Abstract
The use of new technology in order to achieve real improvement and to increase productivity in a business can be effective in the long term only through the correct analysis of the current status of the business. After the current status is detected, the improvement studies should be continued towards the existing constraints and the studies for eliminating new constraints that will occur at certain time intervals should be repeated. Unless improvement can be sustained, long-term solutions cannot be in question. In family foundations or charitable foundations; factors such as close relationships, special connection, and lack of education come to the forefront, and bulky organizations prevent innovative developments. There is a need for approaches that see the business as a whole and predict the future by uncovering the real situation. One of them is Theory of Constraints. In this paper, a case study is presented in which the problems arising from production and planning, sales and management mistakes in a food business, which is a charitable foundation, were elevated with the application of Theory of Constraints. In the study, the steps such as Current Reality Tree, the Evaporating Cloud and the Future Reality Tree from the Thinking Process were realized. As a result of putting the recommendations into practice, significant improvements were made in the business under examination.
Keywords: Theory of constraintsthinking processcurrent reality treefuture reality tree
Introduction
In today's competitive environment, businesses resort to new management approaches in order to sustain their existence and increase their profit share. However, before a fundamental change is made in the business, it is necessary to analyze in detail whether the resources are used effectively, whether the correct and effective management is implemented, whether processes are effectively designed and operated, and so on. Regardless of the type of innovation such as use of a new technology, software application, etc., if the business does not have the right operating conditions, the gains will only be superficial and will not make any effective contribution to the operation in the long term. If the operating conditions are not correct, the data will be reflected precisely onto new investments. As a result, no technology that is run with these data will create a strong improvement in the real system.
For a real improvement; the current situation of the system/business should be analyzed frequently, the mistakes and errors should be revealed along with their causes, the sources of wastage and other wastes should be identified, bottlenecks in the processes should be defined, the situation should be evaluated according to performance criteria, the tendencies and target customers in the market should be re-examined, future predictions should be reviewed, company policies should be reviewed, and a clear decision should be made for parts of the system/business that need correction and improvement in the light of the findings. It should be planned how, under what conditions and by whom these decisions are to be implemented, how long they will take to be answered, and expected benefits should be determined. It is recommended that these steps be repeated periodically for continuous improvement. At this point, it will be possible to make better decisions for new investments/new applications.
Especially in businesses such as family foundations and charitable foundation, human factor is more important than all of the above-mentioned negativities. Factors such as close relationships, special connections, and lack of education arise as a situation that prevents running of the business properly. Some founding managers own the company, do not give anybody the right to speak, do not delegate the authorities, and they are not aware of the fact that they in fact give the biggest damage to their own company to which they feel attached. Or, a few people in business can inhibit innovative developments. It becomes absolutely essential for the future of the system to work with professional managers in such situations
Different approaches and methods are available for revealing the real situation of the business/system and designing the future, such as Value Stream Mapping, Motion and Time Studies, Work Study, Cause-Effect diagrams, simulation, process analysis, design of experiment, etc. One of them is Theory of Constraints.
Theory of Constraints (TOC), developed by Eliyahu Goldratt, is the management philosophy which identifies, governs, and elevates the performance-lowering factors to improve performance in any system, which aims to continuously developing the system by means of synchronized production system, and which is used successfully in production and service sector.
The following part of the study is dedicated to a brief summary of Theory of Constraints. It continues with the implementation part which describes removal of the problems arising from production and planning mistakes in the food business, which is a charitable foundation, by using the TOC. Finally, the conclusion of the study is given.
Theory of Constraints
Theory of Constraints (TOC) is originally a management philosophy put forward by Dr. Eliyahu M. Goldratt. The departing point of the TOC is the assumption that constraints determine the performance of a firm and each system has at least a few constraints (Tollington 1998; Ruhl 1997). In this case, to understand Theory of Constraints, it is necessary to first learn constraints. A constraint means "any element that prevents achieving of monetization goal by a system" (Umble & Spoede, 1991). TOC is defined as "a management approach that focuses on continuous improvement through management of constraints" (Atwater & Gagne, 1997).
TOC sees the system as a whole and takes the parts forming the system as rings of a chain. A chain is only as strong as the weakest ring, and the chain's power shows the success of the system. The weakest ring constitutes constraints of the system and prevents it from progressing, enhancing the performance, and increasing profitability by affecting the performance of the system negatively.
Goldratt developed a 5-step model (Kohli & Gupta, 2010) for continuous growth to elevate constraints. In this model, inner/outer constraints are first determined by assuming that each system has at least one constraint. In the second step, it is decided how to fix the constraints. If it is a physical constraint like capacity, it can be handled effectively by taking various measures such as reducing downtime, accelerating preparation process, reducing workload, and using additional capacity. However, in the case of non-physical constraints like management, the performance of such constraints cannot be increased. For this reason, when managerial constraints are encountered, the constraints need to be changed or elevated. Also, it is far more difficult to identify and elevate managerial constraints compared to physical ones. However, elevation of managerial constraints certainly gives a higher contribution to the system (Büyükyılmaz & Gürkan, 2009).
In order to improve the performance of the system, the performance of the constraints needs to be increased first. Otherwise, any activity to improve the performance of other resources causes the resources to be wasted. Therefore, in the third stage, it is necessary to manage all the other non-constraint resources of the system according to this goal with the aim of maximizing the performance of the restricted resources. In the fourth step, it is necessary to elevate the constraints in order to enhance the performance of the system. Strategies should be developed to elevate the constraints and decision should be made on which constraints to be elevated. The constraints are elevated by taking the necessary precautions. However, since it is known that there will always be a constraint in the system, the same process is repeated to elevate the other constraints as well by going back to the first step. This cycle provides continuous improvement for the system.
The TOC is a guiding theory. In other words, it answers some of the "why" questions regarding some incidents but also gives guidance about what can be done about it or how it can be used. Some of the TOC principles are as follows (Dettmer 1997; Gaga 2009):
In problem solving and management of change, idea of system is more usable than analytical thinking.
As the system environment changes over time, the most appropriate system solution also differs. An ongoing improvement process should be updated and effectiveness of the solution should be maintained.
The highest performance a system can achieve is not more than the highest of any part of it. The optimum of a system is not the sum of the optimum of the parts.
Systems are similar to a chain. Each system has a weak ring (constraint) and it limits the success of the entire system.
Strengthening any ring other than the weakest ring has no effect on improving the whole system.
Knowing what to change requires a good understanding of the magnitude of the difference between the reality of the system and its goal.
Many of the undesirable consequences in a system are created by one or two fundamental problems.
Fundamental problems are almost never easily seen. If several undesirable outcomes are connected within the cause-effect relationship, the fundamental problems manifest themselves.
Individual elimination of undesirable consequences creates a comfort that will result in elimination of fundamental problems. Such solutions are short-lived. Solving of the fundamental problem also ensures elimination of all associated undesirable results.
Fundamental problems are usually maintained by a hidden or basic contradiction.
System constraints can be political or physical. Physical constraints are easier to detect and destroy than others. It is more difficult to identify and kill political constraints but the system reaches a higher degree of improvement compared to elevation of physical ones.
Inertia is the biggest enemy of continuous improvement process. Current solution is inclined to resist to subsequent changes.
Ideas are not a solution.
TOC is a method that tries to guarantee that process development in a part of an existing system will cause change in the whole system, not just in that process. Basically, TOC offers managers a set of tools to respond to the following questions regarding change (Dettmer, 1997; Köksal, 2004):
What to change? (How should organizations determine the constraints?)
Into what to change? (How should organizations determine practical and good solutions?)
How to cause change? (How should organizations implement solutions?)
There are two processes interacting in TOC understanding: thinking process and thinking implementation process. Thinking process (Nahavandi, Parsaei, & Montazeri, 2011; Ainapour, Singh, & Vittal, 2011) establishes a cause-effect relationship for existing problems in the business. In the implementation process, the determined problems are removed with the help of the diagram of five logical trees. Many tools have been developed that regulate and zoom in TOC-related decision-making systems and focus solutions on the main problem of the system. All of these tools are called “Theory of Constraints Thinking Process” (Dettmer, 1997). Some of these are briefly described below (Köksal, 2004):
Map: Shows the cooperation between processes.
UDE- Undesirable Effects: Indicates how to describe problems.
CRT- Current Reality Tree: A logical structure that shows the current situation. It is used to find the main opposition which leads to cause-effect relationships between undesirable situations.
EC – Evaporating Cloud: Also known as conflict cloud or conflict resolution diagram CRD. This tool includes determining encountered conflicts and underlying assumptions and examining them for resolution purposes. Overriding of these assumptions or displacement with others "evaporates" the conflict. It explains how to find successful solutions in systematic scale.
DE- Desirable Effect: Indicates how to describe the benefits that solutions need to achieve.
FRT - Future Reality Tree: Logical definition of the solution. It is used to predict outcomes of any change.
NBr - Negative Branch: Refers to truncation of inevitable reservations (suspicion) with FRT.
PrT - Prerequisites Tree: It refers to separation of the solution into implementation steps. It is used to uncover and solve situations that prevent achieving the goal.
TrT- Transition Tree: A scheme that is planned for each step of PrT and outlines the steps necessary to achieve the goal.
Each tool developed by Goldratt can be used separately or together in the process of thinking. Three basic questions that managers need to answer about change can be answered using five of the tools together. The table shows the relationship among the five logical tools and the three management questions about change (Dettmer 1997; Gaga 2009; Lakshimi & Rao, 2012).
Goldratt defines Current Reality Tree as a logical structure designed to show the current state of reality in the given system. The Current Reality Tree reflects the possible chain of causes and effects given as a set of specific mixed conditions. This structure seeks the causal relationship between the visible symptoms of the system and the causes that bring them to life. Through creation of the Current Reality Tree, the root problem(s) in the system is/are identified (Watson, Blackstone, & Gardiner, 2007).
The first goal in the Current Reality Tree is to identify the root cause by working backwards from undesirable effects to the cause-effect chain. If the Current Reality Tree can respond to 70% or more of the undesirable effects, this can be defined as Root cause.
Once the TOC practitioner has decided what to change, the second stage in this process is to find a plausible solution to remove the fundamental problem, which is the answer to the question of into what to change. Solution for this problem can be achieved with the help of the Evaporating Cloud and the Future Reality Tree. Unlike the trees, Evaporating Cloud is a cluster of 5 boxes (Goldratt & Cox, 2014). The practitioner defines two opposing wishes that show contradiction with one another, the need behind every demand, and a general goal that both needs try to meet. Then the practitioner reveals the assumptions underlying the links between goal and need and need and demand. This direct contradiction is generally the same as the basic one of the Current Reality Tree. According to Goldratt; while solving these contradictions, managers looked for compromising solutions (which satisfy both of these needs at a certain extent) solutions sought. Goldratt thinks that this approach is very useful to solve the problem without a solution based on compromise (Mabin, 1999).
Future Reality Tree is a tool to visualize and predict the future (Scheinkopf, 1999). After finding a solution called the inoculated idea, which is defined by the evaporating cloud method, the next applications are used to prepare the Future Reality Tree. Using the cause-effect method again, the tree is prepared and carefully examined to test the solution. Future Reality Tree defines what will be changed, also taking into account what impact it will bring to the organization in the future. Collectively reviewing each stage of the Future Reality Tree minimizes the possibilities that solution-makers ignore some significant adverse effects or lose much time on the solution or problems.
Goldratt states “Ideas are not a solution yet” as a principle of the TOC. According to him, before you can define something as a solution, the application must finish and the system must work as intended. The goal of the Prerequisite Tree is to define obstacles to the inoculated idea since the application of evaporating clouds. The Prerequisite Tree is used to uncover and solve situations that prevent achieving the goal. We apply all the ideas in Future Reality Tree to create this diagram. This work requires a considerable team work. A team is formed and it examines the step taken for each target and determines the most appropriate location for this step in the diagram. Each step along with the preceding and succeeding steps is examined individually. All the assumptions made in the diagram are shown on a plan. The Prerequisite Tree is created for each analyzer idea in the Future Reality Tree.
The Transition Tree is a sufficient cause diagram used to create a movement plan. The goal of the Transition Tree is to apply the change (Mabin & Balderstone, 2003). It is a cause-and-effect chain designed to reveal step-by-step processes from identification of undesirable effects to completion of the change (Akman & Karakoç, 2005). The Transition Tree structure allows the Future Reality Tree diagram to be understood by everyone (Kıncal, 2007). While Future Reality Tree is a strategic tool; Transition Tree is an operational or tactical tool and through formation of the Transition Tree, the injections developed in the Evaporating Cloud and Future Reality Tree are implemented, and tactical action plans are created for strategic plans (Yüksel, 2011).
A Case Study for Improving the System Performance
In this research, solving of the problems faced in production and management processes of a company operating in the food sector, with the aid of the Theory of Constraints Thinking Process.
The company in this study is occupied in white meat production, storage and marketing. The enterprise started activities for halal food production in Kurtköy near Istanbul in 1997. Then in 2007, it moved to its new facilities where modern white meat cutting machines are installed on 5000 m2 open area and 3000 m2 closed area in Sakarya. Halal slaughtering is applied in this plant and products are cut into pieces and packaged for marketing in conformity with chicken anatomy. Chicken breeding is outsourced by farmers. The firm has production, marketing, veterinary, accounting, logistics and planning departments. It has 27 dealers and 125 employees throughout Turkey. The firm's current organizational chart is given in Figure
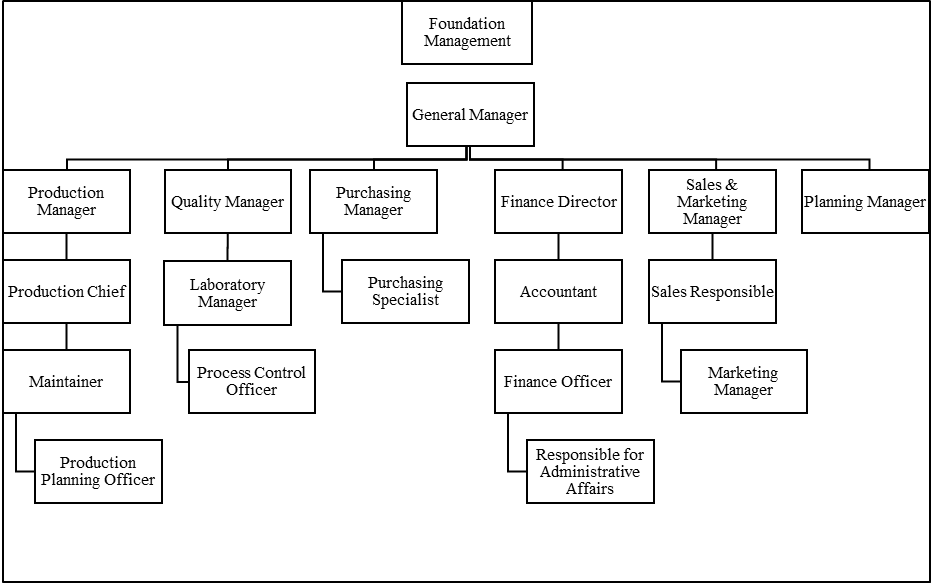
The Thinking Process method focuses on the factors that prevent achievement of the goal. For this reason, a project team consisting of the company manager, the planning supervisor and the employees was established in order to determine the undesirable effects. The troubles in the working systems of the company were detected at round table meetings. In order to get rid of these problems, it was decided to apply the Thinking Process step by step. The project team first received information about the company's current status and activities; and it was found out what the company activities are like, what operations are carried out, and what kind of problems and challenges are encountered. Based on this information from the company, the existing workflow diagram of the company was prepared as shown in Figure
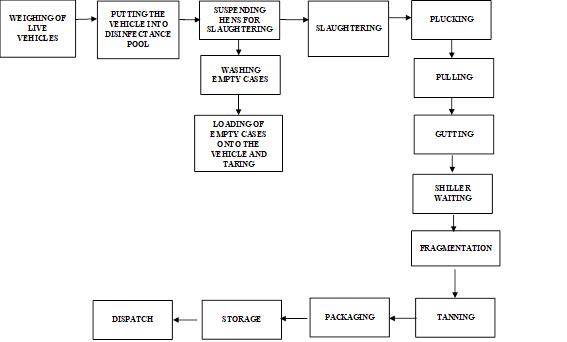
The Thinking Process was implemented as following:
Creating the Current Reality Tree
The first step of Theory of Constraints Thinking Process is the creation of the Current Reality Tree. All the processes of the firm were handled one by one and problems were identified. As shown in Figure
In the market, companies add some additives to feed stuff in order to reduce feed costs and use hot water to facilitate plucking after slaughtering. Unlike others, the company under investigation uses purely natural feed and does not use hot water for plucking. Production with cold water is more difficult than that with hot water because hair removal is easier and quicker thanks to the hot water that comes in contact with the chicken skin. This firm follows its policy so it does not use hot water. This generates higher costs and selling prices compared to other firms in the market.
Consumption rate of each product varies depending on months of the year. For example, the opening of the picnic season increases the consumption of poultry, while the production of poultry decreases during the sacrifice festival. In addition, as separated according to its anatomy, a chicken gives 14 products such as legs, wings, chest, chopped steak, and so on. Sales rates of these products are not equal. For example, chicken grill, tenderloin, butt, chops and wing parts are sold much, whereas sales of the other nine pieces of chicken are not so popular. The marketing department stocks the varieties with a smaller selling rate, which both increases stocking costs and causes accumulation of more than enough goods in the inventory.
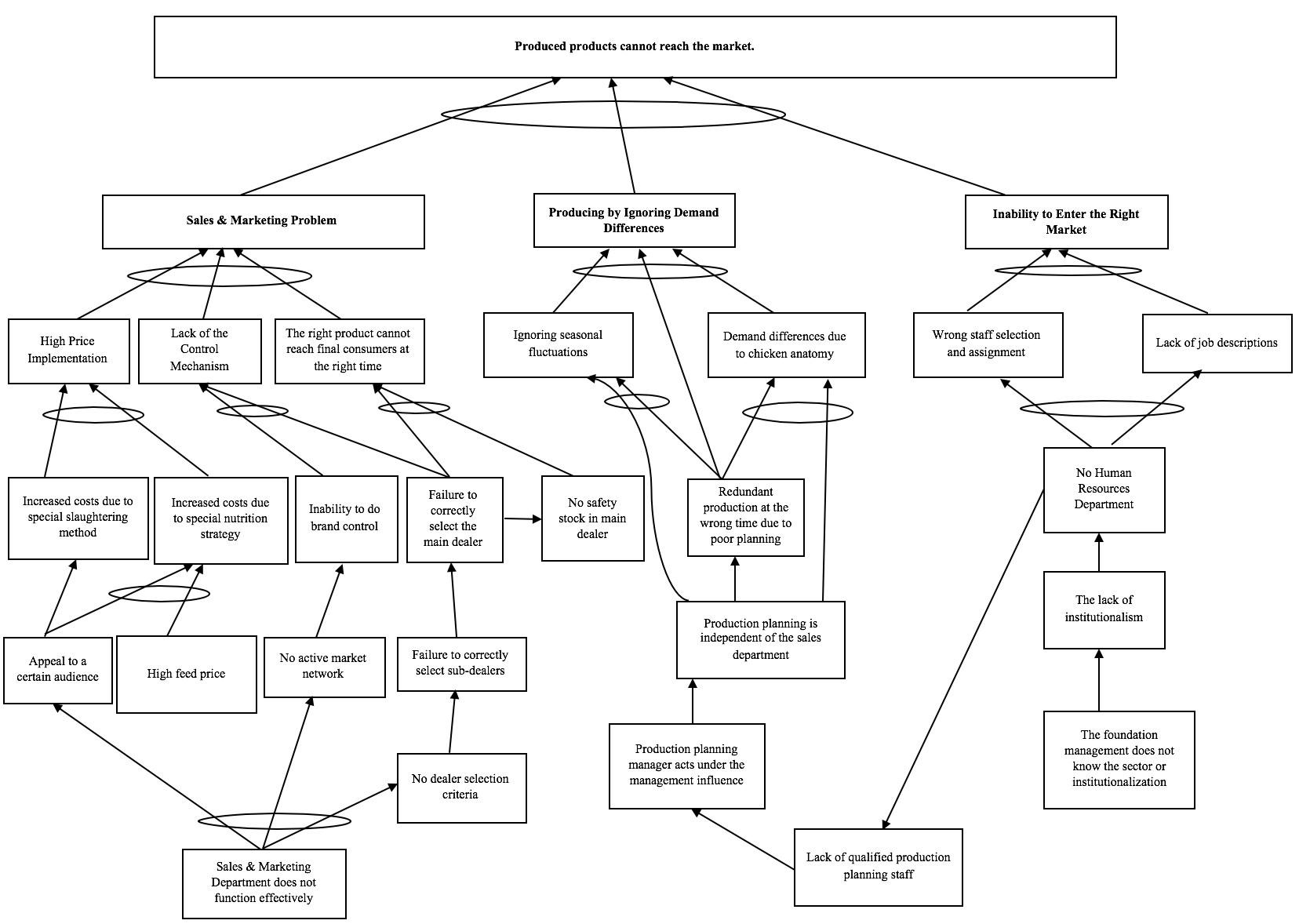
-
The company works with main dealers and sub-dealers to deliver its products to end consumers. As far as its former production capacity concerns, it has not had any trouble with the current dealers. However, it has faced some problems with their dealers as a result of the increased production capacity. For instance, the main dealer does not have enough room to store a certain amount of goods or the dealer does not own cold-chain vehicles for distribution. The main reason for these problems is the lack of dealer selection criteria. Moreover, the lack of a proper dealer system results in ineffective brand control. For this reason, the company is not able to manage its brand in the market or fulfill its responsibilities to its customers. For example; restaurant owners advertise by telling that they use the company's logo and products in their meals to attract the existing customer potential. However, as a result of complaints, it was found out that many of those restaurants are not using the company's products indeed. As a consequence, the products are not delivered to final consumers properly.
-
During production planning, mistakes are made due to the fact that the planning manager ignores sales figures and is close to the foundation management. Because of these wrong plans, redundant production is realized and products are stored. The storage in turn increases the costs incurred by the company.
Since it is a charitable foundation, it is governed in a culture far from the understanding of institutionalism, like many family companies. In addition to this, the foundation management puts pressure on the company management regarding sales figures. The management of the company then has to make production planning accordingly, rather than actual figures of sales. This planning causes excessive production and stocks. Ultimately, blame is put on the marketing department because it cannot sell goods. Therefore, the head of the marketing department is often replaced. A human resources department was not needed when the company was being founded because one employee in the accounting department was in charge of human resources. This person follows only certain aspects of HR such as entrance and exit of staff, annual leave, and overtime. The rest of the tasks of Human Resources are not fulfilled. Over time, with the growth of the company, the lack of Human Resources department caused a chaos because it is not clear exactly who will undertake what job and what sort of a staff will be recruited in each department.
Creating the Evaporating Cloud
The second step of Theory of Constraints Thinking Process is formation of the Evaporating Cloud. The purpose of the arrangement is to present solution proposals to remove the existing Root problem. Evaporating Clouds were applied separately to solve the problems identified within the organization. Examination of the Current Reality Tree revealed the Root causes that need to be evaporated as: High prices of chicken feed, ineffective operations of the sales & marketing department, and foundation management’s limited knowledge of the sector and the idea of institutionalization.
High Feed Prices
Due to the fact that additives in feeds to reduce costs and the use of hot water to facilitate plucking after slaughter as specified in the Current Reality Tree degrade the product quality, this company makes all-natural feed production and complete plucking with cold water only. This increases costs. In order to be able to reduce the costs, feed prices were discounted through bulk purchase of feed. Raising subsidies by increasing sales & marketing activities has helped to evaporate the Root problems (Fig. 04).
Ineffective Operation of the Sales and Marketing Department
The company works with main dealers and sub-dealers to deliver its products to end consumers. As far as its former production capacity concerns, it has not had any trouble with the current dealers. However, it has faced some problems with their dealers as a result of the increased production capacity. For instance, the main dealer does not have enough room to store a certain amount of goods or the dealer does not own cold-chain vehicles for distribution. The main reason for these problems is the lack of dealer selection criteria. A human resources department was not needed when the company was being founded because one employee in the accounting department was in charge of human resources. This person follows only certain aspects of Human Resources such as entrance and exit of staff, annual leave, and overtime. The rest of the tasks of Human Resources are not fulfilled. Over time, with the growth of the company, the lack of Human Resources department caused a chaos because it is not clear exactly who will undertake what job and what sort of a staff will be recruited in each department. For the purpose of enabling the sales & marketing department by eliminating the Root problem here, decision was made to open human resources department and improve qualifications of the current sales & marketing staff through additional training (Fig.05). As a result, evaporation was achieved.
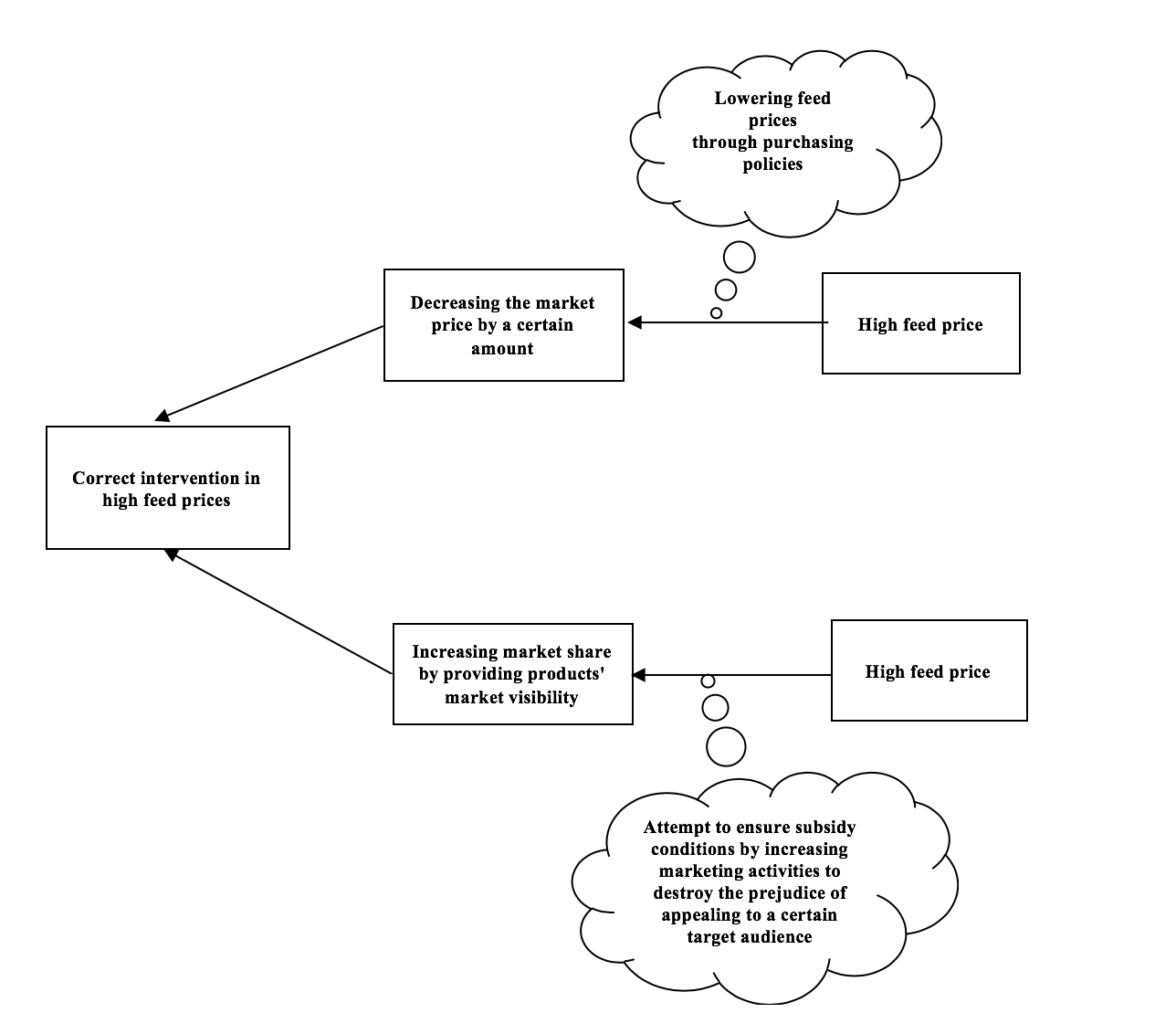
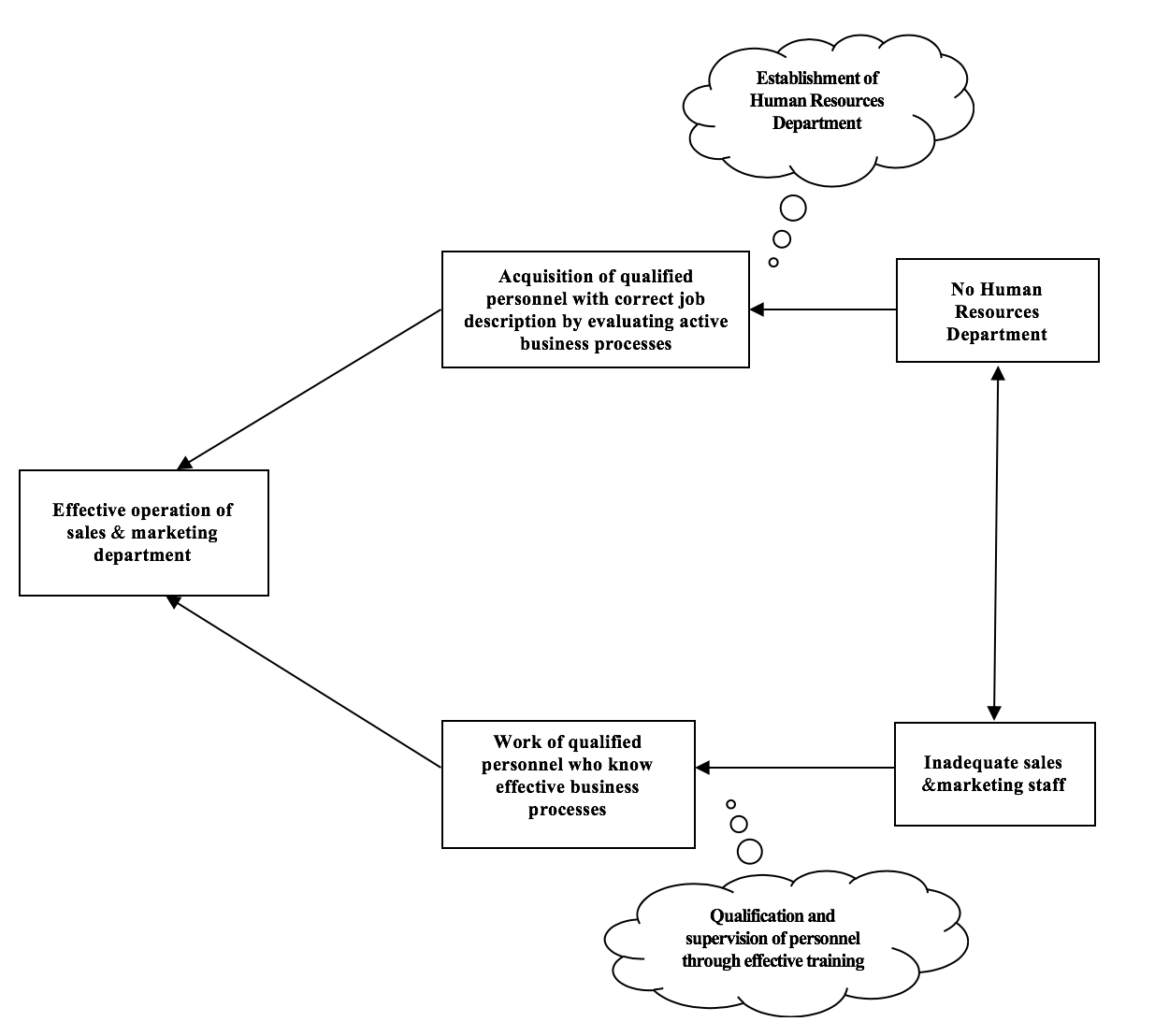
The Foundation Management does not know the Sector or the Idea of Institutionalization
Since it is a charitable foundation, it is governed in a culture far from the understanding of institutionalism, like many family companies. In addition to this, the foundation management puts pressure on the company management regarding sales figures. The management of the company then has to make production planning accordingly, rather than actual figures of sales. This planning causes excessive production and stocks. In order to overcome this Root problem, some measures were taken. To start with, the foundation management was trained by reputable experts about the sector and the management visited the leading companies to hold awareness-raising meetings. In this way, the pressure of the management on the company could be lifted. Apart from that, it was decided to get management consultancy support for internalizing the concept of institutionalism in the foundation management and placing it in the firm well (Fig.06). The Root problem could be overcome in this way.
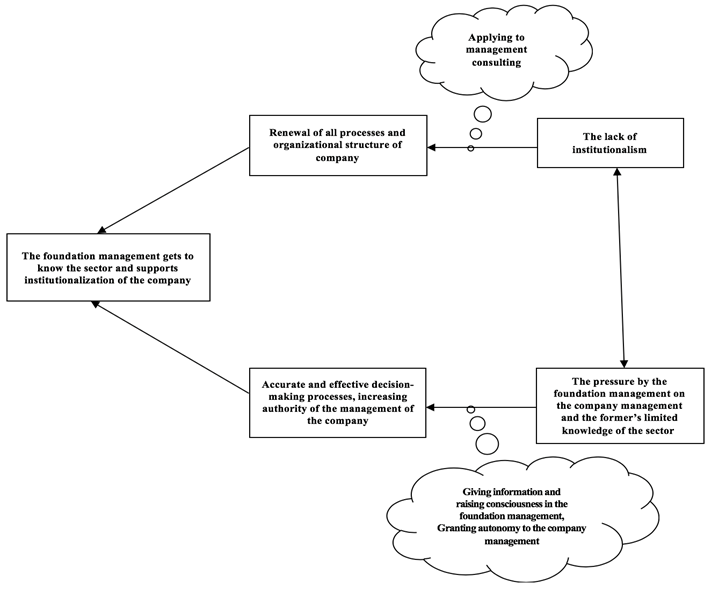
Creating the Future Reality Tree
TOC The third step in the TOC Thinking Process relates to organizing the Future Reality Tree. The Future Reality Tree determines expected impact of propositions of solutions.
Establishment of the Human Resources Department: There is no Human Resources Department in the current organizational chart of the company. For this reason, the employees do not have a clear job description. The Human Resources Department was established to resolve this problem (Fig. 07). Following the establishment of the department, the existing business processes of the company were printed and the job descriptions and organizational schemes were revised as a result of evaluation of the business processes. The company put this work into practice immediately to overcome the problems as soon as possible.
Bad Management Practices: The company has already started cooperation with a firm that gives managerial consultancy and institutionalization works are ongoing.
Problem of Sales: Because the company addresses a certain audience, consumers are still charged with the cost of slaughter and special nutrition. In this respect, preliminary studies are continuing. For example, talks have been started for bulk purchases of feed from abroad to reduce the cost of feed. Also, the foundation and company management have put an additional budget for the next year’s sales & marketing activities.
As a result of correcting the Root causes above, the goal of eliminating the sales & marketing problem was approximated. Furthermore, qualified personnel led to consideration of varying demands, which brought better command of the market facts and thus focusing on the right market. In this way, steps have been taken to convey the products to the target market. Figure
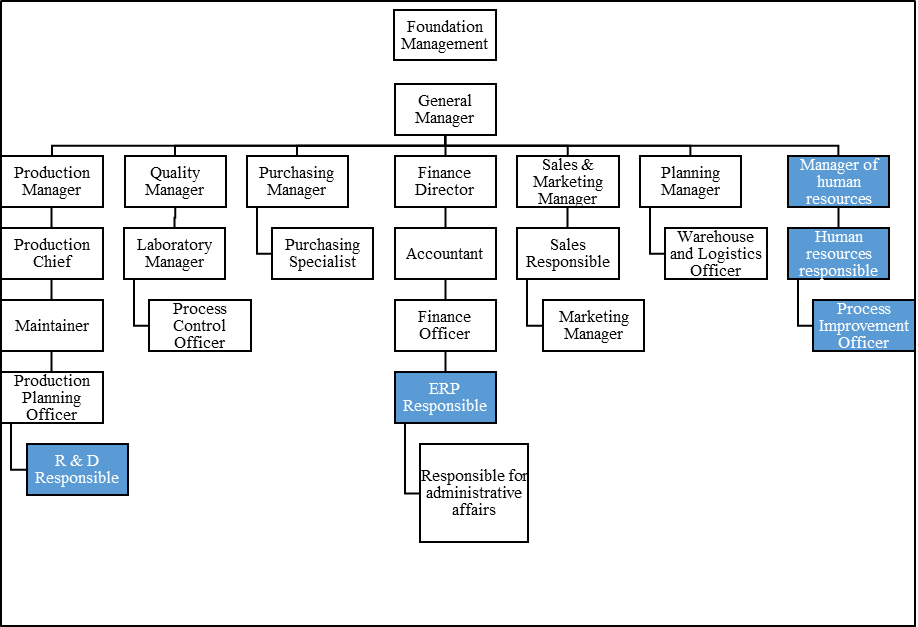
High prices of red meat and unstable meat prices in Turkey have indirectly promoted the poultry sector and facilitated its progress. As a result of the sectoral facts, the supply of chicken meat has increased and companies have started various types of slaughtering and production to hold more shares in the existing market.
The company which is the subject of this research has developed a unique method of slaughtering and plucking. For this reason, it was granted the "Halal Certificate". There is a certain cost due to its unique system. But the firm reflects this cost to consumers. This leads to the product being found in a limited market and its price being seriously higher than its competitors.
Conclusion
Most of the suggestions made in this case study were put into effect. First of all, the foundation management has taken sectoral trainings from a management consultancy firm and initiated institutionalization works. Also, the Human Resources Department was established, business processes were revealed, job descriptions were prepared, and the organization scheme was revised. Besides, qualified personnel recruitment was carried out and existing personnel were given trainings to improve their qualifications. As a result of the modified marketing policy, a wider audience has been targeted and dealers and sub-dealers have been made aware of this issue. As another conclusion, the purchasing policies have been changed and the foundation and company management have planned an additional budget for sales & marketing activities for the next year. Furthermore, preliminary talks have been initiated for bulk feed purchases from abroad to reduce feed costs. Consequently, both the process and the organizational innovation have been realized in the firm.
The improvements above have introduced a different perspective to chicken production activities by means of the TOC Thinking Process in solving problems. If all of the recommendations are realized, the company will increase the market share, ensure customer satisfaction, and increase the profitability. In addition, the company will stop stocking a redundant volume of products. So, the company will incur reduced cost of stocking.

References
- Ainapur, B., Singh, R., & Vittal, P.R. (2011), TOC Approach for Supply Chain Performance Enhancement, International Journal of Business Research and Management (IJBRM), 2, 4, 163-178.
- Akman, G., & Karakoç. Ç. (2005), Yazılım geliştirme projesinde kısıtlar teorisinin düşünce süreçlerinin kullanılması, İstanbul Ticaret Üniversitesi Fen Bilimleri Dergisi , 4(7), 103-121.
- Atwater, B., & Gagne M.L. (1997), The Theory of Constraints versus contribution margin analysis for product mix decisions, Journal of Cost Management, 11(1), 6-15.
- Büyükyılmaz, O., & Gürkan. S. (2009), En zayıf halkanın bulunması: Kısıtlar Teorisi, ZKU Journal of Social Sciences, 5(9), 177-195.
- Dettmer, H. W. (1997), Goldratt’ Theory of Constraints, A System Approach To Continous Improvement, Asqc Quality Press, Milwaukee, Wisconsin Usa.
- Gaga, O. (2009), Süreç Analizi ve Süreç İyileştirme Metodolojisi ve Kısıtlar Teorisi Yöntemiyle Süreç Analizi Uygulaması. Yüksek Lisans Tezi, İstanbul: Yıldız Teknik Üniversitesi.
- Goldratt, E. M., & Cox, J. (2014), The Goal: A Process Of Ongoing Improvement (30 Anv Rev.). North River Pr.
- Kıncal, G. B. (2007), Bir bilimsel makalenin oluşturulma sürecinde Kısıtlar Teorisi: FRT (Gelecek Gerçeklik Ağacı) Uygulaması, Ege Akademik Bakış, 365-377.
- Kohli, A. S., & Gupta, M. (2010), Improving operations strategy: Application of TOC principles in a small business, Journal of Business & Economics Research, 8(4), 37-46.
- Köksal G. (2004), Selecting quality improvement projects and product mixtogether in manufacturing: An improvement of a Theory of Constraints-based approach by incorporating quality loss, International Journal of Production Research, . 42(23), 5009-5029.
- Lakshmi Tulasi, CH., & Rao, A. R. (2012), Review on Theory Of Constraints, International Journal of Advances in Engineering & Technology, 3(1), 334-344.
- Mabin, V. J. (1999), “Goldratt’s ‘Theory of Constraints’ thinking processes: a systems methodology linking soft with hard, systems thinking for the next millennium”, Proceedings of the 17th International System Dynamics Conference and 5th Australian and New Zealand Systems Conference, Wellington, New Zealand, July 20-23.
- Mabin, V. J., & Balderstone, S. J. (2003), The performance of the Theory Of Constraints methodology: Analysis and discussion of successful toc applications, International Journal Of Operations & Production Management, 23(6), 568-595.
- Nahavandi, N., Parsaei, Z. & Montazeri, M. (2011), Integrated framework for using TRIZ and TOC together: A case study, Int. J. Business Innovation and Research, 5(4) 309-324.
- Ruhl, J. M. (1997), The Theory of Constraints within a cost management framework, Journal of Cost Management, 11(6), 16-24.
- Scheinkopf, L. J. (1999). Thinking For A Change, Putting The Toc Thinking Process To Use, St. Luice Press, Usa.
- Tollington, T. (1998), ABC v TOC: Same cloth as absorption v marginal, different style and cut, Management Accounting, 78(4), 44-45.
- Umble, M. M., & Spoede. C. W. (1991), Making sense of managemenet alphabeth soup, Baylor Business Reviev, 9, 26-27.
- Watson, K. J., Blacstone, J. H., & Gardiner, S. C. (2007), The evolution of a management philosophy: the Theory of Constraints, Journal Of Operations Management, 25, 387-402.
- Yüksel, H. (2011), Kısıtlar teorisinin düşünce süreçleri kullanılarak bir üretim işletmesinin etkinliğinin artırılması, Journal of Yaşar University, 21(6), 3622- 3632.
Copyright information
This work is licensed under a Creative Commons Attribution-NonCommercial-NoDerivatives 4.0 International License.
About this article
Publication Date
28 January 2019
Article Doi
eBook ISBN
978-1-80296-053-2
Publisher
Future Academy
Volume
54
Print ISBN (optional)
-
Edition Number
1st Edition
Pages
1-884
Subjects
Business, Innovation, Strategic management, Leadership, Technology, Sustainability
Cite this article as:
Onursal, F. S., Aydın, S., & Birgün, S. (2019). Solving The Sales Problem Of A Poultry Meat Company With Thinking Process. In M. Özşahin, & T. Hıdırlar (Eds.), New Challenges in Leadership and Technology Management, vol 54. European Proceedings of Social and Behavioural Sciences (pp. 858-873). Future Academy. https://doi.org/10.15405/epsbs.2019.01.02.73