Abstract
Ergonomics awareness substantially affects the business, association, administration, workers and general prosperity of the framework. Since there exist a very limited study on the issue of ergomomic awareness, this paper aim at investigating ergonomic awareness and its effect on safety culture. Questionaires were distributed to employees from manufacturing company in Pahang, Negeri Sembilan and Terengganu. A total of 300 questionaires were distributed but only 200 questionares were return and usable represent 67% of respond rate. Data analysis used IBM Statistical Packages for the Social Science (SPSS) version 22, and Partial Least Square Structural Equation Model (PLS-SEM) version 3.0. Finding of the study revealed that all factor loadings and average variance extracted (AVE) surpassed the prescribed estimation of 0.5 and AVE construct range from 0.960 to 0.983 which surpassed the suggested estimation of 0.7. All the hypothesis of this investigation is bolstered and acknowledged. It was discovered that usage and change were the most critical indicator of the degree of ergonomic awareness took after by supportability of occupation. The higher the degree of ergonomic awareness, the better is the firm’s safety culture.
Keywords: Ergonomic awarenesssafety cultureworkplacePLS-SEM
Introduction
Ergonomics has been introduced in Malaysia in 1992 over the formation of ergonomics department in the National Institute of Occupational Safety and Health; while its provision has been stated under Occupational Safety and Health Act 1994. Although ergonomics currently considered as government concern almost centuries ago, but it is still not widely implemented and practiced in Malaysia (Zafirah & Maimunah, 2013). Musonda and Smallwood (2008) contended that awareness is the display of behaviour and an ergonomics awareness support ergonomics provision and benefits safety and human wellbeing. Fernández-Muñiz, Montes-Peon, and Vazquez-Ordas (2007) proposed that a positive safety culture is an arrangement of qualities, recognitions, dispositions, and pattern of conduct with respect to security shared by individuals from the organization. It is an arranged of strategies, practices, and frameworks which related to reducing's related danger, executed at each level of the organization and becoming measure of concern and obligation in reducing accidents and complaint.
Dawal, Taha and Ismail (2009) noted that the actualizing great ergonomics rehearses lead to the capacity to attain work fulfillment, improved human wellbeing and security. Other than that, it also can improve value, efficiency, working conditions, decrease of cost and increase the company profits (Yeow & Sen, 2002). In the meantime, ergonomics risks concerns may give a huge effect towards businesses and industrial if the dangers are underestimated. This will prompt patterns of non-appearance, medicinal leave, unanticipated retirement and the circumstances will get more regrettable if the laborers make requests for compensation. Safety culture includes numerous definitions inside an impressive collection of writing; in certain case, the meaning of the term is still vague (Shappell &Wiegmann, 2000; Helmreich& Merritt, 2001; Zhang, Wiegmann, von Thaden, Sharma, & Mitchell, 2002). Rollenhagen (2010) defined a culture as a concern of what and how individuals trust, feel, think and how they act (after some time) and how this is reflected in aggregate propensities, rules, standards, images, and curios.
Problem Statement
Ergonomics awareness helps in ergonomics application and contributes significantly to human wellbeing and safety due to a comfortable work environment and ergonomically designed tools , man- machine interface design and suitable work method to human anatomy(Grandjean & Kroemer, 1997). Safety culture is defined as ‘a set of value, perceptions and attitudes and patterns of behavior (Ahasan & Imbeau, 2003; DOSH, 2010; Fernández-Muñiz et al., 2007; Pearson, Nelson, Titsworth, & Harter, 2011) The purpose of inculcating a safety culture is to develop a nature whereby we repeatedly work safely while guided by a well- defined set of core values that protect and promote the health and well-being of the individual and the environment (DOSH, 2010). Safety culture required a development of individual safety attitudes and behaviours (Zohar, 1980).
Ergonomics is a term that most employers have heard tossed around by workplace safety and risk management experts, but many are not entirely clear on just what it means and why it is an important issue (Lechner, 2015). ergonomic principles in the design of work tasks and equipment can significantly reduce risk of musculoskeletal injuries. Ergonomics studies human abilities and limitations in order to serve this purpose. It focuses on the human body and behavior in order to adapt tools, equipment, and tasks for them. However many companies don’t take this into consideration even though they should, as it can change everything for a company (Mestre, 2017). People working in factories can easily get exhausted or injured, meaning a decrease in productivity. That is why ergonomics is so important: if their workstation allows them to have a good posture, less exertion, fewer motions and better heights and reaches, they will be less tired and more effective.
The capacity of overseeing safety is typically relegated to an individual in control on safety aand health as embedded in Section 29 Occupational Safety and Health 1994. Currently an individuals is assigned the specific post to cater issues related with safety. Study on ergonomic awareness and safety culture for example (Mustafa, Kamaruddin, Othman, & Mokhtar, 2009) aims at assessing the level of ergonomics mindfulness in Malaysian industry production and to manage the accepted procedures of ergonomics program utilizing Quality Function Deployment (QFD) among the industrial organizations with the most significant awareness of ergonomics. Hudson (2007) study aims at on the improvement of a advance safety culture. Since limited research was done on connection between ergonomics awareness and security culture at working environment, this paper plans to full fill the gaps.
Research Questions
What is the interaction between the Ergonomic Awareness and Safety Culture?
What is the interaction between the Implication and Improvement and Safety Culture?
What is the interaction between the Suitability of Workplace and Safety Culture?
What is the interaction between the Ergonomics Basic Consideration and Safety Culture?
Purpose of the Study
Ergonomic is needed to be understood by all industries due to many reasons. It is related for many safety and health issues in working area. Nowadays, many industries have applied these regulations but not all the workers know about the existence of it. Basically workers cannot understand the act stated and level of implementation among workers is low. Most of workers ignore safety procedures which been ruled by company due to lack of knowledge. This research attempt to measure the relationship between ergonomics awareness and safety culture at workplace
Research Methods
A stratified random sampling technique is adopted in selecting the sample for this study. The sample of the study covers the employees from private sector companies in Malaysia.Sample covers employees from manufacturing organization in Pahang, Negeri Sembilan and Terengganu. A total of 200 self-administered questionares is anylised. Questionnaire is divided into three section. The first section was associated to the respondent’s demographic profile. The second section is related to the ergonomic antecedents. Lastly, the third section is on safety culture. Question is adopted from Chapanis (1985) for ergonomics awareness, and safety culture is adopted from Turner and Pidgeon (1997). Data is analyses using IBM Statistical Packages for the Social Science (SPSS) version 22, and Partial Least Square Structural Equation Model (PLS-SEM) version 3.0, to measure the reliability and validity of the questions.
The following hypothesis is proposed in this study:
H1: There is a significant relationship between ergonomics awareness and safety culture.
H1a: There is a significant relationship between implication and improvement and safety culture.
H1b: There is a significant relationship between suitability of the job to the workers and safety culture.
H1c: There is a significant relationship between ergonomics basic consideration and safety culture
Findings
Respondent profile
From the total of 300 questionnaire distribute only 200 question were return. Majority of the respondent are male with 135 respondents (67.5%), while 65 respondents (32.5%) were female. For race, most of the respondents were Malay with 96 respondent (48%), and least number of respondent are for Chinese, Indian and others with 27%, 17.5% and 7.5%. Average number of respondent for this study are with the age ranged between 21 to 25 years old with 36 respondents (18.0%). As for marital status highest of respondents are married with 119 respondent (59.5%), followed with single with 60 respondent (30.0%), divorced with 12 respondent (6.0%) and widowed with 3 respondent (1.5 %). For academic qualification highest number of respondent are respondent with SPM levels, 61 respondents (31%) and least number of respondent are respondent with Master level with 8 respondents (4%). Last question are for awareness regarding the ergonomic policy, the result shows that, most of the respondent are aware that there are having ergonomic and safety policy at their workplace with 105 respondents (52.5%) and only 22 respondent (11.0%) are not aware the workplace are having the ergonomic and safety policy.
Convergent Validity
Firstly, it is important to test the convergent validity which is how much various things to gauge a similar idea is in understanding. As proposed by Hair, Sarstedt, Ringle, and Mena (2012) the important criterion to measure the convergent validity is factor loadings and AVE. The loadings value for this study indicated that, all items surpassed the prescribed estimation of 0.5. Next for value of composite reliability as in Table
Discriminant Validity
The discriminant validity (how much things separate among construct or measure unmistakable ideas) was surveyed by inspecting the relationships between's the measures of conceivably covering construct. Items should stack all more firmly on their own construct in the model, and the AVE among each construct ought to be more significant than the variance shared between all constructs (Compeau, Higgins, & Huff, 1999). As appeared in Table
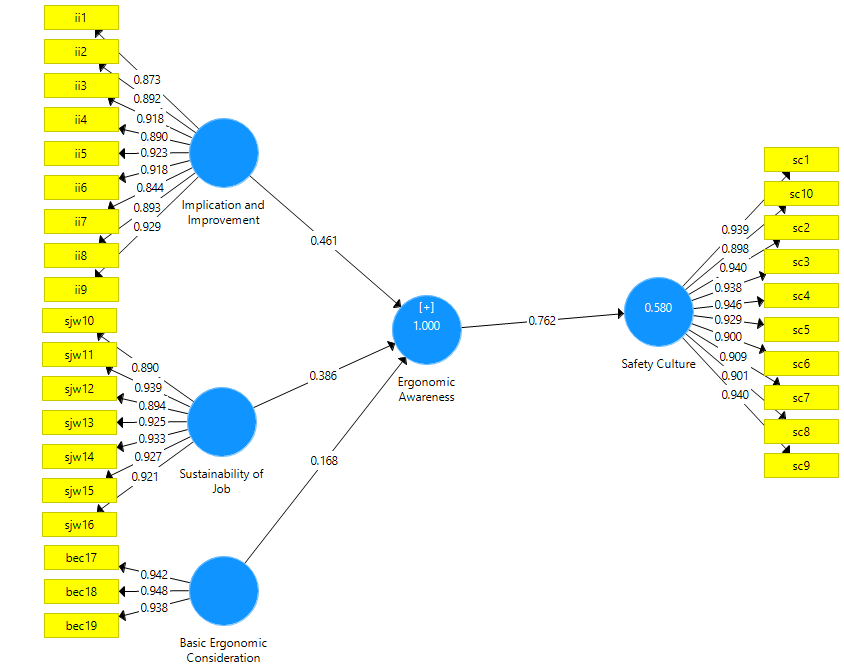
For hypothesis testing, the path analysis was used to test the four hypothesis created. Table
Conclusion
Findings indicated that all dimensions ergonomic awareness have significant positive relationship with employee. All variables in ergonomic awareness were found to be related with safety culture. This finding is important to show the level of ergonomics awareness and its role in shaping safety culture (Rozlina, Awaluddin, Hassan, Abdul, & Norhayati, 2012) However, the variables that should be considered most are implication and improvement and suitability of job to the workers because as these variables could have more influence on safety culture. Ergonomics in the workplace has also been shown to yield significant increases in productivity, reductions in employee absenteeism, and decreases in employee turnover rates (Lechner, 2015).
The finding is expected to serve as guideline to improve safety, quality of work and awareness about safety culture and ergonomic at workplace. Addressing ergonomics in the workplace design and equipment is important to ensuring employees understand and employ good body mechanics in the workplace. Providing employee training in the principles of ergonomics, especially proper posture, appropriate desk and chair heights, along with taking stretch and walk breaks during the workday, all have a place in improving the work environment. The significance of the study hoped to provide evidence in explaining the relationship between Ergonomic Awareness and Safety Culture at workplace. After all, poor worksite design can lead to injured, frustrated and fatigued employees. For this reason ergonomics should be implemented in companies. This way, tasks can be adapted to human capacities and make people more safe, productive and efficient. The multiple benefits for both, the company and its employees.
References
- Ahasan, R., & Imbeau, D. (2003). Who belongs to ergonomics? An examination of the human factors community. Work Study, 52(3), 123-128.
- Barclay, D., Higgins, C., & Thompson, R. (1995). The Partial Least Squares (pls) Approach to Casual Modeling: Personal Computer Adoption Ans Use as an Illustration.
- Chapanis, A. (1985). Some reflections on progress. Paper presented at the Proceedings of the Human Factors Society Annual Meeting.
- Compeau, D., Higgins, C. A., & Huff, S. (1999). Social cognitive theory and individual reactions to computing technology: A longitudinal study. MIS quarterly, 145-158.
- Dawal, S. Z., Taha, Z., & Ismail, Z. (2009). Effect of job organization on job satisfaction among shop floor employees in automotive industries in Malaysia. International Journal of Industrial Ergonomics, 39(1), 1-6.
- DOSH. (2010). Occupational Safety and Health Master Plan 2015 (OSH-MP 15). Retrieved from http://www.dosh.gov.my/
- Fernández-Muñiz, B., Montes-Peon, J. M., & Vazquez-Ordas, C. J. (2007). Safety management system: Development and validation of a multidimensional scale. Journal of Loss Prevention in the process Industries, 20(1), 52-68.
- Grandjean, E., & Kroemer, K. H. (1997). Fitting the task to the human: a textbook of occupational ergonomics: CRC press.
- Hair, J. F. (2007). Research methods for business.
- Hair, J. F., Sarstedt, M., Ringle, C. M., & Mena, J. A. (2012). An assessment of the use of partial least squares structural equation modeling in marketing research. Journal of the academy of marketing science, 40(3), 414-433.
- Helmreich, R. L., & Merritt, A. R. (2001). Culture at work in aviation and medicine: National, organizational and professional influences.
- Hudson, P. (2007). Implementing a safety culture in a major multi-national. Safety science, 45(6), 697-722.
- Lechner, D. (2015). The Importance of Ergonomics: It's All Greek to Me: ErgoScience.
- Mestre, M. (2017). The importance to Improve Ergonomics in the Workplace. Retrieved from https://bridgr.co/the-importance-to-improve-ergonomics-in-the-workplace/
- Musonda, I., & Smallwood, J. (2008). Health and safety (H&S) awareness and implementation in Botswana's construction industry. Journal of Engineering, Design and Technology, 6(1), 81-90.
- Mustafa, S. A., Kamaruddin, S., Othman, Z., & Mokhtar, M. (2009). Ergonomics awareness and identifying frequently used ergonomics programs in manufacturing industries using quality function deployment. American journal of scientific research, 3, 51-66.
- Pearson, J. C., Nelson, P. E., Titsworth, S., & Harter, L. (2011). Human communication: McGraw-Hill New York, NY.
- Rollenhagen, C. (2010). Can focus on safety culture become an excuse for not rethinking design of technology? Safety science, 48(2), 268-278.
- Rozlina, S., Awaluddin, M. S., Hassan, S., Abdul, S., & Norhayati, Z. (2012). Perceptions of ergonomics importance at workplace and safety culture amongst Safety & Health (SH) Practitioners in Malaysia. Paper presented at the Proceedings of the World Congress on Engineering.
- Shappell, S. A., & Wiegmann, D. A. (2000). The human factors analysis and classification system--HFACS. Retrieved from
- Turner, B. A., & Pidgeon, N. F. (1997). Man-made disasters (Vol. 2): JSTOR.
- Yeow, P., & Sen, R. (2002). The promoters of ergonomics in industrially developing countries, their work and challenges. Paper presented at the Proceedings of the 3rd International Cyberspace Conference on Ergonomics.
- Zafirah, M., & Maimunah, S. (2013). Level of Organization Awareness on The Importance of Ergonomics to Health and Safety at The Workplace. 4TH International Conference On Business And Economic Research Proceedings, 972-990.
- Zhang, H., Wiegmann, D. A., Von Thaden, T. L., Sharma, G., & Mitchell, A. A. (2002). Safety culture: A concept in chaos? Paper presented at the Proceedings of the Human Factors and Ergonomics Society Annual Meeting.
- Zohar, D. (1980). Safety climate in industrial organizations: theoretical and applied implications. Journal of applied psychology, 65(1), 96.
Copyright information
This work is licensed under a Creative Commons Attribution-NonCommercial-NoDerivatives 4.0 International License.
About this article
Publication Date
31 July 2018
Article Doi
eBook ISBN
978-1-80296-043-3
Publisher
Future Academy
Volume
44
Print ISBN (optional)
-
Edition Number
1st Edition
Pages
1-989
Subjects
Business, innovation, sustainability, environment, green business, environmental issues, industry, industrial studies
Cite this article as:
Mohamad, M., Hanapiyah, Z. M., & Hanafi, W. N. W. (2018). An Interaction Of Ergonomic Awareness And Safety Culture. In N. Nadiah Ahmad, N. Raida Abd Rahman, E. Esa, F. Hanim Abdul Rauf, & W. Farhah (Eds.), Interdisciplinary Sustainability Perspectives: Engaging Enviromental, Cultural, Economic and Social Concerns, vol 44. European Proceedings of Social and Behavioural Sciences (pp. 274-281). Future Academy. https://doi.org/10.15405/epsbs.2018.07.02.29