Abstract
The research results of the development of optimization and systematization activities to carry out maintenance and repair (M&R) of metallurgical units are presented in the article. One of the most important features of the metallurgical enterprises is the necessity for continuous M&R. Companies are forced to suffer great losses for this purpose. That is why even a little cutting down the expenses is a pressing task. The main problem in repairs planning is a mismatch between the requirements for conducting of the works and the limited allocated funds. There is a need in the rankings of all the repair works using a criterion that can solve this problem. The development strategy of any steel plant should provide for a system of optimal planning of repairs at metallurgical enterprises and its integration into the corporate information system. The repair strategies, considered as different approaches to the organization and evaluation of repair and maintenance works efficiency, allow the company to choose the best option.
Keywords: Efficient technologiesmetallurgystrategymaintenance and repair (M&R)repair organizationoptimization of costs
Introduction
Nowadays, the development of efficient technologies of resources takes place mainly at the expense of energy saving works (reducing energy consumption) and energy efficiency (rational use of energy resources), though the efficiency of resource is the capacity for achieving maximum results by the least made efforts, so as to save resources.
Steady, reliable and safe operation of the main technological equipment of industrial enterprises is closely connected with the repair work. At the same time, the cost of equipment performance, its maintenance and repair (M&R) is one of the most significant items of any industrial enterprise expenses.
Metallurgical equipment has very low indices of operational reliability and durability, so the problem of improving the reliability is of particular importance. The repair service employs about 30% of the total number of production personnel and the mechanical equipment cost is up to 40% of the total value of fixed assets. According to various information sources, expenditure for the M&R of the equipment during its use is 5-10 times greater than that used for the manufacture of the new outfit (Glukhov, 2014; Zhirkin, 2002). Therefore, the development of efficient technologies of resources in the field of maintenance management is a timely problem.
Methods
Problems of equipment repair management
Under modern conditions, the cost reduction strategy is being realized by the staff to ensure high competitiveness of the enterprise products. The result is that the work is organized up to the equipment "failures", minimizing the reserves and resource savings for M&R of major units.
In this case, the efficient technologies of resource mean revealing problems in all the systems and links that determine the operation of the technological equipment. This will allow the company to:
analyze the indicators characterizing the stability of the main technological equipment operation at industrial enterprises;
identify the reasons due to which it is necessary to ensure the stability of the main technological equipment and the factors that ensure the smooth operation of the process equipment;
develop measures for improvement of the operation steadiness taking into account the above-mentioned criteria for the optimal functioning of the main technological equipment;
optimize costs for the maintenance and repair of equipment in the planning system;
ensure trouble-free, safe and reliable operation of the main technological equipment.
Management strategies features of equipment repair
The necessity for ensuring the steady functioning of the main process equipment is caused by several reasons, which are as follows:
- High wear of fixed assets, especially in the chemical enterprises, oil and gas, metallurgical and mining industries, and slow updating of the equipment.
- Increasing the technological capacity of production, the growth of volumes of transportation, storage and use of dangerous substances, materials and products, as well as the accumulation of waste products that pose a threat to the population and the environment.
- Increasing the probability of military conflicts and terrorist attacks.
- The availability of a reliable system for the protection of facility personnel from damaging factors;
- The physical stability of the object, i.e. the ability to withstand the effects of damaging factors;
- Ensuring continuity of production by all the necessary resources (raw materials, materials, fuel and energy resources);
- The possibility of full and rapid recovery of production in violation of technological processes and in emergency situations.
Results
The use of any process equipment gives a positive result, which is due to the release of products, improvement of their quality, etc. As a rule M&R costs increase with time due to aging of the equipment elements and deterioration of their technical characteristics, resulting in an increase of funds for the M&R. The growth intensity of the income tends to a decrease during some period of time, as the duration and frequency of repairs and maintenance of equipment increase in the operation process. Then the time comes when the income from the use of the equipment is fully spent to cover operating costs. That is why, to operate the equipment is not economically feasible as the costs of M&R exceeds the economic benefits from its use.
Repairs management methodology oriented towards resource efficiency problems solution can be based on a wide range of strategies. At the same time, a repair strategy means the approaches to the organization and assessment of the effectiveness of M&R activities. It is necessary to consider the features of the basic strategies for managing the equipment repair.
The enterprises process management strategy on the basis of
One of the most effective strategies that enable the company to optimize its program for the M&R of assets, is the strategy of
To identify the problem of M&R the main technological equipment must be ranked according to the following criteria:
units the stoppage of which will not allow producing similar products;
units the stoppage of which will disrupt the rhythm of the work of the subsequent process stages and aggregates;
units the rejection of the repair of which will inevitably lead to the maximum growth of "lost profits" and the deterioration of the financial condition of the company;
units the stoppage of which will not lead to negative consequences.
The problem for the workshop will be a failure of the equipment, which will result in downtime of the shop on the whole, or of the process chain, or of the main technological equipment (Baskakova et al., 2016).
In the current system, the MRO cost management is organized in the framework of plans. The schedules repair and maintenance of metallurgical equipment are organized in the framework of plans in order to anticipate and prevent its downtime.
Budget planning is considered as a management tool, which can and must be used. Budgetary planning is not a new topic for the Russian companies, but, nevertheless, budgeting is either absent or working not at its full capacity at many enterprises. Budgeting is functioning in the system of metallurgical enterprise repairs, although, in reality, it does not play a great role while the effective formulation of budget planning in the organization helps businesses to make decisions more effectively, carry out these decisions and monitor their implementation. The budgeting system allows evaluating in advance the future results of decisions that should be taken today.
The budgeting system effectiveness of repairs at the metallurgical enterprises is manifested in the fact that it allows making rational (reasonable) administrative decisions favorable to the company.
The cost reduction strategy requires optimization of M&R costs, taking into account the ranking of the works according to the type of repairs and "limit of budgetary resources for repair."
The chosen strategy of M&R will enable to distribute the limited resources optimally to provide the necessary performance of equipment and implementation of the "portfolio of orders" (Baskakova et al., 2016).
The analysis of M&R costs and the comparison of the economic efficiency of the chosen methodology for one of the metallurgical enterprises are presented in Table.
It should be noted that the RCM methodology based on TOC reduces the amount of actual repair costs at the most, and it also makes the efficiency greater compared to that of other proposed techniques. To determine the criteria selection of the planned activities in the preparation of repair schedules, specialists, at first, calculate the duration of downtime the problematic equipment may cause due to the lack of this or that event.
The possible loss of profits due to the failure to solve the “problem” may be determined if there is information about the average size of the profit received during the equipment operation (the stream of the profit in the problematic section of the equipment). Depending on the size of the profits loss, the activities are ranked and the priority tables are drawn up. The following algorithm of the events planning for repairing is proposed (Fig.
For scheduling repairs and maintenance of the enterprise as a whole, it is necessary to determine the problematic equipment the downtime of which will lead to the reduction of the profit.
Resource constraints make the company choose the types of M&R of the basic technological equipment which is problematic, and the refusal to repair it will lead to maximum growth of the "lost profits."
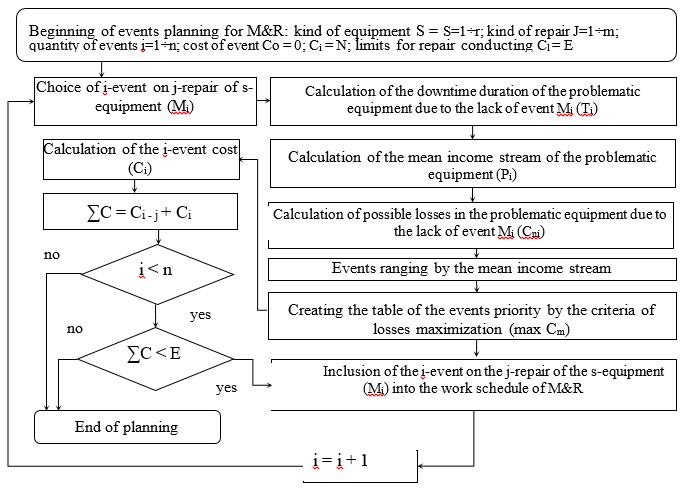
Peculiarities of approaches in the management of maintenance work
The approach from the standpoint of the process involves a more effective achievement of results in the management of the activities and related resources as a process, which is understood as a set of interrelated or interacting activities that transform inputs into outputs. The whole complex of processes grouped according to similar functions, the results of activities or the added value form a business – process, at the output of which the total result is achieved.
In accordance with the process approach in management, business processes, repairs and maintenance are the components of the business process "Production". This process is considered to be auxiliary. The rules of the organization of modern industry should be taken into account: to prevent possible disruption of the normal and uninterrupted course of primary production, i.e. to be preventive; to provide flexibility, mobility, continuity and minimal restructuring in the transition from one product to another in primary production; to promote the production of high-quality products at the lowest cost; to provide the introduction of technological and organizational regulation of the auxiliary processes.
The situational approach in the management of maintenance work is shown in the analysis of problems related to the M&R of the main technological equipment.
The most common, typical problems include the following:
- the lack of the standardized, unified approach to the determination of the cost of repairs: budget allocation is based solely on the "expert" opinion, which often can drastically vary depending on the level of specialization and professionalism of the expert ( a mechanic, an electrician, a power specialist);
- an increase in stocks of spare parts and expenditures for the staff is connected with the desire to be on the safe side, with no significant changes in equipment reliability;
- M&R subdivision of costs for major repairs, routine repairs and maintenance, which has no practical value, but allows concealing the costs. This maintenance service is the most ambiguous expenditure item. Redistribution of actual costs between these types of cost allows manipulating the values of the actual costs for M&R. Moreover, this separation permits understating the actual total budget by eliminating maintenance budget for repairs.
- exclusion of costs for M&R personnel and the personnel on duty from the budget of M&R. This is explained by the fact that the costs of the salaries of the staff are reflected in the general production workshops expenditure and other costs for the M&R are accounted for in the estimates of local costs for repairs and maintenance of fixed assets. Such separate record of costs distorts and gives the incorrect estimates of the costly part for the maintenance and repair costs;
- the inflexible and ambiguous model of estimated pricing of repair works under market conditions. The discrepancy between the estimated cost and the actual, real market value of the M&R works creates problems in planning. In addition, long-term preparation of estimates in non – standard situations (including emergency works) adversely affect the compliance of reliability "cost - quality - price";
- excessive detailing in regulating of certain repair works does not agree with the principle of the system approach to management, the essence of which is that "it is not necessary to overload the model by extra information: there should be a reasonable limit and a certain boundary." Ignoring this rule leads to a decrease in the overall efficiency of the M&R works. The fundamental difference of the M&R with regard to unique and unconventional main technological equipment (individual managerial situations) is the impossibility to use a standard set of regulated operations. In such cases, non-standard, situational thinking of professionals responsible for planning of the M&R works. Detailed regulation is appropriate in integrated overhaul. At the same time, when the works of this nature (current repairs, maintenance) are conducted, the situational approach in the organization of such activities should be used taking into account the results of the monitoring and diagnosing the equipment condition;
- in managing decision-making on the budget costs and the M&R schedules, a limited number of specialists directly serving equipment are often involved. Usually the information on the state of the equipment and the need for repairs and maintenance is mainly possessed by certain specialists, mainly by the third-level managers - foremen and heads of sections. However, the selection of the final version of the decision is up to the managers of the second level - heads of departments, their deputies, and they take full responsibility for that choice. While, according to the methods of development and management of decision-making, it is recommended to create a team with a different-profile (diversified) staff specialization in the analysis of the problems and possibilities of their solution. This provides a synergistic effect. At the same time, there is a need to methodically develop the managerial decisions regarding the organization of repair and maintenance with the use of modern techniques, including democracies such as "brainstorming of problems", the method of Delphi, the nominal group technique, etc. Only methodical development and adoption of specific solutions "at the junction of the views of experts in different fields" allows making the right, effective selection of the best options for problems solving.
- an increase in the equipment downtime is due to ineffective communications (information exchange) between managers of different specializations. This adversely affects the planning of the budget costs and the M&R schedules. Interaction of services should not be based on a personal relationship of managers and specialists and on their individual positions. In such cases, it can be affirmed that the absence of the effective management style - "cooperation" - takes place, according to which each member is able to change its position at the expense of additional information, which allows the targeted use of effects in the M&R system.
Conclusions
Integrated application of the above-mentioned methods, the priority of which is the TOC leads to the redistribution of the budgetary financing of M&R, an increase in the effective operating time of the problematic equipment and a significant increase in profits, which is required by the efficient technologies of resource.
Conceptual directions of increasing the efficiency in the planning of the M&R subsystem may include the following:
- Establishing priorities in the system of equipment repairs.
- The ability to determine the real data about the activities and costs, establishing the lower limit on the M&R costs of equipment, compliance of funding sources with types of repairs and the volume of work related to this M&R kind.
- Identifying the sources and volumes of funding and reproduction of BPA for the effective operation of the equipment based on the minimum cost of maintenance and repair, and reimbursement of costs for hardware upgrades according to management methods using the budgets.
- Optimization of inventory levels, costs and the regulatory framework in order to increase the stability of the system and its linkages with funding sources.
- The calculation and adjustment of the limit of the costs of M&R, depending on the economic situation.
- The ability to rapidly develop options of plans on the basis of calculations automation for a year, a quarter of a year, a month, and the definition of the minimum necessary level of costs on the basis of the allocated limits.
- A decrease in the repair of the main equipment costs by determining the optimal service life, the boundaries of the cost of each type of repair of the main equipment and prevention of emergency repairs.
- Improving the control and planning by choosing the best option based on the borders of the cost of each type of equipment M&R, corresponding to the "bottleneck" and due to the increase of the economic validity of the decisions.
References
- Baskakova, N., Yakobson, Z., & Simaov, D. (2016). The development strategy of the repair services of the enterprise. Moscow. M: INFRA-M (Scientific Thought). www.dx.doi.org/10.12737/19779.
- Dettmer, H.W. (1997). Goldratt’s Theory of Constraints: A Systems Approach to Continuous Improvement. ASQ Quality Press, Milwaukee, WI.
- Glukhov, L. (2014). Reliability of technological machines. M: MISA.
- Goldratt E., M. (1990). The haystack syndrome: sifting information out of the data ocean. New York, NY: North River Press.
- Goldratt E., M., & Cox, J. (1992). The Goal: process of ongoing improvement. New York, NY: North River Press.
- Goldratt E., M., Fox Bob, E. (1986). The race. New York, NY.: North River Press.
- Lubuzh P. (2011). World Class Manufacturing: Survival Tool. Strategy.ru, 40-43. Retrieved from http://strategy.ru/UserFiles/File/Strategy.ru/40-43.pdf
- Noreen, E. W., Smoth, D.A., & MacKey, J. T. (1995). The Theory of Constraints and its Implications for Management Accounting. NY .: North River Press.
- Sedush, V., Sidorov, V. (2009). Changes in the structures of repair of metallurgical enterprises. Metallurgical and Mining industry, 6, 76-78.
- Shuhgalter, A. (2009). Equipment repair problems on the economy of the Russian industrial enterprises. Economy and life, 26, 20-27
- Zhirkin, Y. (2002). Reliability, maintenance and repair of metallurgical machinery. Magnitogorsk: Magnitogorsk NSTU.
Copyright information
This work is licensed under a Creative Commons Attribution-NonCommercial-NoDerivatives 4.0 International License.
About this article
Publication Date
20 July 2017
Article Doi
eBook ISBN
978-1-80296-025-9
Publisher
Future Academy
Volume
26
Print ISBN (optional)
Edition Number
1st Edition
Pages
1-1055
Subjects
Business, public relations, innovation, competition
Cite this article as:
Baskakova, N. Т., Nazarova, O. L., & Simakov, D. B. (2017). Efficient Technologies Of Resource In System Of Metallurgical Equipment Maintenance And Repair. In K. Anna Yurevna, A. Igor Borisovich, W. Martin de Jong, & M. Nikita Vladimirovich (Eds.), Responsible Research and Innovation, vol 26. European Proceedings of Social and Behavioural Sciences (pp. 927-934). Future Academy. https://doi.org/10.15405/epsbs.2017.07.02.120