Abstract
As the competition among manufacturing organizations is getting tough the only choice left to manufacturers is to have an integrations between the customer and the manufacturer at various stages of the product i.e. design, manufacturing, sales and marketing etc. The information which results in this integration can be used to set up modular production facilities. This well informed system which is a smart system right from the design stage to the customer service stage overcomes all limitations which was not possible before and thus helps in the success of agile manufacturing whereas the concept of Industry 4.0 refers to the notion of smart manufacturing works where live data sharing among intelligent machines ends up providing an intelligent manufacturing system. Researchers in this paper examine the similarity of 4th industrial revolution and agile manufacturing concepts. This paper indicates that Small and Medium Enterprises can positively commit into the new concept of industry 4.0 with the perception that they can become more flexible and responsive. However, there is an increasing need for future research to include and emphasize the importance of flexible manufacturing and mass customization.
Keywords: Industry 40manufacturingVirtual EnterpriseAgile Manufacturingsmart system
Introduction
Due to rapid shifts in customer needs, manufacturing strategies has been shifted from its original dynamics. Among these new options, agile manufacturing is the one, which emphasize on adaptive capability to meet the requirements of future changes. Flexibility and responsiveness are essential to fulfilling rapidly changing customer demands.
The main idea of agile manufacturing proposed in 1991 at University Lehigh (Pant, Rattner, & Hsu, 1994). The word agile means to cater change and uncertainty, by integrating organizational information as whole in manufacturing and production (Anonymous, 1995). In agile environment manufacturer could be able to recognize current and future customers demands and translates them into modified design and technologies for achieve competitiveness. Product model data, shop-floor control system, information and communication system, virtual manufacturing and concurrent engineering are critical for the effective accomplishment of agile manufacturing (Cho, Jung, & Kim, 1996).
Manufacturing sector in Germany comprises of small and medium scale enterprises employ agile manufacturing strategies to become competitive player among other global trade (Venohr & Meyer, 2007). However, the path leading toward agile has never been straightforward and some of the manufacturing companies in Germany are still striving towards implementing agile manufacturing (Venohr & Meyer, 2007). This is because various barriers exist in integrating information and it is therefore essential to find the solution for these road blocks first. Industry 4.0. can possibly serve as the best modern day life saver. With the advent of emerging technologies like cyber physical system (CPS) and internet of things (IoT) a new concept of industry 4.0 were initiated by German in 2011.Under this concept, manufacturing would be able to exchange information by controlling and integrating autonomous production facilities for producing customized products.
Industry 4.0 employs innovative application of information and communication system so that entire factory becomes smart and flexible. Nonetheless, financial constraints are one of the reasons that not all Companies are enthusiastic to drive into fourth industrial revolution (Schröder, Schlepphorst, & Kay, 2015). Smart factories are the principal object of industry 4.0, in which modern communication and IT technologies enable human and machines to interchange information. All this is connected with the cyber physical system to combine physical world to the cyber world (Kagermann, Wahlster, & Helbig, 2013).
This research supports that the term “agile” and “industry 4.0” are not mutually exclusive, but these two concepts could be seamlessly integrated for competitive and successful manufacturing facilities. This paper examine the research conducted in the capacity of industry 4.0 and illustrate the fact that how industry 4.0 could be supportive in the implementation of agile manufacturing.
Problem Statement
With the advent of technology the manufacturing processes are drastically changed. The competition is rising every day and organizations need to create some magic to stay on top. The fourth industrial revolution has triggered new avenues for success and industries need to find out the roadmap for being agile and smart.
Research Questions
How virtual enterprise formation will help in making the organization smart and agile?
How integrated production Information will help in making the organization smart and agile?
How customer integration system will help in making the organization smart and agile?
How work force management system: will help in making the organization smart and agile?
Purpose of the Study
To find out the key triggering factors that would enable industries to become successful by implying concepts of agile manufacturing and industry 4.0
Research Method
Actions completed during the analysis is delineated as follows. At the start we tend to carried out in-depth study in the domain of agile manufacturing. As varied definition exist in context to academics and industry. We framed a suitable definition of agile manufacturing and hypothesized into different domains. After that we presented the concept of industry 4.0 and conferred the most critical implication in implementing agile manufacturing. In the next stage we studied the literature regarding industry 4.0 in context to responsive manufacturing. Various researches in the domain of industry 4.0 has been explored that present the solution against barriers in the way of agile implementation. We dig out those solutions and formulate as the enablers for agile manufacturing. Illustration of this model is presented in the figure
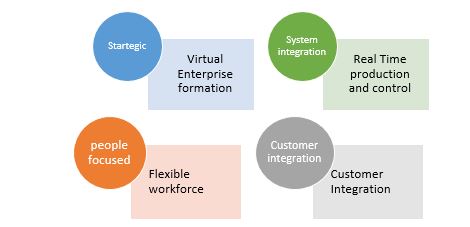
Literature Review
6.1. Agile Manufacturing
The term agile manufacturing can be defined as competence to persist in a competitive and uncertain environment by responding quickly and providing customized products and services. Key parameters to support this concept are Virtual enterprise, physically distributed manufacturing architecture, rapid partnership formation tools and services, concurrent engineering, rapid prototyping and electronic commerce. (Gunneson, 1997).
Agile based corporations are able to respond in volatile market by re-organizing and even reconfiguring themselves to capture the opportunities of market share. The role of information system is quite crucial in the success of agile-based manufacturing system because timely sharing of relevant data helps in integrating and enabling all stages of production in effective manners (Pant et al., 1994). After extensive review of the literature, it has been established that the following four factors are most crucial in the way of agile manufacturing implementation (Figure
Virtual Enterprise formation
Real Time production and control
Customer integration
Flexible workforce
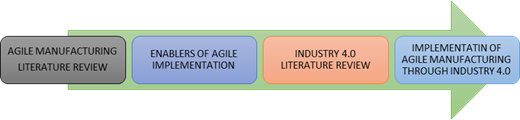
Most significant factor for an organization to become agile is virtual enterprise formation (VE) in which partners can collaborate with each other. Virtual enterprise is an organizational business concepts that integrate competencies of various member companies necessary to develop a new or transformed product as per customer requirement.
VE enable value added activities across the business value chain in such a way that excellent quality product should be delivered to customer (Goldman, Nagel, & Preiss, 1995). Virtual enterprise formation is not an easy task, various barriers exist in its way. Among them, the most crucial is innovative technology acquisition, which is necessary to integrate the essential process of business system. Besides this lack of consolidated models for integrating different levels and specialized skills in a system is another challenge in implementing virtual organization in agile.
The establishment of agile is an integrated system become quite complex due to physically dispersed entities and subsystems. Each member or system have their own control and domain and each have to link with other. (Youssef, 1992). Therefore the system of communication must be developed so that useful information can be synchronized and shared right in production control. This could be possible through advanced technologies so that system would be operative in agile environment. Generic management role from the varied deviations found in low level devices. (Beaumariage, Roberts, & Baweja, 1995). In order to effectively establish production control, manufacturing information could be accessible from number of sources like; from independent computers, patent database system and also from test equipment.
In order to meet customer requirement with increased flexibility in producing products push and pull production models require to be followed. These integrated models are suitable in agile manufacturing environment that involves MRP calculations and Just-in-time system of production. Integrated production models using optimized production technology could be developed in order to enable customized specified production system.
Agile manufacturing require employees to be creative and innovative. This concept demand continues improvement, as the work-force needs to improve existing ways of doing work and always alter some innovative ideas (Cannata, Gerosa, &Taisch, 2008). Enabling workforce to work in quite challenging environment as human nature is to repel change. Continuous education and technological training will help them to be flexible and competitive in a more responsive manner. Also, allocating the right person for right job is also crucial for the productive workforce in agile environment. Due to traditional repetitive practices in production unit this become quite challenging in the way of agile manufacturing implementation
6.2.Industry 4.0
Industry 4 embraces the assurances of greater flexibility in manufacturing with exceptional quality characteristics, mass customization and improved productivity. This derives an improved way to deal shorter life cycle of individualized products with reduced lead-time.
The term Industry 4.0 is propounded by Germans, aiming for the creation of smart factories, where the relevant technologies could be upgraded by cyber physical space (CPSs), the Internet of Things (IoT), and cloud computing (Penas, Plateaux, Patalano, & Hammadi, 2017). Digital twin would be created by communication with sensor, actuators, humans and so forth in industry 4.0 to transform overall industry value chain (Wang, Wan, Zhang, Li, & Zhang, 2015).
Smart system enable identity and communication between each individual entity independently in a value stream, so it will leads to IT-enable mass customization (Brauner & Ziefle, 2015). Internet of things and digitalized smart machines synchronize themselves right from the start to the end of production processes within the value chain. Industry 4.0 in context to manufacturing sector covers extensive concept like, mechatronics in manufacturing has been improved and used to support CPS (Lee, Bagheri, & Kao, 2015).
Customized Products to meet individual needs has been designed and proposed using new technologies (Zawadzki & Żywicki, 2016) Predictive maintenance is a booming topic in prognosising machine condition under the domain of industry4.0 based CPS system (Xia & Xi, 2017). Machine tool 4.0, Energy management 4.0 concepts has been proposed in machining sites and self-optimizing energy sources within the system. Further to this, technologies in logistic 4.0 have also been introduced and investigated to implement (Hofmann & Rüsch, 2017).
Findings:
Competitive Industry 4.0 Supporting Technologies and Concepts to Integrate Agile Manufacturing Crucial Factors:
7.1.1. Virtual Enterprise formation
Among other several challenges in the way of agile manufacturing, virtual enterprise formation is one and most crucial. The need to produce customized products in with shorter life cycle requires traditional organization to broaden its horizon and form an extended virtual organization. Instantaneous and effective information processing from several sources is a main challenge in forming virtual enterprise. As the processed information could be utilized in making decisions for configuring manufacturing strategies based on customer requirements (Almeida, Ferreira, Azevedo, & Caldas, 2013). Relevant to this concept emerging tools and techniques of industry 4.0 could be applied in manufacturing environment for the creation of cyber physical production environment, which could lead an organization to become flexible, efficient and responsive.
The main concept in this regard is “Reference Architectural Model” for industry 4.0, which aims to Integrate the numerous business units with the network to logistic value chain. In RAMI, all business entities represented as components showing service functions and have standardized communication channels. In this way all units can interpolate and exchange useful information which is vital for the formation of virtual organization (Camarinha-Matos, Afsarmanesh, Galeano, & Molina, 2009).
An example of cloud based industry 4.0 is virtual enterprise management architecture. Various components has been included to integrate horizontal and vertical levels in business value chain.
Following stages has been explained in establishing virtual enterprise (Ferreira, Faria, Azevedo, & Marques, 2016);
Model that represent and discover associated companies and its services in designing, managing and operating virtual organizations is called “Services Repository”.
Process manager can arrange all collaboration as per defined process models in virtual enterprise. In order to achieve highest efficiency process manger interacts with optimization and simulation tools and techniques.
Hybrid process manger deal with the situation where highly intensive collaborative knowledge based decisions are relied on human.
Optimization involves to improve the effectiveness of virtual organizations in preceding assignments of task and services.
Finally, business intelligent model extract data from big data sources also called data mining and process it into use full information in making decisions in virtual enterprise
In this way emerging and latest concepts of industry 4.0 provides an avenue to form virtual enterprise in implementing agile manufacturing.
7.1.2. Integrated Production Information:
Data analysis and compilation is the crucial step in achieving smartness in all phases. Due to advanced technologies, like virtual reality and augmented reality traditional designs approaches has become advanced. In this context hybrid prototyping has been designed using VR technique. Latest designed software CAD and CAM can now interlink by means of smart physical prototype structure. In this way, various engineering changes and physical comprehensions would be incorporated in attaining smart paradigm (Kolarevic, 2003).
Cyber physical based system enable smart manufacturing solutions by enabling smart tools to capture real time data from cloud- based central system. In this way smart machining tools and additive service could be synchronize themselves for providing smart product with changing customer needs.
Industry 4.0 has three strategic levels, first one is implementation of equipment connectivity, in which all the machines, factories, devices, production lines are connected to a system that enable the data transparency and visualization possible. After that, value added manufacturing activities and services are introduced in smart manufacturing environment. Last stage is intelligent innovative services that enable intelligent technology and big data analysis (Zheng et al., 2018). Data analysis and compilation is the crucial step in achieving smartness in all phases.
Cloud based manufacturing system provide an innovative control and decision support system called CSaaS (Marzband, Parhizi, Savaghebi, & Guerrero, 2016) User in this structure includes machine operators, machine supervisory vendors and end users. Connectivity of all this chain can create the ultimate solution for catering new and emerging trends in demand.
Cloud- based smart control systemshows how end users, machine operators, management control is connected in a cloud based manufacturing environment to support critical decisions and tasks using adaptive control (Tang & Zhang, 2009)
.
7.1.3. Customer integration system
In order to produce valuable product, customer involvement has been given highest importance right from the product development phase. Therefore, customer feedback plays a crucial role in developing and improving product features as per demand. But in the traditional business environment once the standard are set for manufacturing then customer are no longer being able to demand for alteration which is opposite to agile manufacturing concept. However, with the advent of industry 4.0 intelligent manufacturing concepts, freeze period could be elongated further to entertain interchangeable parameters. Business to customer (B2C) applications, manufacturing execution system could be integrated with different system to achieve this goal. Due to this system customer could be aware of their product stages and communicate their requirement before the completion of product (Cannata, Gerosa, & Taisch, 2008).
Meeting customer demands require systematic procedures in various dimensions like, scheduling, monitoring, controlling and decision making. Smart manufacturing using industry 4.0 concepts, all the value change and design making stages could be synchronized right from the product development phase till the delivery to end customer (SPEC, 2016). This synchronization could be provided by incorporating internet of thing (IoT) in to production processes/stages and control. This will help in predicting occurrence of particular events, such that malfunctioning of machine, exceeding time for performing an operation, and the schedule of maintenance work required in plant and machines. Internet of things allows human to optimized decision making regarding material flow and machine operations (Liu, Xu, Zhang, Wang, & Zhong, 2017). With the help of controllers, sensors, actuators information of manufacturing system can strictly integrated with each other in a cyber-physical environment in a real system.
7.1.4. Work Force Management System:
Employees are mainly involve in producing products and services. So, their suggestions or feedback is important in improving existing situations. One of the obvious factor in reducing employee efficiency is monotonous working environment, but in industry 4.0 concepts monotonous and non-skilled activities are automate so that manual work should be focused on data processing and various non- repetitive task. In this scenario employee can use their own connective devices, thus encouraging to utilized worker creativity and various skills effectively (Schuh, et al, 2015a).
Allocation of right job or task for the right employee and training for multiple skills increase motivational level of employee and eventually enable them to be more productive. (Sanders &Wulfsberg, 2015). In various scenarios, a worker may not be able to present his/her suggestions. This problem has been overcome using industry 4.0 concepts in which production worker can provide instant feedback via real time data sharing integrated overall business operations. In industry 4.0 environment employees can record, explain and present their concerns right at the workplace. (Schuh, et al, 2015b). Not only this Cyber physical system can check the availability of particular employee for the specific operations thus reducing the mangers effort in maintaining workforce. In this way assessment of workforce in term of their availability, speed precision and performance could be simplified by worker support system (Brauner &Ziefle, 2015).
Conclusion
Industries are striving to implement agile manufacturing, but not every firm is yet to achieve its proper execution and acquire benefits from it. This research presented a comprehensive framework of agile implementation from the integration perspective that how industry 4.0 enabled technologies could be supportive in implementing agile manufacturing. With the help of future IT based communication technologies short coming in current practices of agile manufacturing could be overcome to increase competitiveness and improved customized product availability. The research also infers that industries now have benefit in integrating with each other, and enabling machineries and processes to interact and exchange real time information with an assurance to produce mass customization. This paper indicates that Small and Medium Enterprises can positively commit into the new concept of industry 4.0 with the perception that they can become more flexible and responsive. However, there is an increasing need for future research to include and emphasize the importance of flexible manufacturing and mass customization. Rapid increase in digitalization and automation has evolved new technologies. Therefore, exploration of impacts of latest innovation needs to analysis on agile manufacturing over the period of time in order to become progressive. Many researches in industry 4.0 are theoretical based, not readily adoption of an application. So, future researches need to be dedicated on producing conceptual framework and integrating production environment with cyber physical system.
References
- Almeida, A., Ferreira, F., Azevedo, A., & Caldas, Á. (2013). Process performance assessment in collaborative manufacturing environments: a role oriented approach. In Advances in Sustainable and Competitive Manufacturing Systems (pp. 911-924). Springer, Heidelberg.
- Anonymous, (1995). Moving towards agile manufacturing: the agile program at MIT. Technology and Policy, (pp.1, 9).
- Beaumariage, T., Roberts, C., & Baweja, G. (1995). Representation of manufacturing systems in terms of entities and relationships. International Journal of Computer Integrated Manufacturing, 8(1), 43-53.
- Brauner, P., &Ziefle, M. (2015). Human Factors in Production Systems. Advances in Production Technology, Springer International Publishing, 187-199. DOI:
- Camarinha-Matos, L. M., Afsarmanesh, H., Galeano, N., & Molina, A. (2009). Collaborative networked organizations–Concepts and practice in manufacturing enterprises. Computers & Industrial Engineering, 57(1), 46-60.
- Cannata, A., Gerosa, M., &Taisch, M. (2008). SOCRADES: A framework for developing intelligent systems in manufacturing. IEEE International Conference on Industrial Engineering and Engineering Management (IEEM 2008) Singapore. 1904-1908. DOI:
- Cho, H., Jung, M., & Kim, M. (1996). Enabling technologies of agile manufacturing and its related activities in Korea. Computers & Industrial Engineering, 30(3), 323-334.
- Ferreira, F., Faria, J., Azevedo, A., & Marques, A. L. (2016, October). Industry 4.0 as Enabler for Effective Manufacturing Virtual Enterprises. In Working Conference on Virtual Enterprises (pp. 274-285). Springer, Cham.
- Goldman, S. L., Nagel, R. N., & Preiss, K. (1995). Agile competitors and virtual organizations: strategies for enriching the customer (Vol. 8). New York: Van Nostrand Reinhold.
- Gunneson, A.O. (1997), Transitioning to Agility, Addison-Wesley Publishing Company, New York, NY.
- Hofmann, E., & Rüsch, M. (2017). Industry 4.0 and the current status as well as future prospects on logistics. Computers in Industry, 89, 23-34.
- Kagermann, H., Wahlster, W., & Helbig, J. (2013). Recommendations for implementing the strategic initiative Industrie 4.0: Final report of the Industrie 4.0. Frankfurt, Alemanha.
- Kolarevic, B. (2003), Architecture in the Digital Age Design and Manufacturing.
- Lee, J., Bagheri, B., & Kao, H. A. (2015). A cyber-physical systems architecture for industry 4.0-based manufacturing systems. Manufacturing Letters, 3, 18-23.
- Liu, Y., Xu, X., Zhang, L., Wang, L., & Zhong, R. Y. (2017). Workload-based multi-task scheduling in cloud manufacturing. Robotics and Computer-Integrated Manufacturing, 45, 3-20. markets'', Industrial Engineering, December, pp 177-80.
- Marzband, M., Parhizi, N., Savaghebi, M., & Guerrero, J. M. (2016). Distributed smart decision-making for a multimicrogrid system based on a hierarchical interactive architecture. IEEE Transactions on Energy Conversion, 31(2), 637-648.
- Pant, S., Rattner, L., & Hsu, C. (1994). Manufacturing information integration using a reference model. International Journal of Operations & Production Management, 14(11), 52-72
- Penas, O., Plateaux, R., Patalano, S., & Hammadi, M. (2017). Multi-scale approach from mechatronic to Cyber-Physical Systems for the design of manufacturing systems. Computers in Industry, 86, 52-69.
- Sanders, A., & Wulfsberg, J. (2015). Industrie 4.0: Shopfloor Management im Wandel: Konzeptionelle Handlungsempfehlungen. ZWF Zeitschrift für wirtschaftlichen Fabrikbetrieb, 110(10), 653-656.
- Schröder, C., Schlepphorst, S., & Kay, R. (2015). Bedeutung der DigitalisierungimMittelstand (No. 244). IfM-Materialien, InstitutfürMittelstandsforschung (IfM) Bonn.
- Schuh, G., Gartzen, T., Rodenhauser, T., & Marks, A. (2015a). Promoting Work-based Learning through Industry 4.0. Procedia CIRP, 32, 82-87.
- Schuh, G., Reuter, C., Hauptvogel, A., &Dölle, C. (2015b). Hypotheses for a Theory of Production in the Context of Industrie 4.0. Advances in Production Technology. Springer International Publishing. 11-23.
- SPEC, D. (2016). 91345: 2016-04. Reference Architecture Model Industrie 4.0 (RAMI4. 0).
- Tang, L., & Zhang, Y. (2009). Parallel machine scheduling under the disruption of machine breakdown. Industrial & Engineering Chemistry Research, 48(14), 6660-6667.
- Venohr, B., & Meyer, K.E. (2007). The German miracle keeps running: How Germany's hidden champions stay ahead in the global economy. Working paper. Institute of Management, Berlin School of Economics, Berlin, Available at SSRN 991964, March.
- Wang, S., Wan, J., Zhang, D., Li, D., & Zhang, C. (2016). Towards smart factory for industry 4.0: a self-organized multi-agent system with big data based feedback and coordination. Computer Networks, 101, 158-168.
- Xia, T., & Xi, L. (2017). Manufacturing paradigm-oriented PHM methodologies for cyber-physical systems. Journal of Intelligent Manufacturing, 1-14.
- Youssef, M.A. (1992), ``Agile manufacturing: a necessary condition for competing on global
- Zawadzki, P., & Żywicki, K. (2016). Smart product design and production control for effective mass customization in the Industry 4.0 concept. Management and Production Engineering Review, 7(3), 105-112.
- Zheng, P., Sang, Z., Zhong, R. Y., Liu, Y., Liu, C., Mubarok, K., ... & Xu, X. (2018). Smart manufacturing systems for Industry 4.0: Conceptual framework, scenarios, and future perspectives. Frontiers of Mechanical Engineering, 1-14.
Copyright information
This work is licensed under a Creative Commons Attribution-NonCommercial-NoDerivatives 4.0 International License.
About this article
Publication Date
17 May 2019
Article Doi
eBook ISBN
978-1-80296-061-7
Publisher
Future Academy
Volume
62
Print ISBN (optional)
-
Edition Number
1st Edition
Pages
1-539
Subjects
Business, innovation, sustainability, environment, green business, environmental issues
Cite this article as:
kausar Azam, M., & Yaqoob*, S. (2019). Industry 4.0 And Agile Manufacturing. In M. Imran Qureshi (Ed.), Technology & Society: A Multidisciplinary Pathway for Sustainable Development, vol 62. European Proceedings of Social and Behavioural Sciences (pp. 184-193). Future Academy. https://doi.org/10.15405/epsbs.2019.05.02.17