Abstract
The cyber-physical systems complex control is being studied based on information and signal actions of the cyber-physical production processes dynamics. Information action is a result of the virtual environment operation processes modelling, which is transmitted to the digital connection channels control physical loop. The signal action is formed in the integrated computing automatics system and controls electromechanically the equipment moving parts. The technological processes double control technology is based on the mathematical similarity evaluation for the cyber-physical systems states parameters being calculated or being physically watched. The information and signal actions are produced in the automatics loops creating the hierarchy structures of different levels. The double control purpose, which is the base of cyber-physical production intellectual control is to adapt cyber-physical systems for the technological environment properties being changed dynamically. There is a scheme of interconnected and interacting physical and virtual cyber-physical systems loops. In the example of two-level production workshop hierarchy system there is a way described how to control technological processes in the information and signal actions aspects.
Keywords: Cyber-physical system, hierarchy control, Industry 40
Introduction
To stimulate methods and means to automatize the production processes, which is the part of the Industry 4.0 concept they implemented cyber-physical systems (CPSs) and their technologies in the industrial object infrastructure (Cicirelli et al., 2018; Negri et al., 2020). The intellectual production based on CPSs requires to use physical objects analytical models in the technological processes alongside the equipment control traditional ways, which are used in the item manufacturing. Analytical models given with a program code to be realized in the computing models CPS platforms, which are viewed in the cyber-physical production (CPP) structure as a new source of control actions, which action the physical processes directly during the CPS industrial exploiting (Bordel et al., 2017; Pola & Di Benedetto, 2019).
The automatic control theory aspect and CPS technologies to add up to the existing integrated automatics computing systems signal action (electronic, mechanical and other) with informative action (model), which in parallel corrects the physical processes through a computer net, which is so-called two-level task solution to synthesize regulators controlling CPP functionality. Complimentary signal and information actions provides multipurpose CPS control within a CPP characterizing the hierarchy and distributed technological equipment with net structures (Zhang et al., 2019; Zhou et al., 2021).
To concord actions of an individual CPS and their groups united into general technological division is done with a similarity property of the given equipment states parameters values (target) and values being viewed in fact received in physical processes and after a modelling. The CPS autonomous control and CPS regulation from virtual environment (model), which together forms the interconnected and interacting hierarchy automatics loops, which physical and information processes action each other through the net channels of feedback (Magdalena, 2019; Zhu et al., 2020). The transfer from the strict control concept to the iterative calculation procedures of the being controlled parameters evaluation in the virtual environment and CPS intensive communications, which is the CPP automatic control idea core and a way to realize practically a system forming concept of the Industry 4.0 (Zhang et al., 2020b; Zhang et al., 2020).
The model application of signal and information actions of the CPS net control functioning autonomously and cooperatively, which let develop the CPP hierarchy structure, which have (Illmer & Vielhaber, 2021; Zhang et al., 2020a):
- CPS physical device (hardware and software) has a capability to regulate independently the technological processes with integrated computing system resources;
- CPS virtual model (digital twin) has a prognostication control function and is viewed as a digital regulator of higher level super-structured over process core controlling exclusively the technological units.
Dynamically interconnected physical and virtual control loops involved into CPP technological processes regulation forms the industrial object system infrastructure, which let configure peripheral CPSs for the item manufacturing of different purpose (Lopez & Rubio, 2018). The CPP hierarchy virtual level calculating information action from the architecture point of view provides cyclic net tides of CPS control parameters defining the item quality in its similarity criterion to the digital twins. The CPP hierarchy physical level working out signals for the CPS moving parts controls functional properties and mass and dimensions characteristics of the item being manufactured (Batchkova & Ivanova, 2019; Wang et al., 2007).
The CPS Hierarchy Structure Control
The CPP hierarchy structure control functioning is done with integrated physics and logics processes. Automatics elements (executive mechanisms, the control objects regulation organs and other) provide mostly the physical character of the technological processes being done. The computing automatics elements concentrated in the virtual environment realizes exclusively CPP processes (information).
The technological division output parameters changing (control objects of higher level) is done with automatics elements activation (regulators and actuators performed as some industrial manipulators) of the hierarchy lower level controlled with calculators. The CPP control mechanism is the technological division states parameters re-calculation reflecting the laws of simultaneous functioning of all automatics elements into a vector of the equipment state parameters evaluation and the necessary correcting actions for intermediary sections of the dynamic system being regulated. The cyclic corrections of control objects states and processes of all hierarchy levels with the nets of feedback is the regulation core of the applied in multi-loop and multichannel industrial automatics scheme.
Clear the similarity may be between intermediary and global CPP control loops there are some significant differences with some non-definition level calculating the amendments for the regulators. The non-definition is done in informative and technological aspects justified with high autonomous level of CPS functioning for the different levels of hierarchy structure:
- the technological aspect is associated with the material tides movement, which item consumer is the control object of next level;
- the information aspect is expressed with the delay of the calculation evaluations of current and desired control objects states of different levels, which action the multi-measure dynamic systems control quality.
To control the CPP hierarchy structures they require to develop new and to correct the existing methods of dynamic systems mathematical analysis and their parametric synthesis adequate for technological processes being done in complicated CPS industrial automatics.
Signal and Information Actions of the CPS Control Systems
The CPP structure CPS hierarchy is done as organized combination of subordinate control objects, which process regulation is done with a higher level subject. The automatics elements multi-step structure organization is used to control a separate CPS, production sections (workshops) and technological divisions in general based on the balance maintaining principles of all elements constant interactions. The processes to be regulated as much as technological environment CPSs and their relations of the item manufacturing in the fully automated CPP states. The hierarchy control purpose is to reach the necessary CPS states, which are CPP infrastructure components when each subject sends a regulation action to a subordinate.
The CPP structure hierarchy principal is based on CPS groups aggregation within several levels for each of which the CPS classification organizing trait is the control target function, which depends on the technological task being solved. The control subject is an active CPS (the CPP controlling component) forming regulating actions for units or industrial equipment groups. The control object (the CPP being controlled component) is a passive CPS to execute the incoming actions. The regulating CPSs and their ways to action each other is defined with actuator technical realization features, which in the CPP infrastructure could be a wide class of electromechanical devices including robot manipulators, transporters and other.
The given in figure 1(а) enlarged functional scheme two hierarchy levels of the CPP organization structure are shown for which CPS roles (functions) are distributed among control subjects and objects. The CPS hierarchy high level is equal to a production workshop and the lower one are technological equipment units to which controlling actions are done. The scheme reflects the interaction order of one subject and two subordinate objects of control. The CPS authorizations structuring is provided with control signals transmission channels and feedback channels supporting production processes regulation in the required target technological task direction.
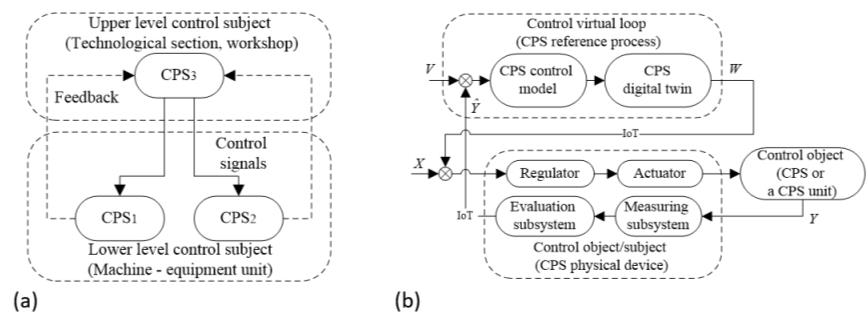
The CPS structure hierarchy control feature is a combination of information and signal actions. Information actions calculate in edge, fog or cloud cyber-modelling environments placed in the company virtual environment, which is transmitted to the CPS physical devices with net message transportation tools (data packages). Signal actions are CPP functioning physical environment elements and reflects normally electrical, optical, mechanical and other processes inside the CPS devices. In figure 1(b) there is a detailed scheme given of a single CPS control system containing typical automatics elements, connections among them and combining information and signal actions for the technological objects and processes.
The CPS hierarchy groups activity coordination supporting information and signal actions united into a single production workshop is done with target inner control mechanisms directed to manufacture an end item. The inner control is used for complicated CPS structures, which organization level keep general principle of CPP hierarchy. In figure 2 there is a detailed scheme given of subject interaction with two subordinate control objects using technologies of direct and indirect CPS regulation based on information and signal actions. The scheme forms a closed loop of the production workshop automatic control in which CPS got simultaneous roles of subjects and objects realizing independent functions.
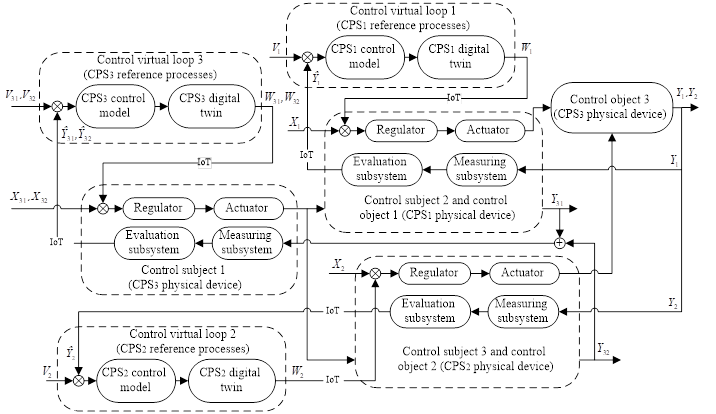
Incoming actions for two-level control system are formalized with information (electronic documentation) and material (technological raw material) tides circulating in physical and virtual company environments. The CPS reaction information for signal controlling action is transmitted through the Internet of Things (IoT) channel into the virtual environment where analytical calculation means (models) are defined with informative action, which CPS modifying behavior into physical environment. The control subjects intervention into CPS technological processes placed in a lower level (control objects) is done within the CPP general task defined with a digital twin of the item being manufactured. Control processes inside the CPS hierarchy approximated levels are mostly general and different in details, which depend on the way to realize a regulator, actuators and information and signal actions values.
Cyber-physical approach to synthesize control subjects and objects control system inside the technological division with the following features important to develop the CPP hierarchy structure based on CPSs:
- the CPS technological resource loading up coefficient completing a production task is restricted with limited permissible level of computing parallelism defined with the inner system controller properties and the cyber-modelling process core and passing through ability of the IoT connection channel general for each CPS;
- CPS technological processes regulation is done with a combination of signal and information actions providing preservation of equal weight states and changes of control objects dynamic parameters in the direction corresponding to the cyber production technological task;
- the given incoming actions received by the CPS control physical and virtual loops depend on the item being manufactured features represented with a digital twin and can be constant values (parameters stabilizing support mode) and also that could be a time function;
- a combination of physical and virtual loops having fixed roles to evaluate the control object state forms the base CPP functional element, which is a CPS with some computing capabilities and capabilities to communicate in the net IoT wireless channel;
- the item being manufactured quality control, which is done through measurement and evaluation of its indications (monitoring) is accompanied by continuous accordance of the primary control purpose (technological task) and private control functions being done in the CPS physical device and its digital twin and other.
In figure 3 there is a general scheme given of CPP model control system including as subjects and objects: elementary CPSs; group CPSs united in a production workshop; technological division integrating workshops into a closed industrial company infrastructure. The full oriented lines (arrows) they show channels of signal and information actions of subjects to the control objects. The gapped lines show feedback channels existing in physical and virtual environments. Horizontal and vertical hierarchy in the CPP structure provides:
- control system division into physical and virtual loops making a complimentary action to separate CPS objects in their current state;
- the production infrastructure elements division into automatics components making a particular executive function for control subjects or objects and their simultaneous combination.
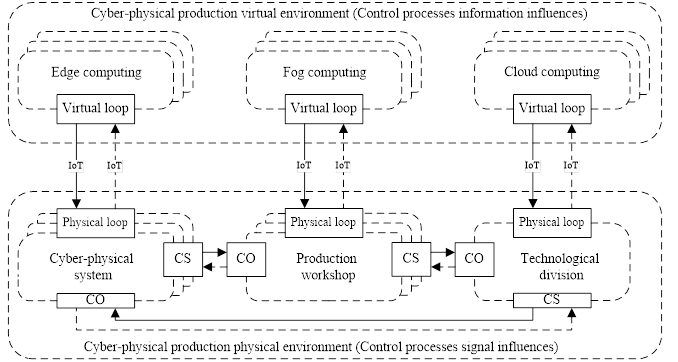
Conclusion
The modern science and the Industry 4.0 production concept grasp led to creation of new type of industrial equipment (CPS), which simultaneously use to manufacture the item in technological and information processes synchronizing through a computing net. Unite technologies of integrated computing systems and net technologies as a part of industrial CPS let CPP designer create completely new scheme solutions for information, measurement and control divisions, which functionality coordination mechanisms require the process state objective data transmission and equipment to the package messages standardized with protocols of IoT.
The constructed as the Industry 3.0 practice to synthesize automatic control systems of technological objects and processes required separate cycles of projection machine and software production infrastructures parts without considering data connections being formed in physical and virtual company environments and reflecting numeric values of the parameters being controlled. An alternative approach to develop the Industry 4.0 production infrastructure based on object oriented projection technologies, which sense is to create mathematical object models (virtual) equal to the technological processes and CPS physical devices.
A multi-representations of CPS structure in a mathematical language enters a formal base (theoretical basis) to automatize a projection of complicated information, measuring and controlling systems (divisions) applying laws of electronics, mechanics, optics and other in the item manufacturing processes. Concord interaction of different CPS set models reflecting particular properties of physical devices, which provide:
- in the control technology aspects ― operative or preventive corrective action on the technological parameters being controlled and adaptive settings coefficients of hierarchy organized CPS regulators;
- in the computing technology aspect ― context dependent model calculations of the CPS functional activity desired parameters within a conveyor line justified with temporal difficulties of the CPP technological task;
- in the communication technology aspects ― information exchange being serviced simultaneously in a CPS net using metrics and data formats standardized as measuring units and protocols accepted in the IoT.
The object oriented projection supports the CPS hierarchy structure synthesis, which general laws of functioning correspond to multi-agent dynamic systems but in some private realization interaction schemes of automatizing components they significantly increased a part of special technologies of control, computing and communication united with information tides. The IoT computing net added with functional automatics elements (detectors, regulating organs, executive mechanisms, control objects and other) forms a CPP dynamic system equipped with a CPS. The complexity of being created using mathematical models CPPs hierarchy structures may vary from one loop scheme of integrated CPS regulators to a multilevel control system covering with net feedback calculating, measuring units of CPS groups and distributed technological environment state sensors with huge industrial objects.
References
Batchkova, I., & Ivanova, T. (2019). Model-driven development of agent-based cyber-physical systems. IFAC-PapersOnLine, 52(25), 258-263. DOI:
Bordel, B., Alcarria, R., Robles, T., & Martín, D. (2017). Cyber-physical systems: Extending pervasive sensing from control theory to the Internet of Things. Pervasive and Mobile Computing, 40, 156-184. DOI:
Cicirelli, F., Nigro, L., & Sciammarella, P. F. (2018). Model continuity in cyber-physical systems: A control-centered methodology based on agents. Simulation Modelling Practice and Theory, 83, 93-107. DOI:
Illmer, B., & Vielhaber, M. (2021). Describing cyber-physical systems using production characteristics and methodical integration into virtual commissioning. Procedia CIRP, 97, 272-277. DOI:
Lopez, J., & Rubio, J. E. (2018). Access control for cyber-physical systems interconnected to the cloud. Computer Networks, 134, 46-54. DOI:
Magdalena, L. (2019). Semantic interpretability in hierarchical fuzzy systems: Creating semantically decouplable hierarchies. Information Sciences, 496, 109-123. DOI:
Negri, E., Berardi, S., Fumagalli, L., & Macchi, M. (2020). MES-integrated digital twin frameworks. Journal of Manufacturing Systems, 56, 58-71. DOI:
Pola, G., & Di Benedetto, M. D. (2019). Control of Cyber-Physical-Systems with logic specifications: A formal methods approach. Annual Reviews in Control, 47, 178-192. DOI:
Wang, Y., He, Y. L., Zhao, T. S., Tang, G. H., & Tao, W. Q. (2007). Implicit-explicit finite-difference lattice Boltzmann method for compressible flows. International Journal of Modern Physics C, 18(12), 1961-1983. DOI: 10.1142/S0129183107011868
Zhang, B., Dou, C., Yue, D., Zhang, Z., & Zhang, T. (2019). Consensus-based economic hierarchical control strategy for islanded MG considering communication path reconstruction. Journal of the Franklin Institute, 356(16), 9043-9075. DOI:
Zhang, B., Dou, C., Yue, D., Zhang, Z., & Zhang, T. (2020a). Hierarchical control strategy for networked DC microgrid based on adaptive dynamic program and event-triggered consensus algorithm considering economy and actuator fault. Journal of the Franklin Institute, 357(13), 8631-8656. DOI:
Zhang, B., Dou, C., Yue, D., Zhang, Z., Zhang, T., & Ma, K. (2020b). Cyber-physical cooperative response strategy for consensus-based hierarchical control in micro-grid facing with communication interruption. International Journal of Electrical Power & Energy Systems, 114, 105405. DOI:
Zhang, Y., Gong, G., Yang, H., Li, W., & Liu, J. (2020). Digital Twin and Industry 4.0 Enablers in Building and Construction: A Survey. Automation in construction, 114, 103173.
Zhou, A., Ren, K., Li, X., Zhang, W., Ren, X., & Deng, K. (2021). Semantic-based discovery method for high-performance computing resources in cyber-physical systems. Microprocessors and Microsystems, 80, 103328. DOI:
Zhu, C., Butler, M., & Cirstea, C. (2020). Formalizing hierarchical scheduling for refinement of real-time systems. Science of Computer Programming, 189, 102390. DOI:
Copyright information
This work is licensed under a Creative Commons Attribution-NonCommercial-NoDerivatives 4.0 International License
About this article
Publication Date
27 February 2023
Article Doi
eBook ISBN
978-1-80296-960-3
Publisher
European Publisher
Volume
1
Print ISBN (optional)
-
Edition Number
1st Edition
Pages
1-403
Subjects
Hybrid methods, modeling and optimization, complex systems, mathematical models, data mining, computational intelligence
Cite this article as:
Shukalov, A. V., Babenkov, V. I., Zharinov, I. O., & Zharinov, O. O. (2023). Information and Signal Actions in the Cyber-Physical Systems Hierarchy Control. In P. Stanimorovic, A. A. Stupina, E. Semenkin, & I. V. Kovalev (Eds.), Hybrid Methods of Modeling and Optimization in Complex Systems, vol 1. European Proceedings of Computers and Technology (pp. 31-38). European Publisher. https://doi.org/10.15405/epct.23021.4