Abstract
Presently, the challenges of environments in the world have resulted to the formation of many policies with focus on environmental at both local and international level. This also involves many sectors such as manufacturing firms and industries, researchers and professionals. However, in the construction sector, there are attempts to minimise or eliminate the effects of environmental as a result of production of cement and reduce the usage of cement in concrete production. Therefore, the focus of this research is the utilization of blended metakaolin (MK) and glass sludge waste (GSW) on ratio of 1:1 as partial cement replacement of 0, 5,10, 20 and 30 percentages respectively. Tests on mechanical properties of the blended concrete were tested at 7, 28, 56 and 90 days respectively. It was observed in the findings that the blended GSW and MK improve both compressive and flexural strength and this was noticed to be because of the high rate of pozzolanic activities of the blended GSW and MK. Likewise, the findings showed that the blended concrete has a significant impact on concrete’s UPV at 28 days of age. This proved that the blended GSW and MK can be used in concrete production as binder and contribute to sustainability of environment.
Keywords: Metakaolin, glass sludge waste, mechanical properties, environmental impact, concrete
Introduction
Going by upsurge in environmental issues, the term sustainability has now become a household word (Hanif, 2017). Based on the definitions pronounced by the Developments of United Nations and World Commission on Environment, term sustainability indicates, attaining the present generation needs without denying the future generation the potentials to attain their own needs (IMO, 2010;WCED, 1987). In the construction industry, concrete is referred to a vital material, hence so important and globally utilized because of its high durability and feasibility relative to economic aspect (Hanif, Lu, Cheng, Diao, & Li, 2017a). Cement, which is the major ingredient of concrete production, has been adjudged to be a source of greenhouse gases especially in the course of production. In this contemporary age, the yearly global cement production was established to have grown from 1.0 billion tons to almost 1.7 billion tons, which can be consider to be sufficient for the production of 1 m3 of concrete per individual, going by the current world population (Gartner, 2004). Based on this fact, the cement industry is often spoken of being in a season of fast growth. Nevertheless, there was an uprising challenge in the industry about the issue of environmental impact and importantly about the emissions of carbon dioxide (CO2). According to literatures, almost 7% of the whole global CO2 emissions were from the worldwide production of cement (Malhotra, 2002; Benhelal, Zahedi, Shamsaei, & Bahadori, 2013). Apart from this, the production of cement includes severe environmental effects, like pollution through dust and large consumption of energy which is needed for plasticity temperature of 1300 degree and above. Relative to this development, there has been a great challenge for the cement industry in the last decade to efficiently manage their CO2 emissions. Out of all four cardinal technology point out in the literatures as way out (Ogbeide, 2010), the use of cement blended with supplementary cementitious materials (SCMs) like FA, SF, MK, GGBS and any other suitable industrial by product is regarded as the most efficient and economical technology and it can be readily utilized in the production of ready-mixed concrete (Becknell & Hale, 2011; Mala, Mullick, Jain, & Singh, 2013). The process of incorporating these natural and industrial by-products as partial cement substitution in concrete production has been accepted globally (Hanif, Kim, Lu, & Park, 2017b). The use of these entire natural and industrial by products has been proven to minimize the emission of CO2 and also lower the effect on environmental related hazard connected to waste and landfill.
Industrial by products recycling goes further to forestall misuse of natural resources and minimize the limited resources consumption and not only that they are eco-friendly but as well economic benefits. Industrial by products of waste glass currently supplied at 700,000 to 800,000 tons annually and out of which seventy percents are being recycled, although glass is not subject of recycled except waste glass bottles. Nearly 300,000 tons of waste glass sludge is produces on annual basis and the whole amount is usually discarded in landfills (Rashad, 2014). Glass sludge waste (GSW) is a by product in the process of plate glass. The use of WGS at 10% was confirmed to be efficient in the enhancement of the apparent density, porosity, loss of fire and water absorption of ceramic products (Tiffo, Elimbi, Manga, & Tchamba, 2015). Likewise, (Ganisen, Mohammed, Nesan, and Kanniyapan 2015), declared that GSW enhance the resistance of thawing and freezing with or without de-icing salts, surface scaling resistance and chloride ion penetration in concrete. Therefore, the air of this research study is to investigate the impact of various percentage replacement of cement with GSW on some of the mechanical and durability properties.
Metakaolin (MK) is a calcined kaolin and a mineral admixture that is consist of both alumina and silica, which was part of Portland cement concrete. Concrete that contain MK has its’ durability and mechanical properties influenced by the high degree of pozzolanic reaction as well as filling effects (Norhasri, Hamidah, Fadzil, & Megawati, 2016). Even though, Duan, Yan, and Zhou (2016) examined the microstructure and mechanical properties and microstructure of blended Mk and fly ash geopolymer paste, the study on the incorporation of MK blended with glass sludge waste has not been thoroughly reported. Therefore, this study aimed at examines the influence of blended MK and GSW on some mechanical and durability properties of concrete.
.
Problem Statement
According to literatures, almost 7% of the whole global CO2 emissions were from the worldwide production of cement (Malhotra, 2002; Benhelal et al., 2013). Apart from this, the production of cement includes severe environmental effects, like pollution through dust and large consumption of energy which is needed for plasticity temperature of 1300 degree and above. Relative to this development, there has been a great challenge for the cement industry in the last decade to efficiently manage their CO2 emissions.
Research Questions
Based on the challenges, this research study aimed to answer the following:
- Can blended MK and GSW make a good partial replacement of cement in concrete production?
- What is the effect of the incorporation of blended MK and GSW on properties of concrete?
- What is the optimum percentage of blended MK and GSW incorporation in concrete?
Purpose of the Study
The aim of this study is to investigate the influence of blended MK and GSW incorporation as partial binder replacement on some concretes’ mechanical and durability properties.
Research Methods
Portland composites cement (PCC) supplied locally were used in the research and the GSW obtained from Schott Glass in Penang, Malaysia was used in different percentage substitution of pcc in 5%, 10% and 20%. MK was produced from natural Kaolin in the laboratory, ground to the fineness using ball mill and characterized as explained by (Ramli & Alonge, 2016). The specific gravity was 2.51. The chemical compositions of PCC, MK and GSW are shown in Table 1. The GSW was de-moisturized in an oven at average temperature of 105±5oC and the fineness particle size of 4.03µm, which was achieved in the laboratory using ball mill machine. The fine aggregate was natural sand obtained locally. It has a fineness modulus of 1.70 and specific gravity of 2.60. It passes through 0.60mm sieve and the sieving was done in compliance with (BS, 1992). The coarse aggregate was of various sizes with the maximum size of 20mm. Portable water from local authority in Penang state of Malaysia was used. The mixes design was done in accordance with ACI 211.1R-91. The concrete mix proportion is shown in Table 2. The specimens were all cure under the ambient temperature of 37±2, open air within the laboratory space.
The methods of test of all property were all in accordance to the prescribed standard of tests. The test was done according with BS EN 12390-3, the flexural test was according to BS EN 12390-5; 2012. The porosity test was conducted according to BS 1881-122, while, water absorption was done according to BS 1881-122
Findings
Compressive strength
The result of all compressive strengths test for the specimens is shown in Figure 1. The result showed that Control specimen had the highest strength at 7 days while 5% MG had 12.16N/mm2 which indicates that the control is 28.38% higher than the specimens of MG that recorded the highest strength. At 28days surprisingly, 10% MG recorded the highest strength of 19.31N/mm2, which is 1.76% above the control. But, at 56 days and 90 days, 5%MG specimens recorded 22.96 and 23.37 N/mm2 respectively. This is 8.41% and 7.49% respectively above the control specimen. This may be as a result of slow pozzolanic reaction of MG. The higher strength attained by MG incorporated concrete was an indication of improved pozzolanic reaction which produced C-S-H formation that is higher. The properties of GW that influence pozzolanic behaviour in the concrete are its chemical composition and fineness as well as pore solution for proper reaction. Since the GW pozzolanic properties were first acknowledge at particle sizes below 300lm and at the particle size below 100Im, glass ware can instigate pozzolanic reactivity at very low replacement of cement at 90days (Imbabi, Carrigan, & McKenna, 2012; Rashad, 2014). Meanwhile, the combination of metakaolin which is finer in particle size activates the pozzolanic reaction. The result conforms to the result of research conducted by Khmiri, Samet, and Chaabouni (2012) and Khmiri, Chaabouni, and Samet (2013).
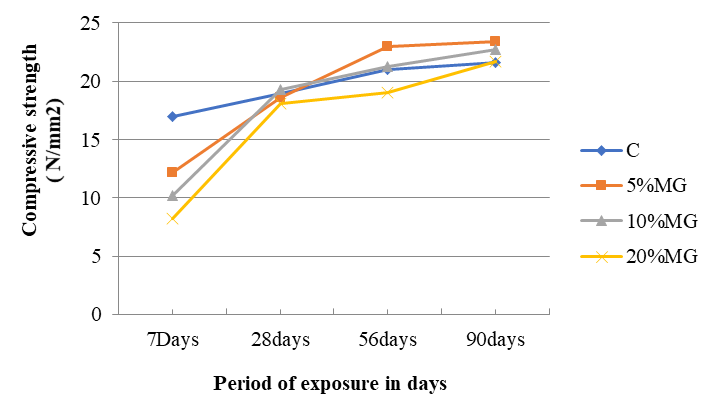
Flexural strength
Flexural strength of all specimens’ results at all ages of 7, 28, 56 as well as 90 days are presented in Figure 2. The result showed continuous increase of flexural strength over the ages. At the ages of 7, 28 and 56 days, the control has the highest flexural strength while the 5%MG recorded highest flexural strength among the MG specimens. But at 90 days 20%MG recorded the maximum flexural strength of 3.49 N/mm2 compare to control specimen that recorded 3.40N/mm2. This agrees with the result of other past research studies (Imbabi et al., 2012; Rashad, 2014; Nassar & Soroushian, 2011).
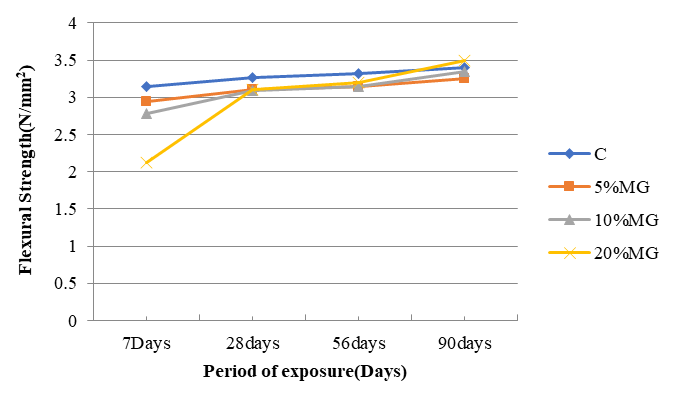
Water Absorption
The result of water absorption test for all specimens showed that the water absorption percentage decreases as the exposure period increase from ages of 7 days until 90 days (Figure 3). When compared to control specimen, all MG specimen recorded reduction at higher rates than the control specimens. At 90 days, the percentage reduction for all the MG specimens of 5%, 10% and 20% recorded 3.09%, 3.13% as well as 2.97% respectively when it was compared to what was recorded by the control specimen. This may likely be as a result of continuous process of hydration in the mix. The hydration was assumed to fill up cement particle pore, hence reduce pores diameter.
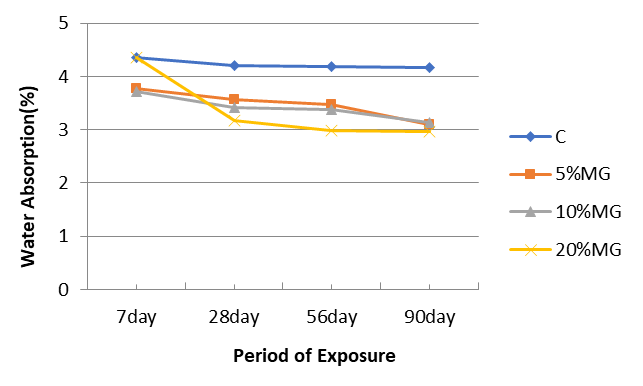
Porosity
Since concrete strength is basically the function of the concrete porosity. The porosity result is shown in Figure 4. It showed that there is reduction in porosity while the period of exposure increases. However, the reduction was more pronounced between the ages of 28days and 90days for specimens of 5%MG than any other MG specimens, although the values of porosity recorded by all MG specimens are lower than control specimens. At 7 days, 5%MG recorded 3.99% reduction compare to control, while at the age of 28, 56 and 90 days, it was 12.01%, 4.59%, and 6.32% respectively. But 10%MG specimen performed better among the MG specimens.
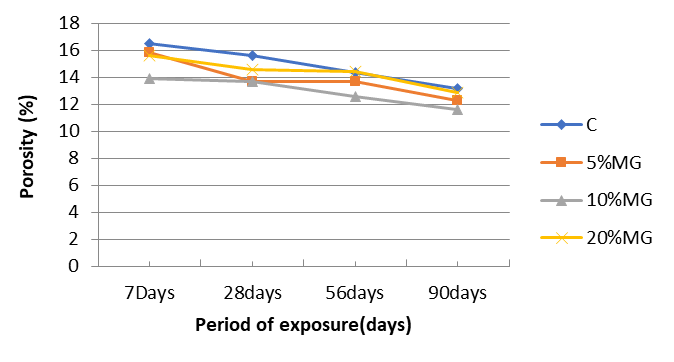
Conclusion
The results of the research study showed that MG can be used as supplementary cementitious materials for binder replacement in the production of concrete. The strength of 5%MG proved to be better than all other MG specimens, while the result of 10%MG was observed to be better than 20%MG. It can be summarized that the highest percentage of partial cement replacement should be 10%MG while 5%MG could produce best properties than other percentage replacement. The chemical composition of WG powders can be acknowledged as pozzolanic material based on ASTM standard. The optimum MG contents should be 10% in consideration of the compressive strength at 90 days. Generally, MG blended can reduce cement production cost at average of 14 %. Similarly, the production of 6 tonne MG blended concrete brings about a reduction of carbon dioxide emission from the production of cement and conserve the environment positively by means of green- house gas emission reduction as well as particulate production.
References
Becknell, N. P., & Hale, W. M. (2011). Effect of slag grade and cement source on the properties of concrete. International Journal of Concrete Structures and Materials, 5(2), 119-123. https:// doi.org/
Benhelal, E., Zahedi, G., Shamsaei, E., & Bahadori, A. (2013). Global strategies and potentials to curb CO2 emissions in cement industry. Journal of cleaner production, 51, 142-161. DOI:
British Standard (BS) (1992). BS-882: Spesification for aggregates from natural sources for concrete.
Duan, P., Yan, C., & Zhou, W. (2016). Influence of partial replacement of fly ash by metakaolin on mechanical properties and microstructure of fly ash geopolymer paste exposed to sulfate attack. Ceramics International, 42(2), 3504-3517. DOI:
Ganisen, S., Mohammed, A. H., Nesan, L. J., & Kanniyapan, G. (2015). Critical Success Factors for Low Cost Housing Building Maintenance Organization. Jurnal Teknologi, 74(2).
Gartner, E. (2004). Industrially interesting approaches to “low-CO2” cements. Cement and Concrete research, 34(9), 1489-1498.
Hanif, A., Lu, Z., Cheng, Y., Diao, S., & Li, Z. (2017a). Effects of different lightweight functional fillers for use in cementitious composites. International Journal of Concrete Structures and Materials, 11(1), 99-113. DOI:
Hanif, A. (2017). Recycled Aggregate Use in Precast Concrete: Properties & Applications. LAP LAMBERT Academic Publishing.
Hanif, A., Kim, Y., Lu, Z., & Park, C. (2017b). Early-age behavior of recycled aggregate concrete under steam curing regime. Journal of Cleaner Production, 152, 103-114. DOI: 10.1016/ j.jclepro.2017.03.107
Imbabi, M. S., Carrigan, C., & McKenna, S. (2012). Trends and developments in green cement and concrete technology. International Journal of Sustainable Built Environment, 1(2), 194-216. DOI:
International Maritime Organization (IMO) (2010). International Convention on Standards of Training, Certification and Watchkeeping for Seafarers, 1978/1995/2010.
Khmiri, A., Samet, B., & Chaabouni, M. (2012). A cross mixture design to optimise the formulation of a ground waste glass blended cement. Construction and Building Materials, 28(1), 680-686. DOI:
Khmiri, A., Chaabouni, M., & Samet, B. (2013). Chemical behaviour of ground waste glass when used as partial cement replacement in mortars. Construction and building materials, 44, 74-80. DOI:
Mala, K., Mullick, A. K., Jain, K. K., & Singh, P. K. (2013). Effect of relative levels of mineral admixtures on strength of concrete with ternary cement blend. International Journal of Concrete Structures and Materials, 7(3), 239-249.
Malhotra, V. M. (2002). Introduction: sustainable development and concrete technology. Concrete International, 24(7).
Nassar, R. U. D., & Soroushian, P. (2011). Field investigation of concrete in corporating milled waste glass. J. Solid Waste Technol. Manage, 37(4), 307–319. Retrieved from http://news.msu.edu/media/documents/2012/02/95cae7f7-726c-4fb5-b1be-7a0991fbea6f.pdf
Norhasri, M. M., Hamidah, M. S., Fadzil, A. M., & Megawati, O. (2016). Inclusion of nano metakaolin as additive in ultra high performance concrete (UHPC). Construction and Building Materials, 127, 167-175. DOI:
Ogbeide, S. O. (2010). Developing an optimization model for CO2 reduction in cement production process. Journal of Engineering Science & Technology Review, 3(1). http://www.jestr.org/ downloads/volume3/fulltext172010.pdf
Ramli, M. B., & Alonge, O. R. (2016). Characterization of metakaolin and study on early age mechanical strength of hybrid cementitious composites. Construction and Building Materials, 121, 599-611. DOI:
Rashad, A. M. (2014). Recycled waste glass as fine aggregate replacement in cementitious materials based on Portland cement. Construction and building materials, 72, 340-357. DOI:
Tiffo, E., Elimbi, A., Manga, J. D., & Tchamba, A. B. (2015). Red ceramics produced from mixtures of kaolinite clay and waste glass. Brazilian Journal of Science and Technology, 2(1), 4. DOI:
World Commission on Environment and Development (WCED). (1987). From One Earth to One World: An Overview. Oxford: Oxford University Press.
Copyright information
This work is licensed under a Creative Commons Attribution-NonCommercial-NoDerivatives 4.0 International License.
About this article
Publication Date
26 December 2017
Article Doi
eBook ISBN
978-1-80296-950-4
Publisher
Future Academy
Volume
2
Print ISBN (optional)
-
Edition Number
1st Edition
Pages
1-882
Subjects
Technology, smart cities, digital construction, industrial revolution 4.0, wellbeing & social resilience, economic resilience, environmental resilience
Cite this article as:
Richard*, A. O., Awang, H., Ying, K., & Kolapo, O. S. (2017). Properties Of Blended Metakaolin And Glass Sludge Waste As Binder In Concrete. In P. A. J. Wahid, P. I. D. A. Aziz Abdul Samad, P. D. S. Sheikh Ahmad, & A. P. D. P. Pujinda (Eds.), Carving The Future Built Environment: Environmental, Economic And Social Resilience, vol 2. European Proceedings of Multidisciplinary Sciences (pp. 385-392). Future Academy. https://doi.org/10.15405/epms.2019.12.37