Abstract
Although lean implementation has been extensively studied in large companies, research in this area is quietly limited in SME sector. Characteristic of SMEs and large manufacturers are different with respect to structure, policy, resource employee, and culture; therefore, the results of study are significantly different. Lean thinking does not provide easy applications in food industry. This fact raises the question of whether the lean implementation is feasible for companies with different characteristics, such as in food industry, particularly in SMEs. Studies in this area are still evolving and limited; therefore, study investigating lean implementation in SMEs sector is required. This exploratory study attempted to explore lean manufacturing implementation in the context of the SMEs in East Java Province of Indonesia. To collect data, this study used a structured questionnaire. The result of this study showed that lean implementation in food processing SMEs in East Java was quite low. Only 13.3% of SMEs were implementing lean manufacturing practices, and 86.7% of SMEs applied lean manufacturing occasionally. The least lean manufacturing implementation was the use of tools such as statistical process control (SPC) and Full Strategy. The higher barrier to lean manufacturing practice consisted of availability of resources; lack of training; internal resistance; variability in raw materials quality and supply. The barriers encountered by SMEs result from the characteristics of this sector and the characteristics of food processing industry.
Keywords: Lean manufacturing practicessmall and medium enterprisesfood processing industry
Introduction
In the highly competitive business world, the existence of businesses depends on their ability to improve their strategies. One of those strategies is reducing cost and waste by the lean implementation. Through lean implementation, companies have enabled to eliminate non-value-added activities, minimize cycle times, improve quality, minimize costs and ultimately achieve significant economic benefits (Corbett & Klassen, 2006; Cudney & Elrod, 2011). If a company wants to survive in a business environment, they should produce defect-free products; deliver service and product on time at a reasonable price (Womack, Jones, & Roos, 1990).
Womack et al. (1990) defined the lean system as “a system that utilizes fewer inputs and creates the same outputs while contributing more value to customers”. The underpinning of lean is achieving customer satisfaction by delivering process improvement and finding the solution to achieve better results. Lean approach focuses on elimination of waste in all processes, such as product development, production and service delivery. Waste also can occur in all departments such as engineering, scheduling, procuring, producing, accounting and marketing. The waste can be in form over production, transportation, inventory, processing, waiting, motion and defect (Mollenkopf, Stolze, Tate, & Ueltschy, 2010; Wee & Wu, 2009). All source of the waste should be eliminated to create value for the customer.
With the purpose to create value for customers, the enterprise should define their value. They should understand the value steam; identify value-added and non-value-added activities; eliminate non-value-added activities; maintain everything that gives value to the customers and eliminate barriers to implementation. In the lean implementation, the organization also endeavours to improve quality, delivery, and service (Shah & Ward, 2003, 2007). In high competition, the company should focus on customer value to achieve significant economic benefits. The company should be going beyond and being best in every process (Cudney & Elrod, 2011). Generally, the enterprise should perform improvement continuously (Womack & Jones, 2003).
An extensive implementation of lean supports organization to give the effective response to customers. Lean contributes to increasing productivity, quality, customer and employee satisfaction (Mann & Kehoe, 1994). Lean also can accelerate throughput, reduce inventory and increase profit (Jain & Lyons, 2009). Therefore lean can initiate value creation (Haksever, Chaganti, & Cook, 2004). Value creation depends on customers point of view. Lean implementation can improve equipment availability, reduce waste and improve quality (Upadhye, Deshmukh, & Garg, 2010). It helps the company to improve efficiency and quality (Engelund, Breum, & Friis, 2009). In particular for food processing SMEs implementing lean contribute to less product recalls (Scott, Wilcock, & Kanetkar, 2009). To conclude, lean thinking can perform a framework to improve enterprise activities and increase their overall performance (Cudney & Elrod, 2011; Shamah, 2013). The success of lean implementation rests on awareness and involvement of employees; training and commitment from top management.
Despite the benefit of lean practice, the previous studies show many failures in its implementation (Balle, 2005; M. Manzouri, Mohd Nizam, Haslina, & Rasdan, 2010; Papadopoulou & Ozbayrak, 2005). There are some types of barrier such as misunderstand the concept and purpose of lean; lack of resource availability; lack of top management support; resistance to change from employees; unsupported organization culture; unsuitable training for employees; functional and professional silos; disparate manufacturing environment; lack of interest and commitment in lean by supplier and customer; and mediocre consultant (Cudney & Elrod, 2011; M. Manzouri, et al., 2010). The biggest obstacle was the resistance to change from both employees and suppliers (Upadhye, et al., 2010).
Problem Statement
In the last decade, study about lean philosophy has increased significantly (Timans, Antony, Ahaus, & Solingen, 2012). Lean implementation has several benefits such as increasing efficiency; reducing the cost of production (Dora, Goubergen, Kumar, Molnar, & Gellynck, 2014); increasing productivity; increasing quality and delivery and satisfying customers and employees (Mann & Kehoe, 1994). Lean implementation gives benefit to the food manufacturing, such as reduced inventories, faster throughputs and increased profit (Jain & Lyons, 2009). Although study about the lean concept is extensively in large companies, it is quietly limited in SME sector whereas they have the fundamental role in economic development (Timans, et al., 2012). The previous studies do not focus on the specific result for SMEs. Probably the result will different because of the different characteristics between SMEs and large company. Characteristic of SMEs and large manufacturers are different with respect to structure, policy, resource employee and culture (Welsh & White, 1981). So as the study of lean implementation in SMEs is a challenge because they have resource-constraint (Achanga, Shehab, Roy, & Nelder, 2006).
The lean implementation is appropriate for industries that have certain characteristics such as the predictable demand; the low variety of products and the long product life cycle (Malihe Manzouri, Rahman, & Saibani, 2013). Food processing industry has various characteristics that are different from the previous one. The characteristics of the food industry can be classified into several components, including product, production process and plant (Dora, et al., 2014). In detail, those characteristics involve perishable product; variable product quality; minimal automatic operation, high variation process, variable product structure; long setup time of machine; and many line productions. Lean thinking does not provide easy applications in industries such as food processing industry (Dora, et al., 2014). This fact raises the question of whether the lean implementation is feasible for companies with different characteristics, such as in food processing industry, particularly in SMEs. Studies in this area are still evolving and limited. In fact, the discussion of lean manufacturing in food processing SMEs is a debatable topic (Anand & Kodali, 2008; Cocca & Alberti, 2010; Dora, et al., 2014; Kumar, Antony, Singh, Tiwari, & Perry, 2006; Thomas & Barton, 2006); therefore, a study investigating lean concept in SMEs sector is required.
In terms of research object, this study observed SMEs in East Java of Indonesia. East Java is one of largest provinces in Indonesia. In the last three years, economic growth of East Java has shown the significant increase. Economy Structure of East Java consists of diverse industries; one of them is the SME sector. Statistics show a significant increase in the number of SMEs in East Java Province of Indonesia from 2014 to 2017. SMEs contribute to support East Java's economic growth rate. More than 54% Gross Domestic Product (GDP) of East Java is obtained from SME sector, one of which is manufacturing and trading of food and beverages. Previous SME studies are not yet focused on the lean implementation in SMEs in the region. This study is going to fill these gaps, particularly in identifying barrier of lean implementation in food processing SMEs in East Java, Indonesia.
Research Questions
This study focuses on a research question as stated below.
RQ1: To what extent do food processing SMEs in East Java Province of Indonesia implement the lean manufacturing?
RQ2: What are the potential barriers to lean manufacturing practices in food processing SMEs in East Java Province of Indonesia?
Purpose of the Study
This study attempted to explore lean manufacturing implementation in the context of the SMEs. Particularly, this study analyzed the implementation level and its barrier in food processing SMEs in East Java Province of Indonesia. This study was expected to improve operational efficiency in SMEs which engage in the manufacturing of food. Identifying barriers of implementation will help SMEs to overcome the obstacles, so SMEs can minimize waste; cut cost, improve service level; increase customer loyalty and ultimately increase the contribution of SMEs to regional gross domestic of East Java.
Research Methods
This study was performed within the scope of food processing SMEs in Malang Regency and Greater Malang, East Java Province of Indonesia. The kind of this research was exploratory research. To collect data, this study used a structured questionnaire. The questionnaire involved the lean practice used by SMEs, their perceived benefits and barriers. The questions in this questionnaire were adapted from previous studies by Dora et al. (2014), Achanga et al. (2006), Kumar and Antony (2008), Shah and Ward (2007). Before the questionnaire was used, the interview was carried out to explore the production and business process of SMEs. There were three parts to the questionnaire. The first part was the SME’s profile. The second part asked about lean manufacturing practices. The third part was used to obtain information about perceived benefits and barriers to lean implementation. The study classified SMEs based on their cluster and number of employees. There were three clusters based on location and two sizes of SMEs based on the number of employees. The questionnaire was sent out to 150 SMEs in Malang Regency and Greater Malang, East Java Province of Indonesia based on a database of the Chamber of Commerce in East Java. From 150 SMEs in the survey, around 30 SMEs returned the answered questionnaires, accounting for participation rate of 20 percent. The SMEs were asked to indicate their agreement or disagreement with statements about the implementation of lean practices on a five-point-Likert scale. After the questionnaire was received by the researcher, the next process was examining the data by conducting validity and reliability tests. The result showed that the questionnaire was valid and reliable. The following process was descriptive statistical analyses to answer the research questions. The following section shows the finding of this study.
Findings
East Java is one of largest provinces in Indonesia. In the last three years, economic growth of East Java has shown significant increase. Economic structure of East Java consists of diverse industries; one of them is SME sector. Statistics show a significant increase in the number of SMEs in East Java Province of Indonesia from 2014 to 2017. SMEs contribute to boosting East Java's economic growth rate. SMEs sector contributes around 54% of East Java GDP. One of the SMEs sectors is manufacturing and trading of food and beverages.
In term of the variable, lean manufacturing practice variable consists of 24 items about implementation level of that variable in food processing SMEs. Based on the results of data analysis of respondents' statements, only 13.3% of SMEs in Malang were implementing lean manufacturing practices, and 86.7% of SMEs applied lean concepts occasionally. In general, the least lean implementation factors applied by the SMEs were the use of tools, such as statistical process control (SPC) and Full Strategy (
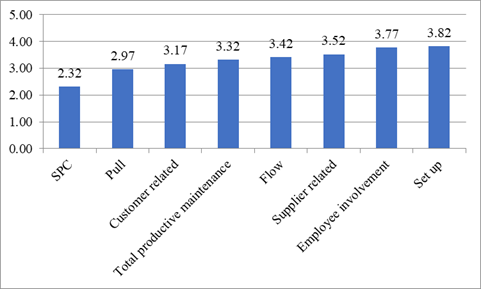
The aspect which was found to be good was setup time. The reason for this condition was related to the kind of equipment. The machines and equipments used are still simple, so they do not require long setup time. Another aspect which was in the same quality was employee involvement. The number of employees in SMEs was not large, so it is still possible to supervise and coach employees well.
The lean implementation barrier variables used 18 items. The result showed that higher barrier to implementing lean practice consisted of availability of resources; lack of training; internal resistance; variability in raw materials quality and supply. The barriers encountered resulted from the characteristics of small and medium enterprises and characteristics of food processing industry. In food processing industry, the raw materials used are seasonal. Their availability, quantity and quality often become constraints at the time of production. The availability of resources relates to the aspect of capital owned by the SMEs. It requires the participation of government to encourage banks to provide low interest rate as credit assistance for the investment of resources. For training, it is necessary to involve academicians and policy makers in government to provide continuous coaching and monitoring, so the tools for lean practice can be implemented sustainably in long-term period. In terms of internal resistance, the entities involved in SMEs have not fully correct understanding of the importance of lean implementation for SMEs.
Conclusion
The current status of lean implementation in food processing SMEs in East Java is quite low. Only 13.3% of SMEs in the region are implementing lean manufacturing practices, and 86.7% of SMEs apply lean manufacturing occasionally. The least lean manufacturing implementation is the use of tools particularly statistical process control (SPC) and Full Strategy. The higher barrier to implementing lean practice consists of availability of resources; lack of training; internal resistance; variability in raw materials quality and supply. The barriers encountered result from the characteristics of small and medium enterprises and characteristics of food processing industry. To sum up, implementing lean practice in food processing SMEs appears to be a complex undertaking.
Acknowledgments
This study was funded by University of Brawijaya
References
- Achanga, P., Shehab, E., Roy, R., & Nelder, G. (2006). Critical success factors for lean implementation within SMEs. Journal of Manufacturing Technology Management, 17(4), 460-471.
- Anand, G., & Kodali, R. (2008). Performance measurement system for lean manufacturing: a perspective from SMEs. International Journal of Globalisation and Small Business, 2(4), 371-410.
- Balle, M. (2005). Lean attitude – lean application often fail to deliver the expected benefits but could the missing link for successful implementations be attitude? Manufacturing Engineer, 84(2), 14-19.
- Cocca, P., & Alberti, M. (2010). A framework to assess performance measurement systems in SMEs. International Journal of Productivity and Performance Management, 59(2), 186-200.
- Corbett, C. J., & Klassen, R. D. (2006). Extending the horizons: environmental excellence as key to improving operations. Manufacturing & Service Operations Management, 8(1), 5-22.
- Cudney, E., & Elrod, C. (2011). A comparative analysis of integrating lean concepts into supply chain management in manufacturing and service industries. International Journal of Lean Six Sigma, 2(1), 5-22.
- Dora, M., Goubergen, D. V., Kumar, M., Molnar, A., & Gellynck, X. (2014). Application of lean practices in small and medium-sized food enterprises. British Food Journal, 116(1), 125-141.
- Engelund, E. H., Breum, G., & Friis, A. (2009). Optimisation of large-scale food production using lean manufacturing principles. Journal of Foodservice, 20(1), 4-14.
- Haksever, C., Chaganti, R., & Cook, R. G. (2004). A model of value creation: strategic view. Journal of Business Ethics, 49, 291-305.
- Jain, R., & Lyons, A. C. (2009). The implementation of lean manufacturing in the UK food and drink industry. International Journal of Services and Operations Management, 5(4), 548-573.
- Kumar, M., & Antony, J. (2008). Comparing the quality management practices in UK SMEs. Industrial Management & Data Systems, 108(9), 1153-1166.
- Kumar, M., Antony, J., Singh, R. K., Tiwari, M. K., & Perry, D. (2006). Implementing the Lean Sigma framework in an Indian SME: a case study. Production Planning & Control, 17(4), 407-423.
- Mann, R., & Kehoe, D. (1994). An evaluation of the effects of quality improvement activities on business performance. The International Journal of Quality & Reliability Management, 11(4), 29-44.
- Manzouri, M., Mohd Nizam, A. B. R., Haslina, A., & Rasdan, I. A. (2010). Barriers of supply chain management implementation in manufacturing companies: a comparison between Iranian and Malaysian companies. J. Chinese Instit. Indus. Eng., 27(6), 456-472.
- Manzouri, M., Rahman, M. N. A., & Saibani, N. (2013). Lean supply chain practices in the halal food. International Journal of Lean Six Sigma, 4(4), 389-408.
- Mollenkopf, D., Stolze, H., Tate, W. L., & Ueltschy, M. (2010). Green, lean, and global supply chains. International Journal of Physical Distribution & Logistics Management, 40(1), 14-41.
- Papadopoulou, T. C., & Ozbayrak, M. (2005). Leaness: experiences from the journey to date. Journal of Manufacturing Technology Management, 16(7), 784-807.
- Scott, B. S., Wilcock, A. E., & Kanetkar, V. (2009). A survey of structured continuous improvement programs in the Canadian food sector. Food Control, 20(3), 209-217.
- Shah, R., & Ward, P. T. (2003). Lean manufacturing: context, practice bundles, and performance. Journal of Operations Management, 21(2), 129-149.
- Shah, R., & Ward, P. T. (2007). Defining and developing measures of lean production. Journal of Operations Management, 25(4), 785-805.
- Shamah, R. A. M. (2013). Measuring and building lean thinking for value creation in supply chains. International Journal of Lean Six Sigma, 4(1), 17-35.
- Thomas, A., & Barton, R. (2006). Developing an SME based six sigma strategy. Journal of Manufacturing Technology Management, 17(4), 417-434.
- Timans, W., Antony, J., Ahaus, K., & Solingen, R. v. (2012). Implementation of Lean Six Sigma in small- and medium-sized manufacturing enterprises in the Netherlands. Journal of the Operational Research Society, 63, 339-353.
- Upadhye, N., Deshmukh, S. G., & Garg, S. (2010). Lean manufacturing in biscuit manufacturing plant: a case. International Journal of Advanced Operations Management, 2(1), 108-139.
- Wee, H. M., & Wu, S. (2009). Lean supply chain and its effect on product cost and quality: a case study on Ford Motor Company. Supply Chain Management: An International Journal, 14(5), 335-341.
- Welsh, J., & White, J. (1981). A small business is not a little big business. Harvard Business Review, July-August, pp. 18-32.
- Womack, J. P., & Jones, D. T. (2003). Lean Thinking: Banish Waste and Create Wealth in Your Corporation. New York: The Free Press.
- Womack, J. P., Jones, D. T., & Roos, D. (1990). The machine that changed the world. New York: Rawson Associates.
Copyright information
This work is licensed under a Creative Commons Attribution-NonCommercial-NoDerivatives 4.0 International License.
About this article
Publication Date
31 July 2018
Article Doi
eBook ISBN
978-1-80296-043-3
Publisher
Future Academy
Volume
44
Print ISBN (optional)
-
Edition Number
1st Edition
Pages
1-989
Subjects
Business, innovation, sustainability, environment, green business, environmental issues, industry, industrial studies
Cite this article as:
Sumantri, Y. (2018). Lean Manufacturing Practices And Their Barriers In Small And Medium Enterprises (Smes). In N. Nadiah Ahmad, N. Raida Abd Rahman, E. Esa, F. Hanim Abdul Rauf, & W. Farhah (Eds.), Interdisciplinary Sustainability Perspectives: Engaging Enviromental, Cultural, Economic and Social Concerns, vol 44. European Proceedings of Social and Behavioural Sciences (pp. 412-418). Future Academy. https://doi.org/10.15405/epsbs.2018.07.02.44