Abstract
This study aims to analyse previous studies on Six Sigma, lean, Lean Six Sigma, and lean accounting as four main quality improvement practices and management frameworks of a lean organisation. This paper builds on past literature by undertaking a quantitative analysis of four business quality improvement practices in business. This study also reveals research gaps and areas of interest for future research agendas in a more comprehensive lean framework. A literature study was undertaken to gather data and information from academic journal articles. Despite a relatively large number of research findings on Six Sigma, lean, Lean Six Sigma, and lean accounting, this study discovered that they are limited to a few sectors namely, healthcare, manufacturing, and automotive industry or sector, and critical success factors as main focus have been addressed mainly by Lean Six Sigma studies. It was also shown that there is still a significant discrepancy among researchers in writing these business improvement practices, and it is noted that implementing lean accounting is a radical change to an organisation’s accounting, control and measurement system.
Keywords: Six sigma, lean, lean six sigma, lean accounting, sustainability performance
Introduction
Successful companies represent a key ingredient for developing nations. Over the years, the manufacturing industry has reported positive trends toward Malaysian development, with a growth of 3.4 percent in the fourth quarter of 2020 as compared to a 2.6 percent decline in the preceding quarter (Neoh & Lai, 2021)). However, rapidly global competition and changes in the business environment, advanced technology, organisational structures, and management accounting practices (Kamal, 2015) have forced companies to implement conventional management accounting (Ahamadzadeh et al., 2011; Al-Omiri & Drury, 2007) and comprehensive quality management practices (Fullerton et al., 2014). Ngu et al. (2020) highlighted that manufacturing practices in Malaysia and other developing nations are unsustainable without the implementation of sustainable manufacturing practices. Therefore, the manufacturer must switch its manufacturing strategy to remain sustainable and reinforce the most effective strategies for adapting businesses in this turbulent environment (Gukasyan et al., 2022; Sheridan, 1990). Management accounting is principally related to measuring processes and providing operational and financial information such as cost-effectiveness that guides and supports managerial towards motivates behaviors, and cultural value is created to help an organisation achieving its ultimate objectives (Bell et al., 2004). Since 1980, the companies have focused their strategy more on value creation (Sugahara et al., 2017) and consequently, new strategic directions have emerged.
The recent pandemic of COVID-19, which affected the global economic and business environment, requires organisations to restructure their business strategy to sustain financial performance and remain competitive in the business market (Soltani et al., 2020). Hence, improving the quality of the manufacturing system while reducing waste and defects and improving the operating system within the processes to sustain the business performance (Malik, 2016). Thus embedding advanced lean practices; Lean Six Sigma (LSS) (Habidin et al., 2016) and lean accounting (B. H. Maskell & Baggaley, 2006), in existing processes and accounting measurement respectively, might lead to valuable organisational practices (Maskell & Baggaley, 2006). LSS derived from a combination of two quality management frameworks, namely Lean and Six Sigma (Habidin et al., 2016). LSS was developed by Bill Smith and Jack Welch at Motorola in General Electric in 1995 from the initial implementation of Six Sigma in 1980s (Pepper & Spedding, 2010). It is acknowledged that the Six Sigma can respond to and identify business problems based on five-phased DMAIC tools (Define, Measure, Analysis, Improve, Control) (Pepper & Spedding, 2010). Moreover, Six Sigma is recognised in previous studies that understand the customer’s requirements and helps implement the policy in a structured manner (Gupta et al., 2020; Salah & Rahim, 2019). Specifically, this study presents a review analysis of four lean management framework, specifically, Six Sigma, Lean, LSS and lean accounting, with the objective to discuss the available studies on the implementation of Six Sigma, Lean, LSS and lean accounting in a lean organisation. It is essential to highlight the benefits derived from the findings of this research that significantly contribute to both theoretical and practical aspects. The analysis substantially contributes to the academic literature by expanding the limited current body of knowledge on lean literature and the development of the conceptual framework for advanced lean manufacturing practices. This study also contributes to and helps the researchers to understand the real phenomena of lean practices are coherent or not in the manufacturing industry. The paper is organised as follows; the next chapter will discuss the review of the literature and a detailed analysis on the Six Sigma, Lean, LSS and lean accounting, followed by quantitative research methodology, result and discussion and conclusion and implication of the study.
Analysis of Literature Review
This section discussed the previous studies on Six Sigma, lean, Lean Six Sigma (LSS) and lean accounting of the lean organisation. This study analyse previous articles to understand the nature of the quality improvement system of a lean organisation.
Six-Sigma
The Six Sigma initially developed by Motorola as a business improvement approach to eliminate defect and reduce the possibilities for variation and fault (Drohomeretski et al., 2014; Shokri, 2017). Six Sigma is a strategy for managing global competitiveness through ongoing development and superior corporate performance (Shokri, 2017; Shokri et al., 2014). Moreover, Six Sigma encourages the deliberate and methodical alignment of project management, statistical thinking, and quality improvement (Habidin & Yusof, 2013). The study acknowledges that Six Sigma is quantitative decision-making and is commonly referred to as a mechanism of business excellence strategy (Gaikwad & Sunnapwar, 2020) and is described as business-oriented, project-oriented and customer-oriented (Assarlind et al., 2013; Nakhai & Neves, 2009). Several advantages of Six Sigma are identified, including enhancing services, processes, products and financial performance of the organisation (Nakhai & Neves, 2009). Since Six Sigma focuses on quantitative facts and data, subjective decision-making is reduced through trustworthy data gathering and analysis (Nakhai & Neves, 2009) through the application of Six Sigma’s fundamental process improvement, DMAIC (Define, Measure, Analysis, Improve, Control) (Gaikwad & Sunnapwar, 2020). However, previous studies have argued that the Six Sigma implementation was limited within an organisation due to poor project selections, resources limitations, internal resistance, higher initial cost, higher failure rate if not implemented properly and can harm customer satisfaction (Antony et al., 2022; Antony & Desai, 2009).
Lean practices
The lean philosophy has emerged in the seminal book of The Machine That Changed the World: Based on the Massachusetts Institute of Technology of the Toyota Production System written by Womack, Jones and Roos in 1990 (Womack et al., 1990). The author has presented the results of a major benchmarking study on the automobile industry, which presented that the performance success of Japanese plants was far ahead of other plants (Wilson, 1997; Womack et al., 1990; Womack & Jones, 2003). Lean principles focus on waste and non-value added elimination (Chavez et al., 2015; Womack & Jones, 2003) explained that, moving towards the elimination of all waste in order to develop an operation that is faster, more dependable, produces higher quality products and services, and operates at low cost (Womack et al., 1990; Womack & Jones, 2003). According to Chavez et al. (2015), lean principles focus on eliminating all kinds of waste. The unnecessary process was eliminated when lean take over by removing unnecessary parts or waste. Foundation of lean theory, supported by Womack and Jones (2003, 2005), there are seven types of waste, as identified by Shingo during the development of the Toyota Production System, Taiichi Ohno, namely defects, overproduction, waiting time, non-utilise talent, transportation, inventory, motion and extra processing. Chavez et al. (2015) have identified waste in the manufacturing environment, including defects, overproduction, transport, excessive inventory, waiting time or other factors that may disrupt the smooth flow of goods and services along the business transformation process. Lean practices is recognised as one of the modern managerial techniques and promoted as an effective method of improving organisational performance (Valmohammadi & Dadashnejad, 2021) and facilitating a company’s transition to a green environment (Gaikwad & Sunnapwar, 2020).
Lean Six-Sigma (LSS)
Lean Six Sigma (LSS) is acknowledged as one of the most successful business transformation programmes that have been developed by combining two total quality management (TQM) performance improvement tools; lean and Six Sigma (Chugani et al., 2017; Habidin & Yusof, 2013). According to Snee (2004), LSS is a corporate strategy and technique that improves process performance, resulting in higher customer satisfaction and better bottom-line results. Numerous studies have looked into various facets of LSS in organisations of various sizes from a research standpoint (Assarlind et al., 2013; Gaikwad & Sunnapwar, 2020; Hallam et al., 2018; Shokri et al., 2014). Albliwi et al. (2015) conducted a systematic literature review and discovered an increase in LSS research in the manufacturing and health industry over the previous several years. Likewise Six Sigma, LSS aims to eliminate waste elements and defects through the systematic reduction of variability and defects (Gaikwad & Sunnapwar, 2020) such as movement, time, material, process, energy, transport and environment (Habidin et al., 2016). LSS has the advantage of incorporating cost and cycle time reduction (lean) and sustainable continuous improvement and profitability (Six Sigma) (Pepper & Spedding, 2010; Salah & Rahim, 2019). Moreover, LSS is also recognised as a green way to reduce environmental waste (Chugani et al., 2017; Gaikwad & Sunnapwar, 2020). Furthermore, an organisation can address its unique issues by using DMAIC, a five-phased project management improvement framework in LSS (Gupta et al., 2020). Despite the benefits of LSS, previous studies have regarded the implementation of LSS in the service sector as limited compared to the manufacturing sector (Bhat et al., 2014).
Lean accounting
Lean accounting is based on lean accounting tools (Maskell & Baggaley, 2006) and is commonly described as integrating lean principles into accounting operations (Baggaley & Maskell, 2003a). Some accounting procedures contain muda, which can not be eliminated, while the majority of accounting operations contain muda, which can be eliminated (Baggaley & Maskell, 2003b; Maskell & Baggaley, 2006). Consequently, applying lean accounting measurement tools enables the persistent elimination of waste. This is accomplished in the same manner as waste reduction is accomplished elsewhere; by consistently removing waste from the organisation’s transaction procedures, reporting, and accounting methods (Maskell & Baggaley, 2006). Appropriate tools measuring lean accounting are crucial for management accounting to predict the organisation’s future performance (DeBusk, 2015).
Value stream costing (VSC) and value stream mapping (VSM) are common tools used in lean accounting, which it takes bumps sales and as the core idea (Malik, 2016; Valmohammadi & Dadashnejad, 2021). Despite the great performance outcomes of lean management implementation, lean organisations cannot be sustained over the long term without significant changes in these systems (Malik, 2016). It is noted that traditional accounting methods are based on mass production laws and principles (Kamal, 2015). However, lean practices violate these rules (Maskell, 2006). However, Hallam et al. (2018) argue that lean transformation companies do not always succeed in their performance without strategic leadership action. Thus, implementing lean in the business environment by utilising lean strategic action will drive towards the company’s performance. In a nutshell, implementing lean accounting rooted in lean thinking addresses and focusing the business around the value created for customer (Maskell, 2016). Moreover, lean accounting enables the organisation to determine the financial impact of lean improvement and thus develop a strategy to maximise its benefits (Maskell & Baggaley, 2006). Figure 1 presents the principles, practices and tools of lean accounting.
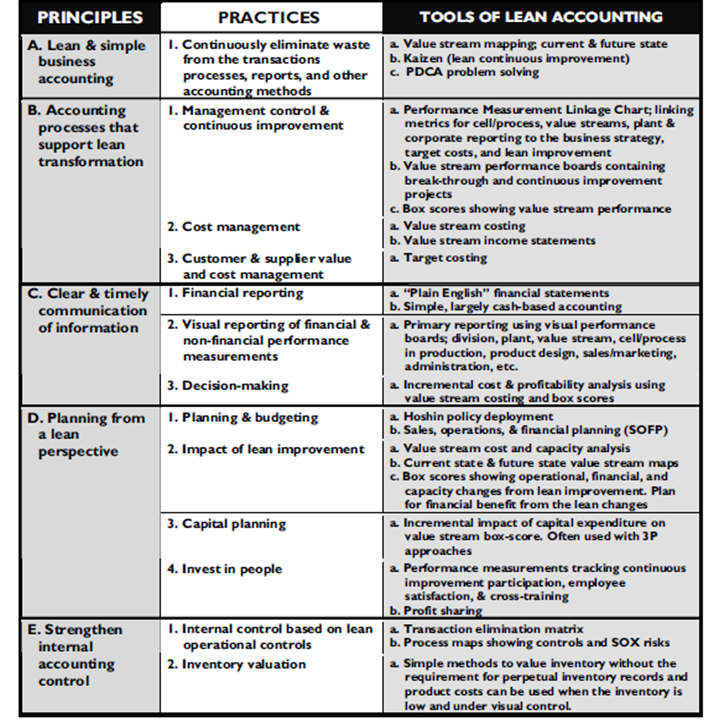
Research Methodology
The study collects the data from published sources and then analyses to produce different knowledge, interpretations and conclusions (Bougie & Sekaran, 2019). This study focused on English peer-reviewed journal articles as the primary source of rigorous research publications and the key source of information for academics and researchers. Hence, publications written in other languages, textbooks, master’s and doctorate dissertations, and unpublished working papers were not taken into account. The study also focuses on articles with a primary focus on Six Sigma, lean, LSS and lean accounting in their content. As part of data collection sources, various online sources and databases were searched to gather required information and data. According to Shokri (2017), other online databases were required due to the uniquenes, characteristics and nature of these quality practices. Key research databases were explored includes Emerald, ScienceDirect (Elsevier), Inderscience, Willey online, IEEE-Xplore, and Google Scholar. These databases provided access to the online fulltext of the articles. However, it was impossible to guarantee that this search would cover all relevant articles. The compilation of the databases takes almost 5 months through extensive databases of reviewed articles. The collected data then transformed to the Excel spreadsheet for review analysis.
Result and Discussion
This study developed a research classification framework based on Shokri (2017). The development of this classification was originally extracted from literature review databases. Accordingly, the dimensions were determined to analyse of reviewed articles. The development of this classification significantly contributes to the new knowledge and ideas on practical improvement practices and research gap identification, specifically; Six-Sigma, lean, LSS and lean accounting. The classification of the framework is determined by the following dimensions; (1) country, (2) theme and focus and (3) industry and sector where the research was conducted for literature review analysis.
Distribution by Country
Table 1 presents an analysis done based on country. Based on the reviewed papers, the distribution of country where the research was conducted are dispersed to four quality improvement factors. Majority the research on Six Sigma, lean, LSS and lean accounting were conducted in USA and India, followed by UK and Malaysia. However, the analysis reveals that limited countries conducted research on lean accounting study. Limited understanding on the practical of lean accounting resulting to resistance to change to advanced accounting practices (Baggaley & Maskell, 2003a; Maskell et al., 2017).
Table 2 presents the distribution by theme and focus of Six Sigma, lean, LSS and lean accounting. The analysis found the variety of themes and focuses used in the previous study. Most articles have more than one theme that focuses on critical success factors and tools and techniques. Theme and focus for Six Sigma and LSS seem as the most common theme used (Shokri, 2017).
Next, Figure 2 presents the industry and sector distribution of four quality improvement practices. It was revealed that Six Sigma, lean and LSS have focused on healthcare and manufacturing industry or sector. Research on lean accounting studies was focused in manufacturing industry. There is clear research gap on lean accounting study between some specific industries. From the analysis, it seem that limited sectors have not been approached by lean accounting. This study also consistent with Shokri (2017) found that an increasing trend of Six Sigma, lean and LSS research on healthcare, manufacturing and automotive sectors.
Conclusion and Implications
This study performs an analysis on reviewed articles of four quality improvement practices; Six Sigma, lean, Lean Six Sigma (LSS) and lean accounting of lean organisation. This study aims to identify research gaps through a comparative analysis of lean implementation and transformation. Despite a relatively large number of research findings on Six Sigma, lean, LSS and lean accounting, research on these four quality improvement practices research largely limited to country, research theme and focus and industry and sectors. Having great support and strategic management decision-making on lean transformation can improve organisational performance (Shokri, 2017). Thus, this study might contribute to practitioners to recognise their organisational areas where substantial improvement can be made through lean practices. Moreover, implementing lean transformation and strategies may contribute to business competitiveness (Hallam et al., 2018). Thus, lean practices within an organisation may impact on long-term business sustainability. In the future, researchers will be expected to collaborate more closely and broadly with businesses to develop the use of these techniques. It was also shown that there is still a significant discrepancy among researchers in writing these business improvement practices, and it is noted that implementing lean accounting is a radical change to an organisation’s accounting, control and measurement system.
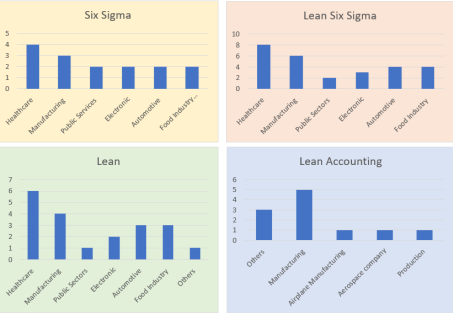
Due to uncertainty in the global market and challenges in meeting customer expectations and requirements, cost minimisation is seen as the priority of most managers. The rapid changes in this turbulent environment, academic researchers are challenged to provide new conceptual frameworks and theories to capture the evolution in existing practices. Empirical evidence of the management accounting method will efficiently translate the improvements made by lean accounting to the overall organisation’s performance. capture the elimination of unnecessary activities while creating value for the organisation as a whole. This paper reviews lean accounting derives from the evolution of management accounting advocates that lean implementation would improve the internal process efficiency and value creation of overall business activities processes. Therefore, adopting lean accounting within manufacturing companies may encourage them that development is needed to compete in world markets. Concentrating on adding value, going upmarket and gaining share market (Gukasyan et al., 2022; Sheridan, 1990), the conventional management accounting practices, lean accounting, should take place and help the management in strategic decisions to meet a sustainable business environment. This study is not devoid of research limitations. This study was mainly based on literature review and quantitative studies and did not perform analysis tests on theory and case studies analysis. Thus, literature review analysis of qualitative research or case studies would be tested and improved with the sound of empirical evidence.
Acknowledgements
The researcher appreciates and thanks the Ministry of Higher Education (MOHE) Malaysia for financial support of this research under the Fundamental Research Grant Scheme (FRGS) with project code FRGS/1/2019/SS08/UNITEN/03/1.
References
Ahamadzadeh, T., Etemadi, H., & Pifeh, A. (2011). Exploration of Factors Influencing on Choice the Activity-Based Costing System in Iranian Organizations. International Journal of Business Administration, 2(1), 61–70.
Al-Omiri, M., & Drury, C. (2007). A survey of factors influencing the choice of product costing systems in UK organizations. Management Accounting Research, 18(4), 399–424.
Albliwi, S. A., Antony, J., & Lim, S. A. H. (2015). A systematic review of Lean Six Sigma for the manufacturing industry. Business Process Management Journal, 21(3), 665–691.
Antony, J., & Desai, D. A. (2009). Assessing the status of six sigma implementation in the Indian industry: Results from an exploratory empirical study. Management Research News, 32(5), 413–423.
Antony, J., Sony, M., & Gutierrez, L. (2022). An Empirical Study Into the Limitations and Emerging Trends of Six Sigma: Findings From a Global Survey. IEEE Transactions on Engineering Management, 69(5), 2088–2101.
Assarlind, M., Gremyr, I., & Bäckman, K. (2013). Multi-faceted views on a Lean Six Sigma application. International Journal of Quality and Reliability Management, 30(4), 387–402.
Baggaley, B., & Maskell, B. (2003a). Value stream management for lean companies, Part I. Journal of Cost Management, 17(3), 24–30.
Baggaley, B., & Maskell, B. (2003b). Value stream management for lean companies, Part II. Journal of Cost Management, 17(3), 24–30. https://www.proquest.com/docview/209699345/fulltextPDF/ 6EE25F76C8FB4A80PQ/1?accountid=13155
Bell, J., Ansari, S., Klammer, T., & Lawrence, C. (2004). Strategy and management accounting. In Module version (1.2).
Bhat, S., Gijo, E. V., & Jnanesh, N. A. (2014). Application of Lean Six Sigma methodology in the registration process of a hospital. International Journal of Productivity and Performance Management, 63(5), 613–643.
Bougie, R., & Sekaran, U. (2019). Research Methods For Business A Skill Building Approach (8th, Asia ed.). Wiley. https://www.wiley.com/en-sg/Research+Methods+For+Business%3A+A+Skill+ Building+Approach%2C+8th+Edition%2C+Asia+Edition-p-9781119683537
Chavez, R., Yu, W., Jacobs, M., Fynes, B., Wiengarten, F., & Lecuna, A. (2015). Internal lean practices and performance: The role of technological turbulence. International Journal of Production Economics.
Chugani, N., Kumar, V., Garza-Reyes, J. A., Rocha-Lona, L., & Upadhyay, A. (2017). Investigating the green impact of Lean, Six Sigma and Lean Six Sigma. International Journal of Lean Six Sigma, 8(1), 7–32.
DeBusk, G. K. (2015). Use lean accounting to add value to the organization. Journal of Corporate Accounting & Finance, 23(3), 29–35.
Drohomeretski, E., Gouvea Da Costa, S. E., Pinheiro De Lima, E., & Garbuio, P. A. D. R. (2014). Lean, six sigma and lean six sigma: An analysis based on operations strategy. International Journal of Production Research, 52(3), 804–824.
Fullerton, R. R., Kennedy, F. A., & Widener, S. K. (2014). Lean manufacturing and firm performance: The incremental contribution of lean management accounting practices. Journal of Operations Management.
Gaikwad, L., & Sunnapwar, V. (2020). An integrated Lean, Green and Six Sigma strategies: A systematic literature review and directions for future research. TQM Journal, 32(2), 201–225.
Gukasyan, Z. O., Tavbulatova, Z. K., Aksenova, Z. A., Gasanova, N. M., & Karpunina, E. K. (2022). Strategies for Adapting Companies to the Turbulence Caused by the COVID-19 Pandemic. In Advances in Science, Technology and Innovation (pp. 639–645). Springer Nature.
Gupta, S., Modgil, S., & Gunasekaran, A. (2020). Big data in lean six sigma: a review and further research directions. International Journal of Production Research, 58(3), 947–969.
Habidin, N. F., Mohd Yusof, S., & Mohd Fuzi, N. (2016). Lean Six Sigma, strategic control systems, and organizational performance for automotive suppliers. International Journal of Lean Six Sigma, 7(2), 110–135.
Habidin, N. F., & Yusof, S. M. (2013). Critical success factors of lean six sigma for the malaysian automotive industry. International Journal of Lean Six Sigma, 4(1), 60–82.
Hallam, C. R. A., Valerdi, R., & Contreras, C. (2018). Strategic lean actions for sustainable competitive advantage. International Journal of Quality and Reliability Management, 35(2), 481–509.
Kamal, S. (2015). Historical evolution of management accounting. The Cost & Management, 43(4), 12–19.
Malik, S. M. (2016). An empirical study of lean accounting variable in the context of manufacturing & non- manufacturing sectors of India for its growth and future aspects: An ardle approach. Journal of Intelectual Studies & Theories, 2(Jul-Dec 2016), 328–359.
Maskell, B. (2006). Solving the standard cost problem. Journal of Cost Management, 20(1), 27–35.
Maskell, B., Baggaley, B., & Grasso, L. (2017). Practical lean accounting: A proven system for measuring and managing the lean enterprise: Second edition. In Practical Lean Accounting: A Proven System for Measuring and Managing the Lean Enterprise, Second Edition.
Maskell, B. H. (2016). Lean accounting. In The Routledge Companion to Lean Management.
Maskell, B. H., & Baggaley, B. L. (2006). Lean accounting: What’s it all about? Association for Manufacturing Excellence: Target Magazine.
Nakhai, B., & Neves, J. S. (2009). The challenges of six sigma in improving service quality. International Journal of Quality and Reliability Management, 26(7), 663–684.
Neoh, S. F., & Lai, T. S. (2021). The impact of trade openness on manufacturing sector performance: evidence from Malaysia. Journal of Economics and Sustainability, 3(1), 11-11.
Ngu, H. J., Lee, M. D., & Bin Osman, M. S. (2020). Review on current challenges and future opportunities in Malaysia sustainable manufacturing: Remanufacturing industries. Journal of Cleaner Production, 273, 123071.
Pepper, M. P. J., & Spedding, T. A. (2010). The evolution of lean Six Sigma. International Journal of Quality and Reliability Management, 27(2), 138–155.
Salah, S., & Rahim, A. (2019). An Integrated Company-Wide Management System. An Integrated Company-Wide Management System, 7(2), 110–135.
Sheridan, T. J. (1990). Accounting and manufacturing. Management Accounting Research, 1(2), 150–154.
Shokri, A. (2017). Quantitative analysis of Six Sigma, Lean and Lean Six Sigma research publications in last two decades. International Journal of Quality and Reliability Management, 34(5), 598–625.
Shokri, A., Oglethorpe, D., & Nabhani, F. (2014). Evaluating Six Sigma methodology to improve logistical measures of food distribution SMEs. Journal of Manufacturing Technology Management, 25(7), 998–1027.
Snee, R. D. (2004). Six-Sigma: the evolution of 100 years of business improvement methodology. International Journal of Six Sigma and Competitive Advantage, 1(1), 4–20.
Soltani, M., Aouag, H., & Mouss, M. D. (2020). Enhancement of the competitiveness and the financial capability of a manufacturing process through a new value stream mapping approach. International Journal of Productivity and Quality Management, 29(4), 439–453.
Sugahara, S., Daidj, N., & Ushio, S. (2017). Value Creation in management accounting and strategic management: An integrated approach. In Diverse and Global Perspectives on Value Creation Set (Vol. 2). ISTE Ltd and John Wiley & Sons, Inc.
Valmohammadi, C., & Dadashnejad, A. A. (2021). Value stream mapping implementation: An operational view. International Journal of Productivity and Quality Management, 32(3), 307–326.
Wilson, J. (1997). Elements of the system dynamics method. Journal of the Operational Research Society, 48, 1144–1150.
Womack, J. P., & Jones, D. T. (2003). Lean Thinking—Banish Waste and Create Wealth in your Corporation. Journal of the Operational Research Society, 48(11), 1148.
Womack, J. P., & Jones, D. T. (2005). Lean consumption. In Harvard Business Review.
Womack, J. P., Jones, D. T., & Roos, D. (1990). The machine that changed the world: Based on the Massachusetts Institute of Technology 5-million-dollar 5-year study on the future of the automobile. Free Press.
Copyright information
This work is licensed under a Creative Commons Attribution-NonCommercial-NoDerivatives 4.0 International License.
About this article
Publication Date
18 August 2023
Article Doi
eBook ISBN
978-1-80296-963-4
Publisher
European Publisher
Volume
1
Print ISBN (optional)
-
Edition Number
1st Edition
Pages
1-1050
Subjects
Multi-disciplinary, Accounting, Finance, Economics, Business Management, Marketing, Entrepreneurship, Social Studies
Cite this article as:
Abdul Hamid, M., & Habidin, N. F. (2023). Quantitative Analysis of Six Sigma, Lean, Lean Six Sigma and Lean Accounting. In A. H. Jaaffar, S. Buniamin, N. R. A. Rahman, N. S. Othman, N. Mohammad, S. Kasavan, N. E. A. B. Mohamad, Z. M. Saad, F. A. Ghani, & N. I. N. Redzuan (Eds.), Accelerating Transformation towards Sustainable and Resilient Business: Lessons Learned from the COVID-19 Crisis, vol 1. European Proceedings of Finance and Economics (pp. 165-175). European Publisher. https://doi.org/10.15405/epfe.23081.14