Abstract
The high level of depreciation of industrial equipment in the country, low labor productivity, and unsatisfactory export performance of Russian products necessitate the introduction of innovations. The production of high-tech products is a priority for the development of the Russian economy. Such products require additional significant costs and, as a rule, have a long cycle from the start of the study to the release of the first batch. Overhead accumulates in the process of its production. The classical methods of distribution of indirect costs significantly distort the unit cost of the product. This is due to a complex system of business processes taking place at industrial enterprises. This problem is solvable by applying a process approach to cost management. The article compares the traditional and process approaches to the allocation of costs per unit of output. An algorithm is proposed for introducing a process approach to cost management in an industrial enterprise, based on an analysis of the value chain. The characteristic of modern techniques and graphical notations for the allocation and image of processes occurring in industrial enterprises is given. The rules for the description of processes are outlined in order to correctly distribute the costs of products. Implementation of a process approach to enterprise cost management, based on ABC-costing systems and functional-cost analysis, allows you to correctly distribute overhead costs to units of products, eliminate unnecessary operations and functions at the enterprise, improve the quality of products, reduce risks production of high-tech and innovative products.
Keywords: Cost managementprocess approachproduction of innovative productsABC-costingfunctional-cost analysis
Introduction
This study is aimed at the implementation of the Federal Law from December 31, 2014 № 488-FL of the Russian Federation “On Industrial Policy in the Russian Federation” and, above all, in the formation of a high-tech, competitive industry that ensures the transition of the state economy from the export-raw type of development to the innovative type of development.
The degree of development of production of high-tech products currently largely determines the level of competitiveness of industrial enterprises and the country as a whole. High-tech products (innovative products), the production of which uses the results of research and development work corresponding to the priority areas of development of science, technology and technology of the Russian Federation (Iskoskov, 2011) are closely associated with a significant level of costs for their production. This fact necessitates increasing control over the level of costs throughout the production cycle of products (works, services), improving and expanding the methods and tools used to manage costs. Proper management of innovation costs, taking into account the particular development of industries, will reduce the risks of innovation; improve the competitiveness of domestic enterprises. The main tool for managing costs at an industrial enterprise is a competent system of accounting and distribution of costs by type of product. In traditional approaches to cost management, the distribution of indirect (overhead costs) per unit of output has not been resolved. At large industrial enterprises around the world, a cost-management methodology based on process-oriented accounting is currently becoming more widespread (Duran & Afonso, 2019; Kaiser, 2019).
The essence of the process approach to cost management is that the product is considered as a complex of interrelated processes (functions) in terms of: utility, efficiency, necessity, etc. The costs of the enterprise are distributed by function, process, and then by type of product according to the principle of involvement.
This approach is based on the Activity-Based Costing method. In the United States, this method became widespread in the 1980s thanks to the work of Johnson (1988), Kaplan (1988). By the 1990s, this method was used by about 10% of large companies, including in the USA, Great Britain, continental Europe and Australia. (Tibor, Schultz, Menaker, Weber, & Young, 2017). This method is also widely used in Japan. It has become so widespread due to the possibility of its application not only in industrial, but also in trade and service enterprises (Tsai & Jhong, 2019). It formed the basis of the material flow management method (Yagi & Kokubu, 2018).
In Russia, a partially similar method, a functional-cost analysis (hereinafter referred to as FCA), has developed almost simultaneously in parallel. This method fits perfectly into the concept of process cost management in industrial enterprises, in particular in the production of innovative products. It allows you to:
Increase the number of functions and usefulness of an innovative product, improve its quality;
Identify the correspondence between the significance of the function performed by the product and the costs of its creation;
Eliminate unnecessary functions, therefore, operations or individual processes;
Rationally and cost-effectively set the selling price for this product, taking into account the functions included in it;
Activate the creative thinking of the team;
Upgrade production technologies;
Increase the competitiveness of products and the enterprise as a whole.
The use of functional-cost analysis is aimed at minimizing costs at the stages of design, production and operation of the product. Practice shows that companies using this method of analysis were able to reduce production costs by 20-25% (ISO 9000, 2017).
The result of the FCA should be to reduce costs per unit of beneficial effect, which is achieved: cost reduction while improving consumer properties of products; improving product quality while maintaining the level of costs; cost reduction while maintaining the level of quality; cost reduction with a reasonable reduction in technical parameters to their functionally necessary level.
Problem Statement
Traditional approaches to cost management in industrial enterprises have ceased to meet modern requirements. This happened because the share of overhead costs has changed. At the time of Henry Ford, it was interest, and now it can exceed half the cost. Both in the distribution of direct and indirect costs, and when applying the direct costing methodology, the unit cost indicators will be distorted. This does not allow correctly justifying the cost of the final product and establishing competitive prices in the market.
Research Questions
To solve the main tasks of management accounting - cost accounting and costing - a simple division of costs into fixed and variable, direct and indirect is no longer enough. The experience of recent decades shows that the standards being developed for integrated planning and enterprise management (MRPII, ERP, CSRP, etc.) are becoming more and more process-oriented. The ultimate goal is to synchronize the activities of the enterprise with the needs of the consumer, which ensures the competitiveness of the enterprise.
The main difference between the process approach to cost management is the accumulation of production overhead costs not in areas (divisions), but in processes (operations), with subsequent allocation by types of products (Figure
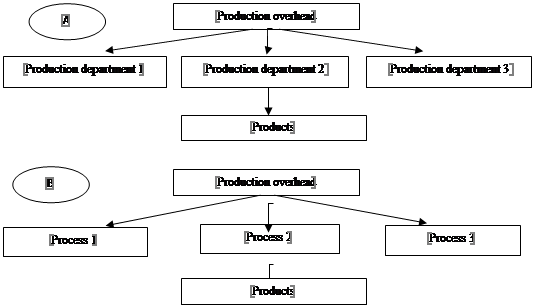
Source: author.
allocation of processes.
According to the tasks to be solved, according to the role in the organization’s activities, processes can be classified as follows (Rother, Shook, Womack, & Jones, 1999):
Key processes are distinguished as functionally closed tasks relating to the entire chain and subprocesses, which can be correlated with specific cost centers.
Different approaches (methods) are used to distinguish processes:
A functional approach involves the allocation of business processes based on the functions performed by departments (Almeida & Cunha, 2017);
Product approach - based on the results of processes (goods and services that the organization produces) (Repin, 2013);
The approach based on the analysis of value chains (Repin, 2013);
Matrix approach: a business process model is a matrix, each element of which is a separate business process, which reflects the subsystems and stages of the life cycle of the manufactured product. (Khlebnikov, Yatsyna, & Savushkin, 2019).
Due to the fact that in Russia the process approach to cost management and the enterprise as a whole is not widespread, the methods considered are not developed. There are no practical guidelines for their use.
Purpose of the Study
The ongoing study is to develop recommendations aimed at:
Research Methods
The research used methods of strategic and innovative analysis, techniques and tools of economic, design and logical analysis. The theoretical basis of the study was the work of domestic and foreign authors in the field of industrial enterprise management, cost management and other areas related to the production and sale of innovative products. The study examined the standards of integrated planning and enterprise management (MRPII, ERP, CSRP, etc.). The methodologies of functional modeling IDEF0, ARIS, graphic notations VAD, Visio, etc., used to formalize and describe business processes are used.
Findings
In our opinion, the approach based on the analysis of the value chain is more in tune with the needs of the market and the conditions in which enterprises operate. Analysis of the value chain allows you to identify bottlenecks in the enterprise, eliminate processes that do not bring value, optimize the duration of processes, build maps of value stream, etc. This approach is reflected in the work of Repin (2013), Rother et al. (1999) and others. To apply this approach, there are not enough practical recommendations for its use in industrial enterprises.
The algorithm for implementing the process approach to cost management in the enterprise, based on the analysis of the value chain, is as follows:
Present the activities of the enterprise in the form of input-output models;
Identify the processes (main, auxiliary, management and development processes), based on the results (outputs);
Substantiate the sequence of processes and individual functions;
Optimize the value chain, excluding unnecessary operations and functions;
Calculate the cost of individual processes;
Attribute the cost of the processes to the result as a whole and the unit of output.
The results of the organization’s activities are nothing but the outputs of the main business processes.
The main business processes should be represented as a value chain, highlighting the main stages of creating results. It is important to start at the end of the chain: from the result provided to the consumer. Results can be created by one or different value chains, while chains at different stages can be combined and disconnected.
Different notations can be used to describe value chains. IDEF0 is quite suitable. There is no need to list and display on the model absolutely all the inputs and outputs, as is often done: the model is too cumbersome. At the initial stage, it is important to fix the main processes, their outputs and participating units. There is a special notation in the ARIS methodology - VAD chain (value added chain).
This way of describing the main business processes is fully consistent with the construction of value flows in the concept of lean manufacturing (Rother, Shook, Womack, & Jones, 1999). The symbiosis of lean manufacturing and a process approach to cost management currently fully meets the need of modern industrial enterprises to improve their competitiveness and products.
An example of a value chain using the example of an industrial enterprise producing innovative products is presented in Figure
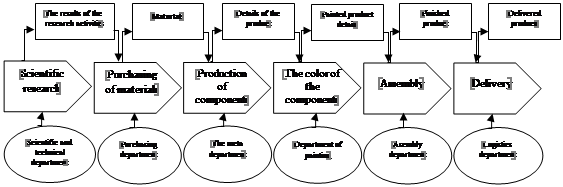
Source: author.
The same value chain created in Business Studio 4.0 using the IDEF0 notation may look like this (Figure

Source: authors
What graphic notation to use for an industrial enterprise is an individual choice of each company. Software products are similar in functionality. The ARIS model is more expensive and complex. To a greater extent, the choice of program is determined by the skills and preferences of specialists who will design business processes in the enterprise.
When describing a business process, it must be indicated: the name of the business process; stages of the business process; business process inputs; business process exits; Performer - structural units of the organization, individual employees, external performers; regulatory, organizational and administrative and methodological documents; process owner the duration of the stages of the business process. When describing processes, in order to correctly distribute the costs of products, the following rules must be observed:
Rule 1. Do not use process diagrams of other enterprises. The process model is always individual.
Rule 2. The main processes should be no more than 7 ± 2. This figure comes from the fact that the top leader, like any person, cannot effectively manage and perceive information from more main areas of activity.
Rule 3. When identifying processes, it is necessary to appoint persons responsible for their effectiveness.
Rule 4. It is necessary to document the authority of the process manager.
Rule 5. Fix a cost driver for each process.
Conclusion
The advantages of the process management of costs for the production of innovative products are the following aspects:
The costs of production are summed up not from the costs of individual units for the reporting period, but from the costs of processes that are directly related to the production of a particular product. This allows you to justify the distribution of overhead costs per unit of output;
The costs of the process are compared with its results and the value of additional functions;
The accumulation of costs for the processes allows you to correctly calculate the final cost of the product, even if its production cycle exceeds the tax-reporting period. For high-tech and innovative products, this is extremely important.
Proper distribution of overhead allows you to improve the accuracy of calculating the cost of a unit of production, therefore, justify pricing and develop marketing systems. This will enhance the competitiveness of domestic enterprises producing innovative products.
References
- Almeida, A., & Cunha, J. (2017). The implementation of an Activity-Based Costing (ABC) system in a manufacturing company. Procedia Manufacturing, 13, 932-939.
- Duran, O., & Afonso, P. S. L. P. (2019). An activity based costing decision model for life cycle economic assessment in spare parts logistic management. International Journal of Production Economics. Retrieved from https://www.sciencedirect.com/science/article/abs/pii/S0925527319303196 Accessed: 11.12.2019.
- Iskoskov, М. О. (2011). Problems of control costs and methods of reduction in the innovation economy. Kazan Science, 9, 60-64. [in Rus.].
- ISO 9000. (2007). Quality management principles and guidelines on their application. Retrieved from https://docplayer.net/9314898-Iso-9000-quality-management-principles-and-guidelines-on-their-application.html Accessed: 11.11.2019.
- Johnson, T. (1988). Activity-based information: A blueprint for world class management accounting. Journal of Management Accounting, 23-30. Retrieved from https://maaw.info/Article Summaries/ArtSumJohnson88.htm Accessed: 11.11.2019.
- Kaiser, M. J. (2019). Decommissioning forecasting and operating cost estimation. Cambridge, M.A.: Gulf Professional Publishing.
- Kaplan, R. (1988). One cost system isn’t enough. Harvard Business Review. Retrieved from https://hbr.org/1988/01/one-cost-system-isnt-enough&cm_sp=Article-_-Links-_-Top%20of%20Page%20Recirculation Accessed: 11.12.2019.
- Khlebnikov, D., Yatsyna, A., & Savushkin, L. (2019). Matrix model of the enterprise. Quality.Eup. Retrieved from https://quality.eup.ru/MATERIALY6/matrixmodel.html Accessed: 11.12.2019. [in Rus.].
- Repin, V. V. (2013). Business processes. Modeling, implementation, management. Moscow: Mann, Ivanov and Ferber. [in Rus.].
- Rother, M., Shook, J., Womack, J., & Jones, D. (1999). Learning to see: Value stream mapping to add value and eliminate MUDA. Cambridge, M.A.: Lean Enterprise Institute.
- The Federal Law from December 31, 2014 № 488-FL “On the Industrial Policy of the Russian Federation”. Retrieved from http://www.consultant.ru/document/cons_doc_LAW_173119/ Accessed: 11.11.2019.
- Tibor, L. C., Schultz, S. R., Menaker, R., Weber, B. D., & Young, P. M. (2017). Improving efficiency using time-driven activity - basedcosting. Journal of the American College of Radiology, 14(3), 353-358. DOI: 10.1016/j.jacr.2016.11.014
- Tsai, W. H., & Jhong, S. Y. (2019). Production decision model with carbon tax for the knitted footwear industry under activity-based costing. Journal of Cleaner Production, 207, 1150-1162.
- Yagi, M., & Kokubu, K. (2018). Corporate material flow management in Thailand: The way to material flow cost. Journal of Cleaner Production, 198, 763-775.
Copyright information
This work is licensed under a Creative Commons Attribution-NonCommercial-NoDerivatives 4.0 International License.
About this article
Publication Date
01 April 2020
Article Doi
eBook ISBN
978-1-80296-081-5
Publisher
European Publisher
Volume
82
Print ISBN (optional)
-
Edition Number
1st Edition
Pages
1-1004
Subjects
Business, innovation, management, management techniques, development studies
Cite this article as:
Naugolnova, I. A. (2020). The Process Approach To Managing The Cost Of Manufacturing Innovative High-Tech Products. In V. V. Mantulenko (Ed.), Problems of Enterprise Development: Theory and Practice, vol 82. European Proceedings of Social and Behavioural Sciences (pp. 554-561). European Publisher. https://doi.org/10.15405/epsbs.2020.04.71