Abstract
This paper presents the process of formation and transformation of professional ethics. Strengthening the role of ethics in the regulation of professional activities in an innovative society is displayed. The article also highlights the modern approach of large corporations to the formation of all the company's business processes, based on the concept of sustainable development, which not only improves the quality of life, increases the volume of business while reducing the environmental impact and increases positive impact on society, but also creates new opportunities to ensure business growth and retain competitive advantage in the market. The attitude of companies on the environment fits into a broader sector such as that of social responsibility. Social responsibility includes topics such as child labor exploitation, safety and quality or environmental impact of companies. They now receive more attention from the media, because they lead to the development of new legislation, causing some of the responses consumers through demand and are considered by investors for setting up the portfolio.
Keywords: Professional ethicscodes of ethicssocial responsibilitycorporate governanceenvironmental responsibility
Introduction
An engineering profession in comparison with the profession of a lawyer, a doctor or a scientist of the university is relatively young. In Europe, despite the very long history of engineering, actually, "engineers" as a professional class formed only at the end of the XVIII century, and in the United States even later - at the beginning of the XIX century. Polytechnic higher education had finally formed in the first half of the XIX century (Davis, 1998). Today it is an extremely common profession and one of the most fundamental occupations, which still provides social progress worldwide.
It is known that the first code of ethics of engineers was drawn up in the UK back in the middle of the XIX century. In the US, full-fledged ethical reflection of the professional activity of engineers began half a century later. On the eve of the World War I, several professional societies of engineers - among them the American Society of Civil Engineers - wrote the first codes of ethics. This experience has not been very successful, as the researchers say, the codes were complicated, very different from each other, the relationship of communities with business and civil society were not differentiated, etc. (Layton, 1986).
In 1974, the Engineering Council of America published a new Code, which, in fact, marks the formation of engineering ethics. The updated Code of arranged new priorities: engineering community is responsible primarily for the health, welfare and safety of the wide audience.
However, in the 90s the last century engineering ethics began to evolve as a scientific industry, and as a resource for the genesis of the current ethical directions such as a computer, bioengineering, nanotechnology ethics and so forth.
Engineering ethics today is closely connected with other areas of professional and applied ethics such as environmental ethics, business ethics, ethics of technological risks, etc. All of these cultural layers in the beginning of XXI century led to blur of the engineering ethics subject matter (Drucker, 1984).
We live in an era of innovation, the growth of open markets and the world economy. There are new opportunities, requirements and restrictions in keeping with the new technologies, the changing role of the government and the entry of new players on the world scene. That is why the role and responsibility of business is constantly increasing under the influence of market and society (Porter & Kramer, 2006). Although the purpose of making a profit in business is clear, people do not take it as an excuse to ignore the values and norms of behaviour. They expect modern business will responsibly use public resources acting not only for the benefit of their companies, but also for the whole society (Dumova, 2014).
Around the world, companies create and implement business ethics programs to address legal, ethical and environmental problems. These enterprises not only satisfy the needs of its employees, shareholders, communities, but also contribute to the economic well-being of their countries.
In this regard, the problem of business ethics is increasingly attracting the attention of researchers, managers, and community leaders over the past twenty years. A relatively new principle of modern business ethics is the principle of social responsibility (Lenssen, Perrin, Tencati, & Lacy, 2007).
Methods
Social responsibility of business begins to actively and successfully implement worldwide. Companies receive certain benefits from solving the problems of society by investing in the advancement of education, medicine, science, industry (Schwartz, & Carroll, 2003).
In my opinion, the interdependence of society and the business implies an objective choice of business in favor of the socially-oriented economic strategy, and moral. In addition, it is important to note that the actions of managers, on what decisions they make, often depend on the fate of many people.
In recent years many studies have been emerging that analyze the results of social and environmental performances of companies. It is of interest academically to analyze the reasons that drive companies to voluntarily provide information beyond what is legally established. The business need for differentiation, easier access to capital markets that provide greater transparency, the positive relationship between good social responsibility practices and more information are presently being investigated.
Also, other studies have attempted to elaborate methodologies for quantifying and evaluating the results of corporate actions on social responsibility. But there are also international initiatives emerging to provide tools for developing sustainability reporting, in order to provide consumers and investors, and generally all stakeholders, information on social and environmental responsibility of companies.
Results
Social responsibility of the WEG Company
Corporate governance philosophy of the company WEG combines the best business administration traditions established by the founders of the company. The main principles are openness, transparency and accessibility to dialogue with all stakeholders, both internal and external (Berman, Wicks, Kotha & Jones, 1999). In this context, being consistent in its aspirations to be a model of a socially responsible company, WEG has joined the list of companies placing an Initial public offering on the National Stock Exchange Bovespa, for companies which voluntarily assume the obligation to introduce and develop the highest standards of corporate governance (Jenkins, 2009).
Corporation WEG Equipamentos Eletricos S.A. is a multinational, vertically integrated company which was founded in 1961, in the Brazilian state of Santa Catharina. Currently, WEG Corporation is the world's largest manufacturer of electric motors, power motors, transformers and power systems for the transformation and redistribution of power. The company is a full member of many international associations, organizations, institutions engaged in the search, development and implementation of alternative and renewable sources of energy and aspects of energy efficiency improvement.
All actions carried out by corporate governance represented by board of directors, the executive board and the audit committee, according to the corporation management, focused on the achievement of planned indicators of economic, social and environmental performance. Therefore, members of the corporate governance can receive in addition to a fixed salary premium pay depending on the level of the achievable value.
This model promotes a consistent and transparent teamwork on the joint achievement of results, and guidance and consistency in decision-making activities between all units and levels of corporate governance in line with best corporate governance practice.
The model of the company's management system WEG is the Participative Management. The principles of its functioning based on the four components of the system:
• Commissions;
• Quality Control Circles – QCC;
• WEG Quality and Productivity Program – WQPP;
• Continuous Improvement Program - PMC).
Working commissions is considered formalizes system basis for all corporate management systems. Working commissions have the right to decide in the first instance, responding to the purposes and principles of the corporate culture:
1. Improving the decision-making processes
2. Professional development of staff through in-desire in all spheres of the company's work spoken proper expansion and development of the vision system processes.
3. Require the search for consensus
QC Circles are coming at the expense of voluntary staff, and decide to search queries, selection, development and implementation of solutions aimed at improving the quality of products, work processes, increase productivity, improve safety in the workplace, improved ergonomics, sustainable development and improving the working environment. Among the objectives of quality circles, they include the creation of a healthy and happy working environment where there is respect for human nature, and job satisfaction.
Improvement programs of the WEG pursue the goal of achieving international standards of quality and performance in all areas of the corporation. Problems to be solved by the programs cover the areas of business, ecology and environmental protection, health and safety, technological development and increased productivity in general.
In accordance with the program, up to 12.5% of the net profit is distributed among employees. The WQPP system established in 1991 enhances employee participation in company management and provides better integration with the execution of work on the basis of a team approach.
PMC was launched in 2008 and is aimed at finding and implementing solutions to eliminate or reduce losses and costs, more efficient use of company resources. Program operation is based on continuous monitoring of all business processes through a powerful set of management tools built on the concept of Lean Manufacturing. Among other priorities, there are the program management processes of collection, sorting, treatment, reuse, recycling or disposal of waste.
Environmental responsibility of the WEG company
Increasing public interest in the activity of the companies on their environmental responsibility encourages socially responsible companies in a new way to look at this problem, because it is directly related to the quality of life of people living now and for future generations (Johnson, 2003).
Company WEG determines that environmental issues are included in the "DNA" of the company, and are part of its business, part of its strategy, part of its commitment to society. Therefore, the company contributes to the protection of and respect for the environment, considering it a guarantee of the possibility of sustainable development.
The main objectives of environmental management are issues for the prevention of pollution of the environment, continuous improvement and compliance with environmental legislation. This takes into account the technological, financial, operational and business aspects as well as the opinions and expectations of stakeholders.
By the company's environmental directives include:
- Directive of the optimization of consumption of raw materials and components
- Directive on the development of processes and products with the least impact on the environment
- Directive of the optimization of the process control directive, reusing and recycling waste and industrial effluents.
Directive, produced on the basis of socially responsible environmental policy of the company, are the basis for development and implementation of environmental programs.
The program of the reduce electric consumption is designed to introduce energy-saving technologies in all industrial parks of the group of companies, through the use of their own development, training and education, carrier staff and management at all levels. As a result, the program launched in 2011, was achieved in stages tangible effect electric energy savings, which amounted to 2.85%. Implementation of standards of the Energy Department, the relevant requirements of ISO 50001 is confirmed by ISO in 2011. The combined effect of the implementation of the energy consumption of the control of quality standards, the implementation of programs to optimize electrical consumption, staff in these matters let go out to the stable dynamics of reducing energy consumption 1 671.2 MW per year.
The program of the careful use of water is designed to implement careful water consumption technologies for industrial applications. The issue of water consumption is very important in the dynamics of growth of corporate production. (Fig.
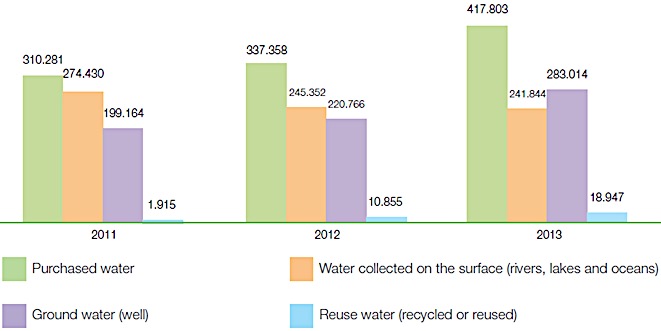
The cumulative effect of the introduction of this program reduces the water consumption, the implementation of treatment and reuse of industrial water programs, staff in these matters have allowed the company to save more than 2 400 tons of fresh water per year (Fig.
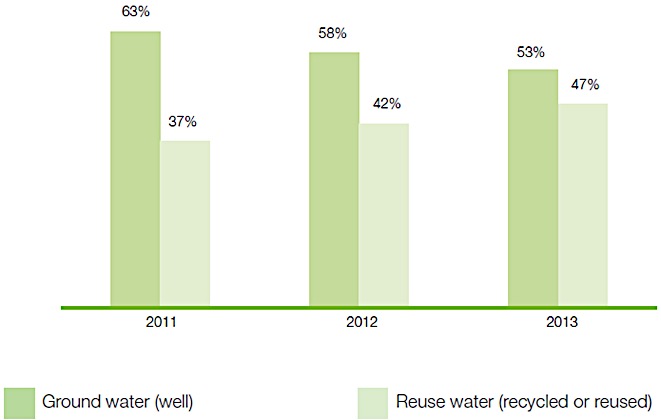
The program of the wastewater aims to develop a wastewater management system in accordance with the applicable environmental regulations. The bulk of the water shall state the cleaning companies, and the rest is returned to the natural water pools after purification and filtration in sewage treatment plants Corporation.
The main part extends biological sewage purification, the remaining portion passes through the various combined biological, physical and chemical types (Fig.
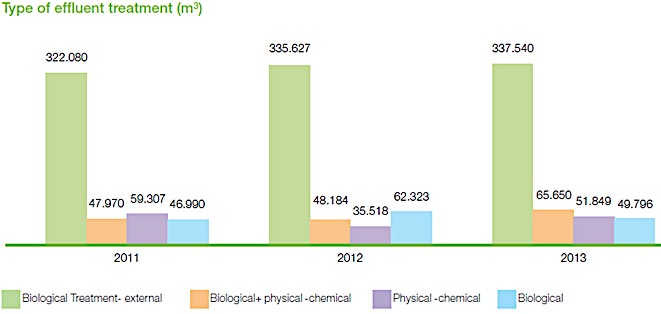
According to the report in 2013, there were no accidental discharges and sewage leaks.
The program of the air emissions control is aimed at solving problems and continuous development of harmful air emissions control technologies. Corporation WEG calculates the amount of equivalent greenhouse gas emissions in accordance with ISO 14064 since 2010. A number of programs aimed at reducing or countering an increase in emissions, including the already mentioned program for improving energy efficiency, program "Solidarity companion", as well as a program to reduce the consumption of acetylene and liquefied gases in welding processes. Emissions accounting is carried out in three categories of influence:
Scope 1 – direct emissions of energy greenhouse gases owned or controlled by the company;
Scope 2 - indirect greenhouse gases emissions from the purchase of electric energy;
Scope 3 – sources of energy not owned or not controlled by the company, including emissions from the use of auto-transport, and personnel activities provoked, such as exhaust emissions of internal combustion engines and aircraft turbines during business trips, commute, etc.
The program of the solid industrial waste management focuses on the development of problem solving and continuous improvement of the quality management of solid wastes arising from the production processes of plants. The quality of this process depends on the efficiency of the collection technology, filtration, separation, reuse and safe disposal of high-quality, in accordance with current environmental legislation; economic, financial, technological capabilities of the company. All processes are focused on the idea of the maximum possible re-use of waste in the production of its products, which in addition to environmental performance is also a plus in economic terms, reducing the raw material cost of the acquisition. Throughout its history, the company has developed several initiatives to improve the reuse of processes and recycling of solid waste, including on methods of "kaizen", such as "Zero Waste".
According to the report in 2013, 70% of the volume of solid waste were recycled again. Accounting for solid waste volumes is carried out in three categories (Fig.
Category 1 – recyclables waste;
Category 2 - non-recyclable / non-hazardous waste;
Category 3- non-recyclable / hazardous waste.
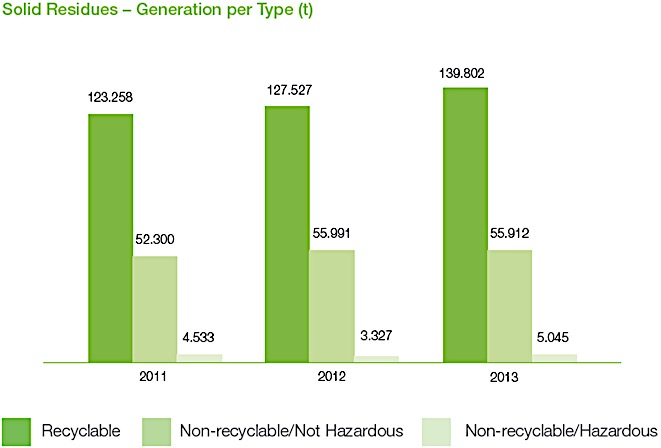
Although the previous graph shows that there is a growth in emissions from 2011 to 2013, over the same period, thanks to implementing programs, the specific waste index (kg/annual income) declined significantly, about 2.65% (Fig.
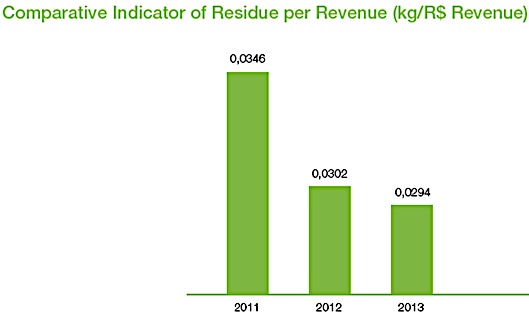
About 37% of the total solid waste was recycled by its own group enterprises, 32.7% of the total volumes of solid waste were delivered to third-party processing companies, 29.5% have been sent for disposal of industrial waste storage as not representing a threat to the environment, 0.9% of energy used in the co-generation.
According to the report in 2013 year WEG company is not imported and exported hazardous waste.
Company WEG maintains records of two types of investments in environmental protection, where:
1st type - an investment / operating costs associated with the handling and disposal of waste, reduction of atmospheric emissions and industrial waste, the acquisition of environmental control equipment, environmental liability insurance and depreciation of technical equipment and consumables to them, and service, in addition to operation;
2nd type - an investment related to the cost of labor and training, which operate in the field of environmental management, research and development, certification of environmental management systems and cleaner production. The total investment for the period from 2011 to 2013 is presented in the following diagram (Fig.
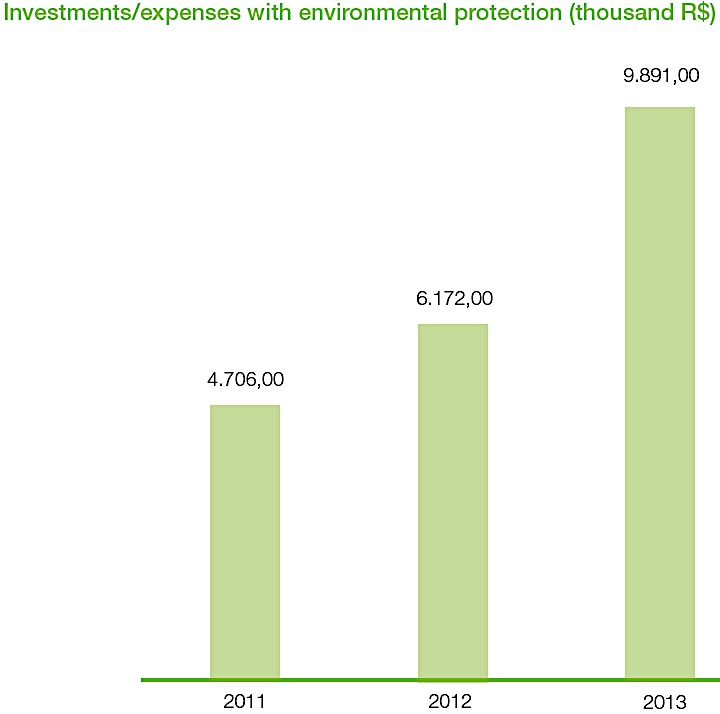
The program of the utilization of electric motors is a very serious addition to the business model of the company ‘WEG’. In fact, the program allows the user to get rid of inefficient old equipment in exchange for the installation of new energy-saving. Thus, in addition to direct benefits from the transaction, the customer receives a competent solution to improve energy efficiency, enhance the level of social environmental responsibility, which is the most valuable component for the participants of the program in the long term.
Conclusions
Company WEG has been selected by the object of study, because it is a prominent representative of the type of global corporations that have managed to make a breakthrough in its development by attracting the best in the field of strategic management competencies. During our research we found out that today the strategic management can be successful only where it builds within a sustainable development paradigm, based on the concept of social responsibility, stakeholders, corporate citizenship.
In conclusion, we note that the understanding and adoption of business ethics as the internal rate today are obligatory for engineers and managers, and especially - for the employer. Management, as a very specific activity, requires managers to take care of the limits and consequences of their actions. In recent years, many businessmen have begun to realize that sustainable development of companies, combining economic, social and environmental factors leads to a decrease in business risks, strengthen competitiveness, increases staff efficiency and customer loyalty, improves the company's reputation, creates a positive contribution to the business community the economic and social development of the regions of its presence.
References
- Berman, S.L., Wicks, A.C., Kotha, S. & Jones, T.M. (1999). Does stakeholder orientation matter? The relationship between stakeholder management models and firm performance. Academy of Management Journal, 42 (5), 488–506.
- Davis, M. (1998). About the milestones of the historical path of the western "engineering profession". New York: Oxford University Press.
- Drucker, P.F. (1984). The new meaning of corporate social responsibility. California Management Review, 26 (2). 53–63.
- Dumova, L.V. (2014). Analysis and development of methods of assessing the effectiveness of the system of corporate social responsibility of mining and metallurgical complex. Modern problems of science and education, 4.
- Jenkins, H.A. (2009). Business opportunity ‘model of corporate social responsibility for small— and medium-sized enterprises. Business Ethics: a European Review, 18 (1).
- Johnson, H. (2003) Does it pay to be good? Social responsibility and financial performance. Business Horizons, 46 (6), 34–40.
- Layton, E.T. (1986). The Revolt of the Engineers. Baltimore: John Hopkins University Press.
- Lenssen, G., Perrin,i F., Tencati, A. & Lacy, P. (2007). Guest editorial. Corporate Governance: The international journal of business and society, 7 (4), 352-353.
- Porter, M. & Kramer, M. (2006). Strategy and Society: the Link Between Competitive Advantage and Corporate Social Responsibility. Harvard Business Review.
- Schwartz, M.S. & Carroll, A.B. (2003). Corporate social responsibility: A threedomain approach. Business Ethics Quarterly, 13 (4), 503–530.
Copyright information
This work is licensed under a Creative Commons Attribution-NonCommercial-NoDerivatives 4.0 International License.
About this article
Publication Date
20 July 2017
Article Doi
eBook ISBN
978-1-80296-025-9
Publisher
Future Academy
Volume
26
Print ISBN (optional)
Edition Number
1st Edition
Pages
1-1055
Subjects
Business, public relations, innovation, competition
Cite this article as:
Shangaraeva, L., & Saychenko, A. S. (2017). Social And Environmental Responsibility Of The Company. In K. Anna Yurevna, A. Igor Borisovich, W. Martin de Jong, & M. Nikita Vladimirovich (Eds.), Responsible Research and Innovation, vol 26. European Proceedings of Social and Behavioural Sciences (pp. 897-905). Future Academy. https://doi.org/10.15405/epsbs.2017.07.02.116