Abstract
The considered model allows developing and implementing labor safety management systems, which reduce the professional risks of staff and in the medium and long term affect the prospects for enterprise efficiency. An effective management tool is a system of safety indicators when it is focused on results, on goals, and not on collecting statistics on the current state of affairs. Indicators should be formed for specific goals set by the business. Strategic planning used in enterprise activities is the efficient methods. Strategic planning as a means of compensating accidents has the impact if it influences all spheres of the enterprise. It can clear up the uncertainty, predict the appearance of bottlenecks in the production cycle, identify the danger in advance and develop a set of compensating measures, a plan for using and connecting reserves. Damage prevention methods reduce damage by preventive measures. Methods aimed at minimizing losses include the mandatory compliance with the requirements of regulatory and technical documentation, labor and production discipline. The most effective methods of this type include the method of strategic planning used in enterprise activities. Strategic planning as a means of compensating accidents is effective if it influences all areas of the enterprise. It can clear up the uncertainty, predict the appearance of bottlenecks in the production cycle, identify the danger in advance and develop a set of compensating measures, a plan for using and connecting reserves. A variation of this method is prediction of accidents and incidents.
Keywords: Professional risksconceptual modelmanagementeconomic aspects
Introduction
The general economic trend to increase production and labor efficiency, announced in the Russian Federation, makes enterprises, on the one hand, increase the specific output per employee, using more efficient technologies, and reduce costs, including ensuring labor and industrial safety. The costs of labor and industrial safety, as a rule, cannot be attributed in the management reporting to projects or work that bring profit, but an understanding of the costs of reducing the risks from unplanned losses associated with any incidents still finds its place in the actions of the top - management of Russian companies in the real sector of the economy (Vorotnikov, 2008).
Of course, it should be noted that modern technologies are more efficient both in terms of energy and environmental impact, and often require fewer employees due to wider automation, robotization and the use of digital technologies. But, nevertheless, the use of “deserted” technologies cannot be called a panacea due to high capital costs and the impossibility of extending these technologies to all types of activities of various organizations.
It is advisable to consider from the point of view of statistical data and assess the risks of lower revenues and profits due to accidents at work, fatal injuries. So, for the Russian Federation, these risks acquire quite definite interest on GDP, which, together with slightly higher data on injuries and lower life expectancy, only reinforces the negative impact on the unsatisfactory state of labor and industrial safety.
There are multidirectional trends - with an annually increasing growth rate of financing preventive measures, the number of victims, including those who died in production, does not increase, but does not fall in proportion to the increase in costs. It is reflected in statistical data demotivate the management of companies to increase costs, which already make up a significant share in the budget of companies. Both the measures to improve production efficiency and further reduction in costs and risks in the field of labor safety requires multiply large financial investment and use much more complex technologies, including labor risk management systems (Thomason & Pozzebon, 2002).
Problem Statement
The systemic work on labor safety is not limited to an increase in costs on personal protective equipment or the implementation of an action plan for Labor and Industrial Safety Department, as well as the creation of a department with several specialists who are competent in their field. The labor safety activities should permeate the activities of all departments of the enterprise, such as production or administrative management departments (Hersch & Pickton, 1995).
In this regard, the costs (Timofeev, Shlychkov, & Nestulaeva, 2017), traditionally attributed to labor safety and considered to be an unreasonable burden on the budget of organizations, are investments in business development, increasing its production (operating) efficiency.
In modern times, efficiency indicators are being tried to digitize to reflect the tangible, natural result, expressed in units, percentages, reflecting both the actual value and the trend in a few years' retrospective (Wang, Liu, & Liu, 2018).
The main value of using a system of performance indicators in business is that it can become an effective tool for managing the achievement of goals and objectives.
Currently, a set of labor safety performance indicators:
is not related to the business strategy of the enterprise;
does not measure the quality of results and processes;
does not contain cost indicators that are clear and necessary for the management and owners of enterprises;
is static (usually does not change from year to year);
does not have managerial value (does not stimulate decision-making);
reflects not the labor safety management system, but only its individual parts.
An effective management tool is a scorecard when it is focused on results, on goals, and not on collecting statistics on the current state of affairs. Performance indicators should be formed for specific goals set by the enterprise.
The system of labor safety performance indicators as a management tool should allow:
formulating tasks and expressing them quantitatively;
communicating tasks in vertical management at all levels (tree of performance indicators and standards “becomes a tool for the coordination of strategic and operational plans);
monitoring and measuring results (the degree of achieving goals);
diagnosing problems that require management intervention (indicators of problems);
carrying out the adjustment of goals in case if it is impossible to achieve them, thereby improving the quality of planning;
delegating authority;
comparing the objects of the enterprise;
evaluating the level of management and the efficiency of departments.
Developing the above, labor safety management systems are represented not only by employees of the labor safety department, but also by line managers of departments (Vedin, Shlychkov, & Khasanova, 2015).
Research Questions
Ensuring safety at the enterprise with hazardous production facilities is one of the priorities. In turn, the labor risk identification and management is fundamental in the security system. There is a question about the efficiency of professional risk management in production activities.
Purpose of the Study
The purposes of this study are:
Study the efficiency of labor risk management systems.
Develop a conceptual model of professional risk management.
Research Methods
When conducting the study, the following research methods were used: synthesis, comparison and system analysis.
Findings
Labor safety management systems are represented not only by employees of the labor safety department, but also by line managers of departments. At the same time, other services of enterprises whose responsibility is to eliminate the causes of these incidents should reduce the loss of working time due to injuries and occupational diseases (Sartawi, Hindawi, Bsoul, & Ali, 2014):
Labor and production management - rationalizes workplaces to ensure labor productivity, quality and safety of labor; rationalizes labor and production processes or eliminates them, as they are not creating added value and being, as a rule, reasons for injury;
Repair and maintenance of equipment - develops systems for the defect-free operation of technological equipment;
Chief technologist - rationalizes and optimizes technological processes;
Staff development - improves the quality of employee training; employee motivation for productive and defect-free work; measures to ensure the labor and production discipline of workers;
Other services that solve security problems.
Of course, all these services carry out activities according to their plan, but business tasks to reduce the level of losses, including those caused by injuries and occupational diseases, become priorities in this plan and they are synchronized by facilities, deadlines and funding levels.
From this point on, the “task tree” begins to intensively “branch out”, moving to the level of individual functions providing tasks, and then to a set of indicators and standards. Under the leadership of Labor Safety Department, an operational plan to implement assigned tasks is drawn up and a budget for labor and industrial safety measures is approved.
It is worth paying attention to another important feature: the scorecard should be a dynamic model. First, it is important to see the prospects for development and the pace of progress. The dynamic model (Nowrouzi et al., 2016), compiled for the medium term (2-3 years) or long-term perspective implies an onward movement towards the goal, including the development factor.
The business goals of the enterprise may change. Respectively, this should be reflected in the tasks of Labor and Industrial Safety Departments and in the list of performance indicators, their values. The second element of dynamism is a change in performance indicators over time. It is extremely dangerous to set unattainable standards. This demotivates staff and challenges the progress.
The performance indicators stand out in accordance with the following principles (Gridin, 2017):
They reflect business goals that are priorities for labor safety management of the enterprise;
They should include cost indicators (top managers operate with economic categories, such as a “cost”);
It is advisable to include a number of performance indicators used in world practice (for comparison with international experience);
Basically, they should be performance indicators, not process performance indicators. First of all, it is necessary to establish a clear accounting of costs and losses of labor and other non-production costs and to train specialists in effective methods of analysis, planning and works on their prevention and elimination.
Damage, loss is an undesirable change in the qualities of the security object, a decrease in its value to the subject or its complete loss (Glebova, Volokhina, Ivanova, & Korobov, 2018).
The level of probable losses is usually determined (calculated) in absolute or relative values. In absolute values, the cost of damage can be estimated in physical, material (kg, hours, kW) or value terms. In relative values, the magnitude of losses is correlated with some base, for example, with the value of assets of the enterprise (fixed and circulating assets), the value of total costs of the enterprise for this type of activity. Material losses occur most often on the basis of errors in the planning of dangerous actions of contractors, violations of technological requirements, accidents, breakdowns, natural disasters, etc. They are manifested in additional costs or direct losses of equipment, property, products, raw materials, energy, etc. For each of the listed types of losses, there are different physical units of measurement (m, kg, kW / h, etc.) therefore, for convenience of calculation, cost indicators are used. To this end, losses in the physical dimension are converted into value by multiplying by the price of a unit of the corresponding material resource.
Labor losses arising from equipment downtime, illness, violations of labor discipline, low work organization, etc., are measured in man-hours, man-days, or simply in working hours. Their conversion into value indicators is carried out by multiplying the labor hours by the cost (price) of one hour (Kumar, 2013).
Financial losses can arise from the payment of fines, payments not provided for in advance, for example, an increase in social security contributions as a result of unsatisfactory security activities. There may be a loss of time, which appear under the influence of both objective circumstances and lead to a prolongation of deadlines for achieving the goals set by the business plan. Such losses are expressed in hours, days, months, and in terms of value, in the reduction of income, profit.
In the process of analyzing damage, the main thing is to identify its price or severity of consequences. This can be estimated by the ratio of possible losses to free assets, which can be called the price.
The first step in estimating losses is to identify their event. The event of a loss is not only the event that can cause losses, but also the determination of the maximum price of damage, i.e. the probable amount of possible losses for this particular event. While this event is unknown, it is impossible to establish the size of losses which can seriously reduce assets of the enterprise. In determining the event of loss, both damage that may be caused to the property of the enterprise and the undelivered commercial and social benefits (for example, lost profits) are summarized.
If losses occur, even if they are insured, they may not be fully covered by insurance payments. For example, most enterprises often do not insure possible loss of profits as a result of an unforeseen interruption in business, as a result of an accident, or insurance reimburses the actual cost of lost, partially obsolete property, and new property, if acquired for reimbursement, and it will require large costs. For some statistical risks, especially those associated with the action of the forces of nature, with the departure of key personnel figures or being universal, the probability of their occurrence is a function of time in most cases.
Damage reduction tools can include incentives, organizational measures, and methods for managing damage.
Based on the analysis of the applied damage management methods, they can be grouped and presented schematically, see Figure
Minimization of losses;
Compensation of damages.
Methods of minimizing losses can reduce the magnitude of damage when accidents cannot be avoided or they suddenly occur.
Prevention methods allow protecting yourself from accidents with the help of preventive measures.
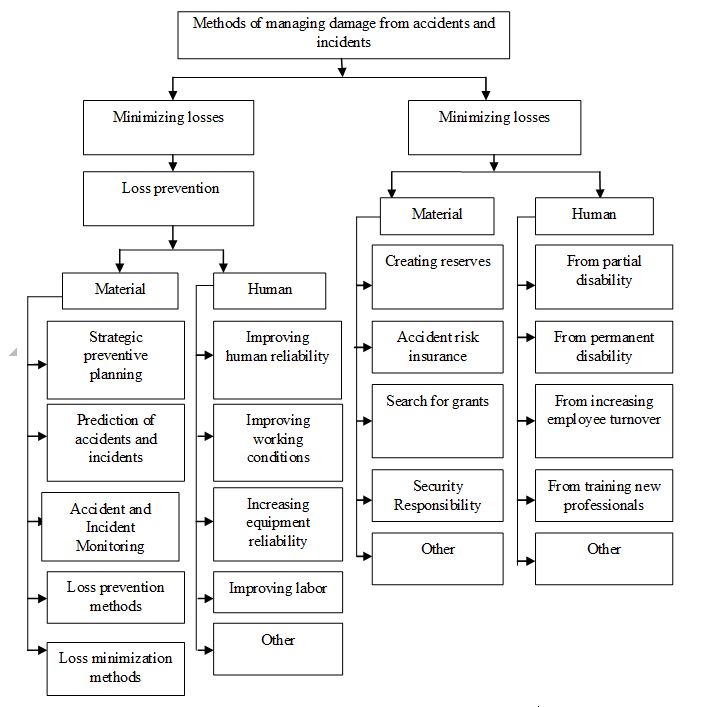
These methods are more laborious, require extensive, analytical work, and the efficient implementation depends on their completeness and thoroughness.
The most effective methods of this type include the method of strategic planning used in enterprise activities. Strategic planning as a means of compensating accidents is effective if it influences all areas of the enterprise. It can clear up the uncertainty, predict the appearance of bottlenecks in the production cycle, identify the danger in advance and develop a set of compensating measures, a plan for using and connecting reserves. A variation of this method is prediction of accidents and incidents.
The essence of this method is:
Periodical development of scenarios and assessment of damage from accidents and incidents;
Forecasting the occurrence of dangerous situations.
The main goal of the method for monitoring accidents and incidents is informatization of the enterprise.
Damage prevention methods allow reducing damage by preventive measures (installation of an alarm system and acquisition of fire extinguishing agents, etc.).
Methods aimed at minimizing losses include mandatory compliance with the requirements of regulatory and technical documentation, labor and production discipline, etc.
Minimizing casualties is achieved in the following ways:
Improved human safety is achieved by ability test, training of professionally significant qualities, professional training, motivation for safe activities and a number of other measures;
Improved working conditions are carried out on the basis of their diagnosis - a special assessment of working conditions. It is carried out by concluding a collective agreement, which includes improving working conditions, measures and a long-term plan, which forms the strategy of such activities;
Improved equipment reliability is achieved by performing preventive maintenance after diagnostics and replacing outdated equipment with modern, more efficient or technological equipment;
Job enrichment is primarily carried out by optimizing all forms of control activities and carrying out a number of other activities (training, provision of personal protective equipment, etc.);
Digitalization of processes (up to the use of augmented reality, for example, when assembling complex products);
Application of unmanned technologies and robotization.
The second group includes methods of compensation for damage. They are aimed at ensuring that, in the event of losses, they will be recovered (even partially) and it will prevent them from rolling beyond the critical limit.
The method of a system development of reserves is close to insurance, but is concentrated within the enterprise itself. The enterprise creates insurance reserves of raw materials, components, reserve funds, it plans for their deployment and use in crisis situations (Darus, Mad, & Nejati, 2015).
Preference is given to financial reserves, which may be in the form of:
Accumulation of own cash insurance funds;
Development of “hot” credit lines;
Use of collateral, etc.
Methods of risk levelling through insurance mechanisms are widely used in high-risk facilities. Insurance is mandatory, which is enshrined in current legislation.
The guarantor’s search method involves enterprises’ appeal to large commercial banks, insurance companies, associations, foundations, and large enterprises, respectively, appeal to government bodies for support and patronage. The guarantor’s services are political support services, trouble-free charity, etc.
The method of distribution of responsibility for ensuring security between officials is formed as official duties and is determined by the requirements of regulatory and technical documentation.
Methods of compensation for human damage are as follows. The method of compensation for losses in case of partial disability provides for the creation of a reserve of workplaces with lightweight working conditions.
The method of reducing losses in staff turnover is to create a personnel reserve for “key” positions in production by mastering the working related professions.
The method of training new specialists involves the training of the most significant specialists in production and is implemented in training centers from among the young workers.
Socio-economic damage from accidents and other incidents consists of the amount of damages [15]:
and the statistical expectation of the total damage value M [Y], which is determined by various combinations of the above incidents, calculated by the following, more complex formula:
where , - the number of jobs in the labor process, and their number with the incidents, respectively; , , and - probabilities, respectively, of the occurrence of a specific incident, some damage from it and the extent of such damage.
Conclusion
The considered model allows developing and implementing labor safety management systems, which increases the level of personnel safety and in the medium and long term affects the prospects for enterprise efficiency.
References
- Darus, F., Mad, S., & Nejati, M. (2015). Influence of internal and external pressure. Procedia Economics and Finance, 28, 183–189.
- Glebova, E.V., Volokhina, A.T., Ivanova, M.V., & Korobov, A.V. (2018). Reducing professional injuries in the fuel and energy complex enterprises by conducting a behavioral safety audit. Life Safety, 8, 13-17.
- Gridin, A.D. (2017). Economic aspects of labor protection. Bulletin of the Russian Academy of Natural Sciences, 1, 53-55.
- Hersch, J., & Pickton T. (1995). ‘Risk-taking activities and heterogeneity of job-risk trade-offs’. Journal of Risk and Uncertainty. 11(3), 205–217.
- Kumar, G. (2013). Voluntary disclosures of U.S.-listed Asian companies. Journal of International Accounting, Auditing and Taxation, 22 (2), 109–118.
- Nowrouzi, B., Gohar, B., Nowrouzi-Kia, B., Garbaczewska, M., Chapovalov, O., Myette-Cote, E., & Carter, L. (2016). Health and safety in small and medium-sized enterprises: a descriptive exploratory study in Ontario, Canada. International Journal of Occupational Safety and Ergonomics, 22 (3), 360-366.
- Sartawi, I., Hindawi, R., Bsoul, R., & Ali, A. (2014). Jordan firms listed on the Amman Stock Exchange. International Business Research, 7 (6), 67–82.
- Thomason, T., & S. Pozzebon (2002). ‘Determinants of firm workplace health and safety and claims management practices’. Industrial and Labor Relations Review 55(2), 286–307.
- Timofeev, R., Shlychkov, V., & Nestulaeva, D. (2017). Methods of economic reliability. SHS Web of Conferences, 35, 1-4.
- Vedin, N.V., Shlychkov, V., & Khasanova, A., (2015). Discursive Practices in Cooperative Structures. Indian Journal of Science and Technology, 8 (S10).1-10.
- Vorotnikov, A.V. (2008). Economic benefits from labor protection measures. Labor Safety, 1, 31-33.
- Wang, Q., Liu, X., & Liu, S. (2018). Study on the Influence of Government Intervention on the Occupational Health and Safety (OHS) Services of Small- and Medium-Sized Enterprises (SMEs). BioMed Research International, 1, 1-12.
Copyright information
This work is licensed under a Creative Commons Attribution-NonCommercial-NoDerivatives 4.0 International License.
About this article
Publication Date
20 March 2019
Article Doi
eBook ISBN
978-1-80296-056-3
Publisher
Future Academy
Volume
57
Print ISBN (optional)
-
Edition Number
1st Edition
Pages
1-1887
Subjects
Business, business ethics, social responsibility, innovation, ethical issues, scientific developments, technological developments
Cite this article as:
Alekina, E., Ovchinnikov, K., & Minina, Y. (2019). Conceptual Model Of Professional Risk Management. In V. Mantulenko (Ed.), Global Challenges and Prospects of the Modern Economic Development, vol 57. European Proceedings of Social and Behavioural Sciences (pp. 1561-1569). Future Academy. https://doi.org/10.15405/epsbs.2019.03.159