Abstract
Maintenance management of public facilities by local authorities is essential but still relatively neglected business function of an organization. There are some issues associated with the dissatisfactions of building condition; which resulted from the failures in determining the exact needs of maintenance executions. The practice of historical-based budgeting indicates a variety of budgeting bases which principally constrained the preliminary budget and fixed budget. The systematic literature review was the primary basis of information for the author to justify the budgeting process as the strategic approach to overcome the maintenance cost uncertainties and provide value for money to the organization’s management. As the budget and control system is built, the organization will concurrently act to reduce the total cost while assuring the capability performance of the facilities. Appropriate techniques motivate the budget, modification and control actions. Significantly, cost budgeting for maintenance is the best practice for achieving the value for money especially for the local authorities that serve the need of the public. This budgeting process allows the organization to implement best practices in maintenance management and it is an effective way to help them deliver their potential towards the efficient and profitable.
Keywords: Maintenance managementbudgetingmaintenance costlocal authorities
Introduction
In maintenance departments, budgeting is a very crucial part of the decision making for maintenance works. It became the primary mechanism that helps the organization to control the financial resources to plan and manage the activities within the department. The budget management uses various types of accounting procedures and software to design, execute, implement, control and measure the department's efficiency. Effective maintenance management allows the organization to generate and serve the goods and services towards customer’s satisfaction (Duffuaa & Ben-Daya, 2009). As emphasized by Gosavi, Murray, Tirumalasetty, & Shewade, (2011) and Craig (2017), it became the crucial aspect as it needs the organization to well provide and invest the necessary capital assets for fulfilling the customer’s requirement. Through various previous studies and reports, many organizations had encountered multiple problems due to an insufficient budget to support the maintenance works.
Nowadays, most of the organisation manoeuvre aggressively in the business milieu which resulted in some conflict in the requirement. Nevertheless, as the non-profit organisation, the local authorities are regulated in terms of resources and financial support; which constraint them to work efficiently in managing the asset and service (Adnan, Fazry, Fauzi, Rahmat, & Supardi, 2012; Atan, Abdul Raman, Sawiran, Mohamed, & Mail, 2010; Brackertz & Kenley, 2002; Rezvani et al., 2009). The concerns on the rapid changes of the maintenance strategies and resources have forced the organization to reflect the proactive maintenance management to encounter not just for the cost-saving measure but also any maintenance issues arise. Significantly, budgeting is a crucial element in the maintenance management that controls the economic value of the organisation (Gosavi et al., 2011; Gupta & Gandhi, 2014; Puķite & Geipele, 2017). The budget for maintenance needs to be well-planned and well-addressed the maintenance required to indicate the capability of the organization to carry out the maintenance works.
The author carried out the systematic literature review to ensures the objective of the study can be achieved. This paper is structured into four sections. Section
Problem statement
Many organizations aim to have the value for money in their business and services. They need to invest in their capital assets to generate revenue from their goods and services for their customers (Sciences, 2012; Tam & Price, 2008). Therefore, it is undeniable that each of the organizations trying to figure out the excellent techniques and strategies to overcome the weaknesses in their management. Equipment that is not working correctly or a building that is deteriorating means that they did not well-producing and working as it was supposed to serve the occupants. The situations have caused the organization potentially lost in revenue. Since the interruption and downtime are unavoidable for servicing the equipment and building, the maintenance manager needs to reflect the financial benefits of forecasting beforehand before the equipment or building breaks or requires laborious maintenance (George Prieskorn, n.d.; Gupta & Gandhi, 2014). Therefore, through budgeting toward the regular preventive maintenance can offer a long way to save time and value for money. Budgeting is a systematic approach to helps the organization to save money through routine maintenance that acts as the preventive instead of reactive (Cruzan, 2009; Peng Au-Yong, Ali, & Ahmad, 2014a; Vilarinhoa, Lopesa, & Oliveiraa, 2017).
Research questions
As the budgeting process for maintenance plays the vital role in determining the effectiveness of the maintenance management, it will give impact to the organization. The maintenance department will have its Key Performance Index (KPI) to be achieved to shows the efficiency of their planning to controlling the maintenance works. The research questions for the study have been defined as:
Q1: What is the state of the budgeting process for the maintenance works?
Q2: What are the potentials impacts and future implementation of budgeting to ensure value for money to the organization?
The purpose of the study
Therefore, the purpose of this study is to present the state of the budgeting process, the application of budget techniques and the limitations focusing on the maintenance context. Most of the organizations have their ways of developing the maintenance budget. The maintenance budget comprises an enormous sum of money that is broken out into different blocks for materials, labor, contract services and other related costs (Duffuaa & Ben-Daya, 2009; Peng Au-Yong et al., 2014b). It is crucial for the maintenance manager and the stakeholders to understand the process of developing the maintenance budget through the proper planning and scheduling of the maintenance works. There are various types of maintenance works that need different expenses and approaches. Hence, the maintenance cost is divided into three categories as shown in Figure
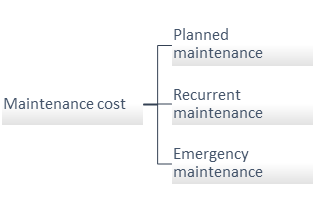
When formulating the maintenance budget, several considerations need to be emphasized which includes (Flores-Colen & De Brito, 2010; Gosavi et al., 2011; Management, 2015; Mohd-Noor, Hamid, Abdul-Ghani, & Haron, 2011; Tithíochta, 2017):
Existing assets to be maintained
Current assets that need to be replaced, refurbished and upgraded
Future maintenance of new assets
Identification of assets that requires special maintenance programs.
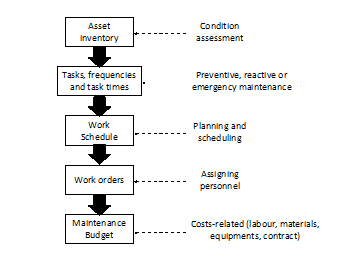

Research methods
To evaluate the state of the budgeting for maintenance, a systematic literature review approach has been conducted. This approach aims to search, review, integrate and analyze any relevant studies for the specific field of research. As described by Okoli (2015), systematic literature seeks to identify the gaps in the literature thus verify future areas of study. Booth, Colomb, & Wlliams, (2016) stated that there are seven steps in establishing systematic literature review: planning, defining scope, searching, assessing, synthesizing, analyzing and writing (Figure
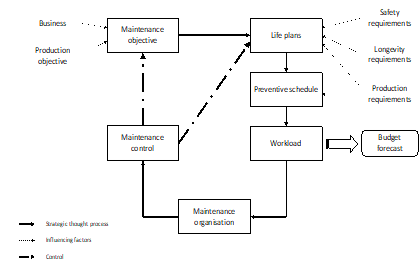
Step 1: Planning
Referring to Figure
ScienceDirect (www.sciencedirect.com)
Scopus (www.scopus.com)
Emerald Insight (www.emeraldinsight.com)
Google Scholar (www.scholar.google.co.uk)
IEEE Xplore (www.ieeexplore.com)
The selection of journals also plays a vital role in giving the overview to the author on the field of research and relevant issues and scope of studies. So, the author is focusing on the few selected journal such as:
Journal of Maintenance
Journal of Quality in Maintenance Engineering
Journal of Productions and Operations Management
Journal of Facilities Management,
Journal Facilities,
Journal of Operations Management,
Journal of Maintenance and Reliability Engineering
The author employs Mendeley (www.mendeley.com) as the reference manager due to its great support and easy to be utilized.
Step 2: Defining the scope
The scope of the study for this research is formulated through the main issues that circulated within the various industries that have been studied by other academic and non-academic community. The scope is defined based on the objective that needs to be achieved through brainstorming and peer-reviewed on selected articles journals. As per limitation on the previous study by other researchers, therefore the author narrowed down the scope of research to the budgeting for maintenance as the main scope of the study.
Step 3: Searching
In this step, the author will be using several keywords as the method to obtain the relevant article's journal in selected databases as specified in Step 1. For some reasons, the author is using “Maintenance Management”, “Budgeting”, “Local Authority” and “Maintenance Cost” as the keywords as the first screening of relevant articles. The selected articles were separated based on the different keywords.
Step 4: Assessing
From hundreds of articles and documents, it is the time for the author to narrow down the final number of documents that were related and relevant to be used. The author also chooses articles from the year of 2000 onwards to ensure the credibility and validity of the articles to show the relevancy of the issues; the exclusion will be on the reference books.
Step 5: Synthesizing and Step 6: Analysing
To answer the research questions, the author synthesized and analysed the selected articles based on the keywords. It is relevant to use 20 articles related to the keywords to address the issue of budgeting and maintenance management. It is easy to extract the information from the selected articles to and transferred to the table to provide the reader with a better understanding of the reason for choosing the scope of the study. As the primary objective is focusing on the state of the budgeting process, it may give the reader overview the budgeting process was not being well-focused in the previous research. According to Table
Step 7: Writing
After having six steps, the author started to clarify and justify the need for the research and study related to the budgeting process for maintenance, especially for the local authority. This is due to the local authority is the local service provider that mostly serve the needs of the customers and the public. The process of budgeting is essential to ensure the effectiveness and efficiencies of the maintenance department in conducting the maintenance works for its equipment and building. Therefore, the primary consideration of this study is focusing on how the budgeting process can assist the local authority to achieve value for money in maintenance management.
Findings
Most of the organizations believe that the budget does not reflect the reality as the some of the building and equipment failures cannot be predicted and unforeseen. Though the maintenance department has considered the contingencies of money to cover the emergency maintenance. However, some of the experts in maintenance argued that, if only the maintenance plan were efficiently conducted, the chances of overspending would not happen (George Prieskorn, n.d.; Gosavi et al., 2011; Management, 2015). This means the maintenance department must forecast the need for the maintenance task to ensure the maintenance management offers the value for money to the organizations. By having a budgeted annual maintenance plan does not positively transformed into effective maintenance results. As we all know, the main purpose of maintenance is to lower the risk of failures and downtime. Typically, the maintenance plans consist of effective maintenance strategies (Velmurugan & Dhingra, 2015). From the maintenance strategy, the respective cost associated with the maintenance tasks will be forecasted. An estimated annual maintenance through selected budget techniques will be generated (Kelly, 2007).
The fundamental significance of budgeting in the formulation of the maintenance plan can be seen through the participation of the stakeholders. The stakeholders which consist of the maintenance supervisors, planners, personnel and operation partners that responsible for the maintenance job (Stenström, Parida, Kumar, & Galar, 2013). The requirement for a maintenance budget initiates the business and organization goals and objective. From year to year, the maintenance budget being revised to accommodate the need of maintenance workload. The estimated cost of each related cost such as the labor, materials, spare parts involved the maintenance department to well-planned the selected strategy (Figure

Conclusions
The cost-effectiveness performance of maintenance management practices requires the organizations to follow the planned management business procedures. The execution needs approval from the responsible maintenance manager which is necessary to ensure the work planning and scheduling can be control efficiently regarding spending. What we can track the performance of the maintenance work orders that are properly conducted is less expensive and more effective. As recommended by Peffen (2014), the maintenance cost can be reduced three to five times when the maintenance department had prepared the maintenance budget accordingly. Besides, it offers a better quality of the maintenance works and less "emergency" spending on the equipment and building itself. A structured process for developing the maintenance budget and well-defined budget can ensure the value for money to the organization primarily to the non-profit organization such as local authority. Ultimately, the maintenance department can contribute to the effectiveness of the business and services of the organization.
References
- Adnan, H., Fazry, Z., Fauzi, M., Rahmat, I., & Supardi, A. (2012). Maintenance Management for Public Infrastructure. APRN Journal of Engineering and Applied Sciences, 7(11), 1514–1522.
- Ansari, F., Fathi, M., & Seidenberg, U. (2016). Problem-solving approaches in maintenance cost management: a literature review. Journal of Quality in Maintenance Engineering, 22(4), 334–352.
- Atan, R., Abdul Raman, S., Sawiran, M. S., Mohamed, N., & Mail, R. (2010). Financial performance of Malaysian local authorities: A trend analysis. In 2010 International Conference on Science and Social Research (CSSR 2010) (pp. 271–276).
- Au-yong, C. P., Ali, A. S., & Ahmad, F. (2014). Participative Mechanisms to Improve Office Maintenance Performance and Customer Satisfaction. Journal of Performance of Constructed Facilities, 29(4), 1–7.
- Booth, W. C., Colomb, G. G., & Wlliams, J. M. (2016). The Craft of Research (Second). The University of Chicago Press.
- Brackertz, N., & Kenley, R. (2002). Evaluating community facilities in local government: Managing for service enablement. Journal of Facilities Management, 1(3), 283–299.
- Chiang, Y., Zhou, L., & Li, J. (2014). Achieving Sustainable Building Maintenance through Optimizing Life-Cycle Carbon, Cost, and Labor: Case in Hong Kong. Journal of Construction …, 140(3), 1–10.
- Craig, C. (2017). The Chaos Theory of Maintenance Management.
- Crespo Marquez, A., & Gupta, J. N. D. (2006). Contemporary maintenance management: Process, framework and supporting pillars. Omega, 34(3), 313–326.
- Cruzan, R. (2009). Manager’s Guide to Preventive Building MAintenance.
- Department of Housing and Public Works. (2012). Building Maintenance Budget. Retrieved from http://www.hpw.qld.gov.au/SiteCollectionDocuments/MMFBmb.pdf
- Dorotinsky Back. (n.d.). THE BUDGET PREPARATION PROCESS.
- Duffuaa, S. O., & Ben-Daya, M. (2009). Handbook of Maintenance Management and Engineering. Handbook of Maintenance Management and Engineering.
- Flores-Colen, I., & De Brito, J. (2010). A systematic approach for maintenance budgeting of buildings faades based on predictive and preventive strategies. Construction and Building Materials, 24(9), 1718–1729.
- George Prieskorn. (n.d.). THE IMPORTANCE OF BUDGETING.
- Gosavi, A., Murray, S. L., Tirumalasetty, V. M., & Shewade, S. (2011). A Budget-Sensitive Approach to Scheduling Maintenance in a Total Productive Maintenance (TPM) Program. Engineering Management Journal, 23(3), 46–56.
- Gupta, P., Gupta, S., & Gandhi, O. P. (2014). Annual maintenance budget estimation for a plant system. Journal of Quality in Maintenance Engineering, 20(2), 193–210.
- Hamzah, S., & Kobayashi, K. (2013). Utilizing Mid-long Term Maintenance Management Policy for Sustainable Maintenance of Infrastructure Facilities. Procedia Environmental Sciences, 17, 478–484.
- Jolicoeur, P. W., & Barrett, J. T. (2004). Coming of age: Strategic asset management in the municipal sector. Journal of Facilities Management, 3(1), 41–52.
- Kelly, T. (2007). Maintenance Budgeting, 32–35.
- Lai, J. H. K. (2010). Operation and maintenance budgeting for commercial buildings in Hong Kong. Construction Management and Economics, 28(January 2015), 415–427.
- Lee, H. H. Y., & Scott, D. (2008). Overview of maintenance strategy, acceptable maintenance standard and resources from a building maintenance operation perspective. Journal of Building Appraisal, 4(4), 269–278.
- Management, C. I. M. of F. and E. (2015). Study of Infrastructure Maintenance Budgets Government of the Cook Islands.
- Mohd-Noor, N., Hamid, M. Y., Abdul-Ghani, A. A., & Haron, S. N. (2011). Building maintenance budget determination: An exploration study in the Malaysia government practice. In Procedia Engineering (Vol. 20, pp. 435–444).
- Okoli, C. (2015). A Guide to Conducting a Standalone Systematic Literature Review. Communications of the AIS, 37, 879–910.
- Ouertani, M. Z., Parlikad, A. K., & McFarlane, D. (2008). Towards an approach to select an asset information management strategy. International Journal of Computer Science and Applications, 5(3b), 25–44.
- Peffen, R. (2014). Managing the Maintenance Budget.
- Pelantova, V., & Cecak, P. (2018). NEW ASPECTS OF MAINTENANCE MANAGEMENT AND THE MATERIAL OF SPARE PARTS. MM Science Journal, (March), 2283–2289.
- Peng Au-Yong, C., Shah Ali, A., & Ahmad, F. (2014a). Preventive Maintenance Characteristics towards Optimal Maintenance Performance: A Case Study of Office Buildings. World Journal of Engineering and Technology, 2(2), 1–6.
- Peng Au-Yong, C., Shah Ali, A., & Ahmad, F. (2014b). Prediction Cost Maintenance Model of office building based on Condition-Based Maintenance. Eksploatacja i Niezawodnosc -Maintenance and Reliability, 16(2), 319–324. Retrieved from http://www.ein.org.pl/sites/default/files/2014
- Puķite, I., & Geipele, I. (2017). Different Approaches to Building Management and Maintenance Meaning Explanation. Procedia Engineering, 172, 905–912.
- Rahmat, N., & Hadi Nawawi, A. (2017). Facilities Management in Malaysian Local Authorities: Identifying Current Issues. Retrieved from http://docsdrive.com/pdfs/medwelljournals/sscience/2017/755-761.pdf
- Rastegari, A. (2015). Strategic maintenance management : Formulating maintenance strategy, (June 2016).
- Rezvani, A., Srinivasan, R., Farhan, F., Parlikad, A. K., Jafari, M., & Brunswick, N. (2009). Towards Value-Based Asset Maintenance. In Proceedings of the 4th World Congress on Engineering Asset Management Athens, Greece (pp. 350–357).
- Schuman, C., & Brent, A. C. (2005). Asset life cycle management: towards improving physical asset performance in the process industry. International Journal of Operations & Production Management, 25(6), 566–579.
- Sciences, N. A. of (Ed.). (2012). Predicting Outcomes from Investments in Maintenance and Repair for Federal Facilities Repair for Federal Facilities ; National Research Council.
- Sinha, P. (2015). Towards higher maintenance effectiveness. International Journal of Quality & Reliability Management, 32(7), 754–762.
- Sinkkonen, T., Marttonen, S., Tynninen, L., & Kärri, T. (2013). Modelling costs in maintenance networks. Journal of Quality in Maintenance Engineering, 19(3), 330–344.
- Söderholm, P., Holmgren, M., & Klefsjö, B. (2007). A process view of maintenance and its stakeholders. Journal of Quality in Maintenance Engineering, 13(1), 19–32.
- Stenström, C., Parida, A., Kumar, U., & Galar, D. (2013). Performance indicators and terminology for value driven maintenance. Journal of Quality in Maintenance Engineering, 19(3), 222–232.
- Sullivan, G. P., Pugh, R., Melendez, A. P., & Hunt, W. D. (2010). Operation and Maintenance Best Practice: A Guide to Achieving Efficiency.
- Talamo, C., & Bonanomi, M. (2015). Knowledge Management and Information Tools for Building Maintenance and Facility Management.
- Tam, A. S. B., & Price, J. W. H. (2008). A maintenance prioritisation approach to maximise return on investment subject to time and budget constraints. Journal of Quality in Maintenance Engineering, 14(3), 272–289.
- Tithíochta, A. R. (2017). Local Government Audit Service Corporate Estate Management and Maintenance in Local Authorities Value for Money Unit Report No . 30 January 2017, (30).
- Velmurugan, R. S., & Dhingra, T. (2015). Maintenance strategy selection and its impact in maintenance function. International Journal of Operations & Production Management (Vol. 35).
- Vilarinhoa, S., Lopesa, I., & Oliveiraa, J. A. (2017). Preventive maintenance decisions through maintenance optimization models : a case study, 11(June), 1170–1177.
Copyright information
This work is licensed under a Creative Commons Attribution-NonCommercial-NoDerivatives 4.0 International License.
About this article
Publication Date
17 May 2019
Article Doi
eBook ISBN
978-1-80296-061-7
Publisher
Future Academy
Volume
62
Print ISBN (optional)
-
Edition Number
1st Edition
Pages
1-539
Subjects
Business, innovation, sustainability, environment, green business, environmental issues
Cite this article as:
Saidin Misnan, M., Mohamed, S. F., & Mong*, S. G. (2019). Budgeting: A Strategic Approach To Achieve Value For Money In Maintenance Management. In M. Imran Qureshi (Ed.), Technology & Society: A Multidisciplinary Pathway for Sustainable Development, vol 62. European Proceedings of Social and Behavioural Sciences (pp. 331-340). Future Academy. https://doi.org/10.15405/epsbs.2019.05.02.32