Abstract
When evaluating the wettability formed in the process of underground mining of coal dust, it is important to take into account not only the brand of coal produced, determined by the output of volatile substances and vitrinite reflectance, but also its physical properties (moisture content, ash content), and petrographic features and chemical formula. The workers of the coal industry are the most susceptible to the influence of harmful factors, including the effects of coal and rock dust. Thus, according to the data for 2013, in Kemerovo region, where the rate of occupational diseases is the highest, and per 10 thousand of the employed population, it equals 14,4 of those found in coal mines. All together, there are 322 occupational diseases found among drifters and stope miners: 95 ― among the drivers of mining excavation machines, 95 ― among the underground electricians, and 51 ― among underground miners. The article presents an analysis of existing technologies to combat dust in the coal mines of the Kemerovo region. The results of a study of the application of a special wetting agent developed at the Mining University, which can be recommended for spraying during mining operations, are presented.
Keywords: Coal dustwettabilitysurfactantshydrodedustingcoagulationhydrophobicity
Introduction
The high concentration of dust in the working air of coal mines is one of the most harmful and dangerous production factors. Constant exposure of the respiratory system of workers to large amounts of dust particles in the air leads to the development of the most serious occupational diseases (Ischuk, & Pozdniakova, 1991). According to Rospotrebnadzor, only in 2013, the proportion of newly reported occupational diseases among workers of mining enterprises was 37.21%, out of which approximately one-fifth (18.25%) relates to diseases connected with dust exposure. The main nosological forms of occupational diseases resulting from the impact of industrial aerosols are chronic dust bronchitis (22.45%), pneumoconiosis (21.78%) and chronic obstructive (asthmatic), bronchitis (18.36%) (Farmer, 1993).
Thus, the dust factor in coal mines is one of the main threats to life and health of people. In this connection, the underground coal mining sites provide a number of measures to combat the dust that can be divided into the following main types:
Hydrodedusting has become the most widely used measure in coal mines. At the same time, the rate of reaction, coagulation and deposition of dust particles hovering in the air is determined by the degree of wettability. Wettability formed during the coal dust treatment and sinking works depends on many factors: the specific surface of the particles, petrographic and chemical formula of mined coal, the degree of metamorphism, density, etc. (Steedman, 2002). However, in most cases, the study of issues of interaction between coal and dust with droplets of spray water or a wetting agent formed upon coal destruction covers the difference in the wettability of various grades of coal, determined mainly by vitrinite reflectivity and volatile content. At the same time, the impact of the original coal moisture, its ash content, chemical formula, and percentage of microcomponents (maceral) are hardly ever considered (Bartknecht, 1987).
Types and composition of coal
For the purposes of a more detailed study of the influence of said coal parameters on their sorption capacity, samples from 10 layers of Kuzbass mines were obtained. First, the humidity levels were determined for all samples
When analyzing the obtained data, it should be noted that coal samples 1 and 3 refer to the same gas grade, but have different wettability. It can be assumed, that the difference in wettability in the present case is primarily affected by the coal ash content, which is respectively Ad = 14.5% and A d = 24.2%. At the same time, it is important to consider the type and percentage of mineral impurities, included in the ash composition. According to the chemical analysis, it was found that in the "DG" coal grade, which is the most hydrophobic, the ash content refers to the alumina type (Al2O3= 31.61%). If we consider the "D" coal grade (sample 4), it has a higher relative humidity ratio as compared to "DG" (sample 2) and "G" (sample 3) coals, which is explained by the minimum value of ash content Ad = 6%, and the low initial moisture content.
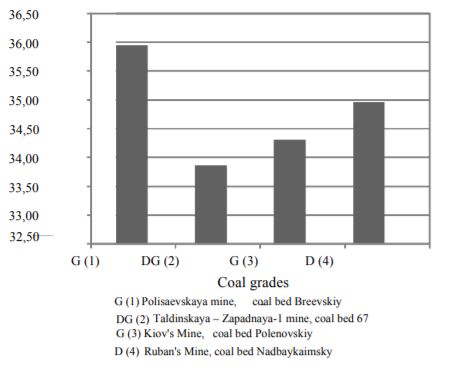
Despite the fact that "DG" coal grade occupies an intermediate position in the metamorphic row, it has the worst wettability, due to the presence of more dense hydrated films on the surface of coal particles and the specified ash type. Also, the wettability of the coal particles depends on the density, strength and proportion of coal petrographic components. This is particularly noticeable at low metamorphism intensity. As compared to other grades, the "DG" coal grade was found to have the most dense inertinite (fusinite) - 11%, and the number of fusinite components (ΣOK) - 12%, which further explains its hydrophobicity.
Thus, when choosing the means and mode of dust control for a particular coal mine, it is important to consider the physical and chemical properties of the coal, especially the material and petrographic composition of mined coal which determines the wettability of the dust formed during mining.
In order to improve wettability of dust generated upon extraction of coals of medium metamorphosis, one shall use a 0.025-0.05% aqueous solution based on sodium tripolyphosphate, sodium carboxymethyl cellulose and pine oil.
In order to improve the wettability and dust binding efficiency, as well as reduce water consumption during humidification and irrigation, the mine wetting reagents are often used, which are aqueous solutions of surface-active substances (surfactants). Their main role is to reduce the surface tension at the interface of the "liquid - solid" phases.
Methods
Efficiency of antidust measures using a wetting reagent should be assessed comprehensively, not only based on the amount by which the dust levels have reduced, but also on the degree of harm of the formula applied for workers and its environmental impact (Silvester, Lowndes, Hargreaves, 2009; Cole, Fabrick, 1984). Therefore, studies were conducted to develop a wetting reagent, which would largely satisfy the requirements of the user. In the early stages of the tests, the surfactants were picked out in order to study their wetting ability, including when exposed to different coal grades. In order to conduct the experiments, four samples of above-mentioned Kuzbass mines coal were used; and the following substances were used as potential wetting reagent components: sodium chloride (NaCl), sodium silicate, sodium carboxymethylcellulose (Na-CMC) (Kovshov, Kovshov, Erzin, 2014), and sodium tripolyphosphate (Na5P3O10).
It was established, that in all cases, the relative humidity indicator upon adding of the above-mentioned substances grew by 1.5-118.7% (as compared with water). For example, the relative humidity ratio of the "D" coal grade sample from the Polysaevskaya mine originally was 36.2%, and with the addition of the carboxymethyl cellulose solution, it respectively became 79.16%. A similar trend is observed with regard to powdered coal fractions of other grades. The fine coal dust of the Polysaevskaya mine becomes wetted better than others, while the coal of Taldinskaya-Zapadnaya-1 mine is worse than others. This difference in wettability is fully correlated with the data of previously conducted studies on the determination of the "natural" relative humidity ratio of coal. The solutions of Na-CMC, Elfor-M, and sodium tripolyphosphate are the most efficient in terms of the relative humidity ratio. Sodium silicate and sodium chloride have the least wetting ability. Also the wetting ability of surfactants depending on their amount in the solution was examined. The influence of 0.001%, 0.01%, 0.025%, 0.05% and 0.1% solutions on wettability of coals was observed. Additionally, a combined formula was obtained, which is a mixture of 25% Na-CMC and 75% Na5P3O10. Table
The relative humidity ratio in the experiments with different coals and surfactants increases as the concentration of the solution is increased, which is due to the accumulation of substances with a significant energy, in the surface layer. Owing to the surface activity growth, a reduction in surface tension occurs, as a result, the interaction of fine coal particles with the solution molecules improves. With 0.05% concentration, almost the maximum state of saturation of the surface layer is achieved and the maximum humidity ratio is observed. Upon further increase of surfactant amount, wettability of coal dust practically stays the same, and in most cases gradually decreases, which is also associated with increased viscosity of the solutions used. Similar results were obtained when using coal samples from Ruban's mine and Kirov's mine.
For the purpose of comprehensive assessment of the wetting ability of solutions of different surfactants, upon variation of their concentrations, the studies were carried out to determine the surface tension (
When analyzing the built isotherms, it can be concluded that with increase of the content or concentration of the above-mentioned substances in the aqueous solution, the surface tension value decreases to a certain limit after which it remains practically unchanged. The minimum value for this parameter is observed at 0.05% surfactant concentration.
The solutions of sodium chloride have the highest values of surface tension (σ = 45.77-62.46 mN / m2), while the solutions based on Na-CMC, sodium tripolyphosphate and pine oil show the lowest values. Depending on the number of the latter in the solution, this parameter ranges from 29.90 to 27.76 mN / m2, with a total surfactant concentration of 0.05%. At that, introduction of 5% pine oil would prove irrational, because it will increase the cost of the finished wetting reagent with a slight reduction of surface tension. The average value of σ Elfor-M solutions is a bit higher than that of the solutions discussed above, and in case of 0.05% concentration, it equals 33.46 mN / m2.
The researches for the contact angle and wetting of 4 coal grades with different formulas have shown that in all cases, at higher concentrations of the used wetting reagent, the angle decreases down to 0.05% with the increase of wetting reagent concentration from 0.05% to 0.1%. The smallest contact angle is formed by the wetting of Polysaevskaya mine coal samples with combined formulas with the addition of 2, 5 and 10% of pine oil.
Thus, to improve the wettability of dust generated during extraction of coals of medium metamorphosis, one shall use 0.025-0.05% aqueous solution based on sodium tripolyphosphate, sodium carboxymethyl cellulose with addition of 2% or 5% of pine oil.
To reduce the dust load on the respiratory system of miners in breaking face and development face of coal mines processing "G", "DG" and "D" coal grades, the irrigation shall be carried out with 0.03% working solution of 30% wetting reagent, which includes 75% of sodium tripolyphosphate, 23% of carboxymethylcellulose and 2% of pine oil, under pressure of 1.5 MPa, and using a 1.5 mm diameter jet nozzle.
In order to assess the effectiveness of dust control when using a designed wetting reagent, the performance tests were carried out in the S.M. Kirov's mine of OJSC SUEK-Kuzbass. The main objectives of the real experiments were as follows:
Results and Discussion
When conducting underground investigations, it is important to consider not only the appearance of the of spray wetting reagent, but also such parameters as the jet nozzle diameter and the pressure of water supplied into the dispenser, both of which have a direct impact on the effectiveness of dust control. That is why, the studies to determine the rational parameters of spraying in terms of reducing dust levels were carried out first. Formula No.2 was used for experiments. The water pressure varied from 1 to 3 MPa at a pitch of 0.5 MPa. The formula was poured into the DS 50/200 dispenser mounted on the JOY 7LS-20 shearer, and was sprayed at the indicated pressure values. The jet nozzles with a diameter of 1.0; 1.5; 2.0; 2.5 and 3.0 mm were used. The measurements of generated dust were taken from the combine driver in the face of Boldyrevsky 24-56 stratum.
As we can see from Table
Conclusion
As a result of experiments it was found that upon adding developed wetting reagents (No. 1, 2, 3) into the combine irrigation system, the efficiency of dust suppression as compared to water irrigation increases by 23.9-55.6%, and as compared to Elfor-M wetting reagent being currently in use at mines, it increases by 3.0-16.6%. However, given the cost, efficiency of dust suppression and reduction of dust loads on the respiratory system of miners, it is recommended to do the following upon development of "G", "DG" and "D" coal grades: irrigation with 0.03% working solution of 30% wetting reagent, which includes 75% of sodium tripolyphosphate, 23% of Na-CMC and 2% of pine oil, under the pressure of 1.5 MPa, and with the jet nozzle diameter of 1.5 m.
The use of such formula makes it possible to increase the efficiency rate of dust suppression by 6.1-11.2%, reduce the dust load on the respiratory system of miners by 340-770 g for 25 years of professional experience, as well as to cut costs by RUB 1, 655, 000 per year.
References
- Abdul-Wahab, S.A., (2006). Impact of fugitive dust emissions from cement plants on nearby communities Ecological Modelling, 4, 338-348.
- Bartknecht, W., (1987). Dust explosion: course, prevention, protection. Springer Verlag, pp: 679.
- Cole, C. & A. Fabrick, (1984). Surface mine pit retention. Journal of the Air Pollution Control Association, 34 (6), 674–675.
- Farmer, A.M., (1993). The effects of dust on vegetation - a review. Environmental Pollution, 79, 63-75.
- Ischuk, I.G. & G.A. Pozdniakova, (1991). Tools integrated dedusting mining enterprises. Moscow: Nedra.
- Kovshov, S., Kovshov, V. & A. Erzin (2015). Bonding dust with environmentally safe compositions on open dust-forming surface in coal producing enterprises. International Journal of Ecology & Development, 30, 11-23.
- Kovshov, S., Kovshov, V. & Erzin A (2014). Application of calcium carbide for reduction of dust release in port complexes. International Journal of Ecology & Development, № 27 (1), 89-95.
- Silvester, S.A., I.S. Lowndes & D.M. Hargreaves, (2009). A computational study of particulate emissions from an open pit quarry under neutral atmospheric conditions. Atmospheric Environment, 43, 6515-6524.
- Steedman, C., (2002). Dust. Manchester: Manchester University Press.
- Wypych, P., D. Cook & P. Cooper, (2005). Controlling dust emissions and explosion hazards in powder handling plants. Chem. Eng. Process, 44, 323-326.
Copyright information
This work is licensed under a Creative Commons Attribution-NonCommercial-NoDerivatives 4.0 International License.
About this article
Publication Date
20 July 2017
Article Doi
eBook ISBN
978-1-80296-025-9
Publisher
Future Academy
Volume
26
Print ISBN (optional)
Edition Number
1st Edition
Pages
1-1055
Subjects
Business, public relations, innovation, competition
Cite this article as:
Kovshov, S. V., & Kovshov, V. P. (2017). Improving Efficiency of Dust Suppression During Underground Coal Mining Using Surfactants. In K. Anna Yurevna, A. Igor Borisovich, W. Martin de Jong, & M. Nikita Vladimirovich (Eds.), Responsible Research and Innovation, vol 26. European Proceedings of Social and Behavioural Sciences (pp. 489-496). Future Academy. https://doi.org/10.15405/epsbs.2017.07.02.63