonCommercial-NoDerivatives 4.0 International License.
About this article
Publication Date
07 December 2020
Article Doi
eBook ISBN
978-1-80296-095-2
Publisher
European Publisher
Volume
96
Print ISBN (optional)
-
Edition Number
1st Edition
Pages
1-833
Subjects
Management, human resources, resource efficiency, investment, infrastructure, research and development
Cite this article as:
Fedorova, S. V. (2020). Study Of Structural Properties Of Aluminosilicate Composite. In A. S. Nechaev, V. I. Bunkovsky, G. M. Beregova, P. A. Lontsikh, & A. S. Bovkun (Eds.), Trends and Innovations in Economic Studies, Science on Baikal Session, vol 96. European Proceedings of Social and Behavioural Sciences (pp. 222-228). European Publisher. https://doi.org/10.15405/epsbs.2020.12.29