Abstract
Global economic development and the influence of political factors lead to the fact that production systems in their development need to reach a new level. One of the options to improve production efficiency is the use of the concept of lean production for which it is necessary to develop an appropriate methodological apparatus for the use of lean production in the enterprise. In today's reality, the introduction of lean manufacturing principles is becoming one of the main ways to improve the competitiveness of business. Abroad, this philosophy is developed and applied for more than a hundred years. The concept helps companies to develop harmoniously in all directions, providing an appropriate level of quality and services, while reducing costs and satisfying their employees working conditions. In Russia, an increasing number of organizations set themselves the task of reducing costs in accordance with international quality standards of products and services. The solution of these problems is increasingly seen by enterprises in the application of the concept of lean production, but a simple repetition of the experience of other organizations will not bring results. The application of lean production concept at Russian industrial enterprises is a disordered, chaotic process. To solve this problem, the authors propose a method of accounting for the impact of losses in one business process on the occurrence in another, which will determine the priority of solving problems, as well as the feasibility of using certain tools of lean production in this business process.
Keywords: Lean productionlossesbusiness processalgorithm lean productionbusiness process
Introduction
Large-scale foreign experience in the use of the concept of lean production has many examples of the use of the concept. Enterprises in Europe (50%), Japan (90%), USA (60%), Canada, Mexico, Australia have introduced lean manufacturing, which helps them to develop harmoniously in all directions, providing an appropriate level of quality and services, while reducing costs and satisfying their employees working conditions.
In Russia, an increasing number of organizations set themselves the task of reducing costs in accordance with international quality standards of products and services (Belysh, 2018). The solution of these problems is increasingly seen by enterprises in the application of the concept of lean production. The introduction of lean production in the Russian and foreign companies leads to lower costs up to 20-40%, to improve the quality of products up to 40%, increasing productivity up to 25%, the profit increase to 15-20%, to reduce the time of execution of orders up to 80% to the turnover increase to 16-20%, freeing up production space in two times. Nevertheless, positive international experience is not the key to the success of Russian companies (Gaisina et al., 2019).
Problem Statement
The lean production at Russian industrial enterprises is a disordered, chaotic process. The general system of knowledge and values of the concept are not formed, there is no understanding of the lean production philosophy. Enterprises grab all the lean production tools, not taking into account that in some business processes the use of these tools is impossible, or will not lead to anything.
At some Russian enterprises, researchers identify objective organizational and methodological problems of implementation and adaptation of lean production to the peculiarities of doing business in Russia, as well as to the specifics of some enterprises, especially oilfield services:
1. Lack of experience in the application of the concept in the service enterprises having a production process. Lean production is successfully applied at the enterprises of mechanical engineering, automotive industry (if we consider together – about 40 %), i.e. on those on the basis of which the philosophy of lean production was built by G. Ford himself. Accordingly, the main part of the concept tools are aimed at solving problems of mass production. Later, lean manufacturing became possible to use services in enterprises through the use of Kaizen philosophy. As for the oil and fuel industry, the percentage of application is not more than 3%, and that too only in manufacturing plants (Chernova & Ageev, 2016).
2. Do not explore the feasibility of applying this concept in every business process (Kazantseva, 2014).
3. Do not identify the dependence and impact of losses in different business processes on each other.
As a rule, this leads to the fact that the desired effect is not achieved, and companies abandon the idea of lean production.
Research Questions
The main research questions are:
To determine the feasibility of applying the concept in a particular business process, analyze business processes;
To identify losses of production processes;
To developed an assessment concept for the impact of losses on each other.
Purpose of the Study
This study is aimed at development of an algorithm of a roadmap construction for optimizing losses. To optimize production processes, it is necessary to identify the losses of each business process, to determine the impact of these losses on each other. This will enable to choose the right tools of the concept and improve the efficiency of the company.
Research Methods
-
At the first stage all business processes existing at the enterprise are analyzed, the purposes of each process are formulated, the necessity of introduction of the concept of lean production is defined and if Yes, these prerequisites are divided into the main and auxiliary (Maslov, 2015).
-
The second stage is that in each business process it is necessary to investigate for the presence of the proposed losses and find the relationship between them.
-
The task of the third stage was to determine the mutual impact of losses of one business process on the losses of another. For this purpose, the authors propose to use a binary matrix (Figure
01 ).
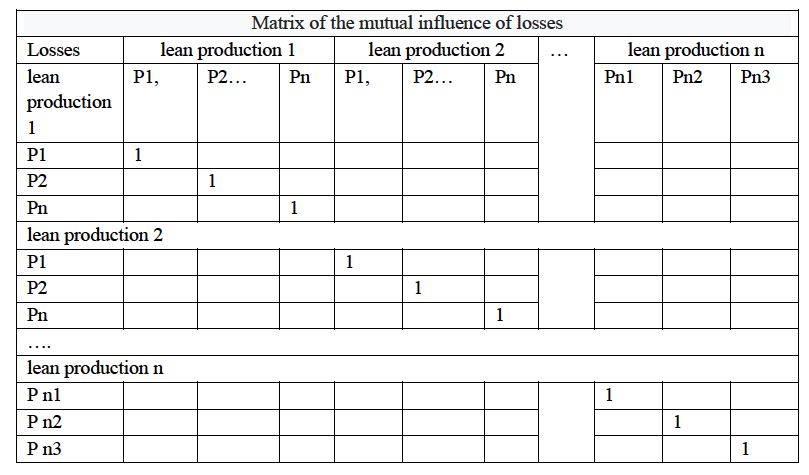
-
After identifying the losses in each business process and the relationship with other losses, it is necessary to form a ranked list of losses by the degree of their influence on the entire process, namely the universal indicator of lean production efficiency – time, and make a chain of losses (Ministry of Economic Development, 2015).
-
At the third stage, it is necessary to choose tools that can be used to eliminate the identified losses. After the application of lean production tools, the authors propose to identify the main KPIs for each business process and conduct a comparative assessment of the "Before"and "After" (Rudov, Khairullina, Gareev, Koltunov, & Skifskaja, 2017).
-
After the introduction of the concept, already at the strategic level, a long-term plan for the enterprise development is worked out taking into account new ideas (Shibanov, 2019).
Findings
The research results include:
The development of an algorithm for determining the mutual impact of losses on each business process: creation of chains of losses, ranking them by the degree of their influence on the final effect (Figure
02 ).A binary matrix is formed for determining the dependence of losses on various business processes (Figure
02 ).The scheme of the concept application is offered taking into account the carried-out actions.
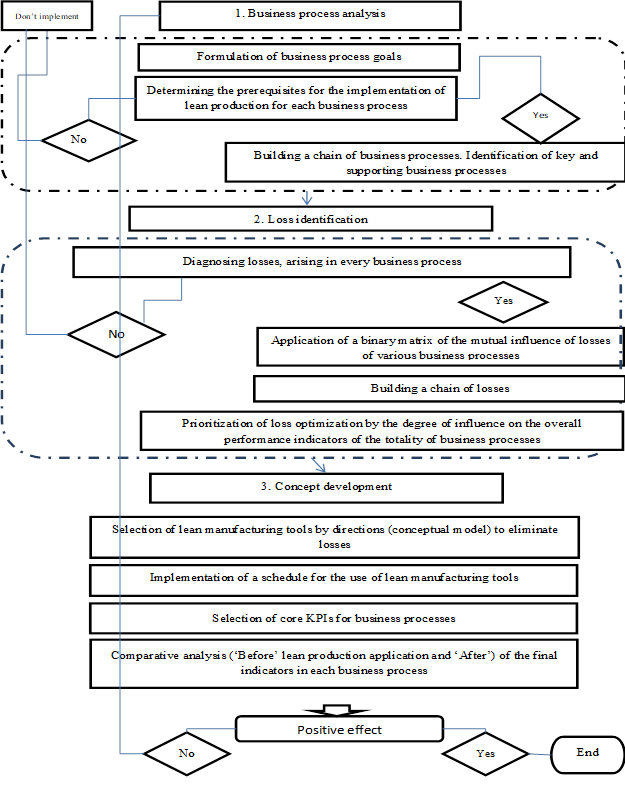
Conclusion
Taking as a basis that the concept of lean production has improved the company's activities, competently integrated into the business processes that really needed it, allowed to eliminate losses, as well as to avoid the emergence of new ones, the author proposes to extend his successful experience to all suppliers and customers of the company to avoid losses from the outside (Shiyanova, Valitova, Munasypov, Kayashev, & Hardina,2014).
This mechanism will make it possible to properly integrate the philosophy of lean production into the business processes of enterprises, taking into account the policy of Russian companies, the features of service companies with the production process (Vanchukhina, Leybert, Khalikova, & Luneva, 2018). Taking into account all the difficulties associated with the effective implementation of the concept, the author proposes an algorithm for determining the mutual impact of losses on each business process, which includes: the creation of loss chains, ranking them according to the degree of influence on the final effect. This will determine the business processes where it is necessary to implement lean production and will make it effective.
References
- Belysh, K. V. (2018). Multipurpose approach to implementation and evaluation the efficiency of the projects on lean production in industrial enterprises. Issues of Innovative Economy, 8(3), 513-530. DOI: 10.18334/vinec.8.3.39364 [in Rus.].
- Chernova, V. A., & Ageev, I. T. (2016). The concept of lean production: Steady reduction of losses. Young Scientist, 26(130), 407-410. [in Rus.].
- Gaisina, L. M., Burhanova, F. B., Minakov, P. A., Yaminova, S. A., Rakhimkulova, L. A., & Gainanova, A. G. (2019). Quality management system of social policy on students' healthy lifestyle in Russia. Espacios, 40(17), 18.
- Kazantseva, S. M. (2014). Problems related to the implementation of lean production within the Russian enterprises. Creative Economy, 12(96), 90-98. [in Rus.].
- Maslov, A. Y. (2015). Formation of the mechanism of modernization of production at industrial enterprises: PhD theses. Nizhny Novgorod: Nizhny Novgorod State University named after N.I. Lobachevsky. [in Rus.].
- Ministry of Economic Development (2015). Monitoring "On the current situation in the economy of the Russian Federation in January-October 2015". Retrieved from http://economy.gov.ru/minec/activity /sections/macro/monitoring/2015261106 Accessed: 28.09.2019. [in Rus.].
- Rudov, S. V., Khairullina, N., Gareev, E. S., Koltunov, A. L., & Skifskaja, A. L. (2017). Labor motivation management in the oil and gas sector enterprise: A sociological approach. Quality – Access to Success, 18(156), 119-124.
- Shibanov, K. S. (2019). Lean production: Continuous flow and pulling systems. Colloquium-Journal, 2(26), 41-43. [in Rus.].
- Shiyanova, N. I., Valitova, E. G., Munasypov, R. A., Kayashev, A. I., & Hardina, A. E. (2014). Quality assessment system for milk acceptance and a mathematical model of dairy produce drying. Automation and Remote Control, 75(4), 767-772. DOI: 10.1134/S000511791404016X
- Vanchukhina, L. I., Leybert, T. B., Khalikova, E. A., & Luneva, N. N. (2018). Modern approaches to operational planning in oil refinery using the PIMS software product. Quality – Access to Success, 19(S2), 123-129.
Copyright information
This work is licensed under a Creative Commons Attribution-NonCommercial-NoDerivatives 4.0 International License.
About this article
Publication Date
01 April 2020
Article Doi
eBook ISBN
978-1-80296-081-5
Publisher
European Publisher
Volume
82
Print ISBN (optional)
-
Edition Number
1st Edition
Pages
1-1004
Subjects
Business, innovation, management, management techniques, development studies
Cite this article as:
Akchurina, A. M., Battalova, A. A., & Battalov, A. M. (2020). Algorithm Of The Road Map Construction For Losses Optimization. In V. V. Mantulenko (Ed.), Problems of Enterprise Development: Theory and Practice, vol 82. European Proceedings of Social and Behavioural Sciences (pp. 40-44). European Publisher. https://doi.org/10.15405/epsbs.2020.04.6