Abstract
This study describes the hardness testing of two composite materials with the same fillers, namely ganodermaboninense mushroom particles (with variations in volume and particle size). This mushroomcan cause rot at the base of oil palm tree so that it can damage the oil palm tree. Matrix used as adhesive are polyester resin and epoxy resin. Mushrooms soaked with alkali (NaOH) for 1 hour to remove dirt and sap which will reduce the bond between the matrix and particles, after that heat it in oven at temperature of 60 degrees Celsius for 12 hours to remove the water content.Then the mushrooms are made into particles using a blender at rotation of 28000 rpm and sieved with mesh of 20, 30, 40, and 50. A mixture of mushroom particles and matrix stirred and poured into a glass mold. After 24 hours the mold can be opened and the specimen has been formed. The test results showed composites with variations of mushroom volume and epoxy resin matrixis harder than polyester resin matrix with a percentage between 23.25% to 64.51%.Whereas with variations in particle size, composites with epoxy resin matrix are also still harder with a percentage between 9.2% and 22.85%. Even so the difference in hardness is not too significant because the unit of hardness is microvickers. The test results were also found that addition more than 5% of ganoderma mushrooms will decreasecomposite hardness. While the variation of mesh filler composites is almost not shows differences in the value of hardness.
Keywords: Hardnesscompositeganoderma boninensematrix
Introduction
As so far, industrial world still uses synthetic fibers as reinforcement of composite materials. Synthetic fibers are used for manufacture of various products such as aircraft, ship hulls, wind turbine blades, cars, and others. Of various types of fiber, fiber glass is the most widely used synthetic fiber.
But this synthesis fiber has several disadvantages such as expensive, cannot decompose naturally, limited in the number, and dangerous for health such as increase the risk of lung cancer. The size of glass fibers varies and the smaller and unseen can inhale and enter into the body, while larger particles can cause irritation to skin, eyes, nose and throat.
Many researchers have sought to find substitute for synthetic fibers from natural sources which have several advantages such as easy to obtain, can biodegrade naturally, not harmful to health, available in large quantities and cheap.
Green-based polymer products such as agricultural crops are the basis for forming products that are economical, efficient, sustainable, and compete with synthetic materials ( Mawardi, Suryanto, & Sudewi, 2019).
Natural fibers can be grouped based on the source that is derived from plants, animals or minerals. Plant fiber consists of cellulose, while animal fibers (hair, silk, and wool) consist of proteins. Plant fibers include tree bark fibers (or fine sclerenkima or stem), leaves or hard fibers, seeds, fruit, wood, wheat, and other grass fibers. Many of these natural fibers have been developed as reinforcement in composite materials. Natural fiber composite materials have increased use because the price is relatively cheap, able to be recycled and can compete well based on the strength per weight of the material.
Fiber derived from plants, generally grouped into 2, namely non-wood fiber and wood fiber. Non-wood fibers are divided into ( Mawardi et al., 2019):
Straw, for example: corn, wheat, and rice.
Bark, for example: kenaf (Hibiscus cannabicus), flax (Linumusitatissimum), jute (Corchorus), flax (Boehmeiranivea), and hemp (Cannabis sativa)
Leaves, for example: sisal (Agave sisalana), pineapple leaves (Ananascomosus), and henequen fiber (Agave fourcroydes)
Fiber grass / grass, for example: bamboo fiber, grass, rattan, switch grass (Panicum virgatum), and elephant grass (Erianthuselephantinus).
In this study, the natural fiber used was derived from ganodermaboninensemushroom.This type was chosen because this mushroom can cause Base Stem Rot disease which is a serious disease that attacks oil palm plantations. Please refer to Figure
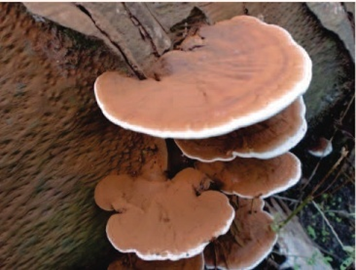
More research has been done on natural fiber composites, such describes hereunder. Astuti ( 2013) examined the effect of kapok banana fiber thickness on the mechanical properties of natural fiberpolyster composite materials. She found that maximum composite compressive strength is 12.92 N/mm2 on fiber addition with a fiber thickness of 0.70 mm while the composite tensile strength reaches a maximum point of 2.53 N/mm2 in fibers addition with a thickness of 0.82 mm.
Al Mosawi ( 2012) has been examined the incorporation of pelem tree synthetic fiber and kevlar synthetic fiber with a percentage of fiber weight of 0, 20. 40. and 60% and tested for impact, hardness, tensile, and flexural strength.
Diharjo and Nuri ( 2006) examined the effect of alkali treatment on composite tensile properties reinforced by continuous hemp fiber with a polistermatrix.The results showed that composite tensile strength and strain had optimum values for 2-hour fiber treatment, namely 190.27 Mpa and 0.44%. Fiber-reinforced composites subjected to 6-hour treatment have the lowest strength. Cross section of composite fiber reinforced treatment subjected to 0.2 and 4 hourstreatment was classified as slitingin multiple area fracture type. In contrast, cross section of 6-hours fiber-reinforced composite fracture was classified as single fracture type.
Agus and Sri Mulyo ( 2018) examined the banana tree midrib fiber. As a result of fiber boiling, changes occur in the microstructure, and the longer it is boiled, the higher the fiber diameter. In the treatment of polyester resin, the longer the boiling, value of fiber density to resin is lower, so that the fiber is not compatible with polyester resin.
Problem Statement
The problems statement is researchers want to study comparison of hardness of natural fiber composites using ganodermaboninensemushroomas a filler with a matrix of polyester resin and epoxy resin.
Research Questions
The research questions is as follow:
Which hardness value is higher between the composite of ganodermaboninensemushroomand epoxy resin or polyester resin matrix and how much the percentage?
What is the effect of adding composite fillers to hardness.
Purpose of the Study
The purpose of this study is to compare hardness of ganodermaboninense mushroom composite with polyester resin and epoxy resin matrix, and study the effect of adding composite fillers to hardness.
Research Methods
The method for making specimens can be seen as below:
Ganoderma mushrooms are cut and washed with water, then soaked in NaOH 5% (alkali) solution for 1 hour to remove sap and dirt which can reduce the bond between matrix and filler
After soaking in alkali then the mushrooms are put in the oven for 12 hours to remove the water content.
After the mushrooms are dried, then blend and sieve with mesh 20,30,40,50, and the volume is measured as desired to be used to make specimens. Volume comparison can be seen as follows:
Filler 5% and matrix 95%.
Filler 10% and matrix 90%.
Filler 15% and matrix 85%.
Filler 20% and matrix 80%.
The matrix used is polyester resin and epoxy resin
Filler and polyester resin BQTN 157 EX which has been mixed with hardener are stirred evenly then poured into the mold. Please refer to Figure
02 for specimen of hardness test.
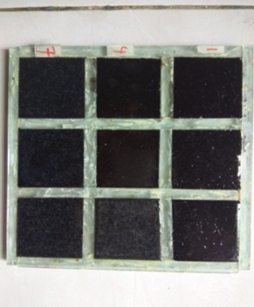
-
Allow the specimen to harden for 24 hours, after which the mold is opened and the specimen has been formed.
-
After that, the hardness was tested with a Micro Vickers FM 800 device. Please refer to Figure
03 for Microvikers FM 800 for hardness test.
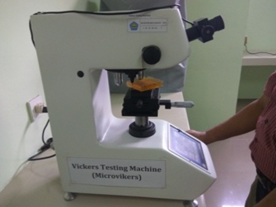
Findings
Variation of Filler Volume
Hardness test showed that with polyester resin matrix,the highest hardness is 0.93 MV for composites with a filler volume of 5%. Addition of composite filler volume to 10% and 15% reduce hardness to 0.8 MV and 0.6 MVrespectively. The lowest hardness value was found in volume 20% which is 0.43 MV. This shows that the more addition of filler in the composite causes a decrease in hardness. Table
The result of hardness test with epoxy resin matrix shows that the highest hardness is 1.53 MV for composites with particle volume of 5%. Addition of composite filler volume to 10% and 15% reduce hardness to 1.2 MV and 0.6 MV, respectively. The lowest hardness value was found in the volume of 20% which is 0, 53 MV. This shows that the more addition of ganoderma mushrooms in composites causes a decrease in hardness.The test results also showed composites with epoxy resin matrix is harder than polyester resin with a percentage of 23.25% to 64.51%.
Variation of Particle Mesh
The test show that variation of composites mesh filler almost not indicate differences in the value of hardness. The hardness value is between 0.7 MV and 0.76 M. Table
The test results show that variation of composites mesh filler does not show a significant difference for the hardness value. The hardness value is between 0.83 MV and 0.86 MV.While for mesh variation, composite with epoxy resin was still harder than polyester resin with a percentage of 9.2% to 22.85%. Figure
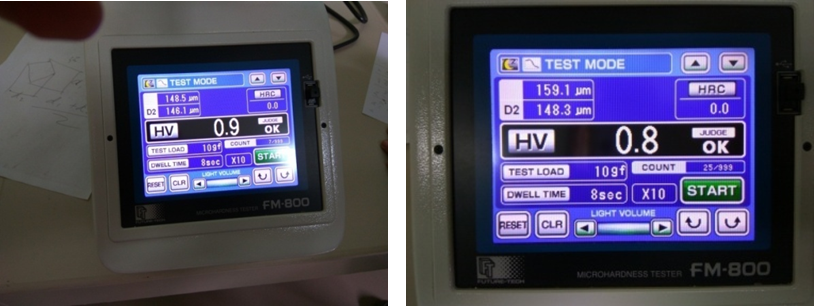
Conclusion
-
Hardness test showed that addition of ganoderma mushrooms above 5% caused a decrease in composite hardness.
The test results also showed composite hardness with volume filler variation using epoxy resin matrix is harder than polyester resin with a percentage of 23.25% to 64.51%.While the mesh variation showed that composite with epoxy resin was still harder than polyester resin with a percentage of 9.2% to 22.85%.
The test results showed that variation of mesh composite particles does not show a significant difference in the value of hardness.
Acknowledgments
The author would like to thank to the Directorate of Research and Community Service, Directorate General of Research and Development Strengthening at the Ministry of Research, Technology, and Higher Education, Indonesia, for funding assistance to this research.
References
- Agus, A., & Sri Mulyo, B. R. (2018). Kompatibilitas Serat Pelepah Pohon Pisang Kepok (Musaceae) Pada Perlakuan Perebusan Air Jahe (Zingiber Officinale) Dan Perlakuan Resin Polyester. Momentum, 13(2), 84-89.
- Al Mosawi (2012). Mechanical Properties of Plants - Synthetic Hybrid Fibers Composites. Research Journal of Engineering Sciences, 1(3), 22-25.
- Astuti (2013). Pengaruh Ketebalan Serat Pelepah Pisang Kepok (Musa Paradisiaca) Terhadap Sifat Mekanik Material Komposit Poliester Serat Alam. Jurnal Ilmiah.
- Diharjo, K., & Nuri, S. H. (2006). StudiSifatTarikBahanKompositBerpenguatSerat Rami DenganMatrik Unsaturated Poliester. In Prosiding, Seminar Nasional Teknik Mesin FT Univ. Petra-Surabaya.
- Mawardi, R. H., Suryanto, E., & Sudewi, S. (2019). Aktivitas Antioksidan Dari Fraksi Tongkol Jagung (Zea Mays L.) Yang Diinduksi Oleh Fe2+ Dan Cahaya Uv-B. Chemistry Progress, 9(1).
Copyright information
This work is licensed under a Creative Commons Attribution-NonCommercial-NoDerivatives 4.0 International License.
About this article
Publication Date
30 March 2020
Article Doi
eBook ISBN
978-1-80296-080-8
Publisher
European Publisher
Volume
81
Print ISBN (optional)
-
Edition Number
1st Edition
Pages
1-839
Subjects
Business, innovation, sustainability, development studies
Cite this article as:
Muhammad Rafiq, Y., Siti Rahmah, S., & Ahmad, B. (2020). Study Of Composite Hardness With Ganoderma Boninense Mushroom As Filler. In N. Baba Rahim (Ed.), Multidisciplinary Research as Agent of Change for Industrial Revolution 4.0, vol 81. European Proceedings of Social and Behavioural Sciences (pp. 723-729). European Publisher. https://doi.org/10.15405/epsbs.2020.03.03.84