Abstract
Every kind of human activity is associated with a certain risk. Man is the least reliable and vulnerable part of the working system “man – machine – environment”. Human failure can cause material damage as well as loss of life. The work environment, management quality, time pressures and human indispositions can adversely affect the quality of work and the health of employees. Furthermore, they can influence decision-making; cause errors and omissions; fail or impede safety assurance; and place the whole system into a critical situation – with domino effect. In this paper, the authors discuss
Keywords: OHSHuman factorPlasma cutting
Introduction
Under human factors one understands factors referring to environmental, organizational and job aspects regarding work conditions, and personal characteristics influencing one´s behaviour at work which can affect health and safety. In this definition there are included three interrelated aspects that must be considered: job, man and organization (Figure
Statistically the most important factor in industrial systems is man because amount of his/her errors influences number of failures of components s/he interacts with (Madonna, et al, 2009). Although it is difficult to obtain valid values, there are estimations that failures of a man are causes of 60 – 90 % of the accidents in industry. The remaining part of the accidents is attributable to technical deficiencies (Griffith, & Mahadevan, 2011; Hollnagel, 1998). As failures of a man are the most significant failings occurring in industrial systems, there is a need to assess human reliability, to reduce probable causes of failures (Iannone, 2004). Human failures, referring to those attributable to human workers, are not random; there are patterns for these occurrences. It is worth to know and be aware different types of failures, because they have different causes and are influenced by different factors. This means that also the ways of failure prevention or elimination are different (Ronald, 2015).
There are three types of human failures (unsafe acts) which may lead to accidents:
Unintentional errors
Errors (slips/lapses) are actions which have occurred unplanned (unintended actions). They can occur during a familiar task, e.g. omissions like forgetting to do something, what is particularly relevant to repair, maintenance, calibration or testing. These are unlikely to be eliminated through training and they need to be designed out.
Mistakes are also errors, but errors of judgement or decision-making processes (intended actions are wrong), where we do the wrong things believing it to be right. Mistakes can appear if behaviour is based on memorised rules or familiar procedures or if decisions are made on first principles what leads to misdiagnoses or miscalculations. Training is the key factor to avoid mistakes (Reason, 1990).
Intentional errors
Contrary to the above-mentioned, violations are intentional (but usually well-meant) failures, such as taking a short-cut or non-compliance with procedures, e.g. deliberate deviations from the rules or procedures. They are rarely wilful (e.g. sabotage) and usually they result from an intention to have the job done despite the consequences. Violations may be situational, routine, exceptional or acts of sabotage (HSE, 2005).
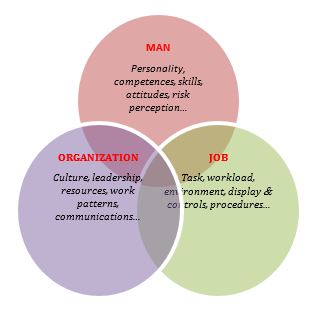
Problem Statement
Human factor is statistically the most important factor in industrial systems, which encounters 60-90 % of errors. The aim of the study was to analyse quantitatively causes of the failures of the human factor, in particular possible failures of particular employees working at the workplace of plasma welding by the means of the Method of Identification of Failure Causes (MIPS; Mikloš & Šolc, 2011; Skřehot et al., 2006) and consequently to assess results of the identified causes of failures in the context of the influence of employees’ activities and to propose measures to eliminate these causes.
For practical applications a workplace of engineering production was selected. A scheme of the facilities and arrangement of the equipment are shown in Figure
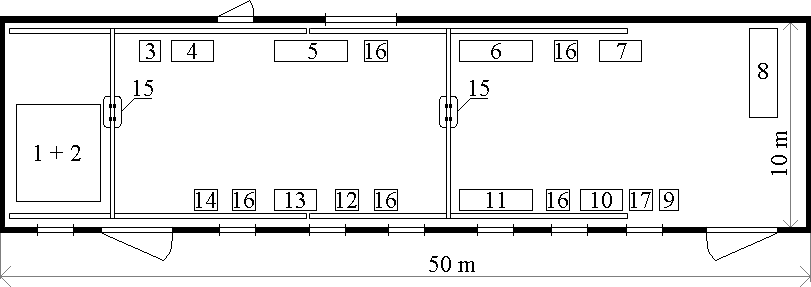
At layout machines the factors affecting employee performance are environment factors, safety factors and ergonomic factors. The most risky activity for employees is cutting plasma material. The main health risks related to plasma devices are:
ultraviolet and infrared radiation,
burns from splashing metal,
fumes, aerosols and gases from the workpiece evaporation,
noise, moving up to about 110 dB,
high arc temperature,
high voltage.
Actually, the activity of material cutting by use of plasma equipment was concerned. For the analysis workers of following professions were selected:
two workers operating the machine (a fitter and a shift foreman) – responded to 227 relevant questions,
operating manager – responded to 234 relevant questions.
Differentiation of questions is essential; these must be formulated with regard to work position. The MIPS method also supposes that the managing workers should know the answers to all questions. Each negative answer allows to define the cause that might lead to failure of the appropriate worker.
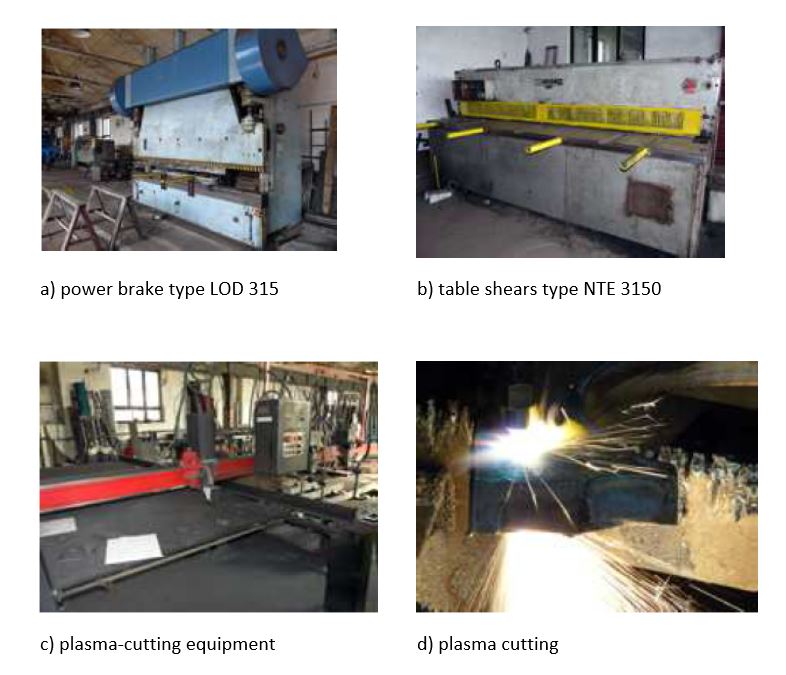
Research Questions
Two main questions of the study were to find out:
whether it is possible to assess effectively and accurately the human factor failure in such a risky workplace as the plasma welding workplace is;
whether the MIPS method is suitable for such kind of assessment.
To answer the stated questions required to carry out a quantitative analysis of the causes of the human factor failures of all included employees at the workplace of the plasma welding by the means of the MIPS methodology and consequently to assess the results of the identified causes of failures in the context of their influence on the employees´ and to propose the measures to eliminate these causes (to lower the influence of human factor on occurrence of injury or accident).
Purpose of the Study
As the human factor is statistically the most important factor in industrial systems, it is necessary to assess its reliability to avoid fatal system failure. On the other hand it is very difficult to choose a way of an appropriate human factor reliability assessment, mainly such one, which would be “user friendly”, i.e. suitable also for unexperienced evaluators.
One of the newer methods in the field of assessment of the human factor failure is the Method of Identification of Failure Causes (MIPS; Mikloš, & Šolc, 2011; Skřehot et al., 2006), qualitative analysis of which is based on a controlled conversation (questions) with a selected worker of appropriate profession. The questions are formulated in such a way that each of them would allow to reveal subsequently the possible cause of worker failure. To support next development and promotion of this method needs to perform statistical assessments of the significant samples of mutually comparable objects. For this reason the MIPS method was used to assess the performance and reliability of the human factor in the above described plasma welding workplace.
Research Methods
The Method of Identification of Failure Causes (MIPS) was created on the basis of the system model - Work Process Analysis Model. This model consists of the elements of task analysis, ergonomic elements and last but not least also the work psychology elements. Due to this wide approach, the MIPS method allows to analyse majority of factors acting upon the workers causing the failure of human factor (Mikloš & Šolc, 2011; Skřehot et al., 2006). For system characteristic (environment and processes) the organisational reliability factors (SOF) are introduced. These factors represent indices, characterising the effect of a part of system upon the appropriate worker, which exerted and/or could exert certain effect upon the occurrence and/or course of undesirable event. The SOF factors are divided to groups, where each SOF group characterises a wider circle of effects and is therefore subdivided to partial ones (DPSOF). The measure of SOF interaction with individual professions differs, therefore MIPS considers this fact via different approach at assessment of the collected answers. For this purpose it is necessary to identify the critical profession groups, which contribute to the occurrence of undesirable events most often.
MIPS can be in a simplified form illustrated by the flow chart presented in Figure
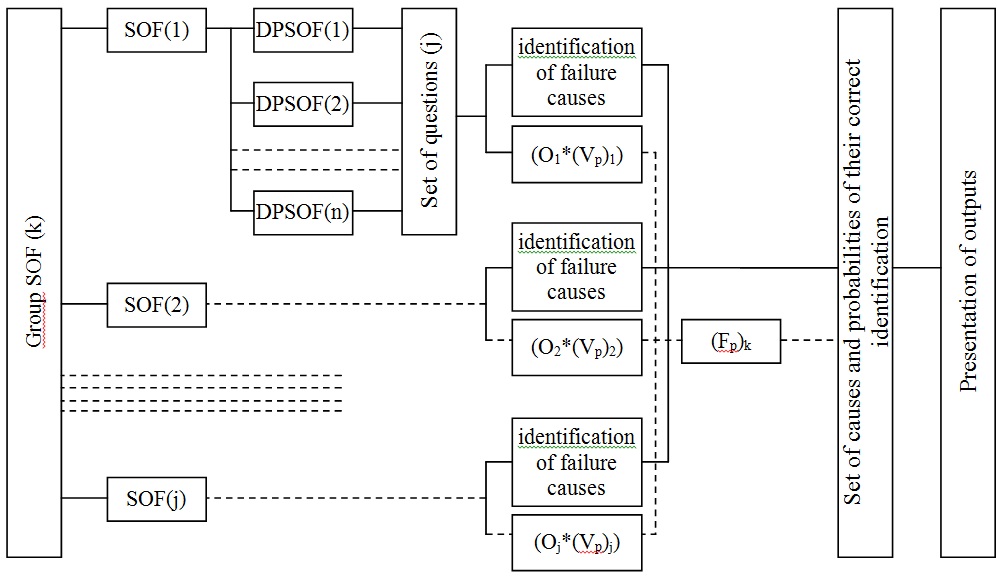
Quantification was performed via the human failure factor – Fp, which allows to determine the probability of a correct determination of human failure causes Pp. Each negative answer from the check lists was penalized by one point and subsequently calculated with the weight coefficient (value 1 – 3). The factor of human element failure (Fp), to be determined for each SOF (k) group separately, is calculated by the formula (1).
(1)
where:
Fpfactor of human element failure,
Vpappropriate weight coefficient z,
Oipenalization coefficient (sum of penalization points for negative assessment of appropriate DPSOF – each negative answer = 1 point),
i question,
jthe number of investigative questions for appropriate SOF,
kSOF group.
The dependence of Pp on Fp does not take into account just the general number of causes and probability of their acting leading to human error but it takes into account also the significance of possible consequences. Conditions of functional relationship (2):
(2)
The resultant Pp value expressed in per cents shows then what is the probability that there exists at least one from among the identified causes, which really caused the failure of a given person. The quantitative assessment shown in Table
Findings
Results achieved at the analysis through the MIPS method have shown that failure of the human factor at the workplace for plasma cutting of materials Fp varies in average from 0.17 to 0.30, what in quantitative assessment means that though human failure is not supposed, the identified cause might affect the behaviour of the worker. In spite of the fact, that the risk of human factor failure is rather low, the analysis has revealed several weak points even in each of the analysed fields. Table
The selected worker assessed the entire system and work team by his answers. At first he followed mainly his own experiences and subjective feelings, then he revealed also the facts concerning himself. If some contradictions between answers of different persons were observed, it was obvious that one side did not respond in accordance with the real state. There was minimal number of subjective questions, mainly due to the fact that such statements are not always trustworthy in practice.
Final step of the analysis consisted of elaboration of the protocol on investigation. This protocol contained the calculated values (Fp)k and (Pp)k and possible reasons of the effect of the human factor on the analysed work activity. In case of a software processing of this method, the protocol is generated by computer automatically.
Predicted imperfections that could exert the most significant effect upon the failure of the human factor within the given SOF group are shown in table
Despite the fact the overall risk of the human factor failure was very low for most of the evaluated areas, the analysis revealed the weaknesses in the management of work, working procedures and the determination of clear responsibilities. Software evaluation of the MIPS methodology allowed to propose the measures for lowering the influence of the human factor errors on the occurrence of adverse event when plasma cutting equipment is used. In general the applied method was assessed as an appropriate and effective method.
Conclusion
It was found out that the tasks and duties for performance of functions were not clearly defined on all stages of the management. Therefore the following corrective measures were proposed:
to elaborate the organisation order for performance of necessary functions with clearly defined tasks and duties,
to appoint unambiguous right powers and responsibilities on all stages of the management.
Not only quantitative assessment of actual risk level brings about the greatest merit of the concerned method, but also qualitative assessment in the form of verbal description of imperfections on the analysed workplace does. It is just the qualitative assessment, based on which the corrective actions can be suggested. One can conclude, that the studied method is a suitable tool at the application of the reliability assessment for the human factor in case of cutting by the use of the plasma equipment.
The MIPS method is relatively new technique in the field of assessment of the human factor failure. Therefore it would be inevitable for next development and application of this method to perform a statistical assessment of the significant samples of mutually comparable plants.
The MIPS method is a suitable analysis method also for unexperienced evaluators because of its simplicity and intuitiveness. It can be used as a software application which facilitates the calculations and the software generates the report of investigation automatically. The designers of the method reported the accuracy of the results at the level of 80 – 90 %. This analysis will most likely reveal majority of real causes which could possibly lead to unexpected events caused by the human factor failures.
References
- Griffith, C.D. & Mahadevan, S. (2011). Inclusion of fatigue effects in human reliability analysis. Reliability Engineering & System Safety, 96 (11), pp. 1437–1447.
- Havlíková, M. (2009). Lidský faktor v systémech MMS. Journal, JOSRA, vol. 2009 (1).
- Hollnagel, E. (1998). Cognitive Reliability and Error Analysis Method CREAM.
- HSE. INSPECTORS TOOLKIT. (2005) Human factors in the management of major accident hazards http:// www.hse.gov.uk/humanfactors/topics/index.htm.
- Iannone, R.et al. (2004). Proposta di un modello simulativo per la determinazione automatica delle pause di lavoro in attività manifatturiere a prevalente contenuto manuale. Treviso - Italy ANIMP Servizi Srl, pp. 46–60.
- Kubovičová, B. (2012). Analysis of the impact of human factors in engineering production. Thesis. STU, MTF. 82 pp.
- Madonna, M., et al. (2009). Il fattore umano nella valutazione dei rischi: confronto metodologico fra le tecniche per l’analisi dell’affidabilità umana. Prevenzione oggi. 5 (n. 1/2), pp. 67–83.
- Mikloš, V. & Šolc, M. (2011) Ľudský činiteľ- základný faktor ovplyvňujúci výkonnosť, kvalitu a bezpečnosť, 16. Medzinárodná vedecká konferencia: Kvalita a spoľahlivosť technických systémov. Nitra, pp. 46-50.
- Reason, J. (1990). Human error. 1st issue. Cambridge : Cambridge University Press, 1990. 302 pp.
- Ronald W. McLeod (2015). Disigning for Human Reliability: Human Factors Engineering in the Oil, Gas, and Process Idustries. Elsevier, Oxford. ISBN 978-0-12-802421-8.
- Skřehot, P. (2009). Errors of human factor and identification of their causes. Journal JOSRA. vol. 2009 (1).
- Skřehot, P. et al. (2006). Methodics for identification of failure causes. User´s guide. Prague , VÚBP, ISSN 1803-3687.
- Tureková, I. & Turňová, Z. (2013). Assessment of human factor in production engineering. In: Occupational Safety and Hygiene: Proceedings of the 9th International Symposium on Occupational Safety and Hygiene, SHO 2013. Guimaraes, Portugal, CRC Press, 2013. pp. 567-571.
Copyright information
This work is licensed under a Creative Commons Attribution-NonCommercial-NoDerivatives 4.0 International License.
About this article
Publication Date
14 September 2017
Article Doi
eBook ISBN
978-1-80296-029-7
Publisher
Future Academy
Volume
30
Print ISBN (optional)
-
Edition Number
1st Edition
Pages
1-376
Subjects
Health, public health, preventive healthcare, preventive care, preventive medicine
Cite this article as:
Tureková, I., & Hašková, A. (2017). Performance And Reliability Of Human Factor: Case Of A Plasma Welding Workplace. In Z. Bekirogullari, M. Y. Minas, & R. X. Thambusamy (Eds.), Health and Health Psychology - icH&Hpsy 2017, vol 30. European Proceedings of Social and Behavioural Sciences (pp. 328-336). Future Academy. https://doi.org/10.15405/epsbs.2017.09.32