Abstract
The following work is done to briefly outline what is mechatronics. Also, this term will be accompanied by the use of a manipulator with 7 degrees of freedom. In modern realities, the combination of different fields is inevitable, since the modern world requires complex and multi-tasking ideas. Mechatronics is a term used to describe the combination of different fields to maximize their potential. since the modern world requires complex and multi-tasking ideas. The paper shows that the use of mechatronics covers a wide range of activities. Similarly, a robotic arm with 7 degrees of freedom will be shown in terms of modelling and improvement. A model of a robotic arm will be presented with the introduction of additional movements, which will bring new possibilities to the system in terms of mobility. The main purpose of the study is to illustrate that 7 DOF robotic arm is a great example of mechatronics.
Keywords: Mechatronics, robotic arm, 7 DOF, mobility
Introduction
Mechatronics is a term used to describe a device or product that combines mechanical, electronic, control and software aspects (Figure 1). Examples of such a term can be any modern robots, vehicles, aircraft, and so on. There are two branches in mechatronics: spatial and movement-related. Both have their own benefits and ease of use. The concept of "spatial", like the word itself, is associated with space. Therefore, the goal is to achieve a high density of mechanical and electronic functions in the available space. The advantage is miniaturization, reduced production costs and higher reliability. The second part is due to the presence of controlled multi-body motion systems. The goal is to improve the behavior of various technical means using sensors to collect information about the environment and the system itself. The use of modern devices (in the context of the use of mechatronics) is commonplace and does not take effort from a person, since the integration of such systems into our lives goes unnoticed. However, the production of mechatronic devices is a labor-intensive business due to the wide functionality and its complex design. Therefore, due to their functionality and availability, the use of various and especially complex mechatronic devices is extensive.
Application of Mechatronics
The use of mechatronics covers a wide range of activities. Mechatronics can be found in almost any modern technique. For example, electronic home appliances, electronic entertainment products, engine systems (cars) and so on. Therefore, the following section will consider the use of mechatronics, namely, in production. When referring to production, it means usage of automated robotics embedded with a lot of electronics (ECPI Blog, 2022; Ordoñez-Avila et al., 2022).
Problem Statement
The use of mechatronics in manufacturing has increased the efficiency and quality of products. Many modern industries began to introduce everything new that would increase productivity and reduce unnecessary costs. The use of automated processes ensures that new implementation techniques save production time, minimize waste, and reduce labor force. Technical errors are also reduced, as the use of intelligent sensors and parameter controllers ensures that the specified operating conditions are maintained. Therefore, endless improvement of these tools will greatly effect the production rate of any industry, hence a small improvement could lead to higher profit too. Thereby, this work tries to find small improvement that can be introduced to the system. The following are the most relevant areas in production when using mechatronic systems (Gausemeier et al., 2011).
Factory Automation. Mechatronics allows the development of a continuous chain process that includes advanced equipment such as barcode readers, as well as image and sound processors that identify and classify products as they move.
Measuring products. In order to produce products with the correct characteristics in terms of size, weight and quantity, companies need to apply mechatronic technologies. Smart sensors and calibration systems are used to ensure product consistency.
Control systems. In order for a manufacturing plant to maintain optimal conditions, parameters such as temperature and pressure must be properly regulated and controlled. Mechatronics provides remote automation of this regulation, increasing efficiency and productivity. The use of mechatronic systems today is, as already mentioned, quite a common phenomenon. However, this is not the limit of the capabilities of these systems, and in the near future such systems will more and more capture different areas of human life and improve the quality and comfort of being on planet Earth.
Research Questions
The possibility of adding extra movement to 7 DOF robotic arm. It is also important to understand how can extra movement of 7 DOF robotic arm improve its ability.
Purpose of the Study
The main purpose of the study is to illustrate that 7 DOF robotic arm is a great example of mechatronics. It includes all before mentioned criteria of mechatronics. 7 DOF robotic arm is designed to mimic a human arm. Not only to imitate the similar ability of mobility, but extend it to new level. Therefore, modern robotic arms are capable of performing many tasks, which can be done by human arm and beyond. Therefore, the task of this work is to develop 7 degree of freedom robotic arm and add new abilities as an improvement (Avila et al., 2021).
Research Methods
Software selection
SolidWorks was used for the modelling of the 7 DOF robotic arm. SolidWorks is a powerful tool for not just to model 3D Objects, but also capable of assembly and analysis. Hence, the software is used throughout of the work. Other software was used at the beginning of the modelling (such as: Inventor, 3ds Max, ANSYS) to outline the best user-friendly tool. Accenting focus on interface and flowless ability for modelling (Magomedov et al., 2021; Zolkin et al., 2010).
Design
Different types of design were covered. But the chose was paused on the design shown in the Figure 1. The main characteristics that were looked up for the design, were easiness to build and to assembly. The main design consists of two elements (and two almost symmetrically mirrored parts too): joint and extender (Figure 1). Where element 1 and 4 represents joints and 2 and 3 represents extenders. Also, base element was built to be added in the beginning and at the end of the assembly. Base element shown in the Figure 2 with the blue color.
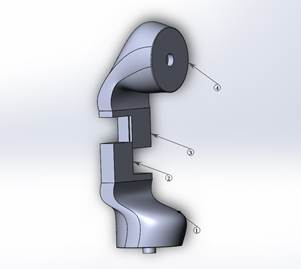
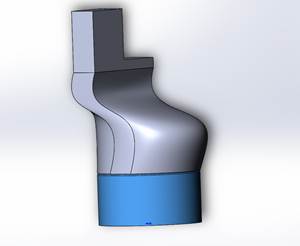
Assembly
As it was mentioned before, SolidWorks was used to assemble the parts. The parts were easily assembled as shown in the Figure 3. In total 26 parts were connected to each other in this assembly. These 26 assembled parts for a 7 Degree of freedom robotic arm. The movements are possible at where joints are connected.
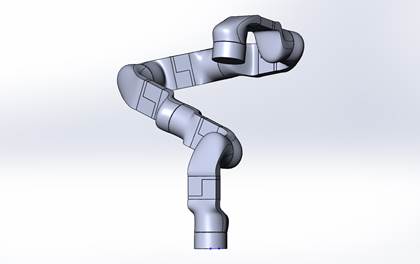
Extra movement
The extra movement was added to the traditional design. Usually, robotic arms rotate at the point where two joints are mated. However, this work presents extra movements at each joint (Figure4). As it can be seen from the Figure 4 each extender can be moved apart for a certain distance. Extra movements give the overall 7 DOF robotic arm mobility that extends its capability in the industry. The assembled body perfectly moves and makes all the operation that the traditional robotic arm can, but with the extra movements at each joint. It is obvious that for the final product, a lot of work needs to be put to this arm. For example, right now, only the design aspects of the structure are working. In reality, the design of the arm must include all three main components of mechatronics, as it was mentioned earlier. Hence, this work does not present the end product, but visual parts only.

Findings
7 DOF robotic arm is use widely in modern times in different fields of industries. It helps to drive production rate to the higher points. As production rate and time management and human errors are the main concerns of any industries. Automatization with the usage of 7 DOF robotic arm is solving before mentioning issues. Therefore, the state of the technology is playing a major role driving production in the progressive way. The aimed to develop new design with the extra movements of the mechanism. The 7 DOF robotic arm was built with extra details to allow its joints not just to rotate but to extend to a certain position.
Conclusion
To conclude, this work briefly outlined the term mechatronics and also represented some ways of its application. The main part of the work was to build and improve the existing 7 DOF robotic arm with the new design. 7 DOF robotic arm was build, and extra functionality was added in terms of new movements. The idea behinds the extra movements in the arm is to bring more mobility to multiply the capabilities.
References
Avila, J. L. O., Avila, M. O., Aguilar, D. A., & Cardona, M. (2021). Propose Method for the Design of a Transtibial Prosthesis using Generative CAD/FEM Analysis and Additive Manufacturing. In 2021 IEEE International Conference on Machine Learning and Applied Network Technologies (ICMLANT) (pp. 1-7). IEEE. DOI:
ECPI Blog. (2022). Application of Mechatronics: What Can This Technology Do? https://www.ecpi.edu/blog/application-of-mechatronics-what-can-this-technology-do
Gausemeier, J., Dumitrescu, R., Kahl, S., & Nordsiek, D. (2011). Integrative development of product and production system for mechatronic products. Robotics and Computer-Integrated Manufacturing, 27(4), 772-778. DOI:
Magomedov, I. A., Dzhabrailov, Z. A., & Elmurzaev, A. A. (2021). Key steps for performing numerical analysis utilizing modern software tools. Journal of Physics: Conference Series, 1889(4), 042078. DOI:
Ordoñez-Avila, J. L., Pineda, A. D., Rodriguez, J. D., & Carrasco, A. M. (2022). Design of Badminton Training Robot with Athlete Detection. In 2022 7th International Conference on Control and Robotics Engineering (ICCRE) (pp. 26-31). IEEE. DOI:
Zolkin, A. L., Tychkov, A. S., & Kalyakulin, A. N. (2010). Possibilities of application and features of the use of freely distributed software in the educational process. Actual problems of the development of the transport complex: Materials of the VI All-Russian remote scientific and practical conference (pp. 63-66). SamGUPS.
Copyright information
This work is licensed under a Creative Commons Attribution-NonCommercial-NoDerivatives 4.0 International License
About this article
Publication Date
27 February 2023
Article Doi
eBook ISBN
978-1-80296-960-3
Publisher
European Publisher
Volume
1
Print ISBN (optional)
-
Edition Number
1st Edition
Pages
1-403
Subjects
Hybrid methods, modeling and optimization, complex systems, mathematical models, data mining, computational intelligence
Cite this article as:
Magomedov, I., Matygov, M., & Dzhabrailov, Z. (2023). Mechatronics: Development and Improvement of the Existing Robotic Arm 7 Degree of Freedom. In P. Stanimorovic, A. A. Stupina, E. Semenkin, & I. V. Kovalev (Eds.), Hybrid Methods of Modeling and Optimization in Complex Systems, vol 1. European Proceedings of Computers and Technology (pp. 264-269). European Publisher. https://doi.org/10.15405/epct.23021.32