Abstract
Rice husk has been used as a thermal energy source for electricity generation, resulting in the formation of silica from rice husk as a by-product. The purpose of this research is to analyse the effect of acid concentration through the extract of silica in the rice husk via acid leaching treatment, due to silica as a raw material that can be apply in industrial. Acid leaching treatment was implemented to extract the silica and organic in rice husk. Besides, the parameters such as concentration of acid and leaching time of organic and inorganic acid during leaching method were also compared. In this research, hydrochloric acid (HCL) and citric acid (C6H8O7) were used for production of silica from rice husk. Various samples were characterized using Fourier Emission Scanning Electron microscopy (FESEM), X-ray diffraction (XRD) and X-ray fluorescence (XRF). The result indicates that highest percentage silica of rice husk after leaching was on 1.0M at 60 minutes and has an amorphous structure.
Keywords: Silica”Rice Husk”Inorganic Acid”Organic Acid”Agriculture Waste”
Introduction
Silica is a group of minerals composed of oxygen and silicon, with the two most torrential elements in the earth's crust. It also can exist in crystalline, amorphous and gel forms. It is the most abandon material on the earth’s crust. It is composed of one atom of silicon and two atoms of oxygen by giving the resulting of the chemical formula SiO2. Furthermore, silica within the years has gained major significance and various application in different industries such as rubber industry, pharmaceuticals and medicine. Hence, silica is also basic raw material that is widely used in electronics, ceramic, and polymer material industries. Because of its particles diameter, ultrafine silica powders have many technological applications, such as thixotropic agents, thermal insulators and composite fillers (Ghosh & Bhattacherjee, 2013).
Biomass is one of the most promising energy-carrying agent and can play an important role in environmentally friendly energy utilization. Rice husk (RH) is an agricultural waste containing high content of silica, distributed in high-volume worldwide. In Malaysia, 1.2 million tonnes of agricultural waste is disposed of into landfills annually. Most of rice husk will burn as fuel to generate energy resulting in the waste product, rice husk ash (RHA). If these RHA are not utilized, it will result in tremendous waste generation, energy loss and environmental pollution. Therefore, it is very important to find ways to utilize rice husk comprehensively. RH usually contains more than 60% of SiO2, 10–40% carbon with minor mineral composition. RH has a relatively high content of inorganic compounds, representing approximately 20% of the dry weight of the husk (Farshid, Maryam, & Ali, 2015). Silica represents 94% of the total while the remaining 6% are K2O, CaO, MgO, Al2O3, and P2O5 in decreasing concentrations (Givi, Rashid, & Aziz, 2010). The majority of rice husk applied as feed for livestock in Malaysia. However, the rice husk has limited applicability in stock-breeding, because it contains more than 70% of lignin-cellulose material and more than 20% of amorphous SiO2 (Habeeb, & Mahmud, 2010). Rice husk removal during rice refining, creates disposal problem due to less commercial interest. Most of them are not practically use and significantly hazardous to environmental problem because of burning of rice husk. Industries use rice husk as fuel in boiler and power generation, the smoke generated because of burning often has unfavourable consequences on domestic as well as international environmental problems. Rice husk is generally not appropriate as cattle feed since its cellulose and other sugar contents are low. Rice husk are the major constituents of rice husks are cellulose, hemi-cellulose, lignin and ash (Uzunova, & Angelova, 2013). The ash mainly consists of silica (SiO2) and some alkali metal impurities. The chemical composition of rice husk is similar to that of many common organic fibres and it contains of cellulose 40% to 50%, lignin 25% to 30%, ash 15% to 20% and moisture 8%- 15% (Govinda, 2007).
Problem Statement
The problems statements are:
Rice husk will be burned in open air or land fill but both approaches emit large quantity of CO2 to the atmosphere. Removal of these agro-wastes develop a destruction problem because of lack of commercial interest.
Most of them are not practically use and significantly hazardous to environmental problem because of burning of rice husk.
Transportation and treatment of agro-wastes are uncertain due to lack of density.
Commercial use of rice husk is the alternative solution to disposal problem.
Research Questions
Leaching treatment is a proper route to extract the silica. Organic acid which is Citric acid (C6H8O7) and Inorganic acid; Hydrochloric acid (HCL) solution are conventionally used in leaching treatment to prepare the silica material. Hence, by using the citric acid and hydrochloric acid in leaching treatment may overcome the extraction of silica from rice husk that are dangerous for environmental and human’s health. The objectives of this research were to study the effect of acid treatment in extraction of silica from rice husk using organic and inorganic acid leaching method and to obtain the optimum parameter of leaching treatment in extraction of silica from rice husk.
Purpose of the Study
This paper is focused on extraction of silica from rice husk by using an inorganic acid, hydrochloric acid (HCL) and organic acid, citric acid (C6H8O7).The performance of this research is covered on characterization studies which are Field emission scanning electron microscopy (FESEM), X-ray fluorescence (XRF) spectroscopy, and X-ray diffraction (XRD) spectroscopy analysis. Chemical study for this research is covered by acid leaching treatment to determine the different concentration of acids and different leaching time to extract silica from rice husk. The acid solutions used in this research are hydrochloric acid (HCL) and citric acid (C6H8O7). Both concentrations of reagents were varied from 0.1M, 0.5M and 1.0M while for leaching time varied 30 minutes, 60 minutes and 90 minutes.
Research Methods
Rice husk from Perlis is used in this research. It was supplied by BERNAS Company in rice straw form into powder. In this stages, rice husk was grinded by using Planetary Ring Mill (Malvern Panalytical) for 3 minutes at rotational speed of 600 rpm to become fine powder before acid leaching process.
About 15 grams of rice husk powder were stirred together with 500ml of hydrochloric acid (HCL) solution in a beaker. Different sample were prepared at different acid concentration which is 0.1M, 0.5M and 1.0M. The beaker was placed on the hot plate magnetic stirrer and the reaction time recorded was 30 minutes, 60 minutes and 90 minutes. This step was repeated using citric acid solution. The hydrolysis of polysaccharides such as cellulose and hemi-cellulose is depending on these parameters. After the acid leaching process, the water rinsing treatment of the rice husk was carried out with the distilled water at room temperature to remove the citric acid and hydrochloric acid content from the husk. The materials were dried at 60 for 60 minutes in the furnace (Faizul, Abdullah, & Fazlul, 2014).
Findings
6.1.Visual Observation
Figure
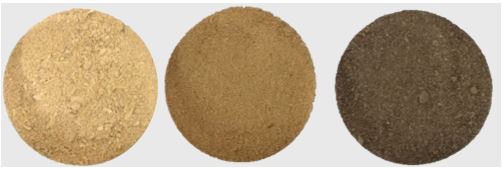
Figure
6.2. Chemical composition analysis of untreated rice husk (RH).
Two types of citric acid and hydrochloric acid were used. The chemical composition was analysed by using X-ray fluorescence spectrometer (XRF) shown in Table
6.3. Chemical composition analysis of treated rice husk (RH) using citric acid solution.
Table
As shown in Table
6.4. Chemical composition analysis of treated rice husk (RH) using hydrochloric acid solution.
Table
The adsorption of silica from rice husk which in-leaching with hydrochloric acid (HCL) also increased. Hence, it is shown in this table that hydrochloric acid (HCL) leaching treatment is significantly useful and efficient compared to citric acid solution to remove impurities and increased the purity of silica in rice husk. This is due to weight percentage of silica form rice husk that leached with hydrochloric acid (HCL) is higher than citric acid. This research can be conclude whether weight percentage of HCL is higher than citric acid, both are significantly better at remaining of silica and removing these impurities. This table can be explained that silica can be extracted more or absorbed using HCL solution compared to citric acid solution. This is due to leaching with hydrochloric acid (HCL) can dissolve inorganic impurities such as metals contained in rice husk up to enlarge the pores. When the pore is increased, the surface area of the material increased as well.
6.5. Phase Analysis of Untreated Rice Husk (RH).
The phase analysis was made by X-ray diffraction analysis for rice husk with Cu Kα radiation in 2θ range between 10° to 70°. While the step scan were performed with 2° per minutes. At y- axis, it shows the intensities of the peak and x –axis is the range of phase in 2θ. XRD analysis was carried out for rice husk, RH and give a resulting in amorphous structure as shown in Figure
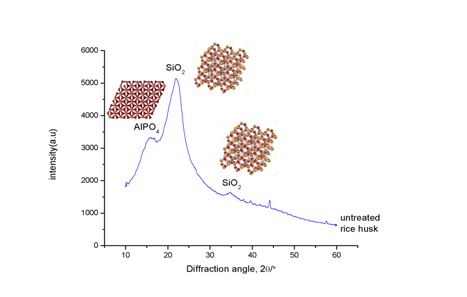
6.6. Phase analysis of treated rice husk (RH).
Figure
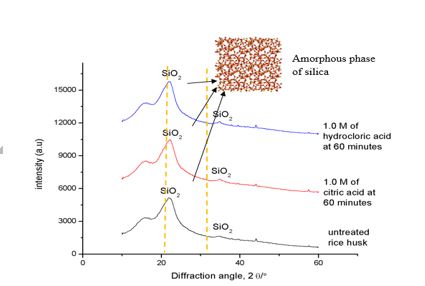
6.7. Morphology Surface Analysis
Field emission scanning electron microscopy (FESEM) provides information on the morphology, topography, composition and crystallography of the rice husk. Hence, Field emission scanning electron microscopy (FESEM) provides topographical and elemental information at magnifications of 10X to 300,000X with virtually unlimited depth of field. Untreated rice husk and both chemically treated (1.0 M of citric acid and 1.0 M of hydrochloric acid) were examined by Fourier Electron scanning electron microscopy (FESEM) in order to find out the effect of chemical treatment on silica. Figure
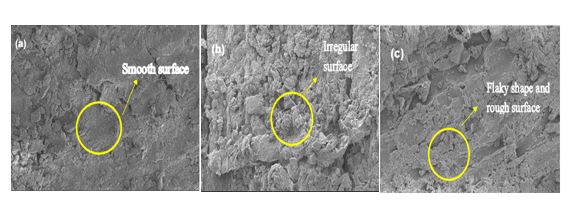
From Figure
The silica and metallic impurities distribution of both acid leaching treatments were analysed by using EDX and results are presented in Figure

The silica and metallic impurities distribution of both acid leaching treatments were analysed by using EDX and results are presented in Figure
Conclusion
The properties of silica dioxide (SiO2) produced via acid leaching treatment process has been studied. The extraction of silica is obtained by grinding the rice husk through powder. Then the samples were stirred with 1.0 M of citric acid and 1.0 M of hydrochloric acid for 60 minutes. In this study, for characterization techniques, 18 samples were analysed using XRF and it is proven that highest silica content of rice husk increased from 82.8 % to 99.3% by 1.0 M of HCL at stirring time of 60 minutes and 82.8 % to 98.6 % by 1.0 M of citric acid at stirring time 60 minutes after leaching treatment. These samples can be used as alternated material for silica source. The silica extraction and its morphological study are done by using FESEM. Amorphous silica is observed. The recycling of major disposal product of rice husk was developed. Hence, untreated rice husk shown that SiO2 consist of smooth surface and for sample of 1.0 M citric acid showed the surface is rough and particulates. Sample of 1.0 M of HCL showed the surface is in flaky shape at the SiO2 particles and rough in surface. Through XRD, it has been proven all these samples are in amorphous phase.
References
- Faizul, C. P., Abdullah, C., and Fazlul, B., (2014). Extraction of Silica from Palm Ash Using Organic Acid Leaching Treatment. Engineering Materials, Vol. 594-595, pp. 329-333.
- Farshid G., Maryam M., and Ali M.S. (2015). Production of Silica Nanoparticles from Rice Husk as Agricultural Waste by Environmental Friendly Technique. Journal of Industrial and Engineering Chemistry, Vol. 50, pp. 79-85.
- Ghosh, R., and Bhattacherjee, S. (2013). A Review Study on Precipitated Silica and Activated Carbon from Rice Husk. Chemistry Engineering Process Technology, Vol. 4, pp. 150-156.
- Givi, A. N., Rashid, S. A., and Aziz, F. N. A. (2010). Contribution of Rice Husk Ash to the Properties of Mortar and Concrete: A Review. American Science, Vol. 6, pp. 157-165.
- Govinda, V. M. H. (2007). Silicon Oxide (SiOx, 0<x<2): a Challenging Material for Optoelectronics. Scientific and Industrial Research, Vol. 39, pp. 495–501.
- Habeeb, G. A., and Mahmud, H. B. (2010). Study on Properties of Rice Husk Ash and Its Use as Cement Replacement Material. Material Research, Vol. 13, pp. 185-190.
- Uzunova S., and Angelova D. (2013). Liquid-Phase Sorption of Oil by Carbonized Rice Husks: Impact of Grain Size Distribution on the Sorption Kinetics. Journal of Chemical Technology and Metallurgy, Vol. 48(5), pp. 505-512.
Copyright information
This work is licensed under a Creative Commons Attribution-NonCommercial-NoDerivatives 4.0 International License.
About this article
Publication Date
17 May 2019
Article Doi
eBook ISBN
978-1-80296-061-7
Publisher
Future Academy
Volume
62
Print ISBN (optional)
-
Edition Number
1st Edition
Pages
1-539
Subjects
Business, innovation, sustainability, environment, green business, environmental issues
Cite this article as:
Jamil, N. H., Abdullah*, S. A., & Zarib, N. S. M. (2019). Extraction Of Silica From Rice Husk Via Acid Leaching Treatment. In M. Imran Qureshi (Ed.), Technology & Society: A Multidisciplinary Pathway for Sustainable Development, vol 62. European Proceedings of Social and Behavioural Sciences (pp. 175-183). Future Academy. https://doi.org/10.15405/epsbs.2019.05.02.16