Abstract
Vagueness in definition of ‘error’ generates its ambiguous interpreting. That is why, there is a need to study genesis of error predetermined by a chain of events: error →action → accident (in which a human factor plays an important role). When reconstructing a role function of the human factor we should admit that, most often, it is the initial cause of method and a means of making the error including emotional-volitional and intellectual constituents. Though, while specialists are getting knowledge, skills and experience, the correlation between two major constituents of error is gradually changed as well. This enables us to accentuate a phenomenon of ‘errors of inexperienced workers’ in which an emotional-volitional constituent prevails over the intellectual one initiating mechanisms of psychological protection, and a phenomenon of ‘errors of experienced workers’ in which intellectual constituent dominates and, thus, induces a coping strategy in problem solving. A functional constituent of error that includes intellectual and emotional-volitional constituents, interacts with a structural constituent and generates conditions under which personal victimity of ‘inexperienced worker’ phenomenon originates, while the basis for constituting the error in an ‘experienced worker’ phenomenon is made of professional victimity lying in the dimension of risk-reducing behavior in a non-standard situation. It is the functional constituent of error that is a manageable chain link as it allows forming the error management system at hazardous production facilities.
Keywords: Constituents of errorage‘experienced worker’ and ‘inexperienced worker’ phenomenaaccident cyclicity
Introduction
The introduction of integrated information and analytical centers of industrial safety at coal mines enables the reduction of the risk of industrial hazards (Sarkisov, 2012). Despite the implemented measures to increase safety, the situation in mining area is far from being perfect. For the past 10 years, major accidents at coal mines in Russia have been taking place every 3-4 years. More than 465 persons died (Grishin, 2014). Still more incidents and accidents happen due to human fault (Safin, 2013). According to the State Labor Inspection of the Russian Federation, over 60% of incidents are explained by ignoring or breaking the safety code or labor discipline, unsatisfactory industrial management, i.e. a human factor (Lieberman, 2006). It is unsafe behavior in an accident zone that explains death of 33-46% of miners because of getting poisoned with carbon oxide (Fistal et al., 2013). The existing situation has defined the expediency to study architectonics of human error since not always psychophysiological characteristics of a human being correspond to the level of complexity of problems to be solved and labor process specifics. Since, nearly 16-20% of virtually healthy people are not able to master a number of trades variable in their complexity because their psychophysiological parameters do not meet labor process requirements what leads to overpressure of regulatory systems and risk of adaptation processes failure (Gryzunov et al., 2015).
Methods
The research objective is a miner’s decision making process as a reflection of dynamic interaction of a personality with a problematic situation and choice of a coping behavior strategy in a non-standard situation. In accordance with the above mentioned, occupational injuries at several coal mines in Russia were analyzed based on age which enabled to detect two age peaks in mine injuries (Picture 1, 2).
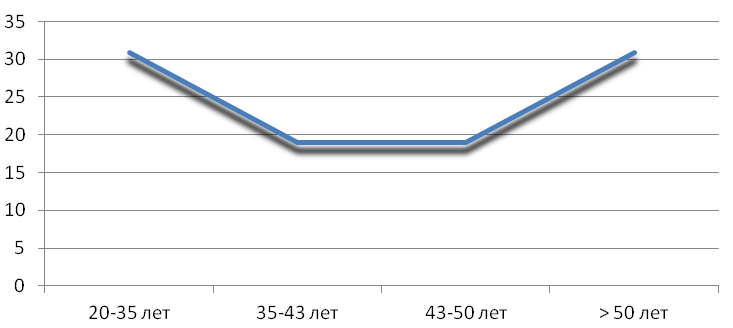
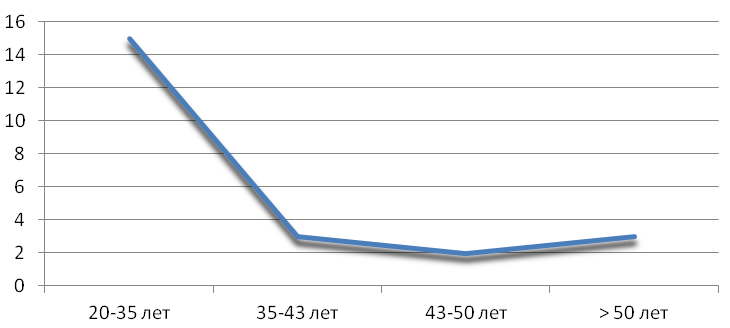
The highest level of injuries is observed among young workers at the ages from 20 to 35 y. o. and experienced workers at the age of 50 and older which enables us to detect age phenomenon in tendency to making errors at highly dangerous facilities (‘inexperienced worker’ phenomenon and ‘experienced worker’ phenomenon). Miners aged 20-35 y. o. make up a group of inexperienced workers among which major reasons of injuries are the following: lack of professional experience, lack of knowledge, inaptitude to correctly diagnose emerging violations and hazardous situations and develop correct solutions, lack of automated skills and actions in a hazardous situation which is largely predetermined by the lack of typical models of a safe behavior in non-standard situations at a production site. Thus, existing typical behavioral solutions of young workers do not assure safety in case of a threat. That is why, an attribute of an inexperienced worker phenomenon is a high level of fatality and occupational injuries (Picture 3). To a large extend, the major reason of occupational injuries among experienced workers is conditioned by a neglectful attitude to the use of protective equipment and carelessness related to quite an extensive range of typical behavior models in non-standard situations that do not consider dynamically changing conditions of production environment and are limited with flexibility of cognitive resources which leads to a certain increase in ‘irrevocability of losses’.
To analyze the state of problem of choosing a production control behavior strategy in the area of labor safety under current conditions, 122 workers were surveyed (Picture 3) using a questionnaire ‘Indicator of Stress Coping Strategies’ by D. Amirkhan (the questionnaire was modified by N. A. Sirota, V. M. Yaltonsky (Ilyin, 2014)).
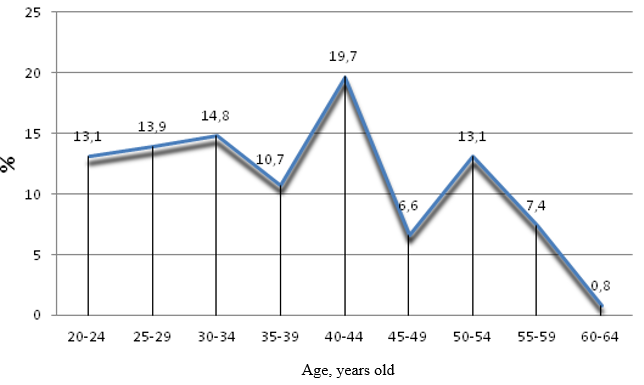
In accordance with the questionnaire survey, it was found that Group 1 – young specialists prefer avoiding the problem strategy which results from a need to reduce emotional pressure in a stressful situation. Yet, such form of coping does not enable one to solve a situation related to accumulation of difficulties and a short-term effect from actions taken to reduce emotional discomfort. Specialists with a more extended working experience made up Group II – they prefer the problem solving strategy that enables one to purposefully and systematically solve a problematic situation. Though at that, excessively rational behavior in a non-standard situation does not ensure an appropriate assessment of dynamically changing conditions in an industrial area. The common moment uniting workers from Group I and Group II are actions of the individuals taking place in time and dimension, in the interest of individuals themselves. But an action of a person may be embodied in its inaction. That is why, it is reasonable to investigate the structure of error through the prism of activity (activity or inactivity) initiated by human motivation based on which behavior patterns and expected results are formed under conditions of real life environment.
That is why, error in behavior patterns may be regarded as:
- a variant of deviation from the final result of the objective that leads to searching of new behavior models to achieve the set goals;
- a variant to achieve the final result;
- a zero variant characterized by the absence of positive and negative moments for a person.
Results
Assuming that the duration of professional stress increases the risk of disruption of adaptation mechanisms and is accompanied by an increase in the number of work accidents, we have analyzed the level of fatal and severe injuries of mine workers in some coal mines. The statistical method of analysis made it possible to obtain a comparative dynamics of injuries for the period from 2012 to 2015. The report data and documents of enterprises served as the initial material. Quantitative assessment of the accident rate enabled us to form groups of risk by age categories. Four age groups of employees of coal enterprises with different frequency of injuries were formed. The analysis of severity and frequency of injuries of mine workers made it possible to identify two high-injury age-associated categories of surveyed workers.
122 workers of coal mines of different ages were interviewed with the help of the Coping Strategy Indicator questionnaire by D. Amirkhan modified by N.A. Sirota, V.M. Yaltonsky (Ilyin, 2014). This test questionnaire made it possible to identify the prevailing strategies of behavior for the solution of problems. The test was carried out with the voluntary consent of the surveyed workers. The results of the analysis were subjected to qualitative analysis. The effect of application of individual characteristics (age, risk of work accidents, prevailing problem-solving strategy) made it possible to identify essential characteristics of high-injury age-associated categories of workers forming the components of human error in decision-making.
Discussion
At present, there is no general definition of ‘error’. Some scientists believe that error is ‘a non-planned action’, other considers error to be a result of an action that is made inaccurately, incorrectly or it is something that is impossible to calculate or predict based on accumulated knowledge. That is why, vagueness of the definition leads to its ambiguous interpreting. The need to study the architectonic of error is predetermined by the chain of events: error →action → accident (in which a human factor plays an important role) (Gryzunov, & Gryzunova, 2014). Drawing on traditional definitions of ‘error’, it is worth noting that their basis is made of an action realized through human behavior and targeted to achieving a definite objective. Therefore, goal orientation of human behavior defines ‘manner’ as a system of consecutive methods, actions and operations in time and space to achieve the objective. Manner as well as action itself is implausible without a will content with emotional coloring that characterizes psychic, inner sense of one’s error and is an attribute of its subjective side. And, the structure of manner may be presented as stages of consecutive actions: preparatory acts to make an error, making an error itself, and after-the-error period. Architectonics of consecutive stages is the object of cognition. Architectonics of consecutive stages is the object of cognition. It is worth emphasizing that every consecutive stage is absorbed by the next one, and has no individual meaning in this sense. Yet, the structure of action manner reflects a morphological constituent of error. But it becomes obvious that including elements with diversified attributes into the structure of manner leads the whole construction to expanding, which predetermines a need to introduce the category of a mechanism. Both notions complement each other while characterizing a misaction via its different qualities and attributes. It is very category of mechanism that introduces another very important quality of error – interaction, interconditionality of elements, phenomena, processes comprising the act. When considering the mechanism of making an error as a complex dynamic system, it is possible to single out: subject of error, attitude of a subject to its actions, its consequences, manner of error, error results, circumstances, connections and relations between actions and erroneous result.
Means of making the error represent constituents used by a person to influence objects of its activity. Consequently, manner and means are constituents of a structural constituent of error, while place, time and situation are conditions of making it. When dissecting error through the prism of behavior acts, it is possible to single out actions, operations, methods, movements used by a person when committing an action (Picture 4), the subjective side of which reflects emotional-volitional and intellectual constituents of a functional constituent of error.
Though, so far as specialists are gaining knowledge, skills and experience, the correlation between major constituents of error (Rivman, 2002) is getting changed that enables to separate the phenomenon of errors of inexperienced workers where an emotional-volitional constituent prevails over intellectual one, thus initializing mechanisms of psychological protection, and a phenomenon of ‘errors of experienced workers’ where an intellectual constituent dominates and initiates generation of coping strategies in problem solving. That is why, the nature of error is characterized as dual: on the one hand, damage, accidents, disasters; and on the other hand – experience in developing a human behavior model in non-standard situations. It is a combination and mixing of human behavior models in non-standard situations that enables to develop tactics and a strategy of behavior under extreme conditions. That is why, quite an extended experience of working in non-standard situations initiates mechanisms of risky behavior that enables one to generate a mechanism of forming direct and indirect prerequisites to erroneous actions under changing environment. Specifically these error actions may lead to severe consequences.
At the heart of an ‘experienced worker’ phenomenon, there are behavior patterns formed on the basis of a professional experience, they have a rigid structure and are not capable to consider changes in production environment generating evident and concealed prerequisites to make a chain of errors growing like a ‘snowball’.
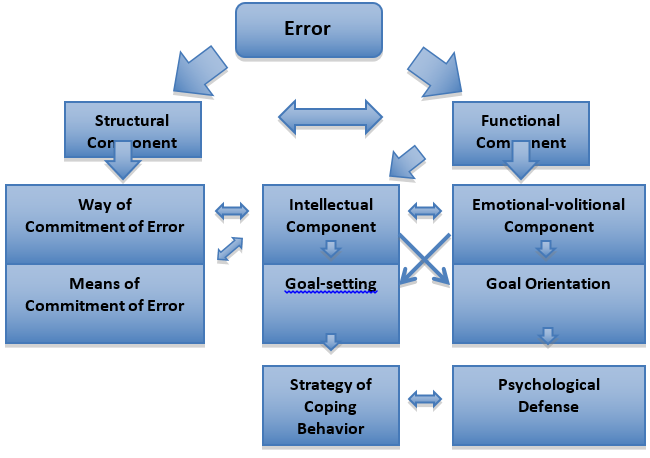
Conclusion
Therefore, the functional constituent of the error includes intellectual and emotional-volitional constituents, interacts with a structural constituent and generates conditions under which personal victimity of an ‘inexperienced worker’ phenomenon originates, while the basis to constitute the error in an ‘experienced worker’ phenomenon is made of professional victimity lying in the dimension of risk-reducing behavior in a non-standard situation. It is a functional constituent of error that is a manageable chain link as it allows forming the error management system at hazardous production facilities.
References
- Fistal, E. Y., Soloshenko, V.V. (2009). Modern possibilities and results of treatment of miners, victims of explosions of methane-coal mixtures. Medicine of emergency, 3-4, 22-24.
- Grishin, V. Y. (2014) Reducing an Additional Risk of Injuries among Mine Workers Predetermined by Violation of Safety Code. Ugol, 10, 68-74.
- Gryzunov, V.V., Gryzunova, I.V. (2014). Vulnerability of Personal Behavior Pattern when Realizing Coping Strategy High Intellectual Technologies and Innovations in Education and Science. Saint Petersburg, 3, 65- 69.
- Gryzunov, V.V., Gryzunova, I.V., Kozlov, G.V., Grishina, A.M. (2015). Professional Victimity as a Determinant of Technical Safety at Mining Facilities. Mining Information and Analytical Letter. 7, 444-452.
- Ilyin, E.P. (2014). Psychology of Individual Differences. Saint Petersburg, Piter, 2014,701.
- Lieberman, A.N. (2006). Technological safety: the human factor.St.Petersburg, 101.
- Naumov, E.S., Tsytsarev, O. I., Naumova, E. Y., Filevskaya, N.S. (2013) A case of mass death of people in the explosion of methane in the coal mine. Medical examination problems, 2(50),13,36-37.
- Rivman, D. V. (2002). Kriminalnaja victimologia. St. Petersburg, 304.
- Safin, A.M. (2013). Phenomen of errors in the structure of human activity. Scientific notes of the Kazan University,155(1),157-162.
- Sarkisov, A.A. (2012). Phenomenon of Public Conscience Perception of a Threat related to Nuclear Power. Research and Development Journal SBbSPU, 2- 3 (154), 9-21.
Copyright information
This work is licensed under a Creative Commons Attribution-NonCommercial-NoDerivatives 4.0 International License.
About this article
Publication Date
20 July 2017
Article Doi
eBook ISBN
978-1-80296-025-9
Publisher
Future Academy
Volume
26
Print ISBN (optional)
Edition Number
1st Edition
Pages
1-1055
Subjects
Business, public relations, innovation, competition
Cite this article as:
Gryzunov, V. V., Mitreykin, V. F., Dzhemilev, E. R., & Chipura, S. I. (2017). Architectonics of Human Error at Production Facilities in Mining Industry. In K. Anna Yurevna, A. Igor Borisovich, W. Martin de Jong, & M. Nikita Vladimirovich (Eds.), Responsible Research and Innovation, vol 26. European Proceedings of Social and Behavioural Sciences (pp. 269-275). Future Academy. https://doi.org/10.15405/epsbs.2017.07.02.35